1. Boilers are used in most chemical plants to generate steam for various purposes, such as to preheat process streams fed to reactors and separation units. In one such process, steam and a cold process fluid are fed to a heat exchanger where enough energy is transferred from the steam to cause a large fraction of it to condense. The uncondensed steam is vented to the atmosphere, and the liquid condensate is recycled to a deaerator into which another liquid stream (makeup water) is fed. The makeup water contains some dissolved impurities and other chemicals that help prevent deposition of solids on boiler walls and heating elements, which would lead to a reduction in operating efficiency and eventually to safety hazards, possibly including explosions. The liquid leaving the deaerator is the feed to the boiler. In the boiler, most of the water in the feed evaporates to form steam, and some of the impurities in the feedwater precipitate to form solid particles suspended in the liquid (kept in suspension by the chemical additives in the makeup water). The liquid and suspended solids are drawn off as boiler blowdown, either in manual bursts or with a continuous blowdown system. A diagram of the system is shown below. The symbol I is used for combined impurities and chemical additives. The makeup water contains 1.0 kg 1/2.0 × 103 kg H2O, and the ratio in the blowdown is 1.0 kg I/3.5 x 102 kg H2O. Of the steam fed to the heat exchanger, 76% is condensed. Blowdown Lost steam I kg I(aq+s)/3.5x10 kg H,0 H,O(v) Heat Process Boiler feedwater I(aq), H,O() fluid, T Steam H,O(v) НЕАТ DEAERATOR BOILER EXCHANGER Makeup water 1.0 kg I/ 2.0x10 kg H,O((1) T2 Condensate, H,0(1) 76% of steam entering exchanger (a) In your own words, describe why makeup water, chemical additives to the makeup water, and blowdown are necessary in this process Speculate on the probable Condensate, H,0(1) 76% of steam entering exchanger (a) In your own words, describe why makeup water, chemical additives to the makeup water, and blowdown are necessary in this process. Speculate on the probable disadvantage of making the I/H2O ratio in the blowdown (i) too small, and (ii) too large. (b) Assume a basis of calculation and draw and fully label a flowchart of the process. (When you draw the heat exchanger you can omit the process fluid, which plays no role in the problem.) mixing point, the reactor, and the separation process. Base the analyses for reactive systems on atomic balances. (b) Write and solve overall balances, and then scale the process to calculate the flow rate (SCM/h) of fresh feed required to produce 1000 kg CNT/h and the mass flow rate of CO2 that would be produced. (c) In your degree-of-freedom analysis of the reactor, you might have counted separate balances for C (atomic carbon) and O (atomic oxygen). In fact, those two balances are not independent, so one but not both of them should be counted. Revise your analysis if necessary, and then calculate the ratio (kmol CO recycled/kmol CO in fresh feed). (d) Prove that the atomic carbon and oxygen balances on the reactor are not independent equations.
