2.8 The expression "tool and die repair" is most commonly used for... O the process of disassembling the die and replacing worn parts with fresh elements O the sequence of material addition (through welding) and subsequent machining to final precise shape in worn areas 2.9 What is the most common material to make deforming tools (dies)? X steel O ceramics O cemented carbide O diamond 2.10 What is one of the main advantages of additive manufacturing compared to subtractive manufacturing? X high degree of freedom with regard to workpiece geometry O high strength of workpieces that can be achieved (e.g. compared to milled workpieces with same workpiece dimensions) 2.11 How is the true strain of a deforming process calculated (referring to a simple upsetting process as explained in the lecture)? (h: height, index 0: prior to deforming) O phi, = In (h/h,) X phi, = In (h,/h.) O phi, = (h,-h,)/h, %3D %3D 2.12 In hot extrusion, the recrystallization process takes place during the deforming process. True O False 2.13 Which feature of the tool and or machine is an important difference between fine blanking and conventional shearing? O In fine blanking, the blank holder has a special geometrical feature ("Vee ring" or "v-ring") that is not used in conventional shearing O In conventional shearing, a counter punch is applied on the opposite side of the workpiece (than the punch) O Fine blanking tools are usually cooled whereas shearing tools usually do not have a cooling system. 2.14 Which bulk forming technology is used to make a cardan joint (a workpiece that resembles an "X" or a cross)? O full forward extrusion O cup backward extrusion O radial extrusion
2.8 The expression "tool and die repair" is most commonly used for... O the process of disassembling the die and replacing worn parts with fresh elements O the sequence of material addition (through welding) and subsequent machining to final precise shape in worn areas 2.9 What is the most common material to make deforming tools (dies)? X steel O ceramics O cemented carbide O diamond 2.10 What is one of the main advantages of additive manufacturing compared to subtractive manufacturing? X high degree of freedom with regard to workpiece geometry O high strength of workpieces that can be achieved (e.g. compared to milled workpieces with same workpiece dimensions) 2.11 How is the true strain of a deforming process calculated (referring to a simple upsetting process as explained in the lecture)? (h: height, index 0: prior to deforming) O phi, = In (h/h,) X phi, = In (h,/h.) O phi, = (h,-h,)/h, %3D %3D 2.12 In hot extrusion, the recrystallization process takes place during the deforming process. True O False 2.13 Which feature of the tool and or machine is an important difference between fine blanking and conventional shearing? O In fine blanking, the blank holder has a special geometrical feature ("Vee ring" or "v-ring") that is not used in conventional shearing O In conventional shearing, a counter punch is applied on the opposite side of the workpiece (than the punch) O Fine blanking tools are usually cooled whereas shearing tools usually do not have a cooling system. 2.14 Which bulk forming technology is used to make a cardan joint (a workpiece that resembles an "X" or a cross)? O full forward extrusion O cup backward extrusion O radial extrusion
Elements Of Electromagnetics
7th Edition
ISBN:9780190698614
Author:Sadiku, Matthew N. O.
Publisher:Sadiku, Matthew N. O.
ChapterMA: Math Assessment
Section: Chapter Questions
Problem 1.1MA
Related questions
Question
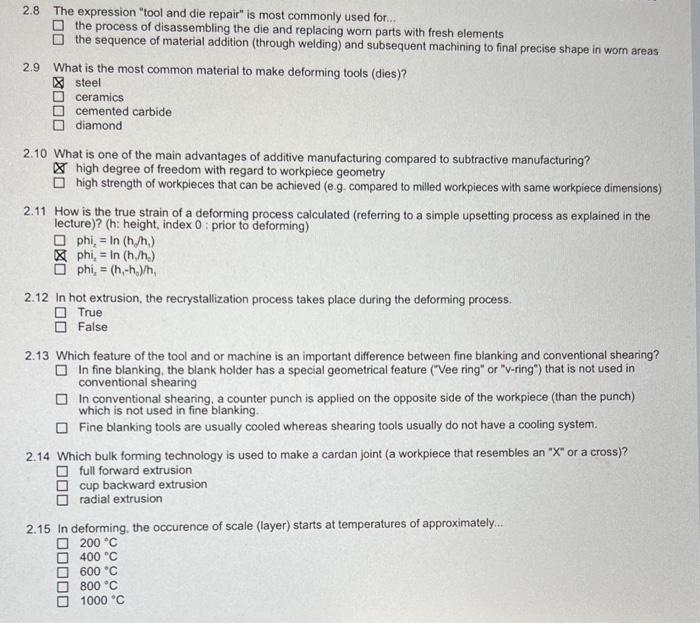
Transcribed Image Text:2.8 The expression "tool and die repair" is most commonly used for..
