Lutz, Inc. produces three products: Quality, Superior, and Superb. The Lutz cost accounting system applied Conversion Costs using a Plant-Wide Application Rate using Direct Labor Hours as the Cost Driver. Lutz is thinking of employing an ABC system for Conversion Costs. Lutz concluded that its plant had six activities with the following Cost Drivers and costs budgeted for the upcoming year: Activity Area Budgeted Costs Cost Driver Material Handeling $258,400 Number of Parts Production Scheduling $114,000 Number of Orders Setups $160,000 Number of Setups Machinery Cost and Maint $3,510,000 Machine Hours Finishing $1,092,000 Direct Labor Hours Packaging/Shipping $190,000 Number orders Shipped TOTAL $5,324,400 It is estimated that there will be 54,600 Direct Labor Hours in the upcoming year The following information summerizes Lutz' Projections of the Cost Drivers listed above by Product type Cost Driver Quality Superior Superb Units to be produced 10,000 5,000 800 # of parts per unit 30 50 120 Production orders 300 70 200 Production Setups 100 50 50 Machine Hrs per unit 7 7 15 DLH per unit 2 5 12 Orders shipped 1,000 2,000 800 Direct Labor $69.11 $72.50 $83.22 Direct Materials $83.00 $97.00 $115.00 Lutz uses a 30% markup above cost to bid for their projects. What are the costs they currently use with the Plant-wide model? What Should the prices be if we used ABC? Discussion topic: What does the difference suggest we might be doing wrong with our bids? And if you were the CFO what activity area would you look to improve and give a few generic examples of options for improvement.
Lutz, Inc. produces three products: Quality, Superior, and Superb. The Lutz cost accounting system applied Conversion Costs using a Plant-Wide Application Rate using Direct Labor Hours as the Cost Driver. Lutz is thinking of employing an ABC system for Conversion Costs. Lutz concluded that its plant had six activities with the following Cost Drivers and costs budgeted for the upcoming year: Activity Area Budgeted Costs Cost Driver Material Handeling $258,400 Number of Parts Production Scheduling $114,000 Number of Orders Setups $160,000 Number of Setups Machinery Cost and Maint $3,510,000 Machine Hours Finishing $1,092,000 Direct Labor Hours Packaging/Shipping $190,000 Number orders Shipped TOTAL $5,324,400 It is estimated that there will be 54,600 Direct Labor Hours in the upcoming year The following information summerizes Lutz' Projections of the Cost Drivers listed above by Product type Cost Driver Quality Superior Superb Units to be produced 10,000 5,000 800 # of parts per unit 30 50 120 Production orders 300 70 200 Production Setups 100 50 50 Machine Hrs per unit 7 7 15 DLH per unit 2 5 12 Orders shipped 1,000 2,000 800 Direct Labor $69.11 $72.50 $83.22 Direct Materials $83.00 $97.00 $115.00 Lutz uses a 30% markup above cost to bid for their projects. What are the costs they currently use with the Plant-wide model? What Should the prices be if we used ABC? Discussion topic: What does the difference suggest we might be doing wrong with our bids? And if you were the CFO what activity area would you look to improve and give a few generic examples of options for improvement.
Cornerstones of Cost Management (Cornerstones Series)
4th Edition
ISBN:9781305970663
Author:Don R. Hansen, Maryanne M. Mowen
Publisher:Don R. Hansen, Maryanne M. Mowen
Chapter7: Allocating Costs Of Support Departments And Joint Products
Section: Chapter Questions
Problem 28E: Minor Co. has a job order cost system and applies overhead based on departmental rates. Service...
