Analytics Exercise 21-1 (Algo) Recently, Phil Harris, the production control manager at Brunswick, read an article on time-phased requirements planning. He was curious about how this technique might work in scheduling Brunswick's engine assembly operations and decided to prepare an example to illustrate the use of time-phased requirements planning. Phil's first step was to prepare a master schedule for one of the engine types produced by Brunswick: the Model 1000 engine. This schedule indicates the number of units of the Model 1000 engine to be assembled each week during the last 12 weeks and is shown on the next page. Next, Phil decided to simplify his requirements planning example by considering only two of the many components that are needed to complete the assembly of the Model 1000 engine. These two components, the gear box and the input shaft, are shown in the product structure diagram below. Phil noted that the gear box is assembled by the Subassembly Department and subsequently is sent to the main engine assembly line. The input shaft is one of several component parts manufactured by Brunswick that are needed to produce a gear box subassembly. Thus, levels 0, 1, and 2 are included in the product structure diagram to indicate the three manufacturing stages that are involved in producing an engine: the Engine Assembly Department, the Subassembly Department, and the Machine Shop. The manufacturing lead times required to produce the gear box and input shaft components are also indicated in the product structure diagram. Note that two weeks are required to produce a batch of gear boxes and that all the gear boxes must be delivered to the assembly line parts stockroom before Monday morning of the week in which they are to be used. Likewise, it takes three weeks to produce a lot of input shafts, and all the shafts that are needed for the production of gear boxes in a given week must be delivered to the Subassembly Department stockroom before Monday morning of that week. In preparing the MRP example Phil planned to use the worksheets shown and to make the following assumptions: 1. Twenty two gear boxes are on hand at the beginning of Week 1, and eight gear boxes are currently on order to be delivered at the start of Week 2. 2. Forty five input shafts are on hand at the start of Week 1, and 25 are scheduled for delivery at the beginning of Week 2 Model 1000 master schedule Week 1 2 3 4 5 6 7 B 9 Demand 18 5 12 10 17 22 10 10 Crankcase Model 1000 product structure Engine assembly Gear box Lead time=2 weeks Used: 1 per engine Input shaft Lead time 3 weeks Used: 2 per gear box 10 10 6 1.1 12 5 20 20
Analytics Exercise 21-1 (Algo) Recently, Phil Harris, the production control manager at Brunswick, read an article on time-phased requirements planning. He was curious about how this technique might work in scheduling Brunswick's engine assembly operations and decided to prepare an example to illustrate the use of time-phased requirements planning. Phil's first step was to prepare a master schedule for one of the engine types produced by Brunswick: the Model 1000 engine. This schedule indicates the number of units of the Model 1000 engine to be assembled each week during the last 12 weeks and is shown on the next page. Next, Phil decided to simplify his requirements planning example by considering only two of the many components that are needed to complete the assembly of the Model 1000 engine. These two components, the gear box and the input shaft, are shown in the product structure diagram below. Phil noted that the gear box is assembled by the Subassembly Department and subsequently is sent to the main engine assembly line. The input shaft is one of several component parts manufactured by Brunswick that are needed to produce a gear box subassembly. Thus, levels 0, 1, and 2 are included in the product structure diagram to indicate the three manufacturing stages that are involved in producing an engine: the Engine Assembly Department, the Subassembly Department, and the Machine Shop. The manufacturing lead times required to produce the gear box and input shaft components are also indicated in the product structure diagram. Note that two weeks are required to produce a batch of gear boxes and that all the gear boxes must be delivered to the assembly line parts stockroom before Monday morning of the week in which they are to be used. Likewise, it takes three weeks to produce a lot of input shafts, and all the shafts that are needed for the production of gear boxes in a given week must be delivered to the Subassembly Department stockroom before Monday morning of that week. In preparing the MRP example Phil planned to use the worksheets shown and to make the following assumptions: 1. Twenty two gear boxes are on hand at the beginning of Week 1, and eight gear boxes are currently on order to be delivered at the start of Week 2. 2. Forty five input shafts are on hand at the start of Week 1, and 25 are scheduled for delivery at the beginning of Week 2 Model 1000 master schedule Week 1 2 3 4 5 6 7 B 9 Demand 18 5 12 10 17 22 10 10 Crankcase Model 1000 product structure Engine assembly Gear box Lead time=2 weeks Used: 1 per engine Input shaft Lead time 3 weeks Used: 2 per gear box 10 10 6 1.1 12 5 20 20
Practical Management Science
6th Edition
ISBN:9781337406659
Author:WINSTON, Wayne L.
