Using your own words, explain in brief the idea behind six-sigma concept, and how it does benefit the business?
Using your own words, explain in brief the idea behind six-sigma concept, and how it does benefit the business?
Practical Management Science
6th Edition
ISBN:9781337406659
Author:WINSTON, Wayne L.
Publisher:WINSTON, Wayne L.
Chapter2: Introduction To Spreadsheet Modeling
Section: Chapter Questions
Problem 20P: Julie James is opening a lemonade stand. She believes the fixed cost per week of running the stand...
Related questions
Question
Using your own words, explain in brief the idea behind six-sigma concept, and how it does benefit the business? ( 100 -150 words)
note : I couldn't upload al photos of case study
so this the link https://www.researchgate.net/publication/324817361_Using_Six_Sigma_DMAIC_to_Improve_the_Quality_of_the_Production_Process_A_Case_Study

Transcribed Image Text:.ull mobily ?
4:03 AM
96%
( Back 1-s2.0-S187704281830...
Using Six Sigma DMAIC to improve the quality of
the production process: a case study
Monika Smętkowska, Beata Mrugalska"
Poznan University of Technology, Faculty of Engineering Management,ul. Strzelecka 11, 60-965 Poznan, Poland
Abstract
Over the last two decades there has been a growing awareness of the need to improve quality in the industrial sector. This paper
presents how to implement the DMAIC cycle as an element of continuous improvement in practice. In order to achieve it, the
problem of quality and quality improvement is widely discussed. Based on the recognized problem in the organization, an
analysis with the application of DMAIC is done. The propositions of improvements, which can be implemented in the
organization in order to increase the effectiveness of production process, are also presented.
© 2018 Published by Elsevier Ltd. This is an open access article under the CC BY-NC-ND license
(http://creativecommons.org/licenses/by-nc-nd/4.0/).
Peer-review under responsibility of SIM 2017 / 14th International Symposium in Management.
Keywords: DMAIC; quality; improvement; Six Sigma
1. Introduction
Nowadays, there is a huge pressure on organizations to improve the customer satisfaction and quality in the
organization, and at the same time to decrease ineffectiveness and reduce the number of errors. The organizations
have to solicit to gain and keep customers, because now, they are the key elements that drive economy. There are
many different conceptions, methods and tools that may be used to maintain the good quality level and help in
continuous development in the company (Zu, et al., 2008; Bendoly, 2016; Gołaś, et al., 2016). For example, it can
* Corresponding author. Tel.: +48-61-665-3364; fax: +48-61- 665-3375.
E-mail address: beata.mrugalska@put.poznan.pl
1877-0428 © 2018 Published by Elsevier Ltd. This is an open access article under the CC BY-NC-ND license
(http://creativecommons.org/licenses/by-nc-nd/4.0/).
Peer-review under responsibility of SIM 2017 / 14th International Symposium in Management.
doi:10.1016/j.sbspro.2018.04.039
Monika Smętkowska and Beata Mrugalska / Procedia - Social and Behavioral Sciences 238 (2018) 590 – 596
591
be Six Sigma which is an innovative method of quality management introduced in Motorola by Bob Galvin and Bill
Smith in the middle of the eighties (Schroeder et al., 2008; Evans & Lindsay, 2014).
"Sigma" is a notion taken from statistics. It means any standard deviation of the random variable around the
mean value. Therefore, Six Sigma means six times the distance of standard deviation. To achieve Six Sigma a
process cannot produce more than 3.4 defects per million opportunities. A defect is defined as anything outside the
customer specifications (Moosa, & Sajid, 2010; Lei, 2015). It is inseparably connected with the principles of TQM.
Due to its dynamic character it has become one of the most effective tools in continuous development and pursuit of
oxeelloee
Siv Sig mo hog develo
CYstomotized
u atotiatioel ond husinesa tools vhila vod:
seata

