IMPORTANT: I HAVE SOLVED OTHER WORKSHEETS MYSELF WITH THE ATTACHMENT, I JUST NEED HELP STARTING FROM MANUFACTORING OVERHEAD BUDGET TO THE REST, PLEASE AND THANK YOU I WOULD BE GRATEFUL AND APPRECIATE YOUR HELP Manufacturing Overhead Budget January - June Variable Overhead (per DLH) January February March April May June Totals Indirect Materials (per DLH) $ 1.00 $ 1.00 $ 1.00 $ 1.00 $ 1.00 $ 1.00 $ 6.00 Indirect Labor (per DLH) $ 1.40 $ 1.40 $ 1.40 $ 1.40 $ 1.40 $ 1.40 $ 8.40 Utilities (per DLH) $ 0.10 $ 0.10 $ 0.10 $ 0.10 $ 0.10 $ 0.10 $ 0.60 Maintenance (per DLH) $ 0.30 $ 0.30 $ 0.30 $ 0.30 $ 0.30 $ 0.30 $ 1.80 Total Variable MOH per DL Hour $ 2.80 $ 2.80 $ 2.80 $ 2.80 $ 2.80 $ 2.80 $ 16.80 Total Direct Labor Hours 129 199 185 376 399 390 1678 Total Variable Overhead $ 360.50 $ 556.50 $ 518.00 $ 1,053.50 $ 1,118.25 $ 1,092.00 $ 4,698.75 Fixed Overhead (monthly costs) Utilities $ 800.00 $ 800.00 $ 800.00 $ 800.00 $ 800.00 $ 800.00 $ 4,800.00 Maintenance $ 400.00 $ 400.00 $ 400.00 $ 400.00 $ 400.00 $ 400.00 $ 2,400.00 Supervisory Salaries $ 2,500.00 $ 2,500.00 $ 2,500.00 $ 2,500.00 $ 2,500.00 $ 2,500.00 $ 15,000.00 Depreciation $ - Property Taxes $ - Total Fixed Overhead $ 3,700.00 $ 3,700.00 $ 3,700.00 $ 3,700.00 $ 3,700.00 $ 3,700.00 $ 22,200.00 Total Overhead Per Month $ 4,060.50 $ 4,256.50 $ 4,218.00 $ 4,753.50 $ 4,818.25 $ 4,792.00 $ 26,898.75 Direct Labor Hours 129 199 185 376 399 390 1678 MOH Rate per direct labor hour $ 16.03 Cost Per Unit Calculation Direct Materials: Quantity Cost Total wood 23 $ 0.30 $ 6.90 wheels 206 $ 0.10 $ 20.60 Direct Labor Cost $ - Total Overhead Cost $ 16.03 $ - Total Unit Cost $ 27.50 Total Unit Cost $ 27.50 Number of Trains Sold (Jan-June) 6650 Cost of Goods Sold $ 182,875 Selling and Administrative Budget January - June Months January February March April May June Totals Advertising
Master Budget
A master budget can be defined as an estimation of the revenue earned or expenses incurred over a specified period of time in the future and it is generally prepared on a periodic basis which can be either monthly, quarterly, half-yearly, or annually. It helps a business, an organization, or even an individual to manage the money effectively. A budget also helps in monitoring the performance of the people in the organization and helps in better decision-making.
Sales Budget and Selling
A budget is a financial plan designed by an undertaking for a definite period in future which acts as a major contributor towards enhancing the financial success of the business undertaking. The budget generally takes into account both current and future income and expenses.
