Design a minimum required diameter for the shaft based on operational parameters as prescribed above following that of ASME-Elliptic criterion of fatigue loading. As shaft diameter is the unknown quantity, use a coefficient to modify the endurance limit due of size factor, kb = 0.8499.
Design a minimum required diameter for the shaft based on operational parameters as prescribed above following that of ASME-Elliptic criterion of fatigue loading. As shaft diameter is the unknown quantity, use a coefficient to modify the endurance limit due of size factor, kb = 0.8499.
Mechanics of Materials (MindTap Course List)
9th Edition
ISBN:9781337093347
Author:Barry J. Goodno, James M. Gere
Publisher:Barry J. Goodno, James M. Gere
Chapter3: Torsion
Section: Chapter Questions
Problem 3.4.20P: A magnesium-alloy wire of diameter d = 4mm and length L rotates inside a flexible tube in order to...
Related questions
Question
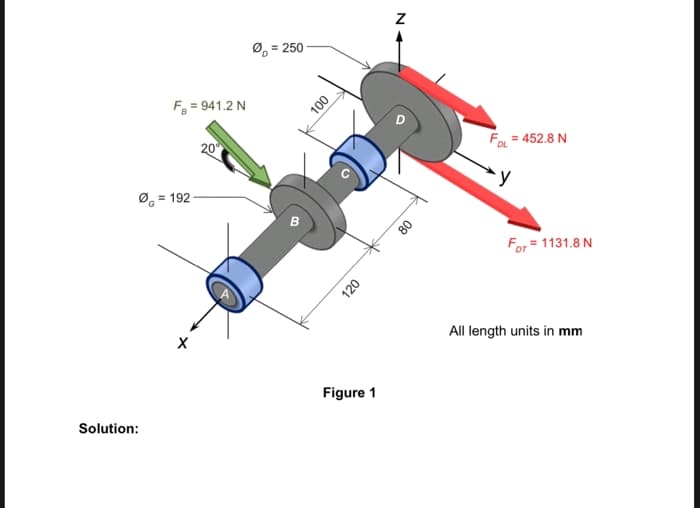
Transcribed Image Text:F = 941.2 N
Ø 192
Solution:
20
Ø = 250
100
Jog
120
N
Figure 1
80
FOL
= 452.8 N
y
FDT=1131.8 N
All length units in mm
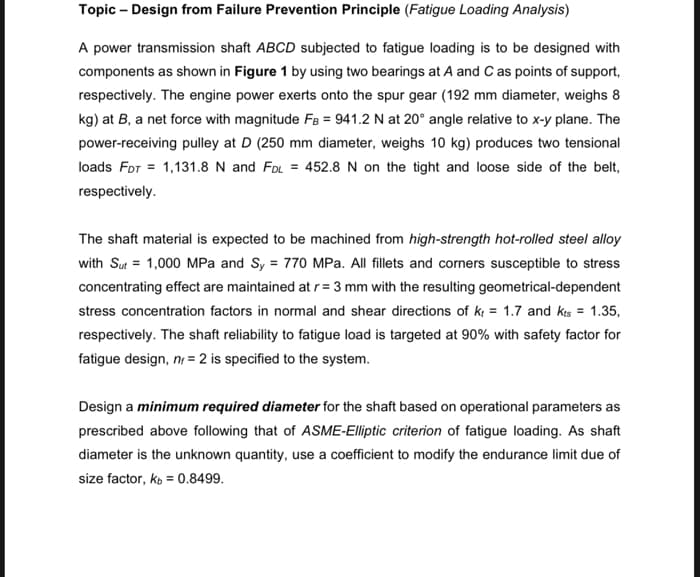
Transcribed Image Text:Topic - Design from Failure Prevention Principle (Fatigue Loading Analysis)
A power transmission shaft ABCD subjected to fatigue loading is to be designed with
components as shown in Figure 1 by using two bearings at A and C as points of support,
respectively. The engine power exerts onto the spur gear (192 mm diameter, weighs 8
kg) at B, a net force with magnitude FB = 941.2 N at 20° angle relative to x-y plane. The
power-receiving pulley at D (250 mm diameter, weighs 10 kg) produces two tensional
loads FDT = 1,131.8 N and FDL = 452.8 N on the tight and loose side of the belt,
respectively.
The shaft material is expected to be machined from high-strength hot-rolled steel alloy
with Sut= 1,000 MPa and Sy = 770 MPa. All fillets and corners susceptible to stress
concentrating effect are maintained at r = 3 mm with the resulting geometrical-dependent
stress concentration factors in normal and shear directions of k = 1.7 and Kts = 1.35,
respectively. The shaft reliability to fatigue load is targeted at 90% with safety factor for
fatigue design, nr = 2 is specified to the system.
Design a minimum required diameter for the shaft based on operational parameters as
prescribed above following that of ASME-Elliptic criterion of fatigue loading. As shaft
diameter is the unknown quantity, use a coefficient to modify the endurance limit due of
size factor, kb = 0.8499.
Expert Solution

This question has been solved!
Explore an expertly crafted, step-by-step solution for a thorough understanding of key concepts.
Step by step
Solved in 3 steps with 4 images

Knowledge Booster
Learn more about
Need a deep-dive on the concept behind this application? Look no further. Learn more about this topic, mechanical-engineering and related others by exploring similar questions and additional content below.Recommended textbooks for you
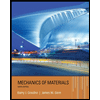
Mechanics of Materials (MindTap Course List)
Mechanical Engineering
ISBN:
9781337093347
Author:
Barry J. Goodno, James M. Gere
Publisher:
Cengage Learning
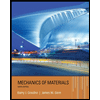
Mechanics of Materials (MindTap Course List)
Mechanical Engineering
ISBN:
9781337093347
Author:
Barry J. Goodno, James M. Gere
Publisher:
Cengage Learning