PROBLEM 17.6B Applying Overhead Costs Using ABCL017-6, LO17-7 Logan Pharmaceutical produces two products: Caltrate and Dorkamine. The company uses activity-based costing (ABC) to allocate manufacturing costs to each product line. The costs incurred by the Quality Control Department average $5 million per year and constitute one of the largest components of the company's total manufacturing overhead. The Quality Control Department conducts routine inspections at two critical points. First, all raw materials are inspected before they are entered into the production process. Second, all completed batches of product are inspected before being shipped to the finished goods warehouse. The department's costs are assigned to two activity cost pools: (1) preproduction inspections and (2) postproduction inspections. Costs are assigned to the pools based on the number of employees engaged in each activity. Of the department's 16 full-time employees, 4 are responsible for preproduction inspections and 12 are responsible for postproduction inspections. Page 812 Costs assigned to the preproduction pool are allocated to products based on the number of materials shipments received for each product line. Costs assigned to the postproduction pool are allocated to products based on the number of batches of each product produced. For the upcoming year, Logan Pharmaceutical estimates the following activity levels: Shipments received Batches produced Total 1,200 2,000 Caltrate Dorkamine 900 300 400 1,600 The materials used to produce Caltrate can be ordered only in small quantities and therefore must be ordered frequently. The company's four preproduction inspectors devote a disproportionate amount of their time inspecting the 900 shipments of Caltrate materials. Dorkamine can be produced only in small batches and therefore must be produced frequently. Most of the problems associated with completed batches of Dorkamine can be traced to poor-quality materials. Very few problems are associated with the quality of Caltrate materials. Instructions a. Assign the Quality Control Department's costs to the individual cost pools. b. Allocate the preproduction inspection cost pool to each product line. c. Allocate the postproduction inspection cost pool to each product line. d. Suggest how Logan Pharmaceutical might reassign responsibilities to make better use of its quality control inspectors.
Process Costing
Process costing is a sort of operation costing which is employed to determine the value of a product at each process or stage of producing process, applicable where goods produced from a series of continuous operations or procedure.
Job Costing
Job costing is adhesive costs of each and every job involved in the production processes. It is an accounting measure. It is a method which determines the cost of specific jobs, which are performed according to the consumer’s specifications. Job costing is possible only in businesses where the production is done as per the customer’s requirement. For example, some customers order to manufacture furniture as per their needs.
ABC Costing
Cost Accounting is a form of managerial accounting that helps the company in assessing the total variable cost so as to compute the cost of production. Cost accounting is generally used by the management so as to ensure better decision-making. In comparison to financial accounting, cost accounting has to follow a set standard ad can be used flexibly by the management as per their needs. The types of Cost Accounting include – Lean Accounting, Standard Costing, Marginal Costing and Activity Based Costing.


Trending now
This is a popular solution!
Step by step
Solved in 3 steps with 6 images

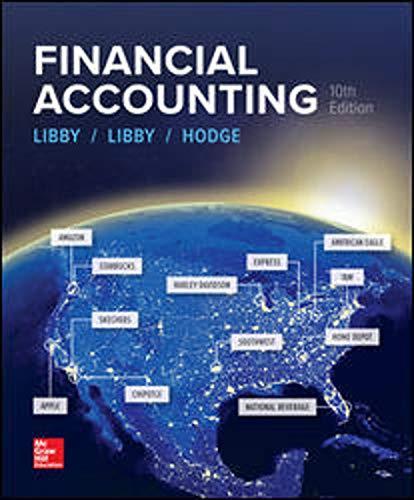
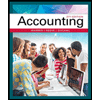
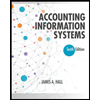
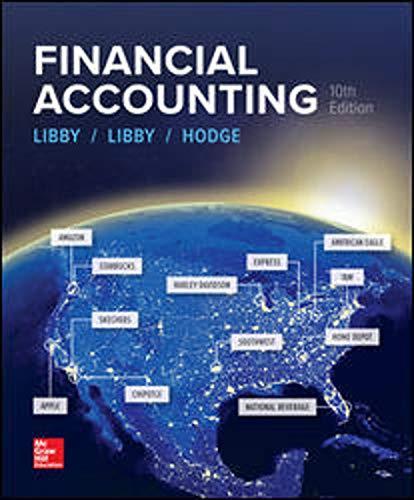
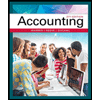
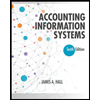
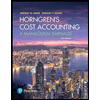
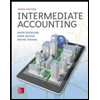
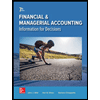