IMPORTANT: I HAVE SOLVED OTHER WORKSHEETS MYSELF WITH THE ATTACHMENT, I JUST NEED HELP STARTING FROM MANUFACTORING OVERHEAD BUDGET TO THE REST, PLEASE AND THANK YOU I WOULD BE GRATEFUL AND APPRECIATE YOUR HELP
Manufacturing Overhead Budget | |||||||
January - June | |||||||
Variable Overhead (per DLH) | |||||||
January | February | March | April | May | June | Totals | |
Indirect Materials (per DLH) | $ 1.00 | $ 1.00 | $ 1.00 | $ 1.00 | $ 1.00 | $ 1.00 | $ 6.00 |
Indirect Labor (per DLH) | $ 1.40 | $ 1.40 | $ 1.40 | $ 1.40 | $ 1.40 | $ 1.40 | $ 8.40 |
Utilities (per DLH) | $ 0.10 | $ 0.10 | $ 0.10 | $ 0.10 | $ 0.10 | $ 0.10 | $ 0.60 |
Maintenance (per DLH) | $ 0.30 | $ 0.30 | $ 0.30 | $ 0.30 | $ 0.30 | $ 0.30 | $ 1.80 |
Total Variable MOH per DL Hour | $ 2.80 | $ 2.80 | $ 2.80 | $ 2.80 | $ 2.80 | $ 2.80 | $ 16.80 |
Total Direct Labor Hours | 129 | 199 | 185 | 376 | 399 | 390 | 1678 |
Total Variable Overhead | $ 360.50 | $ 556.50 | $ 518.00 | $ 1,053.50 | $ 1,118.25 | $ 1,092.00 | $ 4,698.75 |
Fixed Overhead (monthly costs) | |||||||
Utilities | $ 800.00 | $ 800.00 | $ 800.00 | $ 800.00 | $ 800.00 | $ 800.00 | $ 4,800.00 |
Maintenance | $ 400.00 | $ 400.00 | $ 400.00 | $ 400.00 | $ 400.00 | $ 400.00 | $ 2,400.00 |
Supervisory Salaries | $ 2,500.00 | $ 2,500.00 | $ 2,500.00 | $ 2,500.00 | $ 2,500.00 | $ 2,500.00 | $ 15,000.00 |
$ - | |||||||
Property Taxes | $ - | ||||||
