Thompson Industrial Products Inc. (TIPI) is a diversified industrial-cleaner processing company. The company’s Dargan plant produces two products: a table cleaner and a floor cleaner from a common set of chemical inputs (CDG). Each week, 900,000 ounces of chemical input are processed at a cost of $210,000 into 600,000 ounces of floor cleaner and 300,000 ounces of table cleaner. The floor cleaner has no market value until it is converted into a polish with the trade name FloorShine. The additional processing costs for this conversion amount to $240,000. FloorShine sells at $20 per 30-ounce bottle. The table cleaner can be sold for $17 per 25-ounce bottle. However, the table cleaner can be converted into two other products by adding 300,000 ounces of another compound (TCP) to the 300,000 ounces of table cleaner. This joint process will yield 300,000 ounces each of table stain remover (TSR) and table polish (TP). The additional processing costs for this process amount to $100,000. Both table products can be sold for $14 per 25-ounce bottle. The company decided not to process the table cleaner into TSR and TP based on the following analysis. Process Further Table Cleaner Table Stain Remover (TSR) Table Polish (TP) Total Production in ounces 300,000 300,000 300,000 Revenues $204,000 $168,000 $168,000 $336,000 Costs: CDG costs 70,000 * 52,500 52,500 105,000 ** TCP costs 0 50,000 50,000 100,000 Total costs 70,000 102,500 102,500 205,000 Weekly gross profit $134,000 $65,500 $65,500 $131,000 *If table cleaner is not processed further, it is allocated 1/3 of the $210,000 of CDG cost, which is equal to 1/3 of the total physical output. **If table cleaner is processed further, total physical output is 1,200,000 ounces. TSR and TP combined account for 50% of the total physical output and are each allocated 25% of the CDG cost. After you have completed P20-3A, consider the following additional question. Assume that the selling price of the two table products after further processing changed to $13 for each 25-ounce bottle and the cost of TCP compound to further process changed to $120,000. How do these changes impact the decision to process or not process further?
Thompson Industrial Products Inc. (TIPI) is a diversified industrial-cleaner processing company. The company’s Dargan plant produces two products: a table cleaner and a floor cleaner from a common set of chemical inputs (CDG). Each week, 900,000 ounces of chemical input are processed at a cost of $210,000 into 600,000 ounces of floor cleaner and 300,000 ounces of table cleaner. The floor cleaner has no market value until it is converted into a polish with the trade name FloorShine. The additional
FloorShine sells at $20 per 30-ounce bottle. The table cleaner can be sold for $17 per 25-ounce bottle. However, the table cleaner can be converted into two other products by adding 300,000 ounces of another compound (TCP) to the 300,000 ounces of table cleaner. This joint process will yield 300,000 ounces each of table stain remover (TSR) and table polish (TP). The additional processing costs for this process amount to $100,000. Both table products can be sold for $14 per 25-ounce bottle.
The company decided not to process the table cleaner into TSR and TP based on the following analysis.
Process Further | ||||||||||||
Table Cleaner |
Table Stain Remover (TSR) |
Table Polish (TP) |
Total | |||||||||
Production in ounces | 300,000 | 300,000 | 300,000 | |||||||||
Revenues | $204,000 | $168,000 | $168,000 | $336,000 | ||||||||
Costs: | ||||||||||||
CDG costs | 70,000 | * | 52,500 | 52,500 | 105,000 | ** | ||||||
TCP costs | 0 | 50,000 | 50,000 | 100,000 | ||||||||
Total costs | 70,000 | 102,500 | 102,500 | 205,000 | ||||||||
Weekly gross profit | $134,000 | $65,500 | $65,500 | $131,000 |
*If table cleaner is not processed further, it is allocated 1/3 of the $210,000 of CDG cost, which is equal to 1/3 of the total physical output.
**If table cleaner is processed further, total physical output is 1,200,000 ounces. TSR and TP combined account for 50% of the total physical output and are each allocated 25% of the CDG cost.
After you have completed P20-3A, consider the following additional question. Assume that the selling price of the two table products after further processing changed to $13 for each 25-ounce bottle and the cost of TCP compound to further process changed to $120,000. How do these changes impact the decision to process or not process further?
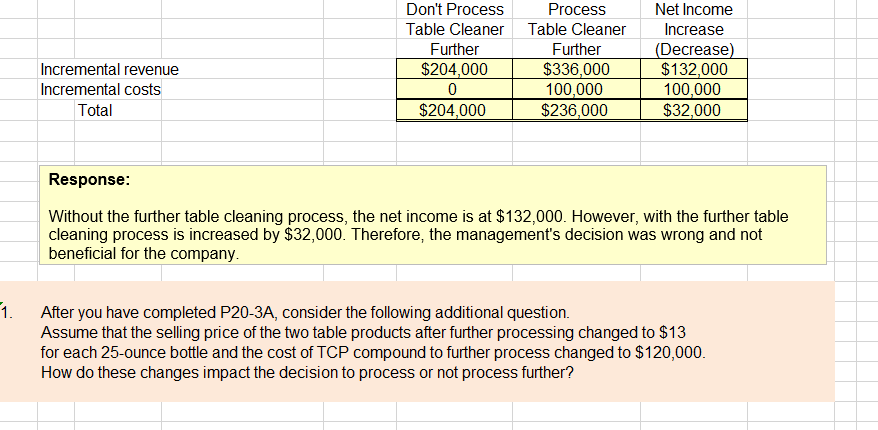

Trending now
This is a popular solution!
Step by step
Solved in 2 steps

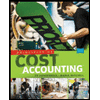
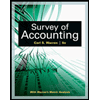
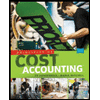
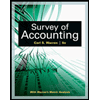