Bateman Company produces helmets for drivers of motorcycles. Helmets are produced in batches according to model and size. Although the setup and production time vary for each model, the smallest lead time is six days. The most popular model, Model HA2, takes two days for setup, and the production rate is 1,125 units per day. The expected annual demand for the model is 54,000 units. Demand for the model, however, can reach 67,500 units. The cost of carrying one HA2 helmet is $3 per unit. The setup cost is $9,000. Bateman chooses its batch size based on the economic order quantity criterion. Expected annual demand is used to compute the EOQ. Recently, Bateman has encountered some stiff competition—especially from foreign sources. Some of the foreign competitors have been able to produce and deliver the helmets to retailers in half the time it takes Bateman to produce. For example, a large retailer recently requested a delivery of 18,000 Model HA2 helmets with the stipulation that the helmets be delivered within seven working days. Bateman had 4,500 units of HA2 in stock. Bateman informed the potential customer that it could deliver 4,500 units immediately and the other 13,500 units in about 14 working days—with the possibility of interim partial orders being delivered. The customer declined the offer indicating that the total order had to be delivered within seven working days so that its stores could take advantage of some special local conditions. The customer expressed regret and indicated that it would accept the order from another competitor who could satisfy the time requirements. Required: 1. Calculate the optimal batch size for Model HA2 using the EOQ model. Round your answer to the nearest whole number if rounding is required. fill in the blank units 2. Upon learning of the lost order, the marketing manager grumbled about Bateman's inventory policy, "We lost the order because we didn't have sufficient inventory. We need to carry more units in inventory to deal with unexpected orders like these." How much additional inventory would have been needed to meet the customer's requirements? fill in the blank additional units 3. Fenton Gray, the head of industrial engineering, reacted differently to the lost order: "Our problem is more complex than insufficient inventory. I know that our foreign competitors carry much less inventory than we do. What we need to do is decrease the lead time. I have been studying this problem, and my staff has found a way to reduce setup time for Model HA2 from two days to 1.5 hours. Using this new procedure, setup cost can be reduced to about $94. Also, by rearranging the plant layout for this product—creating what are called manufacturing cells—we can increase the production rate from 1,125 units per day to about 3,000 units per day. This is done simply by eliminating a lot of move time and waiting time—both non-value-added activities." Assume that there are eight hours available in each workday. Assume that the engineer's estimates are on target. Compute the new optimal batch size (using the EOQ formula). Round your answer to the nearest whole number. fill in the blank units What is the new lead time? Round your answer to one decimal place. fill in the blank hours 4. Suppose that the setup time and cost are reduced to 0.5 hour and $10, respectively. What is the batch size now? Round your answer to the nearest whole number. fill in the blank units
Bateman Company produces helmets for drivers of motorcycles. Helmets are produced in batches according to model and size. Although the setup and production time vary for each model, the smallest lead time is six days. The most popular model, Model HA2, takes two days for setup, and the production rate is 1,125 units per day. The expected annual demand for the model is 54,000 units. Demand for the model, however, can reach 67,500 units. The cost of carrying one HA2 helmet is $3 per unit. The setup cost is $9,000. Bateman chooses its batch size based on the economic order quantity criterion. Expected annual demand is used to compute the EOQ.
Recently, Bateman has encountered some stiff competition—especially from foreign sources. Some of the foreign competitors have been able to produce and deliver the helmets to retailers in half the time it takes Bateman to produce. For example, a large retailer recently requested a delivery of 18,000 Model HA2 helmets with the stipulation that the helmets be delivered within seven working days. Bateman had 4,500 units of HA2 in stock. Bateman informed the potential customer that it could deliver 4,500 units immediately and the other 13,500 units in about 14 working days—with the possibility of interim partial orders being delivered. The customer declined the offer indicating that the total order had to be delivered within seven working days so that its stores could take advantage of some special local conditions. The customer expressed regret and indicated that it would accept the order from another competitor who could satisfy the time requirements.
Required:
1. Calculate the optimal batch size for Model HA2 using the EOQ model. Round your answer to the nearest whole number if rounding is required.
fill in the blank units
2. Upon learning of the lost order, the marketing manager grumbled about Bateman's inventory policy, "We lost the order because we didn't have sufficient inventory. We need to carry more units in inventory to deal with unexpected orders like these."
How much additional inventory would have been needed to meet the customer's requirements?
fill in the blank additional units
3. Fenton Gray, the head of industrial engineering, reacted differently to the lost order: "Our problem is more complex than insufficient inventory. I know that our foreign competitors carry much less inventory than we do. What we need to do is decrease the lead time. I have been studying this problem, and my staff has found a way to reduce setup time for Model HA2 from two days to 1.5 hours. Using this new procedure, setup cost can be reduced to about $94. Also, by rearranging the plant layout for this product—creating what are called manufacturing cells—we can increase the production rate from 1,125 units per day to about 3,000 units per day. This is done simply by eliminating a lot of move time and waiting time—both non-value-added activities." Assume that there are eight hours available in each workday.
Assume that the engineer's estimates are on target. Compute the new optimal batch size (using the EOQ formula). Round your answer to the nearest whole number.
fill in the blank units
What is the new lead time? Round your answer to one decimal place.
fill in the blank hours
4. Suppose that the setup time and cost are reduced to 0.5 hour and $10, respectively. What is the batch size now? Round your answer to the nearest whole number.
fill in the blank units

Trending now
This is a popular solution!
Step by step
Solved in 2 steps

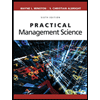
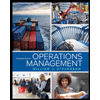
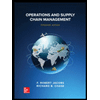
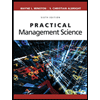
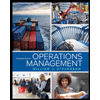
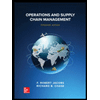
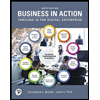
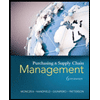
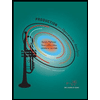