water separator efficiency will be lower if oilwater emulsion is present in the separator feed (iniet fluid). One alternative to break emulsions is the use of chemical demulsifiers. A demulsifier system (chemical pump injection), installed upstream of the separator, has a capacity to treat up to 40,000 barrels of fluid per day. However, the actual average daily demand is 90%. The following cost expenditure data are below. Determine the present worth, future worth and annual worth capital equivalent. Use 8% interest rate per year. Estimate the unitary cost per barrel (S/bbl) for the use of this chemical, assuming a project life of 10 years. Investment: Chemical iniertion
water separator efficiency will be lower if oilwater emulsion is present in the separator feed (iniet fluid). One alternative to break emulsions is the use of chemical demulsifiers. A demulsifier system (chemical pump injection), installed upstream of the separator, has a capacity to treat up to 40,000 barrels of fluid per day. However, the actual average daily demand is 90%. The following cost expenditure data are below. Determine the present worth, future worth and annual worth capital equivalent. Use 8% interest rate per year. Estimate the unitary cost per barrel (S/bbl) for the use of this chemical, assuming a project life of 10 years. Investment: Chemical iniertion
Managerial Economics: Applications, Strategies and Tactics (MindTap Course List)
14th Edition
ISBN:9781305506381
Author:James R. McGuigan, R. Charles Moyer, Frederick H.deB. Harris
Publisher:James R. McGuigan, R. Charles Moyer, Frederick H.deB. Harris
Chapter8: Cost Analysis
Section: Chapter Questions
Problem 1.3CE
Related questions
Question
3

Transcribed Image Text:te tacilities.
An oil/water separator efficiency will be lower if oil/water emulsion is present in the separator feed
(inlet fluid). One alternative to break emulsions is the use of chemical demulsifiers. A demulsifier system
(chemical pump injection), installed upstream of the separator, has a capacity to treat up to 40,000
barrels of fluid per day. However, the actual average daily demand is 90%. The following cost
expenditure data are below. Determine the present worth, future worth and annual worth capital
equivalent. Use 8% interest rate per vear. Estimate the unitary cost per barrel (S/bbl) for the use of
this chemical, assuming a project life of 10 years.
Investment:
Chemical injection system: $ 50,000 (the investment includes 3 positive displacement 0.25 hp
pumps, each with electric motor, and storage tanks)
Annual expenses
Electricity: $ 600
Maintenance and repair: $ 10,000
Operation: $ 120,000
Chemical consumption and cost: 10 gallons of demulsifier per day at $60 per gallon.
Future
Pump overhaul cost $400 per pump at the fifth year.
Salvage value at end of the useful life: negligible.
Expert Solution

This question has been solved!
Explore an expertly crafted, step-by-step solution for a thorough understanding of key concepts.
Step by step
Solved in 2 steps

Knowledge Booster
Learn more about
Need a deep-dive on the concept behind this application? Look no further. Learn more about this topic, economics and related others by exploring similar questions and additional content below.Recommended textbooks for you
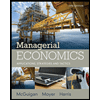
Managerial Economics: Applications, Strategies an…
Economics
ISBN:
9781305506381
Author:
James R. McGuigan, R. Charles Moyer, Frederick H.deB. Harris
Publisher:
Cengage Learning
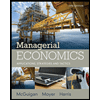
Managerial Economics: Applications, Strategies an…
Economics
ISBN:
9781305506381
Author:
James R. McGuigan, R. Charles Moyer, Frederick H.deB. Harris
Publisher:
Cengage Learning