How can we apply these operation management concepts to the current operations of a college, which has a major direct impact of the covid currently. What are the five recommended ways that a college can improve thier operations based on the concepts. The operation management concepts are attached below. Please blur the attached file when publishing to the public. Appreciate it.
How can we apply these operation management concepts to the current operations of a college, which has a major direct impact of the covid currently. What are the five recommended ways that a college can improve thier operations based on the concepts. The operation management concepts are attached below. Please blur the attached file when publishing to the public. Appreciate it.
Practical Management Science
6th Edition
ISBN:9781337406659
Author:WINSTON, Wayne L.
Publisher:WINSTON, Wayne L.
Chapter2: Introduction To Spreadsheet Modeling
Section: Chapter Questions
Problem 20P: Julie James is opening a lemonade stand. She believes the fixed cost per week of running the stand...
Related questions
Question
100%
Looking for answers. Thanks!
How can we apply these operation management concepts to the current operations of a college, which has a major direct impact of the covid currently. What are the five recommended ways that a college can improve thier operations based on the concepts.
The operation management concepts are attached below. Please blur the attached file when publishing to the public. Appreciate it.
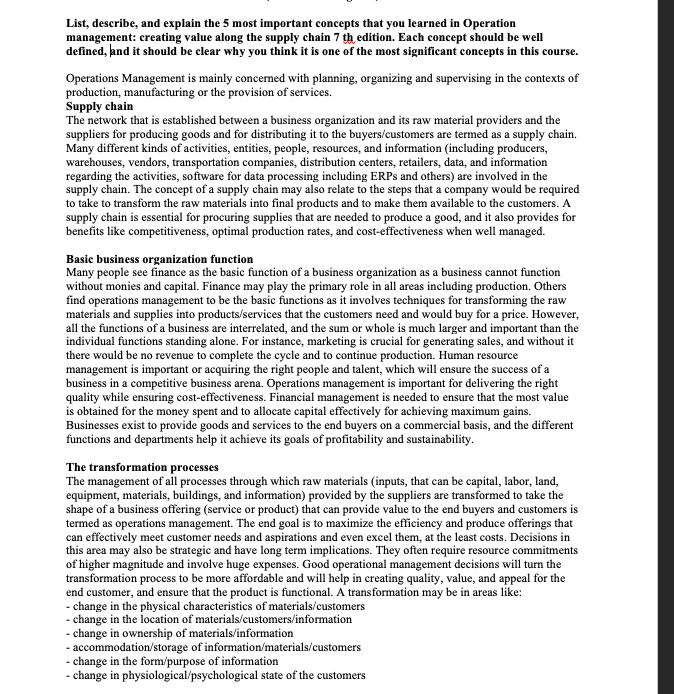
Transcribed Image Text:List, describe, and explain the 5 most important concepts that you learned in Operation
management: creating value along the supply chain 7 th edition. Each concept should be well
defined, and it should be clear why you thỉnk it is one of the most significant concepts in this course.
Operations Management is mainly concerned with planning, organizing and supervising in the contexts of
production, manufacturing or the provision of services.
Supply chain
The network that is established between a business organization and its raw material providers and the
suppliers for producing goods and for distributing it to the buyers/customers are termed as a supply chain.
Many different kinds of activities, entities, people, resources, and information (including producers,
warehouses, vendors, transportation companies, distribution centers, retailers, data, and information
regarding the activities, software for data processing including ERPS and others) are involved in the
supply chain. The concept of a supply chain may also relate to the steps that a company would be required
to take to transform the raw materials into final products and to make them available to the customers. A
supply chain is essential for procuring supplies that are needed to produce a good, and it also provides for
benefits like competitiveness, optimal production rates, and cost-effectiveness when well managed.
Basic business organization function
Many people see finance as the basic function of a business organization as a business cannot function
without monies and capital. Finance may play the primary role in all areas including production. Others
find operations management to be the basic functions as it involves techniques for transforming the raw
materials and supplies into products/services that the customers need and would buy for a price. However,
all the functions of a business are interrelated, and the sum or whole is much larger and important than the
individual functions standing alone. For instance, marketing is crucial for generating sales, and without it
there would be no revenue to complete the cycle and to continue production. Human resource
management is important or acquiring the right people and talent, which will ensure the success of a
business in a competitive business arena. Operations management is important for delivering the right
quality while ensuring cost-effectiveness. Financial management is needed to ensure that the most value
is obtained for the money spent and to allocate capital effectively for achieving maximum gains.
Businesses exist to provide goods and services to the end buyers on a commercial basis, and the different
functions and departments help it achieve its goals of profitability and sustainability.
