Develop a production schedule to produce the exact production requirements by varying the workforce size for the following problem. Also, evaluate the cost of the schedule. Use the example in the chapter as a guide (Plan 1). The monthly forecasts for Product X for January, February, and March are 1,000, 1,500, and 1,200, respectively. Safety stock policy recommends that half of the forecast for that month be defined as safety stock. There are 22 working days in January, 19 in February, and 21 in March. Beginning inventory is 500 units. Manufacturing cost is $200 per unit, storage cost is $3 per unit per month (based on expected end-of-month levels), standard pay rate is $6 per hour, overtime rate is $9 per hour, cost of backorder is $10 per unit per month, marginal cost of subcontracting is $10 per unit, hiring and training cost is $200 per worker, layoff cost is $300 per worker, and worker productivity is 0.1 unit per hour. Assume that you start off with 50 workers and that they work 8 hours per day.
Develop a production
The monthly forecasts for Product X for January, February, and March are 1,000, 1,500, and 1,200, respectively. Safety stock policy recommends that half of the

Trending now
This is a popular solution!
Step by step
Solved in 2 steps with 2 images

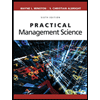
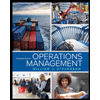
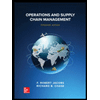
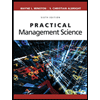
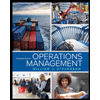
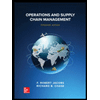
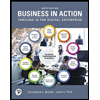
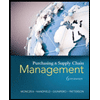
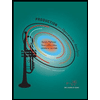