The conversion cycle of the company is triggered by a report from the warehouse. When the quantity of an inventory item falls below a pre-set minimum level, the warehouse manager sends an online inventory status report to the production department advising them to schedule a production batch run for the item. Upon receipt of the report, the production clerk assesses the digital bill of materials and the route sheet files for the item to be produced and adds the production details to the online production schedule. The system automatically adds a record to the openwork order file and sends an online work order to the work center supervisor’s computer and to the accounting clerk’s computer. The work center supervisor receives the work order from his computer and print hard-copy move tickets and materials requisitions for each production process. Production employees take the materials requisitions to store clerk and receive the materials and subassemblies needed to perform the production tasks. If additional materials beyond the standard amount are needed, the work center supervisor prepares additional materials requisitions. Production employees complete job time tickets after completing a production process to record the time spent on the job. The job time tickets are then sent together with the move tickets to the accounting department. After releasing the materials into production, the store clerk updates the material inventory records and sends the materials requisitions to the accounting department. The clerk prepares a journal voucher and posts to the general ledger material control account at the end of each day. The accounting clerk assesses the work orders and set up a work-in-process account for a production batch. Throughout the production period, the clerk also receives move tickets, job tickets, and materials requisitions, which he uses to post to the work-in-process account. At the end of each day, the accounting clerk prepares a digital journal voucher and post it to the general ledger work-in-process and finished goods control accounts. Identify the risks that exist in the conversion cycle of Central Production Limited.
The conversion cycle of the company is triggered by a report from the warehouse. When the quantity of an inventory item falls below a pre-set minimum level, the warehouse manager sends an online inventory status report to the production department advising them to schedule a production batch run for the item. Upon receipt of the report, the production clerk assesses the digital bill of materials and the route sheet files for the item to be produced and adds the production details to the online production schedule. The system automatically adds a record to the openwork order file and sends an online work order to the work center supervisor’s computer and to the accounting clerk’s computer. The work center supervisor receives the work order from his computer and print hard-copy move tickets and materials requisitions for each production process. Production employees take the materials requisitions to store clerk and receive the materials and subassemblies needed to perform the production tasks. If additional materials beyond the standard amount are needed, the work center supervisor prepares additional materials requisitions. Production employees complete job time tickets after completing a production process to record the time spent on the job. The job time tickets are then sent together with the move tickets to the accounting department. After releasing the materials into production, the store clerk updates the material inventory records and sends the materials requisitions to the accounting department. The clerk prepares a journal voucher and posts to the general ledger material control account at the end of each day. The accounting clerk assesses the work orders and set up a work-in-process account for a production batch. Throughout the production period, the clerk also receives move tickets, job tickets, and materials requisitions, which he uses to post to the work-in-process account. At the end of each day, the accounting clerk prepares a digital journal voucher and post it to the general ledger work-in-process and finished goods control accounts.
Identify the risks that exist in the conversion cycle of Central Production Limited.

Trending now
This is a popular solution!
Step by step
Solved in 2 steps

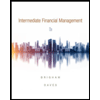
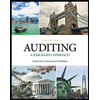
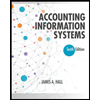
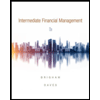
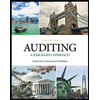
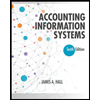
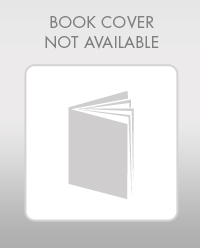
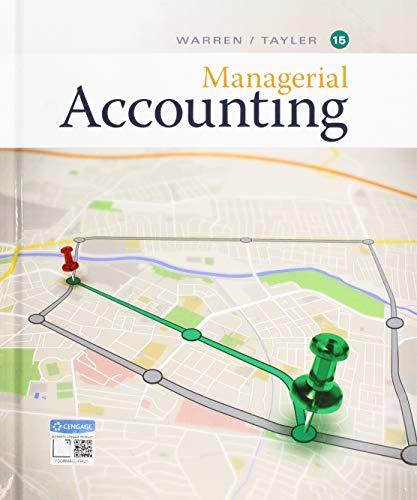