The transformation processes
The management of all processes through which raw materials (inputs, that can be capital, labor, land,
equipment, materials, buildings, and information) provided by the suppliers are transformed to take the
shape of a business offering (service or product) that can provide value to the end buyers and customers is
termed as operations management. The end goal is to maximize the efficiency and produce offerings that
can effectively meet customer needs and aspirations and even excel them, at the least costs. Decisions in
this area may also be strategic and have long term implications. They often require resource commitments
of higher magnitude and involve huge expenses. Good operational management decisions will turn the
transformation process to be more affordable and will help in creating quality, value, and appeal for the
end customer, and ensure that the product is functional. A transformation may be in areas like:
- change in the physical characteristics of materials/customers
- change in the location of materials/customers/information
- change in ownership of materials/information
- accommodation/storage of information/materials/customers
- change in the form/purpose of information
- change in physiological/psychological state of the customers
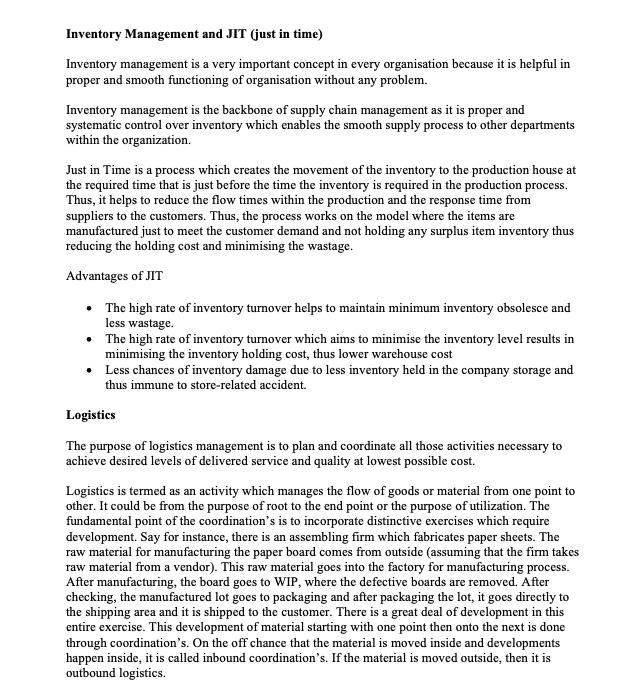
Transcribed Image Text:Inventory Management and JIT (just in time)
Inventory management is a very important concept in every organisation because it is helpful in
proper and smooth functioning of organisation without any problem.
Inventory management is the backbone of supply chain management as it is proper and
systematic control over inventory which enables the smooth supply process to other departments
within the organization.
Just in Time is a process which creates the movement of the inventory to the production house at
the required time that is just before the time the inventory is required in the production process.
Thus, it helps to reduce the flow times within the production and the response time from
suppliers to the customers. Thus, the process works on the model where the items are
manufactured just to meet the customer demand and not holding any surplus item inventory thus
reducing the holding cost and minimising the wastage.
Advantages of JIT
• The high rate of inventory turnover helps to maintain minimum inventory obsolesce and
less wastage.
• The high rate of inventory turnover which aims to minimise the inventory level results in
minimising the inventory holding cost, thus lower warehouse cost
• Less chances of inventory damage due to less inventory held in the company storage and
thus immune to store-related accident.
Logistics
The purpose of logistics management is to plan and coordinate all those activities necessary to
achieve desired levels of delivered service and quality at lowest possible cost.
Logistics is termed as an activity which manages the flow of goods or material from one point to
other. It could be from the purpose of root to the end point or the purpose of utilization. The
fundamental point of the coordination's is to incorporate distinctive exercises which require
development. Say for instance, there is an assembling firm which fabricates paper sheets. The
raw material for manufacturing the paper board comes from outside (assuming that the firm takes
raw material from a vendor). This raw material goes into the factory for manufacturing process.
After manufacturing, the board goes to WIP, where the defective boards are removed. After
checking, the manufactured lot goes to packaging and after packaging the lot, it goes directly to
the shipping area and it is shipped to the customer. There is a great deal of development in this
entire exercise. This development of material starting with one point then onto the next is done
through coordination's. On the off chance that the material is moved inside and developments
happen inside, it is called inbound coordination's. If the material is moved outside, then it is
outbound logistics.
Expert Solution

This question has been solved!
Explore an expertly crafted, step-by-step solution for a thorough understanding of key concepts.
Step by step
Solved in 2 steps

Knowledge Booster
Learn more about
Need a deep-dive on the concept behind this application? Look no further. Learn more about this topic, operations-management and related others by exploring similar questions and additional content below.Recommended textbooks for you
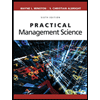
Practical Management Science
Operations Management
ISBN:
9781337406659
Author:
WINSTON, Wayne L.
Publisher:
Cengage,
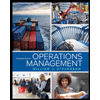
Operations Management
Operations Management
ISBN:
9781259667473
Author:
William J Stevenson
Publisher:
McGraw-Hill Education
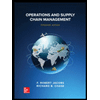
Operations and Supply Chain Management (Mcgraw-hi…
Operations Management
ISBN:
9781259666100
Author:
F. Robert Jacobs, Richard B Chase
Publisher:
McGraw-Hill Education
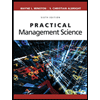
Practical Management Science
Operations Management
ISBN:
9781337406659
Author:
WINSTON, Wayne L.
Publisher:
Cengage,
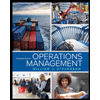
Operations Management
Operations Management
ISBN:
9781259667473
Author:
William J Stevenson
Publisher:
McGraw-Hill Education
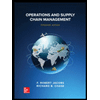
Operations and Supply Chain Management (Mcgraw-hi…
Operations Management
ISBN:
9781259666100
Author:
F. Robert Jacobs, Richard B Chase
Publisher:
McGraw-Hill Education
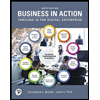
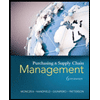
Purchasing and Supply Chain Management
Operations Management
ISBN:
9781285869681
Author:
Robert M. Monczka, Robert B. Handfield, Larry C. Giunipero, James L. Patterson
Publisher:
Cengage Learning
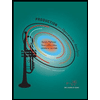
Production and Operations Analysis, Seventh Editi…
Operations Management
ISBN:
9781478623069
Author:
Steven Nahmias, Tava Lennon Olsen
Publisher:
Waveland Press, Inc.