Publisher:WINSTON, Wayne L.
Chapter2: Introduction To Spreadsheet Modeling
Section: Chapter Questions
Problem 20P: Julie James is opening a lemonade stand. She believes the fixed cost per week of running the stand...
Related questions
Question
A initially assume that Phi wants to minimize his inventory requirements. Assume that each order will be only for what is required for a single period. Calculate the net requirements and planned order releases for the gear boxes and input shafts. Assume that lot sizing is done using a lot-for-lot (L4L).
Gear box requirements
Week 1 2 3 4 5 6 7 8 9 10 11 12
Gross requirements
Scheduled receipts
Projected available balance
Net requirements
Planned order receipt
Planned order release
Input shaft requirements
Week 1 2 3 4 5 6 7 8 9 10 11 12
Gross requirements
Scheduled receipts
Projected available balance
Net requirements
Planned order receipt
Planned order release
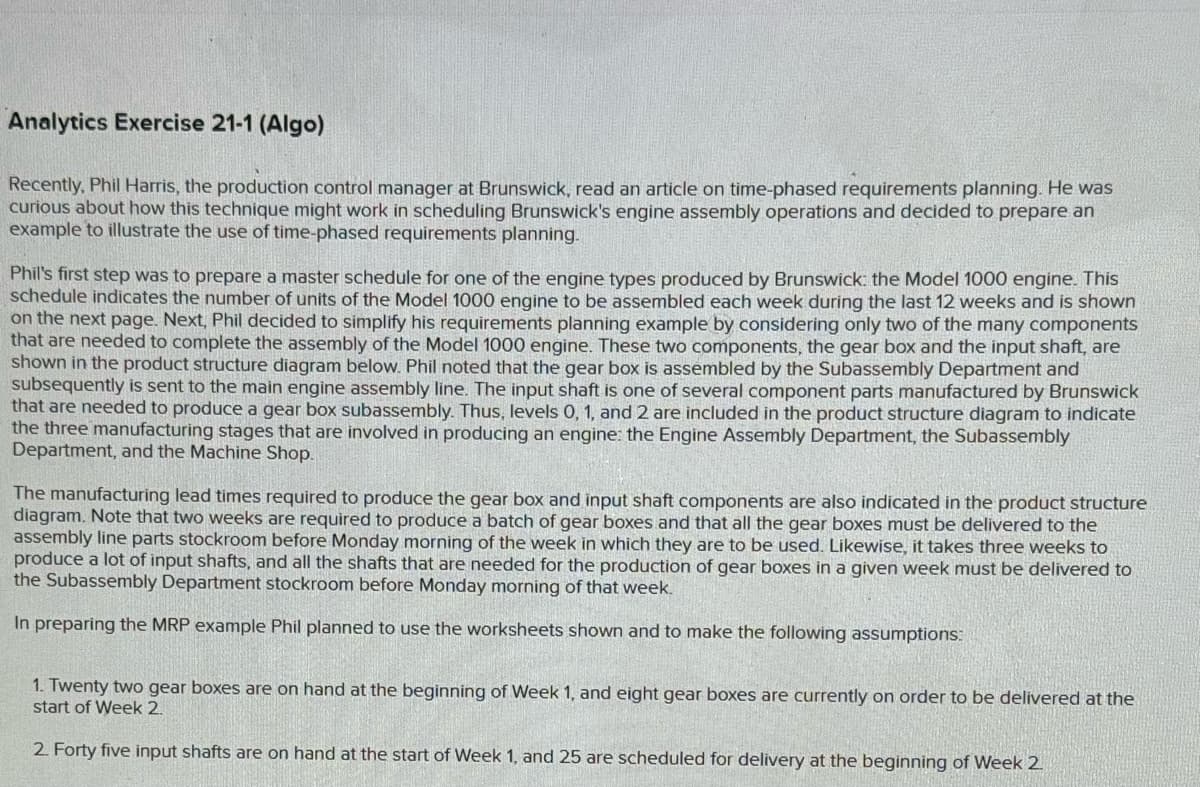
Transcribed Image Text:Analytics Exercise 21-1 (Algo)
Recently, Phil Harris, the production control manager at Brunswick, read an article on time-phased requirements planning. He was
curious about how this technique might work in scheduling Brunswick's engine assembly operations and decided to prepare an
example to illustrate the use of time-phased requirements planning.
