A mixture containing 65.0 mole % acetone (A) and the balance acetic acid (AA) is separated in a continuous distillation column at 1 atm. Condenser Top Product 3 Feed 1 6 Bottom Product Reboiler The stream from the top of the column is a vapor that passes though a condenser. The condensed liquid is divided into two equal streams: one is taken off as the overhead product (distillate) and the other (the reflux) is returned to the column. The stream from the bottom of the column is a liquid that is partially vaporized in a reboiler. The liquid stream emerging from the reboiler is taken off as the bottoms product, and the vapor is returned to the column as boilup. Negligible heat is lost from the column, so that the only places in the system where external heat transfer takes place are the condenser and the reboiler. The conditions of the stream are as follows: Stream No. Stream State Liquid, 67.5°C, 65 mole% A, 35% AA Vapor, 63.0°C, 98 mole% A, 2% AA Liquid, 56.8°C, 98 mole% A, 2% AA Liquid, 56.8°C, 98 mole% A, 2% AA Liquid, 98.7°C, 15.5 mole% A, 84.5% AA Vapor, 98.7°C, 54.4 mole% A, 45.6% AA 2 3 4 For this system, the following thermodynamic data is available (the units of the specific enthalpy are cal/mole): Acetone Acetic Acid T°C H1 Hv 56.8 7205 5723 63.0 205 7322 194 6807 67.5 354 7403 335 6884 98.7 1385 7946 1312 7420 (a) Taking 100 mol of feed as a basis, calculate the net heat requirement (cal) for the process. (You may neglect heats of mixing, although doing so for dissimilar liquids like acetone and acetic acid may introduce some error.) (b) For the same basis, calculate the required heat input to the reboiler and the required heat removal from the condenser. (c) Suppose that instead of the condensed liquid from the top of column being split into two equal streams to form the reflux and the overhead product, it is split into two streams, with the reflux being 3 times the overhead product. As before, take a basis of 100 mol of feed and determine the net heating requirements (cal) for the process and the heat removed in the condenser and added in the reboiler.
A mixture containing 65.0 mole % acetone (A) and the balance acetic acid (AA) is separated in a continuous distillation column at 1 atm. Condenser Top Product 3 Feed 1 6 Bottom Product Reboiler The stream from the top of the column is a vapor that passes though a condenser. The condensed liquid is divided into two equal streams: one is taken off as the overhead product (distillate) and the other (the reflux) is returned to the column. The stream from the bottom of the column is a liquid that is partially vaporized in a reboiler. The liquid stream emerging from the reboiler is taken off as the bottoms product, and the vapor is returned to the column as boilup. Negligible heat is lost from the column, so that the only places in the system where external heat transfer takes place are the condenser and the reboiler. The conditions of the stream are as follows: Stream No. Stream State Liquid, 67.5°C, 65 mole% A, 35% AA Vapor, 63.0°C, 98 mole% A, 2% AA Liquid, 56.8°C, 98 mole% A, 2% AA Liquid, 56.8°C, 98 mole% A, 2% AA Liquid, 98.7°C, 15.5 mole% A, 84.5% AA Vapor, 98.7°C, 54.4 mole% A, 45.6% AA 2 3 4 For this system, the following thermodynamic data is available (the units of the specific enthalpy are cal/mole): Acetone Acetic Acid T°C H1 Hv 56.8 7205 5723 63.0 205 7322 194 6807 67.5 354 7403 335 6884 98.7 1385 7946 1312 7420 (a) Taking 100 mol of feed as a basis, calculate the net heat requirement (cal) for the process. (You may neglect heats of mixing, although doing so for dissimilar liquids like acetone and acetic acid may introduce some error.) (b) For the same basis, calculate the required heat input to the reboiler and the required heat removal from the condenser. (c) Suppose that instead of the condensed liquid from the top of column being split into two equal streams to form the reflux and the overhead product, it is split into two streams, with the reflux being 3 times the overhead product. As before, take a basis of 100 mol of feed and determine the net heating requirements (cal) for the process and the heat removed in the condenser and added in the reboiler.
