TOYS AND JOB DESIGN AT THE HOVEY AND BEARD COMPANY The following is a situation that occurred in the Hovey and Beard Company, as reported by J. V. Clark. This company manufactured a line of wooden toys. One part of the process involved spray painting partially assembled toys, after which the toys were hung on moving hooks that carried them through a drying oven. The operation, staffed entirely by women, was plagued with absenteeism, high turnover, and low morale. Each woman at her paint booth would take a toy from the tray beside her, position it in a fixture, and spray on the color according to the required pattern. She then would release the toy and hang it on the conveyor hook. The rate at which the hooks moved had been calculated so that each woman, once fully trained, would be able to hang a painted toy on each hook before it passed beyond her reach. The women who worked in the paint room were on a group incentive plan that tied their earnings to the production of the entire group. Since the operation was new, they received a learning allowance that decreased by regular amounts each month. The learning allowance was scheduled to fall to zero in six months because it was expected that the women could meet standard output or more by that time. By the second month of the training period, trouble had developed. The women had progressed more slowly than had been anticipated, and it appeared that their production level would stabilize somewhat below the planned level. Some of the women complained about the speed that was expected of them, and a few of them quit. There was evidence of resistance to the new situation. Through the counsel of a consultant, the supervisor finally decided to bring the women together for general discussions of working conditions. After two meetings in which relations between the work group and the supervisor were somewhat improved, a third meeting produced the suggestion that control of the conveyor speed be turned over to the work group. The women explained that they felt that they could keep up with the speed of the conveyor but that they could not work at that pace all day long. They wished to be able to adjust the speed of the belt, depending on how they felt. After consultation, the supervisor had a control marked, “low, medium, and fast” installed at the booth of the group leader, who could adjust the speed of the conveyor anywhere between the lower and upper limits that had been set. The women were delighted and spent many lunch hours deciding how the speed should be varied from hour to hour throughout the day. Within a week, a pattern had emerged: the first half-hour of the shift was run on what the women called “medium speed” (a dial setting slightly above the point marked “medium”). The next two and one-half hours were run at high speed, and the half-hour before lunch and the half-hour after lunch were run at low speed. The rest of the afternoon was run at high speed, with the exception of the last 45 minutes of the shift, which were run at medium speed. In view of the women’s report of satisfaction and ease in their work, it is interesting to note that the original speed was slightly below medium on the dial of the new control. The average speed at which the women were running the belt was on the high side of the dial. Few, if any, empty hooks entered the drying oven, and inspection showed no increase of rejects from the paint room. Production increased, and within three weeks the women were operating at 30 to 50 percent above the level that had been expected according to the original design. Evaluate the experience of the Hovey and Beard Company as it reflects on job design, human relationships, and the supervisor’s role. How would you react as the supervisor to the situation where workers determine how the work will be performed? If you were designing the spray-painting set-up, would you design it differently?
TOYS AND JOB DESIGN AT THE HOVEY AND BEARD COMPANY The following is a situation that occurred in the Hovey and Beard Company, as reported by J. V. Clark. This company manufactured a line of wooden toys. One part of the process involved spray painting partially assembled toys, after which the toys were hung on moving hooks that carried them through a drying oven. The operation, staffed entirely by women, was plagued with absenteeism, high turnover, and low morale. Each woman at her paint booth would take a toy from the tray beside her, position it in a fixture, and spray on the color according to the required pattern. She then would release the toy and hang it on the conveyor hook. The rate at which the hooks moved had been calculated so that each woman, once fully trained, would be able to hang a painted toy on each hook before it passed beyond her reach. The women who worked in the paint room were on a group incentive plan that tied their earnings to the production of the entire group. Since the operation was new, they received a learning allowance that decreased by regular amounts each month. The learning allowance was scheduled to fall to zero in six months because it was expected that the women could meet standard output or more by that time. By the second month of the training period, trouble had developed. The women had progressed more slowly than had been anticipated, and it appeared that their production level would stabilize somewhat below the planned level. Some of the women complained about the speed that was expected of them, and a few of them quit. There was evidence of resistance to the new situation. Through the counsel of a consultant, the supervisor finally decided to bring the women together for general discussions of working conditions. After two meetings in which relations between the work group and the supervisor were somewhat improved, a third meeting produced the suggestion that control of the conveyor speed be turned over to the work group. The women explained that they felt that they could keep up with the speed of the conveyor but that they could not work at that pace all day long. They wished to be able to adjust the speed of the belt, depending on how they felt. After consultation, the supervisor had a control marked, “low, medium, and fast” installed at the booth of the group leader, who could adjust the speed of the conveyor anywhere between the lower and upper limits that had been set. The women were delighted and spent many lunch hours deciding how the speed should be varied from hour to hour throughout the day. Within a week, a pattern had emerged: the first half-hour of the shift was run on what the women called “medium speed” (a dial setting slightly above the point marked “medium”). The next two and one-half hours were run at high speed, and the half-hour before lunch and the half-hour after lunch were run at low speed. The rest of the afternoon was run at high speed, with the exception of the last 45 minutes of the shift, which were run at medium speed. In view of the women’s report of satisfaction and ease in their work, it is interesting to note that the original speed was slightly below medium on the dial of the new control. The average speed at which the women were running the belt was on the high side of the dial. Few, if any, empty hooks entered the drying oven, and inspection showed no increase of rejects from the paint room. Production increased, and within three weeks the women were operating at 30 to 50 percent above the level that had been expected according to the original design. Evaluate the experience of the Hovey and Beard Company as it reflects on job design, human relationships, and the supervisor’s role. How would you react as the supervisor to the situation where workers determine how the work will be performed? If you were designing the spray-painting set-up, would you design it differently?