Phil's first step was to prepare a master schedule for one of the engine types produced by Brunswick: the Model 1000 engine. This
schedule indicates the number of units of the Model 1000 engine to be assembled each week during the last 12 weeks and is shown
on the next page. Next, Phil decided to simplify his requirements planning example by considering only two of the many components
that are needed to complete the assembly of the Model 1000 engine. These two components, the gear box and the input shaft, are
shown in the product structure diagram below. Phil noted that the gear box is assembled by the Subassembly Department and
subsequently is sent to the main engine assembly line. The input shaft is one of several component parts manufactured by Brunswick
that are needed to produce a gear box subassembly. Thus, levels 0, 1, and 2 are included in the product structure diagram to indicate
the three manufacturing stages that are involved in producing an engine: the Engine Assembly Department, the Subassembly
Department, and the Machine Shop.
The manufacturing lead times required to produce the gear box and input shaft components are also indicated in the product structure
diagram. Note that two weeks are required to produce a batch of gear boxes and that all the gear boxes must be delivered to the
assembly line parts stockroom before Monday morning of the week in which they are to be used. Likewise, it takes three weeks to
produce a lot of input shafts, and all the shafts that are needed for the production of gear boxes in a given week must be delivered to
the Subassembly Department stockroom before Monday morning of that week.
In preparing the MRP example Phil planned to use the worksheets shown and to make the following assumptions:
1. Twenty two gear boxes are on hand at the beginning of Week 1, and eight gear boxes are currently on order to be delivered at the
start of Week 2.
2. Forty five input shafts are on hand at the start of Week 1, and 25 are scheduled for delivery at the beginning of Week 2
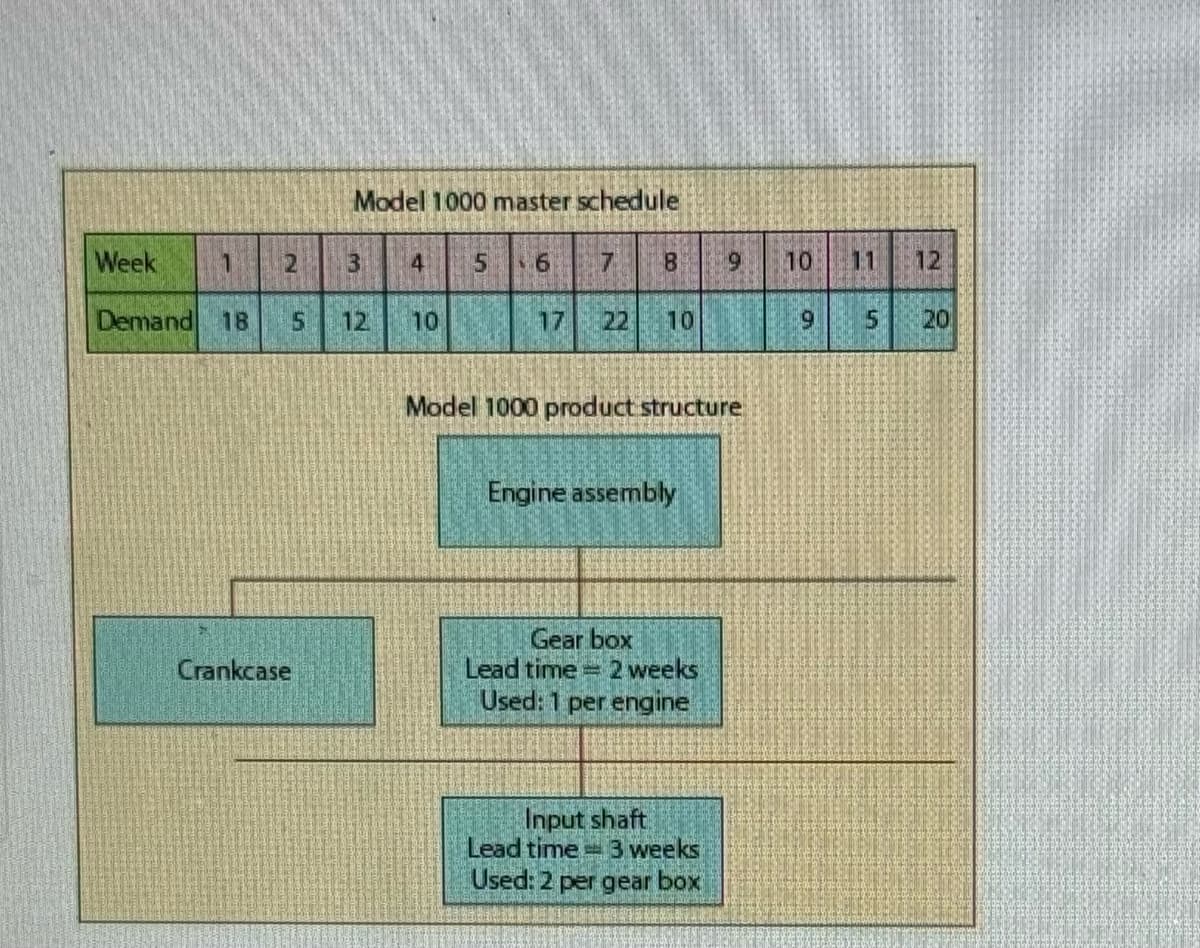
