Tombro Industries is in the process of automating one of its plants and developing a flexible manufacturing system. The company is finding it necessary to make many changes in operating procedures. Progress has been slow, particularly in trying to develop new performance measures for the factory. In an effort to evaluate performance and determine where improvements can be made, management has gathered the following data relating to activities over the last four months: Month 1 2 3 4 Quality control measures: Number of defects 185 163 124 91 Number of warranty claims 46 39 30 27 Number of customer complaints 102 96 79 58 Material control measures: Purchase order lead time 8 days 7 days 5 days 4 days Scrap as a percent of total cost 1% 1% 2% 3% Machine performance measures: Machine downtime as a percentage of availability 3% 4% 4% 6% Use as a percentage of availability 95% 92% 89% 85% Setup time (hours) 8 10 11 12 Delivery performance measures: Throughput time ? ? ? ? Manufacturing cycle efficiency (MCE) ? ? ? ? Delivery cycle time ? ? ? ? Percentage of on-time deliveries 96% 95% 92% 89% The president has read in industry journals that throughput time, MCE, and delivery cycle time are important measures of performance, but no one is sure how they are computed. You have been asked to assist the company, and you have gathered the following data relating to these measures: Average per Month (in days) 1 2 3 4 Wait time per order before start of production 9.0 11.5 12.0 14.0 Inspection time per unit 0.8 0.7 0.7 0.7 Process time per unit 2.1 2.0 1.9 1.8 Queue time per unit 2.8 4.4 6.0 7.0 Move time per unit 0.3 0.4 0.4 0.5 Required: 1-a. Compute the throughput time for each month. 1-b. Compute the manufacturing cycle efficiency (MCE) for each month. 1-c. Compute the delivery cycle time for each month. 3-a. Refer to the inspection time, process time, and so forth, given for month 4. Assume that in month 5 the inspection time, process time, and so forth, are the same as for month 4, except that the company is able to completely eliminate the queue time during production using Lean Production. Compute the new throughput time and MCE. 3-b. Refer to the inspection time, process time, and so forth, given for month 4. Assume that in month 6 the inspection time, process time, and so forth, are the same as in month 4, except that the company is able to eliminate both the queue time during production and the inspection time using Lean Production. Compute the new throughput time and MCE. sub parts 3a and 3b only
Tombro Industries is in the process of automating one of its plants and developing a flexible manufacturing system. The company is finding it necessary to make many changes in operating procedures. Progress has been slow, particularly in trying to develop new performance measures for the factory.
In an effort to evaluate performance and determine where improvements can be made, management has gathered the following data relating to activities over the last four months:
Month | ||||||||
---|---|---|---|---|---|---|---|---|
1 | 2 | 3 | 4 | |||||
Quality control measures: | ||||||||
Number of defects | 185 | 163 | 124 | 91 | ||||
Number of warranty claims | 46 | 39 | 30 | 27 | ||||
Number of customer complaints | 102 | 96 | 79 | 58 | ||||
Material control measures: | ||||||||
Purchase order lead time | 8 | days | 7 | days | 5 | days | 4 | days |
Scrap as a percent of total cost | 1% | 1% | 2% | 3% | ||||
Machine performance measures: | ||||||||
Machine downtime as a percentage of availability | 3% | 4% | 4% | 6% | ||||
Use as a percentage of availability | 95% | 92% | 89% | 85% | ||||
Setup time (hours) | 8 | 10 | 11 | 12 | ||||
Delivery performance measures: | ||||||||
Throughput time | ? | ? | ? | ? | ||||
Manufacturing cycle efficiency (MCE) | ? | ? | ? | ? | ||||
Delivery cycle time | ? | ? | ? | ? | ||||
Percentage of on-time deliveries | 96% | 95% | 92% | 89% |
The president has read in industry journals that throughput time, MCE, and delivery cycle time are important measures of performance, but no one is sure how they are computed. You have been asked to assist the company, and you have gathered the following data relating to these measures:
Average per Month (in days) | ||||
---|---|---|---|---|
1 | 2 | 3 | 4 | |
Wait time per order before start of production | 9.0 | 11.5 | 12.0 | 14.0 |
Inspection time per unit | 0.8 | 0.7 | 0.7 | 0.7 |
Process time per unit | 2.1 | 2.0 | 1.9 | 1.8 |
Queue time per unit | 2.8 | 4.4 | 6.0 | 7.0 |
Move time per unit | 0.3 | 0.4 | 0.4 | 0.5 |
Required:
1-a. Compute the throughput time for each month.
1-b. Compute the manufacturing cycle efficiency (MCE) for each month.
1-c. Compute the delivery cycle time for each month.
3-a. Refer to the inspection time, process time, and so forth, given for month 4. Assume that in month 5 the inspection time, process time, and so forth, are the same as for month 4, except that the company is able to completely eliminate the queue time during production using Lean Production. Compute the new throughput time and MCE.
3-b. Refer to the inspection time, process time, and so forth, given for month 4. Assume that in month 6 the inspection time, process time, and so forth, are the same as in month 4, except that the company is able to eliminate both the queue time during production and the inspection time using Lean Production. Compute the new throughput time and MCE.
sub parts 3a and 3b only

Trending now
This is a popular solution!
Step by step
Solved in 3 steps

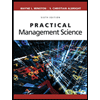
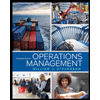
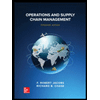
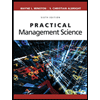
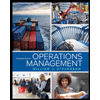
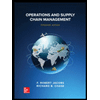
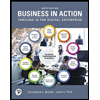
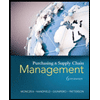
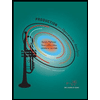