Techno Instruments uses a manufacturing costing system with one direct-cost category (direct materials) and three indirect-cost categories: a. Setup, production-order, and materials-handling costs that vary with the number of batches b. Manufacturing-operations costs that vary with machine-hours c. Costs of engineering changes that vary with the number of engineering changes made In response to competitive pressures at the end of 2016, Techno Instruments used value-engineering techniques to reduce manufacturing costs. Actual information for 2016 and 2017 is as follows: 2016 2017 Setup, production-order, and materials-handling costs per batch $8,600 $7,800 Total manufacturing-operations cost per machine-hour $59 $53 Cost per engineering change $18,750 $14,000 The management of Techno Instruments wants to evaluate whether value engineering has succeeded in reducing the target manufacturing cost per unit of one of its products, HJ6, by 20%. Actual results for 2016 and 2017 for HJ6 are: Actual Results for 2016 Actual Results for 2017 Units of HJ6 produced 6,000 7,000 Direct material cost per unit of HJ6 $1,800 $1,400 Total number of batches required to produce HJ6 80 90 Total machine-hours required to produce HJ6 39,600 36,400 Number of engineering changes made 16 10 1. Calculate the manufacturing cost per unit of HJ6 in 2016. 2. Calculate the manufacturing cost per unit of HJ6 in 2017. 3. Did Techno Instruments achieve the target manufacturing cost per unit for HJ6 in 2017? Explain.
Process Costing
Process costing is a sort of operation costing which is employed to determine the value of a product at each process or stage of producing process, applicable where goods produced from a series of continuous operations or procedure.
Job Costing
Job costing is adhesive costs of each and every job involved in the production processes. It is an accounting measure. It is a method which determines the cost of specific jobs, which are performed according to the consumer’s specifications. Job costing is possible only in businesses where the production is done as per the customer’s requirement. For example, some customers order to manufacture furniture as per their needs.
ABC Costing
Cost Accounting is a form of managerial accounting that helps the company in assessing the total variable cost so as to compute the cost of production. Cost accounting is generally used by the management so as to ensure better decision-making. In comparison to financial accounting, cost accounting has to follow a set standard ad can be used flexibly by the management as per their needs. The types of Cost Accounting include – Lean Accounting, Standard Costing, Marginal Costing and Activity Based Costing.
Instruments uses a manufacturing costing system with one direct-cost category (direct materials) and three indirect-cost categories:
a.
|
Setup, production-order, and materials-handling costs that vary with the number of batches
|
b.
|
Manufacturing-operations costs that vary with machine-hours
|
c.
|
Costs of engineering changes that vary with the number of engineering changes made
|
|
2016
|
2017
|
---|---|---|
Setup, production-order, and materials-handling costs per batch
|
$8,600
|
$7,800
|
Total manufacturing-operations cost per machine-hour
|
$59
|
$53
|
Cost per engineering change
|
$18,750
|
$14,000
|
|
Actual Results for 2016
|
Actual Results for 2017
|
---|---|---|
Units of HJ6 produced
|
6,000
|
7,000
|
Direct material cost per unit of HJ6
|
$1,800
|
$1,400
|
Total number of batches required to produce HJ6
|
80
|
90
|
Total machine-hours required to produce HJ6
|
39,600
|
36,400
|
Number of engineering changes made
|
16
|
10
|
1.
|
Calculate the manufacturing cost per unit of HJ6 in
2016.
|
2.
|
Calculate the manufacturing cost per unit of HJ6 in
2017.
|
3.
|
Did
Techno
Instruments achieve the target manufacturing cost per unit for HJ6 in
2017?
Explain. |
4.
|
Explain how
Techno
Instruments reduced the manufacturing cost per unit of HJ6 in
2017.
|
5.
|
What challenges might managers at
Techno
Instruments encounter in achieving the target cost? How might they overcome these challenges? |

Trending now
This is a popular solution!
Step by step
Solved in 3 steps

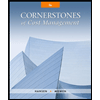
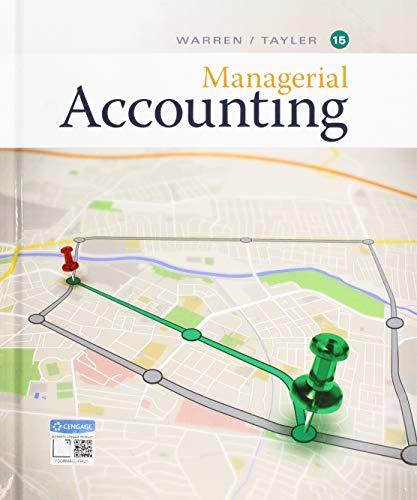
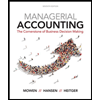
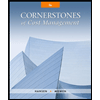
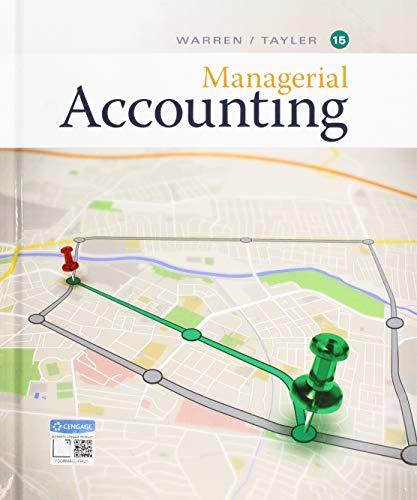
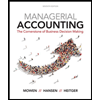
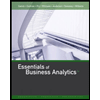
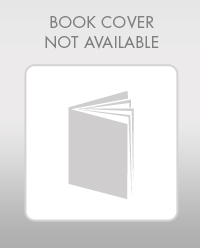