Transcribed Image Text:Model 1000 master schedule
Week 1
2
3
4
5
6
7
B 9
Demand 18
5
12
10
17 22
10
10
Crankcase
Model 1000 product structure
Engine assembly
Gear box
Lead time=2 weeks
Used: 1 per engine
Input shaft
Lead time 3 weeks
Used: 2 per gear box
10
10
6
1.1 12
5 20
20
Expert Solution

This question has been solved!
Explore an expertly crafted, step-by-step solution for a thorough understanding of key concepts.
Step by step
Solved in 2 steps with 2 images

Recommended textbooks for you
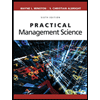
Practical Management Science
Operations Management
ISBN:
9781337406659
Author:
WINSTON, Wayne L.
Publisher:
Cengage,
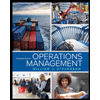
Operations Management
Operations Management
ISBN:
9781259667473
Author:
William J Stevenson
Publisher:
McGraw-Hill Education
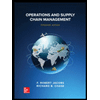
Operations and Supply Chain Management (Mcgraw-hi…
Operations Management
ISBN:
9781259666100
Author:
F. Robert Jacobs, Richard B Chase
Publisher:
McGraw-Hill Education
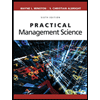
Practical Management Science
Operations Management
ISBN:
9781337406659
Author:
WINSTON, Wayne L.
Publisher:
Cengage,
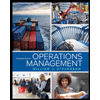
Operations Management
Operations Management
ISBN:
9781259667473
Author:
William J Stevenson
Publisher:
McGraw-Hill Education
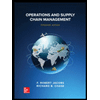
Operations and Supply Chain Management (Mcgraw-hi…
Operations Management
ISBN:
9781259666100
Author:
F. Robert Jacobs, Richard B Chase
Publisher:
McGraw-Hill Education
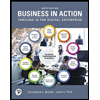
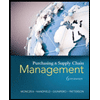
Purchasing and Supply Chain Management
Operations Management
ISBN:
9781285869681
Author:
Robert M. Monczka, Robert B. Handfield, Larry C. Giunipero, James L. Patterson
Publisher:
Cengage Learning
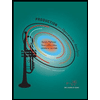
Production and Operations Analysis, Seventh Editi…
Operations Management
ISBN:
9781478623069
Author:
Steven Nahmias, Tava Lennon Olsen
Publisher:
Waveland Press, Inc.