Total Fixed Overhead | $ 3,700.00 | $ 3,700.00 | $ 3,700.00 | $ 3,700.00 | $ 3,700.00 | $ 3,700.00 | $ 22,200.00 |
Total Overhead Per Month | $ 4,060.50 | $ 4,256.50 | $ 4,218.00 | $ 4,753.50 | $ 4,818.25 | $ 4,792.00 | $ 26,898.75 |
Direct Labor Hours | 129 | 199 | 185 | 376 | 399 | 390 | 1678 |
MOH Rate per direct labor hour | $ 16.03 |
Cost Per Unit Calculation | |||||||
Direct Materials: | Quantity | Cost | Total | ||||
wood | 23 | $ 0.30 | $ 6.90 | ||||
wheels | 206 | $ 0.10 | $ 20.60 | ||||
Direct Labor Cost | $ - | ||||||
Total Overhead Cost | $ 16.03 | $ - | |||||
Total Unit Cost | $ 27.50 | ||||||
Total Unit Cost | $ 27.50 | ||||||
Number of Trains Sold (Jan-June) | 6650 | ||||||
Cost of Goods Sold | $ 182,875 |
Selling and Administrative Budget | |||||||
January - June | |||||||
Months | January | February | March | April | May | June | Totals |
Advertising | $ - | ||||||
Office Salaries | $ - | ||||||
Depreciation | $ - | ||||||
Property Taxes | $ - | ||||||
Total | $ - | $ - | $ - | $ - | $ - | $ - | $ - |
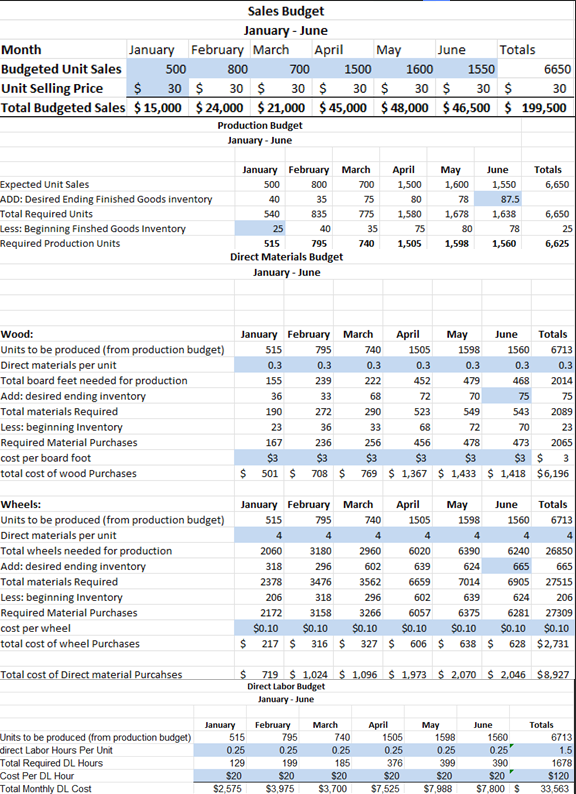
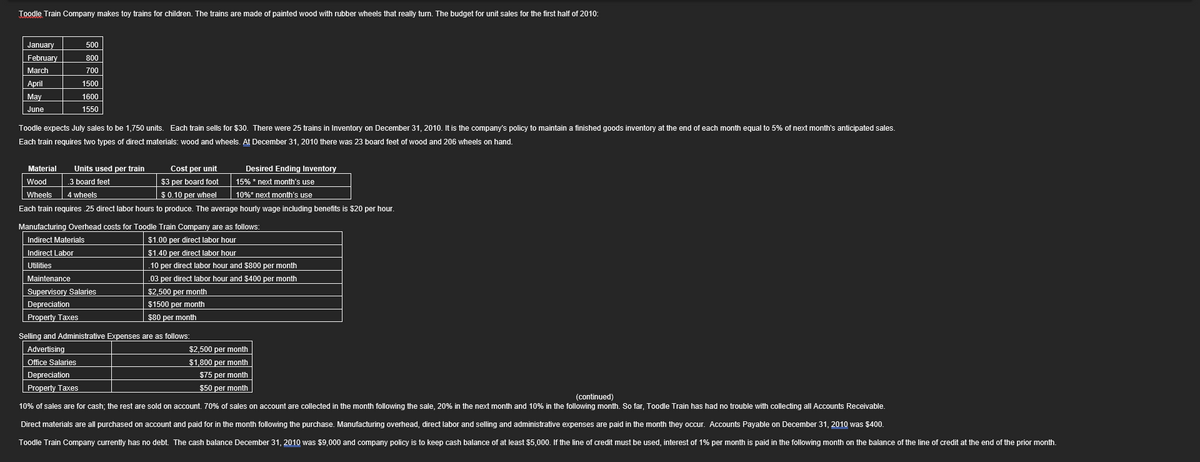

Step by step
Solved in 4 steps with 2 images

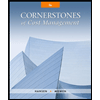
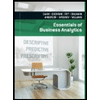
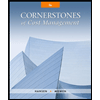
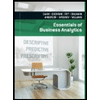
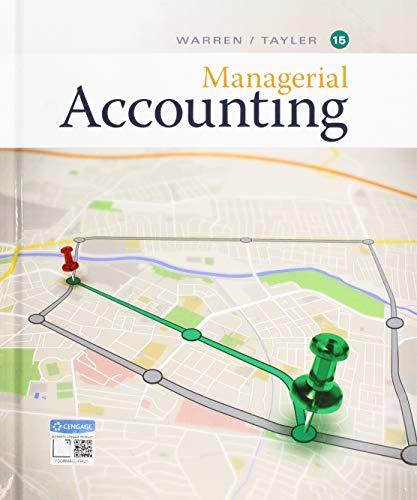
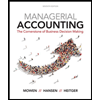