1. Boilers are used in most chemical plants to generate steam for various purposes, such as to preheat process streams fed to reactors and separation units. In one such process, steam and a cold process fluid are fed to a heat exchanger where enough energy is transferred from the steam to cause a large fraction of it to condense. The uncondensed steam is vented to the atmosphere, and the liquid condensate is recycled to a deaerator into which another liquid stream (makeup water) is fed. The makeup water contains some dissolved impurities and other chemicals that help prevent deposition of solids on boiler walls and heating elements, which would lead to a reduction in operating efficiency and eventually to safety hazards, possibly including explosions. The liquid leaving the deaerator is the feed to the boiler. In the boiler, most of the water in the feed evaporates to form steam, and some of the impurities in the feedwater precipitate to form solid particles suspended in the liquid (kept in suspension by the chemical additives in the makeup water). The liquid and suspended solids are drawn off as boiler blowdown, either in manual bursts or with a continuous blowdown system. A diagram of the system is shown below. The symbol I is used for combined impurities and chemical additives. The makeup water contains 1.0 kg 1/2.0 × 103 kg H2O, and the ratio in the blowdown is 1.0 kg I/3.5 x 102 kg H2O. Of the steam fed to the heat exchanger, 76% is condensed. Blowdown Lost steam I kg I(aq+s)/3.5x10 kg H,0 H,O(v) Heat Process Boiler feedwater I(aq), H,O() fluid, T Steam H,O(v) НЕАТ DEAERATOR BOILER EXCHANGER Makeup water 1.0 kg I/ 2.0x10 kg H,O((1) T2 Condensate, H,0(1) 76% of steam entering exchanger (a) In your own words, describe why makeup water, chemical additives to the makeup water, and blowdown are necessary in this process Speculate on the probable Condensate, H,0(1) 76% of steam entering exchanger (a) In your own words, describe why makeup water, chemical additives to the makeup water, and blowdown are necessary in this process. Speculate on the probable disadvantage of making the I/H2O ratio in the blowdown (i) too small, and (ii) too large. (b) Assume a basis of calculation and draw and fully label a flowchart of the process. (When you draw the heat exchanger you can omit the process fluid, which plays no role in the problem.) mixing point, the reactor, and the separation process. Base the analyses for reactive systems on atomic balances. (b) Write and solve overall balances, and then scale the process to calculate the flow rate (SCM/h) of fresh feed required to produce 1000 kg CNT/h and the mass flow rate of CO2 that would be produced. (c) In your degree-of-freedom analysis of the reactor, you might have counted separate balances for C (atomic carbon) and O (atomic oxygen). In fact, those two balances are not independent, so one but not both of them should be counted. Revise your analysis if necessary, and then calculate the ratio (kmol CO recycled/kmol CO in fresh feed). (d) Prove that the atomic carbon and oxygen balances on the reactor are not independent equations.
Introduction to Chemical Engineering Thermodynamics
8th Edition
ISBN:9781259696527
Author:J.M. Smith Termodinamica en ingenieria quimica, Hendrick C Van Ness, Michael Abbott, Mark Swihart
Publisher:J.M. Smith Termodinamica en ingenieria quimica, Hendrick C Van Ness, Michael Abbott, Mark Swihart
Chapter1: Introduction
Section: Chapter Questions
Problem 1.1P
Related questions
Question
Please do last 3 parts if possible

Transcribed Image Text:1. Boilers are used in most chemical plants to generate steam for various purposes, such
as to preheat process streams fed to reactors and separation units. In one such process,
steam and a cold process fluid are fed to a heat exchanger where enough energy is
transferred from the steam to cause a large fraction of it to condense. The uncondensed
steam is vented to the atmosphere, and the liquid condensate is recycled to a deaerator
into which another liquid stream (makeup water) is fed. The makeup water contains some
dissolved impurities and other chemicals that help prevent deposition of solids on boiler
walls and heating elements, which would lead to a reduction in operating efficiency and
eventually to safety hazards, possibly including explosions. The liquid leaving the
deaerator is the feed to the boiler. In the boiler, most of the water in the feed evaporates
to form steam, and some of the impurities in the feedwater precipitate to form solid
particles suspended in the liquid (kept in suspension by the chemical additives in the
makeup water). The liquid and suspended solids are drawn off as boiler blowdown, either
in manual bursts or with a continuous blowdown system.
A diagram of the system is shown below. The symbol I is used for combined
impurities and chemical additives. The makeup water contains 1.0 kg 1/2.0 × 103 kg H2O,
and the ratio in the blowdown is 1.0 kg I/3.5 x 102 kg H2O. Of the steam fed to the heat
exchanger, 76% is condensed.
