Case Study 5 This case study is all about linear programming. (Section 3.3) A company produces two different grades of steel, A and B at two different factories, 1 and 2. The following table summarizes the production capabilities of the factories, the cost per day and the number of units of each grade of steel that is required to fill orders. Factory 1 Factory 2 Required Grade A 1 unit 2 units 80 units Steel Grade B 3 units 2 units 140 units Steel Cost per $5000 $6000 |day How many days should each factory operate in order to fill the orders at minimum cost? What is the minimum cost? Start by defining the appropriate variables. Solve using graphical methods and clearly explain your solution.
Case Study 5 This case study is all about linear programming. (Section 3.3) A company produces two different grades of steel, A and B at two different factories, 1 and 2. The following table summarizes the production capabilities of the factories, the cost per day and the number of units of each grade of steel that is required to fill orders. Factory 1 Factory 2 Required Grade A 1 unit 2 units 80 units Steel Grade B 3 units 2 units 140 units Steel Cost per $5000 $6000 |day How many days should each factory operate in order to fill the orders at minimum cost? What is the minimum cost? Start by defining the appropriate variables. Solve using graphical methods and clearly explain your solution.
College Algebra (MindTap Course List)
12th Edition
ISBN:9781305652231
Author:R. David Gustafson, Jeff Hughes
Publisher:R. David Gustafson, Jeff Hughes
Chapter6: Linear Systems
Section6.8: Linear Programming
Problem 21E: Making furniture Two woodworkers, Chase and Devin, get 100 for making a table and 80 for making a...
Related questions
Question
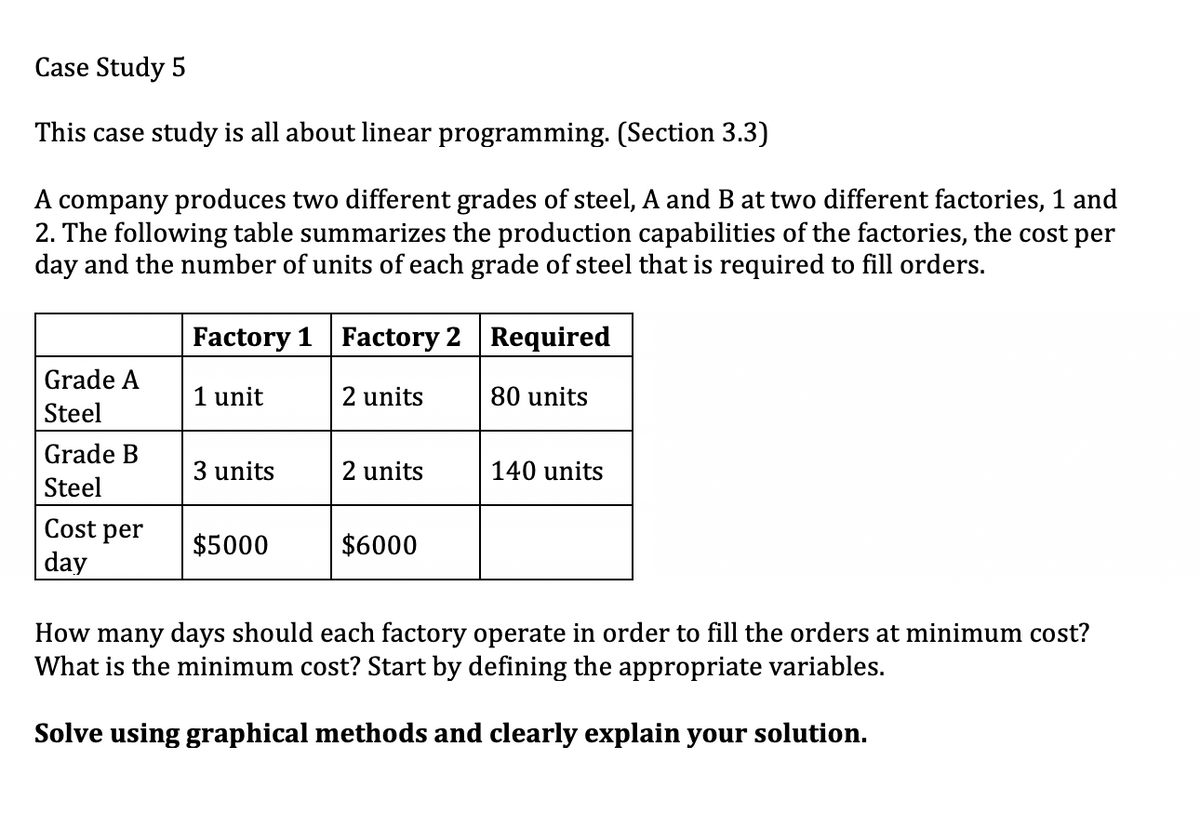
Transcribed Image Text:Case Study 5
This case study is all about linear programming. (Section 3.3)
A company produces two different grades of steel, A and B at two different factories, 1 and
2. The following table summarizes the production capabilities of the factories, the cost per
day and the number of units of each grade of steel that is required to fill orders.
Factory 1 Factory 2 Required
Grade A
1 unit
2 units
80 units
Steel
Grade B
3 units
2 units
140 units
Steel
Cost per
$5000
$6000
day
How many days should each factory operate in order to fill the orders at minimum cost?
What is the minimum cost? Start by defining the appropriate variables.
Solve using graphical methods and clearly explain your solution.
Expert Solution

This question has been solved!
Explore an expertly crafted, step-by-step solution for a thorough understanding of key concepts.
This is a popular solution!
Trending now
This is a popular solution!
Step by step
Solved in 5 steps with 1 images

Recommended textbooks for you
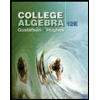
College Algebra (MindTap Course List)
Algebra
ISBN:
9781305652231
Author:
R. David Gustafson, Jeff Hughes
Publisher:
Cengage Learning
Algebra & Trigonometry with Analytic Geometry
Algebra
ISBN:
9781133382119
Author:
Swokowski
Publisher:
Cengage
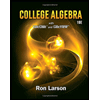
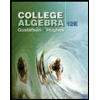
College Algebra (MindTap Course List)
Algebra
ISBN:
9781305652231
Author:
R. David Gustafson, Jeff Hughes
Publisher:
Cengage Learning
Algebra & Trigonometry with Analytic Geometry
Algebra
ISBN:
9781133382119
Author:
Swokowski
Publisher:
Cengage
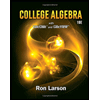