Case Study: Optimizing Supply Chain Management with a Custom Computer Application Introduction: In the dynamic landscape of modern business, efficient supply chain management is crucial for organizations aiming to stay competitive and meet customer demands. This case study explores the implementation of a custom computer application designed to optimize supply chain processes for a global manufacturing company, XYZ Manufacturing Inc. Background: XYZ Manufacturing Inc. operates in a highly competitive market with a diverse range of products. The company faced challenges in managing its complex supply chain, including inventory control, order processing, and logistics coordination. Manual processes and disparate systems led to inefficiencies, delays, and increased operational costs. To address these issues, XYZ Manufacturing Inc. decided to invest in a customized computer application tailored to its unique requirements. Development and Implementation: A cross-functional team consisting of IT specialists, supply chain experts, and key stakeholders was formed to develop the computer application. The application aimed to integrate various supply chain functions, providing real-time visibility into inventory levels, order status, and shipment tracking. Key features of the computer application included: Inventory Management: A centralized system for tracking and managing inventory levels across multiple warehouses, reducing the risk of stockouts and overstock situations. Order Processing: Automated order processing to streamline the fulfillment process, minimizing errors and expediting order-to-delivery timelines. Logistics Coordination: Integration with logistics partners to facilitate seamless communication and coordination, ensuring timely and cost-effective transportation of goods. Data Analytics: Robust analytics capabilities to generate actionable insights, helping in demand forecasting, identifying trends, and optimizing overall supply chain performance. Results: After the successful implementation of the computer application, XYZ Manufacturing Inc. experienced significant improvements in its supply chain efficiency. The company witnessed: Reduction in Operational Costs: Automation and streamlined processes led to a decrease in manual errors and operational costs. Improved Customer Satisfaction: Faster order processing and accurate inventory management contributed to enhanced customer satisfaction. Optimized Inventory Levels: Real-time visibility into inventory levels allowed for better demand planning, reducing excess stock and minimizing stockouts. Enhanced Decision-Making: Data analytics provided valuable insights, enabling the company to make informed decisions and adapt to market changes promptly. Conclusion: The custom computer application proved to be a game-changer for XYZ Manufacturing Inc., transforming its supply chain management and positioning the company for sustained growth in a competitive market. Objective Type Question: What key benefits did XYZ Manufacturing Inc. experience after implementing the custom computer application for supply chain management? A. Increased manual errors and operational costs. B. Longer order-to-delivery timelines. C. Decreased stockouts and optimized inventory levels. D. Limited visibility into inventory across warehouses.
Case Study: Optimizing Supply Chain Management with a Custom Computer Application Introduction: In the dynamic landscape of modern business, efficient supply chain management is crucial for organizations aiming to stay competitive and meet customer demands. This case study explores the implementation of a custom computer application designed to optimize supply chain processes for a global manufacturing company, XYZ Manufacturing Inc. Background: XYZ Manufacturing Inc. operates in a highly competitive market with a diverse range of products. The company faced challenges in managing its complex supply chain, including inventory control, order processing, and logistics coordination. Manual processes and disparate systems led to inefficiencies, delays, and increased operational costs. To address these issues, XYZ Manufacturing Inc. decided to invest in a customized computer application tailored to its unique requirements. Development and Implementation: A cross-functional team consisting of IT specialists, supply chain experts, and key stakeholders was formed to develop the computer application. The application aimed to integrate various supply chain functions, providing real-time visibility into inventory levels, order status, and shipment tracking. Key features of the computer application included: Inventory Management: A centralized system for tracking and managing inventory levels across multiple warehouses, reducing the risk of stockouts and overstock situations. Order Processing: Automated order processing to streamline the fulfillment process, minimizing errors and expediting order-to-delivery timelines. Logistics Coordination: Integration with logistics partners to facilitate seamless communication and coordination, ensuring timely and cost-effective transportation of goods. Data Analytics: Robust analytics capabilities to generate actionable insights, helping in demand forecasting, identifying trends, and optimizing overall supply chain performance. Results: After the successful implementation of the computer application, XYZ Manufacturing Inc. experienced significant improvements in its supply chain efficiency. The company witnessed: Reduction in Operational Costs: Automation and streamlined processes led to a decrease in manual errors and operational costs. Improved Customer Satisfaction: Faster order processing and accurate inventory management contributed to enhanced customer satisfaction. Optimized Inventory Levels: Real-time visibility into inventory levels allowed for better demand planning, reducing excess stock and minimizing stockouts. Enhanced Decision-Making: Data analytics provided valuable insights, enabling the company to make informed decisions and adapt to market changes promptly. Conclusion: The custom computer application proved to be a game-changer for XYZ Manufacturing Inc., transforming its supply chain management and positioning the company for sustained growth in a competitive market. Objective Type Question: What key benefits did XYZ Manufacturing Inc. experience after implementing the custom computer application for supply chain management? A. Increased manual errors and operational costs. B. Longer order-to-delivery timelines. C. Decreased stockouts and optimized inventory levels. D. Limited visibility into inventory across warehouses.