Introduction to Chemical Engineering Thermodynamics
8th Edition
ISBN:9781259696527
Author:J.M. Smith Termodinamica en ingenieria quimica, Hendrick C Van Ness, Michael Abbott, Mark Swihart
Publisher:J.M. Smith Termodinamica en ingenieria quimica, Hendrick C Van Ness, Michael Abbott, Mark Swihart
Chapter1: Introduction
Section: Chapter Questions
Problem 1.1P
Related questions
Question
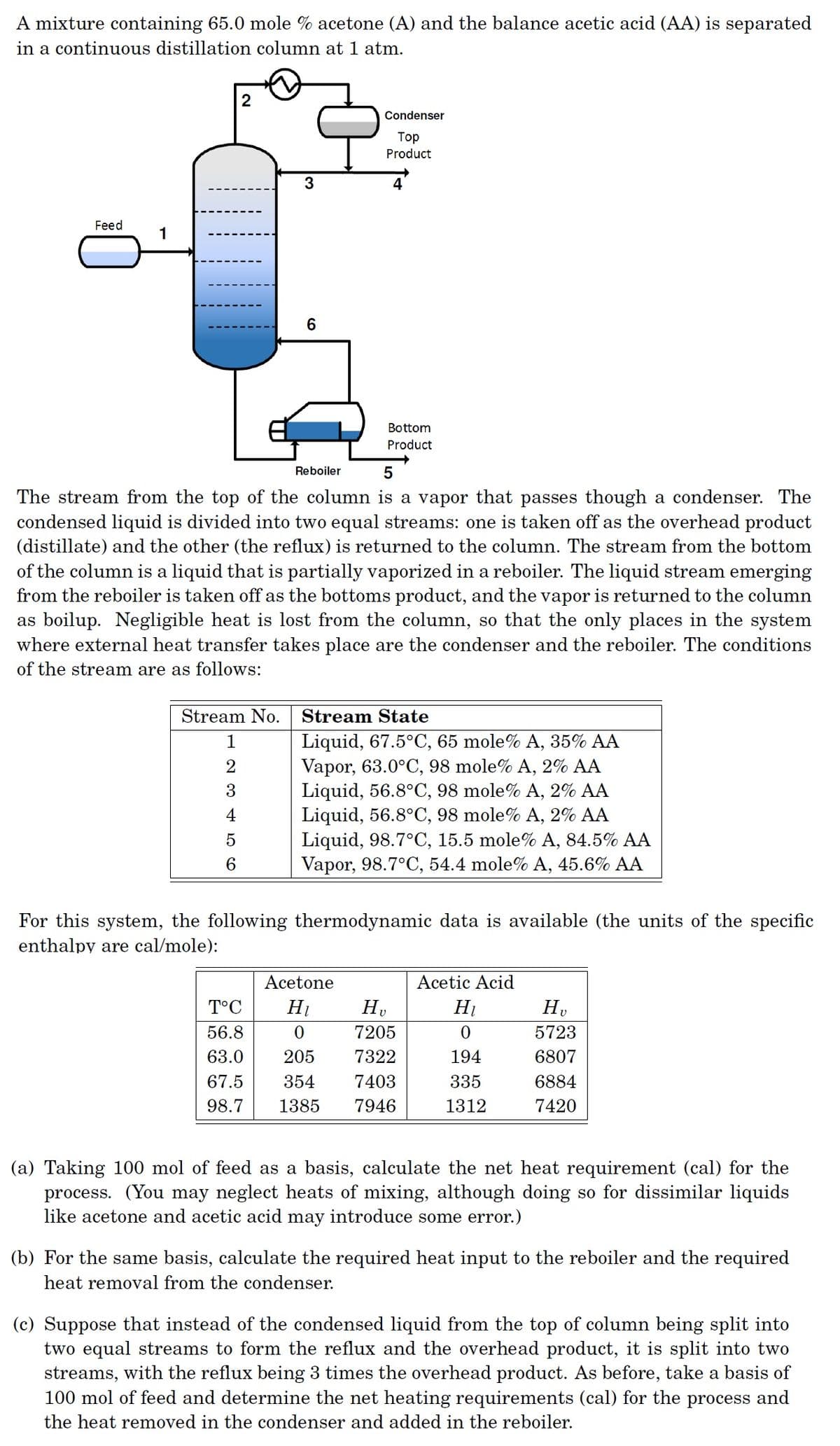
Transcribed Image Text:A mixture containing 65.0 mole % acetone (A) and the balance acetic acid (AA) is separated
in a continuous distillation column at 1 atm.