Related questions
Question
Lutz, Inc. produces three products: Quality, Superior, and Superb. The Lutz cost accounting system applied Conversion Costs using a Plant-Wide Application Rate using Direct Labor Hours as the Cost Driver. Lutz is thinking of employing an ABC system for Conversion Costs. | ||||||||||
Lutz concluded that its plant had six activities with the following Cost Drivers and costs budgeted for the upcoming year: | ||||||||||
Activity Area | Budgeted Costs | Cost Driver | ||||||||
Material Handeling | $258,400 | Number of Parts | ||||||||
Production Scheduling | $114,000 | Number of Orders | ||||||||
Setups | $160,000 | Number of Setups | ||||||||
Machinery Cost and Maint | $3,510,000 | Machine Hours | ||||||||
Finishing | $1,092,000 | Direct Labor Hours | ||||||||
Packaging/Shipping | $190,000 | Number orders Shipped | ||||||||
TOTAL | $5,324,400 | |||||||||
It is estimated that there will be 54,600 Direct Labor Hours in the upcoming year | ||||||||||
The following information summerizes Lutz' Projections of the Cost Drivers listed above by Product type | ||||||||||
Cost Driver | Quality | Superior | Superb | |||||||
Units to be produced | 10,000 | 5,000 | 800 | |||||||
# of parts per unit | 30 | 50 | 120 | |||||||
Production orders | 300 | 70 | 200 | |||||||
Production Setups | 100 | 50 | 50 | |||||||
Machine Hrs per unit | 7 | 7 | 15 | |||||||
DLH per unit | 2 | 5 | 12 | |||||||
Orders shipped | 1,000 | 2,000 | 800 | |||||||
Direct Labor | $69.11 | $72.50 | $83.22 | |||||||
Direct Materials | $83.00 | $97.00 | $115.00 | |||||||
Lutz uses a 30% markup above cost to bid for their projects. What are the costs they currently use with the Plant-wide model? | ||||||||||
What Should the prices be if we used ABC? | ||||||||||
Discussion topic: What does the difference suggest we might be doing wrong with our bids? And if you were the CFO what activity area would you look to improve and give a few generic examples of options for improvement. |
Expert Solution

This question has been solved!
Explore an expertly crafted, step-by-step solution for a thorough understanding of key concepts.
This is a popular solution!
Trending now
This is a popular solution!
Step by step
Solved in 2 steps

Recommended textbooks for you
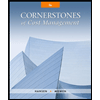
Cornerstones of Cost Management (Cornerstones Ser…
Accounting
ISBN:
9781305970663
Author:
Don R. Hansen, Maryanne M. Mowen
Publisher:
Cengage Learning
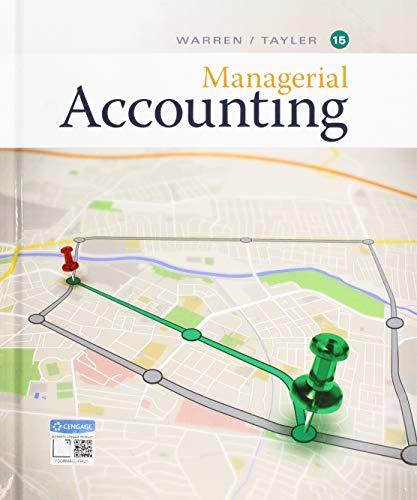
Managerial Accounting
Accounting
ISBN:
9781337912020
Author:
Carl Warren, Ph.d. Cma William B. Tayler
Publisher:
South-Western College Pub
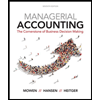
Managerial Accounting: The Cornerstone of Busines…
Accounting
ISBN:
9781337115773
Author:
Maryanne M. Mowen, Don R. Hansen, Dan L. Heitger
Publisher:
Cengage Learning
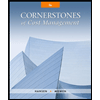
Cornerstones of Cost Management (Cornerstones Ser…
Accounting
ISBN:
9781305970663
Author:
Don R. Hansen, Maryanne M. Mowen
Publisher:
Cengage Learning
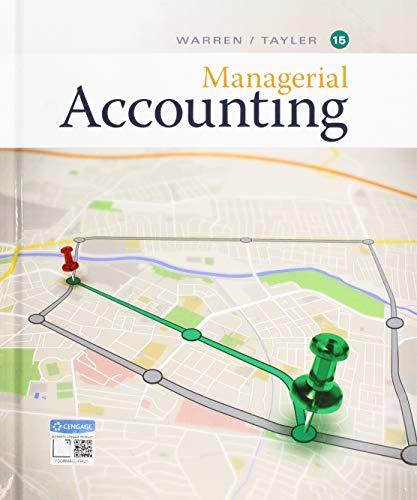
Managerial Accounting
Accounting
ISBN:
9781337912020
Author:
Carl Warren, Ph.d. Cma William B. Tayler
Publisher:
South-Western College Pub
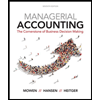
Managerial Accounting: The Cornerstone of Busines…
Accounting
ISBN:
9781337115773
Author:
Maryanne M. Mowen, Don R. Hansen, Dan L. Heitger
Publisher:
Cengage Learning
Principles of Accounting Volume 2
Accounting
ISBN:
9781947172609
Author:
OpenStax
Publisher:
OpenStax College
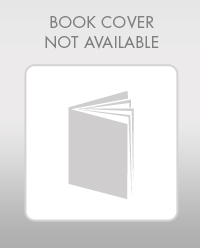
Financial And Managerial Accounting
Accounting
ISBN:
9781337902663
Author:
WARREN, Carl S.
Publisher:
Cengage Learning,