A company is introducing reusable straws in the Canadian market on 1st of January 2022. They estimate the total market for reusable straws in Canada is approximately 3 million per year. The company expects to sell 500000 straws in the first year. There is a competitor already in the market whose sales per year is 1 million straws per year. Your group have been hired as consultants to answer the following questions: Q 1-The company is building a facility to produce 1 million straws per year. Is this capacity just right, too little or too much? What factors will you consider in building capacities? Should they adopt a a) leading strategy b) lag strategy or c) straddle strategy to build further capacities. Please justify. Q-2The company also wants you to recommend an aggregate planning strategy. They have provided you with the following information. Month Expected Demand Production Days January 2022 35000 22 February 2022 30000 18 March 37000 22 April 38000 21 May 39000 22 Workers pay per hour - $25.00 Number of labour hour required to produce 1 straw – 1 minute Number of hours in a shift – 8 hours The company operates two shifts The inventory carrying cost is 5 cents per unit The cost of increasing daily production rate (hiring and training) is $ 1 per unit The cost of decreasing daily production rate (layoffs) is $2 per unit Cost of subcontracting = 50 cents per unit Based on these data, what aggregate planning strategy should the company pursue.
A company is introducing reusable straws in the Canadian market on 1st of January 2022. They estimate the total market for reusable straws in Canada is approximately 3 million per year. The company expects to sell 500000 straws in the first year. There is a competitor already in the market whose sales per year is 1 million straws per year. Your group have been hired as consultants to answer the following questions:
Q 1-The company is building a facility to produce 1 million straws per year. Is this capacity just right, too little or too much? What factors will you consider in building capacities? Should they adopt a a) leading strategy b) lag strategy or c) straddle strategy to build further capacities. Please justify.
Q-2The company also wants you to recommend an aggregate planning strategy. They have provided you with the following information.
Month |
Expected Demand |
Production Days |
January 2022 |
35000 |
22 |
February 2022 |
30000 |
18 |
March |
37000 |
22 |
April |
38000 |
21 |
May |
39000 |
22 |
Workers pay per hour - $25.00
Number of labour hour required to produce 1 straw – 1 minute
Number of hours in a shift – 8 hours
The company operates two shifts
The inventory carrying cost is 5 cents per unit
The cost of increasing daily production rate (hiring and training) is $ 1 per unit
The cost of decreasing daily production rate (layoffs) is $2 per unit
Cost of subcontracting = 50 cents per unit
Based on these data, what aggregate planning strategy should the company pursue.

Step by step
Solved in 2 steps with 1 images

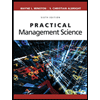
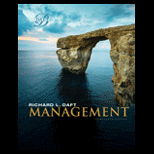
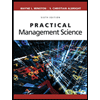
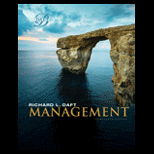