SCENARIO A steel-working organisation operates 30 steel-working plants globally, including a plant located on the outskirts of a large town, where you are employed. This steelworks contains many different workshops that cover the whole steel-producing process. This involves repair, maintenance, fabrication and welding of large steel structures. Within the fabrication and welding workshop an overhead crane is used to move heavy steel into position. There are signs on this crane stating that only trained workers can operate it. Workers understand that manual handling and mechanical lifting aids should be considered first, with the crane only used as a last resort. The workforce consists of 20 workers. These include a general workshop manager (GWM) and 2 workshop supervisors. There are also 3 apprentices, who are not trained in the use of the crane. In your new role, you work in the fabrication and welding department as the Health and Safety Manager, reporting to the GWM. The GWM does not believe that they should be responsible for health and safety, and they do not have time for it. They welcome the fact that you are taking on this role and acknowledge that you have recently started to study the NEBOSH General Certificate. You have observed hazards such as scrap metal in walkways. This sometimes forces workers to step into the path of the overhead crane, while walking through the workshop. Because of these obstructed walkways workers often carry heavy objects instead of using mechanical aids. Workers inform you that there are frequent near misses, involving the overhead crane, when it is being operated by the apprentices. You find an email from one of the supervisors to the GWM requesting crane operation training for the apprentices, but this seems to have been ignored. There are no written records of any of these near misses. Workers have told you that they have complained to the GWM many times about the workshop working conditions. They have also informed the GWM that the crane operation alarm is not working. You cannot find any written records of such complaints. No-one represents the workers in raising health and safety concerns. The GWM is not interested in people moaning about insignificant issues; which makes workers believe their views are not heard. The GWM is only seen if something goes wrong. Workers tell you that the GWM wants tasks completed quickly and demands too much of them. The GWM knows that shortcuts are taken to achieve this. You start looking for different risk assessments, but only find one generic risk assessment. This lacks specific details and seems to focus on low-risk activities. It was completed three years ago. You try to convince the GWM that health and safety in the workshop needs prioritising. The GWM says that there is “no money for that kind of thing, and even if it were available, it would cause too much disruption to production”. There have been many injuries recorded over the years that have led to worker absences. Most recently, an apprentice was injured after being hit by a load suspended from an overhead crane. On one of the dedicated ground-level walkways, an apprentice was typing a message on their mobile phone, although they knew that the use of mobile phones was banned in the workshop. At the same time, an overhead crane, operated by another apprentice, was moving a steel beam. The apprentice, on the ground-level walkway, tripped on a trailing cable. This forced them to move outside of the dedicated walkway and into the path of the steel beam. Fortunately, they noticed the steel beam and bent down to avoid it, instinctively raising their arm. The beam struck their forearm, which caused them to fall onto some scrap metal. IG1_IGC1-0019-ENG-OBE-QP-V1 Oct22 © NEBOSH 2022 page 3 of 5 A first-aider attended the scene and said that the apprentice’s arm appeared to be broken. The first-aider also treated a deep cut on the apprentice’s leg. The first-aider reported this to one of the workshop supervisors, who then called for an ambulance. The hospital confirmed that the apprentice had broken their arm in several places and required an operation. They were expected to be off work for six to eight weeks to recover from the initial injuries. However, there were complications following surgery that extended their time off work. The apprentice, who operated the crane, was off work for one week due to post-traumatic stress. You talk to the GWM about the accident, they tell you to take no further action for now, and that an investigation will be carried out in a few weeks. Task 4: Management failures Based on the scenario only, what management failures could have contributed to this accident?
SCENARIO
A steel-working organisation operates 30 steel-working plants globally, including a plant located on the outskirts of a large town, where you are employed.
This steelworks contains many different workshops that cover the whole steel-producing process. This involves repair, maintenance, fabrication and welding of large steel structures.
Within the fabrication and welding workshop an overhead crane is used to move heavy steel into position. There are signs on this crane stating that only trained workers can operate it. Workers understand that manual handling and mechanical lifting aids should be considered first, with the crane only used as a last resort.
The workforce consists of 20 workers. These include a general workshop manager (GWM) and 2 workshop supervisors. There are also 3 apprentices, who are not trained in the use of the crane.
In your new role, you work in the fabrication and welding department as the Health and Safety Manager, reporting to the GWM. The GWM does not believe that they should be responsible for health and safety, and they do not have time for it. They welcome the fact that you are taking on this role and acknowledge that you have recently started to study the NEBOSH General Certificate.
You have observed hazards such as scrap metal in walkways. This sometimes forces workers to step into the path of the overhead crane, while walking through the workshop. Because of these obstructed walkways workers often carry heavy objects instead of using mechanical aids. Workers inform you that there are frequent near misses, involving the overhead crane, when it is being operated by the apprentices. You find an email from one of the supervisors to the GWM requesting crane operation training for the apprentices, but this seems to have been ignored.
There are no written records of any of these near misses. Workers have told you that they have complained to the GWM many times about the workshop working conditions. They have also informed the GWM that the crane operation alarm is not working. You cannot find any written records of such complaints.
No-one represents the workers in raising health and safety concerns. The GWM is not interested in people moaning about insignificant issues; which makes workers believe their views are not heard. The GWM is only seen if something goes wrong.
Workers tell you that the GWM wants tasks completed quickly and demands too much of them. The GWM knows that shortcuts are taken to achieve this.
You start looking for different risk assessments, but only find one generic risk assessment. This lacks specific details and seems to focus on low-risk activities. It was completed three years ago.
