1. Read the following case study and answer the questions: London Elevator Repair London Elevator Repair (LER) provides a maintenance and repair service for a variety of elevator systems. Its customers include department stores and other business organizations throughout the London. The elevator systems include conventional lifts, paternosters, and escalators. Customers can take out a maintenance contract with LER, for which they pay on an annual basis. One maintenance contract can cover several elevators (for example, all of the escalators in a department store). Due to their nature, some elevators are covered by an individual contract (for example, a paternoster would have its own contract rather than be included in a contract for the maintenance of conventional lifts). Hence each customer can have more than one maintenance contract. The hourly rate to be charged for engineers’ time is agreed as part of the contract negotiations. In addition to the work carried out under maintenance contracts, LER can be called in to carry out emergency repairs (for example, in the event of lift failure) either by existing customers with a maintenance contract or by organizations who do not have one. Sometimes, as a result either of an emergency callout or because of routine maintenance, a need for major repair is identified. In this case, a separate contract for the required work is negotiated. A job (whether routine maintenance, an emergency callout, or any other contract work) is carried out by one or more engineers, depending on its complexity. Each job is provisionally scheduled before engineers are assigned to it, then the schedule is finalized after engineer assignment. A job can be cancelled at any time before it is started. While it is in progress, parts may be ordered, and engineers’ time booked by the senior engineer. A record is kept of the parts that have been used. There is a defined parts list for each type of elevator and particular parts work in conjunction with other parts (for example, an Otis 4000 lift will have a particular hoist which only works with a particular control box). When a job has been completed, a final invoice is sent to the customer. The job is now awaiting final payment. Six months after the final payment has been received, the job is archived. Invoices are sent to customers on an annual basis for maintenance contracts. When routine maintenance results in repairs not covered by the contract a separate invoice is generated. emergency callouts are also invoiced after the repair has been completed. If a major elevator refurbishment takes more than a month to complete, an interim invoice is sent to the customer each month for work completed to date. LER requires an information system to keep track of all contracts, to manage repair work and maintenance jobs and to produce invoices for customers. 2.Answer the following questions: - Write the business process for this case. - Identify the four main elements: entity, process, data store and data flow of the data flow diagrams. - Then use one of the System and Design Software to draw a Data Flow Diagram for the following case study “London Elevator Repair”
1. Read the following case study and answer the questions:
London Elevator Repair
London Elevator Repair (LER) provides a maintenance and repair service for a variety of elevator systems. Its customers include department stores and other business organizations throughout the London. The elevator systems include conventional lifts, paternosters, and escalators.
Customers can take out a maintenance contract with LER, for which they pay on an annual basis. One maintenance contract can cover several elevators (for example, all of the escalators in a department store). Due to their nature, some elevators are covered by an individual contract (for example, a paternoster would have its own contract rather than be included in a contract for the maintenance of conventional lifts). Hence each customer can have more than one maintenance contract. The hourly rate to be charged for engineers’ time is agreed as part of the contract negotiations.
In addition to the work carried out under maintenance contracts, LER can be called in to carry out emergency repairs (for example, in the event of lift failure) either by existing customers with a maintenance contract or by organizations who do not have one. Sometimes, as a result either of an emergency callout or because of routine maintenance, a need for major repair is identified. In this case, a separate contract for the required work is negotiated.
A job (whether routine maintenance, an emergency callout, or any other contract work) is carried out by one or more engineers, depending on its complexity. Each job is provisionally
Invoices are sent to customers on an annual basis for maintenance contracts. When routine maintenance results in repairs not covered by the contract a separate invoice is generated. emergency callouts are also invoiced after the repair has been completed. If a major elevator refurbishment takes more than a month to complete, an interim invoice is sent to the customer each month for work completed to date.
LER requires an information system to keep track of all contracts, to manage repair work and maintenance jobs and to produce invoices for customers.
2.Answer the following questions:
- Write the business process for this case.
- Identify the four main elements: entity, process, data store and data flow of the data flow diagrams.
- Then use one of the System and Design Software to draw a Data Flow Diagram for the following case study “London Elevator Repair”

Trending now
This is a popular solution!
Step by step
Solved in 3 steps with 1 images

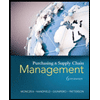
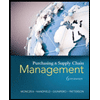