Silicon Valley Transport Commission (SVTC) has a fleet of maintenance vehicles that includes cars, vans, and trucks. SVTC is currently evaluating four different approaches to help them maintain their fleet of cars and vans efficiently at the lowest possible cost. Their options are: (1) No preventive maintenance at all and repair vehicle components when they fail; (2) Take oil samples at regular intervals and perform whatever preventive maintenance is indicated by the oil analysis; (3) Perform an oil change on a regular basis on each vehicle and perform repairs when needed; (4) perform oil changes at regular intervals, take oil samples regularly, and perform maintenance repairs as indicated by the sample analysis. Option #1 costs nothing to implement and results in two possible outcomes: There is a .10 probability that a defective component will occur, requiring emergency maintenance at a cost of $1,200, or there is a chance that no defects will occur and no maintenance will be necessary. Option #2 costs $20 to implement, and there is a .10 probability that the maintenance crew will discover a defective part. If the crew actually finds a defective part, there is a .70 probability that the sample will correctly identify it, resulting in preventive maintenance at a cost of $500. However, there is a .30 probability that the sample will not identify the defect and indicate that everything is okay, resulting in emergency maintenance later at a cost of $1,200. On the other hand, if there are actually no defects, there is a .20 probability that the sample will erroneously indicate that there is a defect, resulting in unnecessary maintenance at a cost of $250. There is an .80 probability that the sample will correctly indicate that there are no defects, resulting in no maintenance and no costs. Option #3 costs $14.80 to implement and has two outcomes: a .04 probability of a defective component, which will require emergency maintenance at a cost of $1,200, and a chance that no defects will occur, hence no need for maintenance and no cost expended. Option #4 costs $34.80 to implement and results in the same probabilities of defects and no defects as Option #3. If there is a defective component, there is a .70 probability that the sample will detect it and $500 in preventive maintenance costs will be incurred. Alternatively, there is a .30 probability that the sample will not detect the defect, resulting in emergency maintenance at a cost of $1,200. If there is no defect, there is a .20 probability that the sample will indicate that there is a defect, resulting in an unnecessary maintenance cost of $250, and there is an .80 probability that the sample will correctly indicate no defects, resulting in no cost. 1. Using decision analysis, and only considering the cost, the best decision is Option 4: Perform oil changes at regular intervals, take oil samples regularly, and perform maintenance repairs as indicated by the sample analysis. Option 3: Perform an oil change on a regular basis on each vehicle and perform repairs when needed. Option 2: Take oil samples at regular intervals and perform whatever preventive maintenance is indicated by the oil analysis. Cannot be determined. Option 1: No preventive maintenance at all and repair vehicle components when they fail. 2. Using decision analysis, and only considering the cost, the expected value of your best decision is $ 3. Using decision analysis, the amount difference between the expected valu
Critical Path Method
The critical path is the longest succession of tasks that has to be successfully completed to conclude a project entirely. The tasks involved in the sequence are called critical activities, as any task getting delayed will result in the whole project getting delayed. To determine the time duration of a project, the critical path has to be identified. The critical path method or CPM is used by project managers to evaluate the least amount of time required to finish each task with the least amount of delay.
Cost Analysis
The entire idea of cost of production or definition of production cost is applied corresponding or we can say that it is related to investment or money cost. Money cost or investment refers to any money expenditure which the firm or supplier or producer undertakes in purchasing or hiring factor of production or factor services.
Inventory Management
Inventory management is the process or system of handling all the goods that an organization owns. In simpler terms, inventory management deals with how a company orders, stores, and uses its goods.
Project Management
Project Management is all about management and optimum utilization of the resources in the best possible manner to develop the software as per the requirement of the client. Here the Project refers to the development of software to meet the end objective of the client by providing the required product or service within a specified Period of time and ensuring high quality. This can be done by managing all the available resources. In short, it can be defined as an application of knowledge, skills, tools, and techniques to meet the objective of the Project. It is the duty of a Project Manager to achieve the objective of the Project as per the specifications given by the client.
Silicon Valley Transport Commission (SVTC) has a fleet of maintenance vehicles that includes cars, vans, and trucks. SVTC is currently evaluating four different approaches to help them maintain their fleet of cars and vans efficiently at the lowest possible cost. Their options are: (1) No preventive maintenance at all and repair vehicle components when they fail; (2) Take oil samples at regular intervals and perform whatever preventive maintenance is indicated by the oil analysis; (3) Perform an oil change on a regular basis on each vehicle and perform repairs when needed; (4) perform oil changes at regular intervals, take oil samples regularly, and perform maintenance repairs as indicated by the sample analysis.
Option #1 costs nothing to implement and results in two possible outcomes: There is a .10 probability that a defective component will occur, requiring emergency maintenance at a cost of $1,200, or there is a chance that no defects will occur and no maintenance will be necessary.
Option #2 costs $20 to implement, and there is a .10 probability that the maintenance crew will discover a defective part. If the crew actually finds a defective part, there is a .70 probability that the sample will correctly identify it, resulting in preventive maintenance at a cost of $500. However, there is a .30 probability that the sample will not identify the defect and indicate that everything is okay, resulting in emergency maintenance later at a cost of $1,200. On the other hand, if there are actually no defects, there is a .20 probability that the sample will erroneously indicate that there is a defect, resulting in unnecessary maintenance at a cost of $250. There is an .80 probability that the sample will correctly indicate that there are no defects, resulting in no maintenance and no costs.
Option #3 costs $14.80 to implement and has two outcomes: a .04 probability of a defective component, which will require emergency maintenance at a cost of $1,200, and a chance that no defects will occur, hence no need for maintenance and no cost expended.
Option #4 costs $34.80 to implement and results in the same probabilities of defects and no defects as Option #3. If there is a defective component, there is a .70 probability that the sample will detect it and $500 in preventive maintenance costs will be incurred. Alternatively, there is a .30 probability that the sample will not detect the defect, resulting in emergency maintenance at a cost of $1,200. If there is no defect, there is a .20 probability that the sample will indicate that there is a defect, resulting in an unnecessary maintenance cost of $250, and there is an .80 probability that the sample will correctly indicate no defects, resulting in no cost.
1. Using decision analysis, and only considering the cost, the best decision is

Step by step
Solved in 2 steps

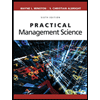
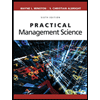