External Linkages, Activity-Based Supplier Costing Jackson, Inc., manufactures motorcycles. Jackson produces all the components necessary for the production of the cycles except for one (a carburetor). This component is purchased from two local suppliers: Harvey Parts and Curtis, Inc. Harvey sells the component for $62 per unit, while Curtis sells the same component for $56. Because of the lower price, Jackson purchases 75 percent of its components from Curtis. Jackson purchases the remaining 25 percent from Harvey to ensure an alternative source. The total annual demand is 157,000 carburetors. Harvey's sales manager is pushing Jackson to purchase more of its units, arguing that its component is of much higher quality and so should prove to be less costly than Curtis's lower-quality component. Harvey has sufficient capacity to supply all the carburetors needed and is asking for a long-term contract. With a five-year contract for 117,750 or more units, Harvey will sell the component for $59 per unit with a contractual provision for an annual product-specific inflationary adjustment. Jackson's purchasing manager is intrigued by the offer and wonders if the higher-quality carburetor actually does cost less than the lower-quality Curtis carburetor. To help assess the cost effect of the two products, the following data were collected for quality-related activities and suppliers: I. Activity data: Activity Cost Inspecting components (sampling only) $ 167,610 Expediting work (due to late delivery) 138,620 Reworking products (due to failed component) 957,600 Warranty work (due to failed component) 1,707,650 II. Supplier data: Harvey Curtis Unit purchase price $62 $56 Units purchased 39,250 117,750 Expediting orders 30 260 Sampling hours* 80 4,450 Rework hours 290 4,270 Warranty hours 280 5,670 *The Quality Control Department indicates that sampling inspection for the Harvey component has been reduced because the reject rate is so low. Required: 1. Calculate the cost per component for each supplier, taking into consideration the costs of the quality-related activities and using the current prices and sales volume. If required, round your unit cost answers to the nearest cent. Harvey Curtis Purchase cost $fill in the blank 1 $fill in the blank 2 Inspecting components fill in the blank 3 fill in the blank 4 Expediting work fill in the blank 5 fill in the blank 6 Reworking products fill in the blank 7 fill in the blank 8 Warranty work fill in the blank 9 fill in the blank 10 Total supplier cost $fill in the blank 11 $fill in the blank 12 Units supplied fill in the blank 13 fill in the blank 14 Unit cost $fill in the blank 15 $fill in the blank 16
External Linkages, Activity-Based Supplier Costing
Jackson, Inc., manufactures motorcycles. Jackson produces all the components necessary for the production of the cycles except for one (a carburetor). This component is purchased from two local suppliers: Harvey Parts and Curtis, Inc. Harvey sells the component for $62 per unit, while Curtis sells the same component for $56. Because of the lower price, Jackson purchases 75 percent of its components from Curtis. Jackson purchases the remaining 25 percent from Harvey to ensure an alternative source. The total annual demand is 157,000 carburetors.
Harvey's sales manager is pushing Jackson to purchase more of its units, arguing that its component is of much higher quality and so should prove to be less costly than Curtis's lower-quality component. Harvey has sufficient capacity to supply all the carburetors needed and is asking for a long-term contract. With a five-year contract for 117,750 or more units, Harvey will sell the component for $59 per unit with a contractual provision for an annual product-specific inflationary adjustment. Jackson's purchasing manager is intrigued by the offer and wonders if the higher-quality carburetor actually does cost less than the lower-quality Curtis carburetor. To help assess the cost effect of the two products, the following data were collected for quality-related activities and suppliers:
I. Activity data: | |||
Activity | Cost | ||
Inspecting components (sampling only) | $ | 167,610 | |
Expediting work (due to late delivery) | 138,620 | ||
Reworking products (due to failed component) | 957,600 | ||
Warranty work (due to failed component) | 1,707,650 |
II. Supplier data: | |||
Harvey | Curtis | ||
Unit purchase price | $62 | $56 | |
Units purchased | 39,250 | 117,750 | |
Expediting orders | 30 | 260 | |
Sampling hours* | 80 | 4,450 | |
Rework hours | 290 | 4,270 | |
Warranty hours | 280 | 5,670 |
*The Quality Control Department indicates that sampling inspection for the Harvey component has been reduced because the reject rate is so low.
Required:
1. Calculate the cost per component for each supplier, taking into consideration the costs of the quality-related activities and using the current prices and sales volume. If required, round your unit cost answers to the nearest cent.
Harvey | Curtis | |
Purchase cost | $fill in the blank 1 | $fill in the blank 2 |
Inspecting components | fill in the blank 3 | fill in the blank 4 |
Expediting work | fill in the blank 5 | fill in the blank 6 |
Reworking products | fill in the blank 7 | fill in the blank 8 |
Warranty work | fill in the blank 9 | fill in the blank 10 |
Total supplier cost | $fill in the blank 11 | $fill in the blank 12 |
Units supplied | fill in the blank 13 | fill in the blank 14 |
Unit cost | $fill in the blank 15 | $fill in the blank 16 |

Trending now
This is a popular solution!
Step by step
Solved in 2 steps with 1 images

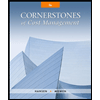
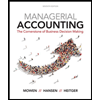
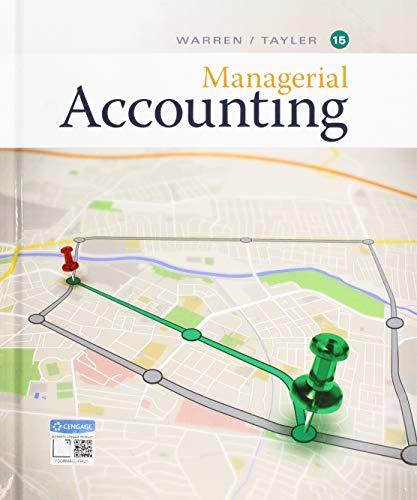
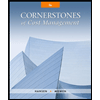
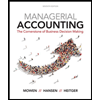
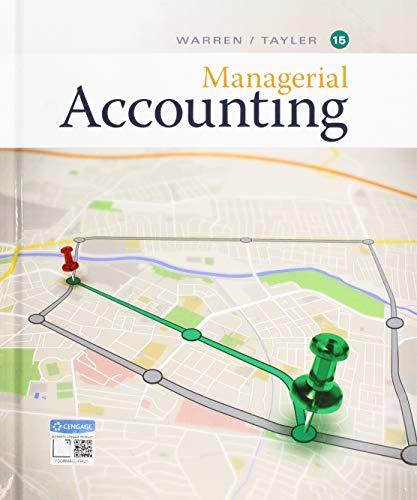