O the process of disassembling the die and replacing worn parts with fresh elements
O the sequence of material addition (through welding) and subsequent machining to final precise shape in worn areas
2.9 What is the most common material to make deforming tools (dies)?
X steel
O ceramics
O cemented carbide
O diamond
2.10 What is one of the main advantages of additive manufacturing compared to subtractive manufacturing?
X high degree of freedom with regard to workpiece geometry
O high strength of workpieces that can be achieved (e.g. compared to milled workpieces with same workpiece dimensions)
2.11 How is the true strain of a deforming process calculated (referring to a simple upsetting process as explained in the
lecture)? (h: height, index 0: prior to deforming)
O phi, = In (h,h,)
X phi, = In (h./h.)
O phi, = (h,-h./h,
2.12 In hot extrusion, the recrystallization process takes place during the deforming process.
O True
O False
2.13 Which feature of the tool and or machine is an important difference between fine blanking and conventional shearing?
O In fine blanking, the blank holder has a special geometrical feature ("Vee ring" or "v-ring") that is not used in
conventional shearing
O In conventional shearing, a counter punch is applied on the opposite side of the workpiece (than the punch)
which is not used in fine blanking.
O Fine blanking tools are usually cooled whereas shearing tools usually do not have a cooling system.
2.14 Which bulk forming technology is used to make a cardan joint (a workpiece that resembles an "X" or a cross)?
O full forward extrusion
O cup backward extrusion
radial extrusion
2.15 In deforming, the occurence of scale (layer) starts at temperatures of approximately.
O 200 °C
O 400 °C
600 °C
800 °C
1000 °C
Expert Solution

This question has been solved!
Explore an expertly crafted, step-by-step solution for a thorough understanding of key concepts.
Step by step
Solved in 2 steps with 2 images

Knowledge Booster
Learn more about
Need a deep-dive on the concept behind this application? Look no further. Learn more about this topic, mechanical-engineering and related others by exploring similar questions and additional content below.Recommended textbooks for you
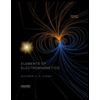
Elements Of Electromagnetics
Mechanical Engineering
ISBN:
9780190698614
Author:
Sadiku, Matthew N. O.
Publisher:
Oxford University Press
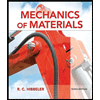
Mechanics of Materials (10th Edition)
Mechanical Engineering
ISBN:
9780134319650
Author:
Russell C. Hibbeler
Publisher:
PEARSON
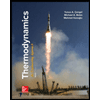
Thermodynamics: An Engineering Approach
Mechanical Engineering
ISBN:
9781259822674
Author:
Yunus A. Cengel Dr., Michael A. Boles
Publisher:
McGraw-Hill Education
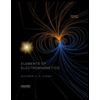
Elements Of Electromagnetics
Mechanical Engineering
ISBN:
9780190698614
Author:
Sadiku, Matthew N. O.
Publisher:
Oxford University Press
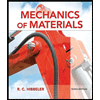
Mechanics of Materials (10th Edition)
Mechanical Engineering
ISBN:
9780134319650
Author:
Russell C. Hibbeler
Publisher:
PEARSON
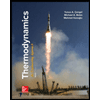
Thermodynamics: An Engineering Approach
Mechanical Engineering
ISBN:
9781259822674
Author:
Yunus A. Cengel Dr., Michael A. Boles
Publisher:
McGraw-Hill Education
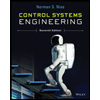
Control Systems Engineering
Mechanical Engineering
ISBN:
9781118170519
Author:
Norman S. Nise
Publisher:
WILEY
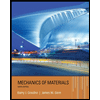
Mechanics of Materials (MindTap Course List)
Mechanical Engineering
ISBN:
9781337093347
Author:
Barry J. Goodno, James M. Gere
Publisher:
Cengage Learning
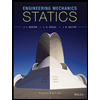
Engineering Mechanics: Statics
Mechanical Engineering
ISBN:
9781118807330
Author:
James L. Meriam, L. G. Kraige, J. N. Bolton
Publisher:
WILEY