Management, Loose-Leaf Version
13th Edition
ISBN:9781305969308
Author:Richard L. Daft
Publisher:Richard L. Daft
Chapter10: Designing Organization Structure
Section: Chapter Questions
Problem 3ED
Related questions
Question
TOYS AND JOB DESIGN AT THE HOVEY AND BEARD COMPANY
The following is a situation that occurred in the Hovey and Beard Company, as reported by J. V.
Clark.
This company manufactured a line of wooden toys. One part of the process involved
spray painting partially assembled toys, after which the toys were hung on moving hooks that
carried them through a drying oven. The operation, staffed entirely by women, was plagued with
absenteeism, high turnover, and low morale. Each woman at her paint booth would take a toy
from the tray beside her, position it in a fixture, and spray on the color according to the required
pattern. She then would release the toy and hang it on the conveyor hook. The rate at which the
hooks moved had been calculated so that each woman, once fully trained, would be able to hang
a painted toy on each hook before it passed beyond her reach.
The women who worked in the paint room were on a group incentive plan that tied their
earnings to the production of the entire group. Since the operation was new, they received a
learning allowance that decreased by regular amounts each month. The learning allowance was
scheduled to fall to zero in six months because it was expected that the women could meet
standard output or more by that time. By the second month of the training period, trouble had
developed. The women had progressed more slowly than had been anticipated, and it appeared
that their production level would stabilize somewhat below the planned level. Some of the
women complained about the speed that was expected of them, and a few of them quit. There
was evidence of resistance to the new situation.
Through the counsel of a consultant, the supervisor finally decided to bring the women
together for general discussions of working conditions. After two meetings in which relations
between the work group and the supervisor were somewhat improved, a third meeting produced
the suggestion that control of the conveyor speed be turned over to the work group. The women
explained that they felt that they could keep up with the speed of the conveyor but that they
could not work at that pace all day long. They wished to be able to adjust the speed of the belt,
depending on how they felt.
After consultation, the supervisor had a control marked, “low, medium, and fast”
installed at the booth of the group leader, who could adjust the speed of the conveyor anywhere
between the lower and upper limits that had been set. The women were delighted and spent many lunch hours deciding how the speed should be varied from hour to hour throughout the day.
Within a week, a pattern had emerged: the first half-hour of the shift was run on what the women
called “medium speed” (a dial setting slightly above the point marked “medium”). The next two
and one-half hours were run at high speed, and the half-hour before lunch and the half-hour after
lunch were run at low speed. The rest of the afternoon was run at high speed, with the exception
of the last 45 minutes of the shift, which were run at medium speed.
In view of the women’s report of satisfaction and ease in their work, it is interesting to
note that the original speed was slightly below medium on the dial of the new control. The
average speed at which the women were running the belt was on the high side of the dial. Few, if
any, empty hooks entered the drying oven, and inspection showed no increase of rejects from the
paint room. Production increased, and within three weeks the women were operating at 30 to 50
percent above the level that had been expected according to the original design.
Evaluate the experience of the Hovey and Beard Company as it reflects on job design,
human relationships, and the supervisor’s role. How would you react as the supervisor to the
situation where workers determine how the work will be performed? If you were designing the
spray-painting set-up, would you design it differently?
Expert Solution

This question has been solved!
Explore an expertly crafted, step-by-step solution for a thorough understanding of key concepts.
This is a popular solution!
Trending now
This is a popular solution!
Step by step
Solved in 4 steps

Knowledge Booster
Learn more about
Need a deep-dive on the concept behind this application? Look no further. Learn more about this topic, management and related others by exploring similar questions and additional content below.Recommended textbooks for you
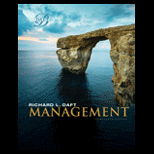
Management, Loose-Leaf Version
Management
ISBN:
9781305969308
Author:
Richard L. Daft
Publisher:
South-Western College Pub
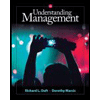
Understanding Management (MindTap Course List)
Management
ISBN:
9781305502215
Author:
Richard L. Daft, Dorothy Marcic
Publisher:
Cengage Learning
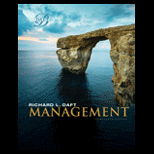
Management, Loose-Leaf Version
Management
ISBN:
9781305969308
Author:
Richard L. Daft
Publisher:
South-Western College Pub
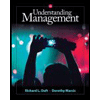
Understanding Management (MindTap Course List)
Management
ISBN:
9781305502215
Author:
Richard L. Daft, Dorothy Marcic
Publisher:
Cengage Learning