Condenser
Тоp
Product
3
Feed
1
6
Bottom
Product
Reboiler
The stream from the top of the column is a vapor that passes though a condenser. The
condensed liquid is divided into two equal streams: one is taken off as the overhead product
(distillate) and the other (the reflux) is returned to the column. The stream from the bottom
of the column is a liquid that is partially vaporized in a reboiler. The liquid stream emerging
from the reboiler is taken off as the bottoms product, and the vapor is returned to the column
as boilup. Negligible heat is lost from the column, so that the only places in the system
where external heat transfer takes place are the condenser and the reboiler. The conditions
of the stream are as follows:
Stream No.
Stream State
Liquid, 67.5°C, 65 mole% A, 35% AA
Vapor, 63.0°C, 98 mole% A, 2% AA
Liquid, 56.8°C, 98 mole% A, 2% AA
Liquid, 56.8°C, 98 mole% A, 2% AA
Liquid, 98.7°C, 15.5 mole% A, 84.5% AA
Vapor, 98.7°C, 54.4 mole% A, 45.6% AA
3
4
6.
For this system, the following thermodynamic data is available (the units of the specific
enthalpy are cal/mole):
Acetone
Acetic Acid
T°C
H1
Hi
56.8
7205
5723
63.0
205
7322
194
6807
67.5
354
7403
335
6884
98.7
1385
7946
1312
7420
(a) Taking 100 mol of feed as a basis, calculate the net heat requirement (cal) for the
process. (You may neglect heats of mixing, although doing so for dissimilar liquids
like acetone and acetic acid may introduce some error.)
(b) For the same basis, calculate the required heat input to the reboiler and the required
heat removal from the condenser.
(c) Suppose that instead of the condensed liquid from the top of column being split into
two equal streams to form the reflux and the overhead product, it is split into two
streams, with the reflux being 3 times the overhead product. As before, take a basis of
100 mol of feed and determine the net heating requirements (cal) for the process and
the heat removed in the condenser and added in the reboiler.
Expert Solution

This question has been solved!
Explore an expertly crafted, step-by-step solution for a thorough understanding of key concepts.
This is a popular solution!
Trending now
This is a popular solution!
Step by step
Solved in 7 steps

Knowledge Booster
Learn more about
Need a deep-dive on the concept behind this application? Look no further. Learn more about this topic, chemical-engineering and related others by exploring similar questions and additional content below.Recommended textbooks for you
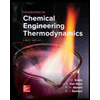
Introduction to Chemical Engineering Thermodynami…
Chemical Engineering
ISBN:
9781259696527
Author:
J.M. Smith Termodinamica en ingenieria quimica, Hendrick C Van Ness, Michael Abbott, Mark Swihart
Publisher:
McGraw-Hill Education
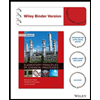
Elementary Principles of Chemical Processes, Bind…
Chemical Engineering
ISBN:
9781118431221
Author:
Richard M. Felder, Ronald W. Rousseau, Lisa G. Bullard
Publisher:
WILEY
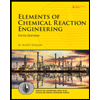
Elements of Chemical Reaction Engineering (5th Ed…
Chemical Engineering
ISBN:
9780133887518
Author:
H. Scott Fogler
Publisher:
Prentice Hall
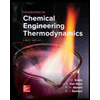
Introduction to Chemical Engineering Thermodynami…
Chemical Engineering
ISBN:
9781259696527
Author:
J.M. Smith Termodinamica en ingenieria quimica, Hendrick C Van Ness, Michael Abbott, Mark Swihart
Publisher:
McGraw-Hill Education
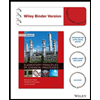
Elementary Principles of Chemical Processes, Bind…
Chemical Engineering
ISBN:
9781118431221
Author:
Richard M. Felder, Ronald W. Rousseau, Lisa G. Bullard
Publisher:
WILEY
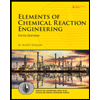
Elements of Chemical Reaction Engineering (5th Ed…
Chemical Engineering
ISBN:
9780133887518
Author:
H. Scott Fogler
Publisher:
Prentice Hall
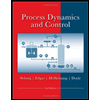
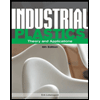
Industrial Plastics: Theory and Applications
Chemical Engineering
ISBN:
9781285061238
Author:
Lokensgard, Erik
Publisher:
Delmar Cengage Learning
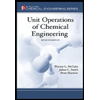
Unit Operations of Chemical Engineering
Chemical Engineering
ISBN:
9780072848236
Author:
Warren McCabe, Julian C. Smith, Peter Harriott
Publisher:
McGraw-Hill Companies, The