Blowdown
Lost steam
I kg I(aq+s)/3.5x10 kg
H,0
H,O(v)
Heat
Process
Boiler
feedwater
I(aq), H,O()
fluid, T
Steam
H,O(v)
НЕАТ
DEAERATOR
BOILER
EXCHANGER
Makeup water
1.0 kg I/
2.0x10 kg H,O((1)
T2
Condensate, H,0(1)
76% of steam entering exchanger
(a) In your own words, describe why makeup water, chemical additives to the makeup
water, and blowdown are necessary in this process Speculate on the probable

Transcribed Image Text:Condensate, H,0(1)
76% of steam entering exchanger
(a) In your own words, describe why makeup water, chemical additives to the makeup
water, and blowdown are necessary in this process. Speculate on the probable
disadvantage of making the I/H2O ratio in the blowdown (i) too small, and (ii) too
large.
(b) Assume a basis of calculation and draw and fully label a flowchart of the process.
(When you draw the heat exchanger you can omit the process fluid, which plays
no role in the problem.)
mixing point, the reactor, and the separation process. Base the analyses for
reactive systems on atomic balances.
(b) Write and solve overall balances, and then scale the process to calculate the flow
rate (SCM/h) of fresh feed required to produce 1000 kg CNT/h and the mass flow
rate of CO2 that would be produced.
(c) In your degree-of-freedom analysis of the reactor, you might have counted
separate balances for C (atomic carbon) and O (atomic oxygen). In fact, those two
balances are not independent, so one but not both of them should be counted.
Revise your analysis if necessary, and then calculate the ratio (kmol CO
recycled/kmol CO in fresh feed).
(d) Prove that the atomic carbon and oxygen balances on the reactor are not
independent equations.
Expert Solution

This question has been solved!
Explore an expertly crafted, step-by-step solution for a thorough understanding of key concepts.
This is a popular solution!
Trending now
This is a popular solution!
Step by step
Solved in 3 steps with 1 images

Recommended textbooks for you
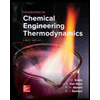
Introduction to Chemical Engineering Thermodynami…
Chemical Engineering
ISBN:
9781259696527
Author:
J.M. Smith Termodinamica en ingenieria quimica, Hendrick C Van Ness, Michael Abbott, Mark Swihart
Publisher:
McGraw-Hill Education
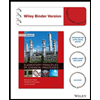
Elementary Principles of Chemical Processes, Bind…
Chemical Engineering
ISBN:
9781118431221
Author:
Richard M. Felder, Ronald W. Rousseau, Lisa G. Bullard
Publisher:
WILEY
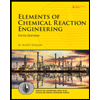
Elements of Chemical Reaction Engineering (5th Ed…
Chemical Engineering
ISBN:
9780133887518
Author:
H. Scott Fogler
Publisher:
Prentice Hall
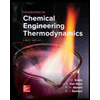
Introduction to Chemical Engineering Thermodynami…
Chemical Engineering
ISBN:
9781259696527
Author:
J.M. Smith Termodinamica en ingenieria quimica, Hendrick C Van Ness, Michael Abbott, Mark Swihart
Publisher:
McGraw-Hill Education
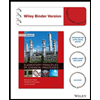
Elementary Principles of Chemical Processes, Bind…
Chemical Engineering
ISBN:
9781118431221
Author:
Richard M. Felder, Ronald W. Rousseau, Lisa G. Bullard
Publisher:
WILEY
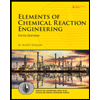
Elements of Chemical Reaction Engineering (5th Ed…
Chemical Engineering
ISBN:
9780133887518
Author:
H. Scott Fogler
Publisher:
Prentice Hall
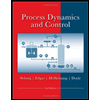
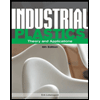
Industrial Plastics: Theory and Applications
Chemical Engineering
ISBN:
9781285061238
Author:
Lokensgard, Erik
Publisher:
Delmar Cengage Learning
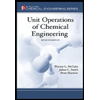
Unit Operations of Chemical Engineering
Chemical Engineering
ISBN:
9780072848236
Author:
Warren McCabe, Julian C. Smith, Peter Harriott
Publisher:
McGraw-Hill Companies, The