Problem #1: Extension of the solved problem in the class The washing machine plant is interested in determining work force and production levels for the next 8 months. Forecasted demands for Jan-Aug. are: 420, 280, 460, 190, 310, 145, 110, 125. Starting inventory at the end of December is 200. The firm would like to have 100 units on hand at the end of August. Suppose we are told that over a period of 40 days, the plant had 38 workers who produced 520 units. Assume we are given the following number of working days per month (January to August): 22, 16, 23, 20, 21, 22, 21, 22. The holding cost (per unit per month): $8.50, hiring cost per worker: $800, firing cost per worker: $1,250, payroll cost: $75/worker/day, and shortage cost: $50 unit short/month. The company has 40 workers at the end of December. We solved this problem in class and obtained a value of K = 0.3421 units/worker/day. In addition, we developed a constant workforce plan with 46 workers over the planning horizon and estimated the total cost of the plan to be $599,590.50. We discussed that the cost is very high due to the high inventory level. Hence, we decided to reduce the workforce to reduce the production and the unneeded inventory. Develop a production plan with constant workforce over January to March, reduce it to be constant over April and May, and finally reduce it again to be constant over June to August without any shortage of demand. Estimate the workforce levels over these three periods and the new total cost of the developed plan.
Problem #1: Extension of the solved problem in the class The washing machine plant is interested in determining work force and production levels for the next 8 months. Forecasted demands for Jan-Aug. are: 420, 280, 460, 190, 310, 145, 110, 125. Starting inventory at the end of December is 200. The firm would like to have 100 units on hand at the end of August. Suppose we are told that over a period of 40 days, the plant had 38 workers who produced 520 units. Assume we are given the following number of working days per month (January to August): 22, 16, 23, 20, 21, 22, 21, 22. The holding cost (per unit per month): $8.50, hiring cost per worker: $800, firing cost per worker: $1,250, payroll cost: $75/worker/day, and shortage cost: $50 unit short/month. The company has 40 workers at the end of December. We solved this problem in class and obtained a value of K = 0.3421 units/worker/day. In addition, we developed a constant workforce plan with 46 workers over the planning horizon and estimated the total cost of the plan to be $599,590.50. We discussed that the cost is very high due to the high inventory level. Hence, we decided to reduce the workforce to reduce the production and the unneeded inventory. Develop a production plan with constant workforce over January to March, reduce it to be constant over April and May, and finally reduce it again to be constant over June to August without any shortage of demand. Estimate the workforce levels over these three periods and the new total cost of the developed plan.
Practical Management Science
6th Edition
ISBN:9781337406659
Author:WINSTON, Wayne L.
Publisher:WINSTON, Wayne L.
Chapter12: Queueing Models
Section: Chapter Questions
Problem 59P
Related questions
Question
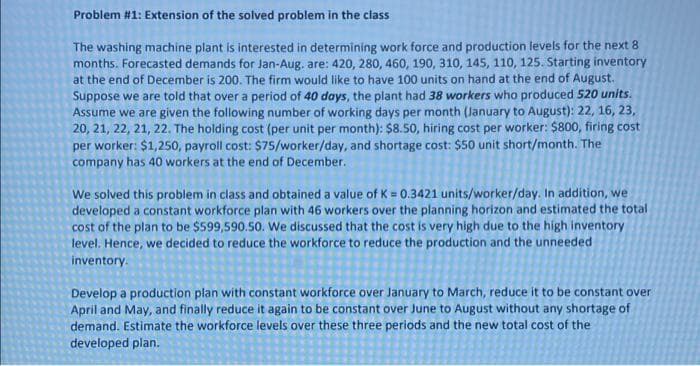
Transcribed Image Text:Problem #1: Extension of the solved problem in the class
The washing machine plant is interested in determining work force and production levels for the next 8
months. Forecasted demands for Jan-Aug, are: 420, 280, 460, 190, 310, 145, 110, 125. Starting inventory
at the end of December is 200. The firm would like to have 100 units on hand at the end of August.
Suppose we are told that over a period of 40 days, the plant had 38 workers who produced 520 units.
Assume we are given the following number of working days per month (January to August): 22, 16, 23,
20, 21, 22, 21, 22. The holding cost (per unit per month): $8.50, hiring cost per worker: $800, firing cost
per worker: $1,250, payroll cost: $75/worker/day, and shortage cost: $50 unit short/month. The
company has 40 workers at the end of December.
We solved this problem in class and obtained a value of K = 0.3421 units/worker/day. In addition, we
developed a constant workforce plan with 46 workers over the planning horizon and estimated the total
cost of the plan to be $599,590.50. We discussed that the cost is very high due to the high inventory
level. Hence, we decided to reduce the workforce to reduce the production and the unneeded
inventory.
Develop a production plan with constant workforce over January to March, reduce it to be constant over
April and May, and finally reduce it again to be constant over June to August without any shortage of
demand. Estimate the workforce levels over these three periods and the new total cost of the
developed plan.
Expert Solution

This question has been solved!
Explore an expertly crafted, step-by-step solution for a thorough understanding of key concepts.
This is a popular solution!
Trending now
This is a popular solution!
Step by step
Solved in 5 steps with 7 images

Recommended textbooks for you
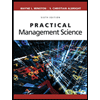
Practical Management Science
Operations Management
ISBN:
9781337406659
Author:
WINSTON, Wayne L.
Publisher:
Cengage,
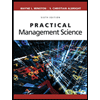
Practical Management Science
Operations Management
ISBN:
9781337406659
Author:
WINSTON, Wayne L.
Publisher:
Cengage,