Purchasing and Supply Chain Management
6th Edition
ISBN:9781285869681
Author:Robert M. Monczka, Robert B. Handfield, Larry C. Giunipero, James L. Patterson
Publisher:Robert M. Monczka, Robert B. Handfield, Larry C. Giunipero, James L. Patterson
ChapterC: Cases
Section: Chapter Questions
Problem 5.3SD: Scenario 4 Sharon Gillespie, a new buyer at Visionex, Inc., was reviewing quotations for a tooling...
Related questions
Question
Case Study: Optimizing Supply Chain Management with a Custom Computer Application
Introduction: In the dynamic landscape of modern business, efficient supply chain management is crucial for organizations aiming to stay competitive and meet customer demands. This case study explores the implementation of a custom computer application designed to optimize supply chain processes for a global manufacturing company, XYZ Manufacturing Inc.
Background: XYZ Manufacturing Inc. operates in a highly competitive market with a diverse range of products. The company faced challenges in managing its complex supply chain, including inventory control, order processing, and logistics coordination. Manual processes and disparate systems led to inefficiencies, delays, and increased operational costs. To address these issues, XYZ Manufacturing Inc. decided to invest in a customized computer application tailored to its unique requirements.
Development and Implementation: A cross-functional team consisting of IT specialists, supply chain experts, and key stakeholders was formed to develop the computer application. The application aimed to integrate various supply chain functions, providing real-time visibility into inventory levels, order status, and shipment tracking.
Key features of the computer application included:
Inventory Management: A centralized system for tracking and managing inventory levels across multiple warehouses, reducing the risk of stockouts and overstock situations.
Order Processing: Automated order processing to streamline the fulfillment process, minimizing errors and expediting order-to-delivery timelines.
Logistics Coordination: Integration with logistics partners to facilitate seamless communication and coordination, ensuring timely and cost-effective transportation of goods.
Data Analytics: Robust analytics capabilities to generate actionable insights, helping in demand forecasting , identifying trends, and optimizing overall supply chain performance.
Results: After the successful implementation of the computer application, XYZ Manufacturing Inc. experienced significant improvements in its supply chain efficiency. The company witnessed:
Reduction in Operational Costs: Automation and streamlined processes led to a decrease in manual errors and operational costs.
Improved Customer Satisfaction: Faster order processing and accurate inventory management contributed to enhanced customer satisfaction.
Optimized Inventory Levels: Real-time visibility into inventory levels allowed for better demand planning, reducing excess stock and minimizing stockouts.
Enhanced Decision-Making: Data analytics provided valuable insights, enabling the company to make informed decisions and adapt to market changes promptly.
Conclusion: The custom computer application proved to be a game-changer for XYZ Manufacturing Inc., transforming its supply chain management and positioning the company for sustained growth in a competitive market.
Objective Type Question: What key benefits did XYZ Manufacturing Inc. experience after implementing the custom computer application for supply chain management?
A. Increased manual errors and operational costs.
B. Longer order-to-delivery timelines.
C. Decreased stockouts and optimized inventory levels.
D. Limited visibility into inventory across warehouses.
Expert Solution

This question has been solved!
Explore an expertly crafted, step-by-step solution for a thorough understanding of key concepts.
Step by step
Solved in 4 steps

Knowledge Booster
Learn more about
Need a deep-dive on the concept behind this application? Look no further. Learn more about this topic, operations-management and related others by exploring similar questions and additional content below.Recommended textbooks for you
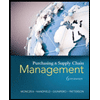
Purchasing and Supply Chain Management
Operations Management
ISBN:
9781285869681
Author:
Robert M. Monczka, Robert B. Handfield, Larry C. Giunipero, James L. Patterson
Publisher:
Cengage Learning
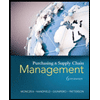
Purchasing and Supply Chain Management
Operations Management
ISBN:
9781285869681
Author:
Robert M. Monczka, Robert B. Handfield, Larry C. Giunipero, James L. Patterson
Publisher:
Cengage Learning