Transcribed Image Text:ll mobily ?
4:03 AM
96%
Back 1-s2.0-S187704281830...
Peer-Tevievw unuer TesponsIomty OI SIM ZU17T 140 IMeTTiational Symposium II Management.
doi:10.1016/j.sbspro.2018.04.039
Monika Smętkowska and Beata Mrugalska / Procedia - Social and Behavioral Sciences 238 (2018) 590 – 596
591
be Six Sigma which is an innovative method of quality management introduced in Motorola by Bob Galvin and Bill
Smith in the middle of the eighties (Schroeder et al., 2008; Evans & Lindsay, 2014).
"Sigma" is a notion taken from statistics. It means any standard deviation of the random variable around the
mean value. Therefore, Six Sigma means six times the distance of standard deviation. To achieve Six Sigma a
process cannot produce more than 3.4 defects per million opportunities. A defect is defined as anything outside the
customer specifications (Moosa, & Sajid, 2010; Lei, 2015). It is inseparably connected with the principles of TQM.
Due to its dynamic character it has become one of the most effective tools in continuous development and pursuit of
excellence. Six Sigma has developed and systematized many statistical and business tools while reducing costs,
defects and cycle time of production, and at the time increasing market share, maintaining customers, product
development. Its program can be used at every stage of the production and administrative process (Zu, et al., 2008;
Glasgow et al., 2010).
Six Sigma is perceived as a philosophy or concept of a broad sense. Using it as a philosophy helps with changing
the world and transformation of an enterprise. Treating it as a strategy ensures development and increases the
position of the company. It is based on six main principles which should be implemented in companies that want to
develop and increase their position on the market. The very first point is concentration on the customer. Every
action, which is taken, should be in agreement with customers’ specifications and requirements. Six Sigma is also
based on real data and facts which are used to perform a detailed analysis. It is based on continuous improvement of
all aspects of functioning development in the organization as well as proactive management and cooperation without
boundaries at every level in enterprise. It should be underlined that it is not only an approach for solving the
problems with manufacturing but also business processes (Taborski, 2010).
2. DMAIC cycle
Among many different tools of quality management which may be considered as methods of quality
improvement, there are two main ones used in Six Sigma concept: DMAIC and DMADV (Kumar & Sosnoski,
2009; Jones, et al., 2010). DMAIC is an acronym from the words Define-Measure-Analyze-Improve-Control. This
method is based on process improvement according to Deming cycle. It is a process improvement of many different
areas in the enterprise. DMAIC cycle consists of five stages which are connected with each other (Sokovic, et al.,
2010; Sin, et al., 2015):
Defining the goal and its requirements:
V defining needed resources and responsibilities,
V defining organization structure which is favorable to achieve the goals,
identification of the elements and setting the estimated date of the end of project,
V obtaining support from management.
The main purpose of this stage is to verify if the actions, which should be taken in order to solve the problems, are
connected with the priorities in the organization and that there is support from management and availability of
required resources. It starts with identifying the problem which needs a solution and ends with understanding this
issues as well as a clear evidence of management supervision. There are a lot of ways how to identify a project for
improvement. Firstly, it is better to focus on external factors, which create the cost for organization and take the
actions to eliminate them and after that solve the internal-costs problems. A useful tool which helps to narrow the
problem can be Pareto diagram (Shankar, 2009).
Measuring the current process:
identification of valid and reliable metrics,
V checking if there is enough data to measure,
documentation of current performance and effectiveness,
performing comparative tests.
The measure stage concerns gathering information about processes which are going to be improved. It focuses on
Expert Solution

This question has been solved!
Explore an expertly crafted, step-by-step solution for a thorough understanding of key concepts.
Step by step
Solved in 2 steps

Recommended textbooks for you
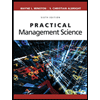
Practical Management Science
Operations Management
ISBN:
9781337406659
Author:
WINSTON, Wayne L.
Publisher:
Cengage,
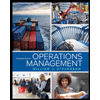
Operations Management
Operations Management
ISBN:
9781259667473
Author:
William J Stevenson
Publisher:
McGraw-Hill Education
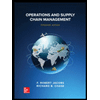
Operations and Supply Chain Management (Mcgraw-hi…
Operations Management
ISBN:
9781259666100
Author:
F. Robert Jacobs, Richard B Chase
Publisher:
McGraw-Hill Education
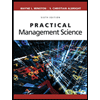
Practical Management Science
Operations Management
ISBN:
9781337406659
Author:
WINSTON, Wayne L.
Publisher:
Cengage,
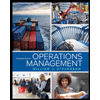
Operations Management
Operations Management
ISBN:
9781259667473
Author:
William J Stevenson
Publisher:
McGraw-Hill Education
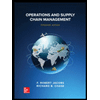
Operations and Supply Chain Management (Mcgraw-hi…
Operations Management
ISBN:
9781259666100
Author:
F. Robert Jacobs, Richard B Chase
Publisher:
McGraw-Hill Education
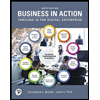
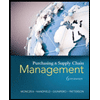
Purchasing and Supply Chain Management
Operations Management
ISBN:
9781285869681
Author:
Robert M. Monczka, Robert B. Handfield, Larry C. Giunipero, James L. Patterson
Publisher:
Cengage Learning
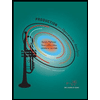
Production and Operations Analysis, Seventh Editi…
Operations Management
ISBN:
9781478623069
Author:
Steven Nahmias, Tava Lennon Olsen
Publisher:
Waveland Press, Inc.