You try to convince the GWM that health and safety in the workshop needs prioritising. The GWM says that there is “no money for that kind of thing, and even if it were available, it would cause too much disruption to production”.
There have been many injuries recorded over the years that have led to worker absences. Most recently, an apprentice was injured after being hit by a load suspended from an overhead crane.
On one of the dedicated ground-level walkways, an apprentice was typing a message on their mobile phone, although they knew that the use of mobile phones was banned in the workshop. At the same time, an overhead crane, operated by another apprentice, was moving a steel beam. The apprentice, on the ground-level walkway, tripped on a trailing cable. This forced them to move outside of the dedicated walkway and into the path of the steel beam. Fortunately, they noticed the steel beam and bent down to avoid it, instinctively raising their arm. The beam struck their forearm, which caused them to fall onto some scrap metal.
IG1_IGC1-0019-ENG-OBE-QP-V1 Oct22 © NEBOSH 2022 page 3 of 5
A first-aider attended the scene and said that the apprentice’s arm appeared to be broken. The first-aider also treated a deep cut on the apprentice’s leg. The first-aider reported this to one of the workshop supervisors, who then called for an ambulance.
The hospital confirmed that the apprentice had broken their arm in several places and required an operation. They were expected to be off work for six to eight weeks to recover from the initial injuries. However, there were complications following surgery that extended their time off work.
The apprentice, who operated the crane, was off work for one week due to post-traumatic stress. You talk to the GWM about the accident, they tell you to take no further action for now, and that an investigation will be carried out in a few weeks.
Task 4: Management failures
Based on the scenario only, what management failures could have contributed to this accident?

Trending now
This is a popular solution!
Step by step
Solved in 2 steps

How could you notify the component authority about this accident
SCENARIO
A steel-working organisation operates 30 steel-working plants globally, including a plant located on the outskirts of a large town, where you are employed.
This steelworks contains many different workshops that cover the whole steel-producing process. This involves repair, maintenance, fabrication and welding of large steel structures.
Within the fabrication and welding workshop an overhead crane is used to move heavy steel into position. There are signs on this crane stating that only trained workers can operate it. Workers understand that manual handling and mechanical lifting aids should be considered first, with the crane only used as a last resort.
The workforce consists of 20 workers. These include a general workshop manager (GWM) and 2 workshop supervisors. There are also 3 apprentices, who are not trained in the use of the crane.
In your new role, you work in the fabrication and welding department as the Health and Safety Manager, reporting to the GWM. The GWM does not believe that they should be responsible for health and safety, and they do not have time for it. They welcome the fact that you are taking on this role and acknowledge that you have recently started to study the NEBOSH General Certificate.
You have observed hazards such as scrap metal in walkways. This sometimes forces workers to step into the path of the overhead crane, while walking through the workshop. Because of these obstructed walkways workers often carry heavy objects instead of using mechanical aids. Workers inform you that there are frequent near misses, involving the overhead crane, when it is being operated by the apprentices. You find an email from one of the supervisors to the GWM requesting crane operation training for the apprentices, but this seems to have been ignored.
There are no written records of any of these near misses. Workers have told you that they have complained to the GWM many times about the workshop working conditions. They have also informed the GWM that the crane operation alarm is not working. You cannot find any written records of such complaints.
No-one represents the workers in raising health and safety concerns. The GWM is not interested in people moaning about insignificant issues; which makes workers believe their views are not heard. The GWM is only seen if something goes wrong.
Workers tell you that the GWM wants tasks completed quickly and demands too much of them. The GWM knows that shortcuts are taken to achieve this.
You start looking for different risk assessments, but only find one generic risk assessment. This lacks specific details and seems to focus on low-risk activities. It was completed three years ago.
You try to convince the GWM that health and safety in the workshop needs prioritising. The GWM says that there is “no money for that kind of thing, and even if it were available, it would cause too much disruption to production”.
There have been many injuries recorded over the years that have led to worker absences. Most recently, an apprentice was injured after being hit by a load suspended from an overhead crane.
On one of the dedicated ground-level walkways, an apprentice was typing a message on their mobile phone, although they knew that the use of mobile phones was banned in the workshop. At the same time, an overhead crane, operated by another apprentice, was moving a steel beam. The apprentice, on the ground-level walkway, tripped on a trailing cable. This forced them to move outside of the dedicated walkway and into the path of the steel beam. Fortunately, they noticed the steel beam and bent down to avoid it, instinctively raising their arm. The beam struck their forearm, which caused them to fall onto some scrap metal.
IG1_IGC1-0019-ENG-OBE-QP-V1 Oct22 © NEBOSH 2022 page 3 of 5
A first-aider attended the scene and said that the apprentice’s arm appeared to be broken. The first-aider also treated a deep cut on the apprentice’s leg. The first-aider reported this to one of the workshop supervisors, who then called for an ambulance.
The hospital confirmed that the apprentice had broken their arm in several places and required an operation. They were expected to be off work for six to eight weeks to recover from the initial injuries. However, there were complications following surgery that extended their time off work.
The apprentice, who operated the crane, was off work for one week due to post-traumatic stress. You talk to the GWM about the accident, they tell you to take no further action for now, and that an investigation will be carried out in a few weeks.
Task 9: Training 9 You have decided to compile an induction pack for new apprentices. Based on the scenario only, what information should you prioritise in this induction pack?
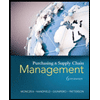
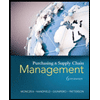