Your company produces sandwich cookie snack packs. There are three main processes used to make the cookies. The first process preps and mixes the ingredients into the cookie and the filling. The second process shapes, forms and bakes the cookies. The third process packages the cookies. The cookies are sold in cases of 30 cookie packs (1 case is a unit) Information on the direct materials is listed in table 1. Consider this information the standard. Direct labor information given in Table 2. Consider this information the standard. Annual overhead information is given in Table 3. Overhead is allocated based direct labor hours. Estimated annual direct labor hours are 221,800. Calculate a predetermined OH rate (round to two decimal places if needed). Use this rate when you need to apply OH. Table 4 gives you the information for the last six months on the manufacturing overhead cost and machine hours. Using the high/low method of cost estimation and this information, determine the fixed and variable portions of the manufacturing overhead cost. (You will need this information to complete Table 5). Machine hours have been determined as the best cost driver for manufacturing OH. It takes one machine hour to make 200 cases of cookies. Table 5 is where you will list all your production cost (DM, DL, MOH), separated into their fixed and variable components. Note this table wants variable cost per unit and annual fixed cost. Table 1: Direct Materials Material Quantity per unit Cost Total per unit Cookie Ingredients 240 grams $0.0065 $1.56
Process Costing
Process costing is a sort of operation costing which is employed to determine the value of a product at each process or stage of producing process, applicable where goods produced from a series of continuous operations or procedure.
Job Costing
Job costing is adhesive costs of each and every job involved in the production processes. It is an accounting measure. It is a method which determines the cost of specific jobs, which are performed according to the consumer’s specifications. Job costing is possible only in businesses where the production is done as per the customer’s requirement. For example, some customers order to manufacture furniture as per their needs.
ABC Costing
Cost Accounting is a form of managerial accounting that helps the company in assessing the total variable cost so as to compute the cost of production. Cost accounting is generally used by the management so as to ensure better decision-making. In comparison to financial accounting, cost accounting has to follow a set standard ad can be used flexibly by the management as per their needs. The types of Cost Accounting include – Lean Accounting, Standard Costing, Marginal Costing and Activity Based Costing.
Your company produces sandwich cookie snack packs. There are three main processes used to make the cookies. The first process preps and mixes the ingredients into the cookie and the filling. The second process shapes, forms and bakes the cookies. The third process packages the cookies. The cookies are sold in cases of 30 cookie packs (1 case is a unit)
Information on the direct materials is listed in table 1. Consider this information the standard. Direct labor information given in Table 2. Consider this information the standard.
Annual overhead information is given in Table 3. Overhead is allocated based direct labor hours. Estimated annual direct labor hours are 221,800. Calculate a predetermined OH rate (round to two decimal places if needed). Use this rate when you need to apply OH.
Table 4 gives you the information for the last six months on the
Table 5 is where you will list all your production cost (DM, DL, MOH), separated into their fixed and variable components. Note this table wants variable cost per unit and annual fixed cost.
Table 1: Direct Materials
Material |
Quantity per unit |
Cost |
Total per unit |
Cookie Ingredients |
240 grams |
$0.0065 |
$1.56 |
Filling |
90 grams |
0.0080 |
0.72 |
Packaging 1 |
1 box |
0.2000 |
0.20 |
Packaging 2 |
30 wrappers |
0.0250 |
0.75 |
Total cost |
|
|
$3.23 |
Table 2: Direct Labor
Job description |
Hours per unit |
Rate |
Total cost |
Processor |
0.30 |
$18.00 |
$5.40 |
Baker |
0.04 |
18.00 |
0.72 |
Packager |
0.02 |
18.00 |
0.36 |
|
|
|
|
Total cost |
|
|
$6.48 |
Table 3: YEARLY OVERHEAD COSTS
Cost description |
Amount |
Indirect material |
$14,400 |
Indirect labor |
72,000 |
Machine Maintenance |
19,200 |
Electricity |
6,380 |
|
21,600 |
Quality testing |
54,950 |
Total |
$188,530 |
Table 4 – Actual Overhead cost for the last six months
|
Machine hours |
OH Cost |
Month 1 |
320 |
$16,600 |
Month 2 |
200 |
$14,500 |
Month 3 |
420 |
$18,460 |
Month 4 |
500 |
$19,900 |
Month 5 |
220 |
$14,860 |
Month 6 |
210 |
$14,680 |
|
|
|
*200 cases produced per machine hour
Complete any calculations here:
Table 5: Variable and Fixed Costs
COSTS Description VARIABLE Cost per unit FIXED Cost per Year
|
|
|
|
|
|
|
|
|
|
|
|
TOTAL |
|
|
If a cost is mixed, put the fixed amount in the fixed column and the variable amount in the variable column.
CVP Calculations:

Trending now
This is a popular solution!
Step by step
Solved in 2 steps

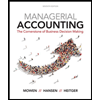
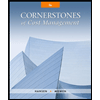
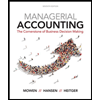
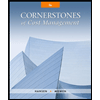
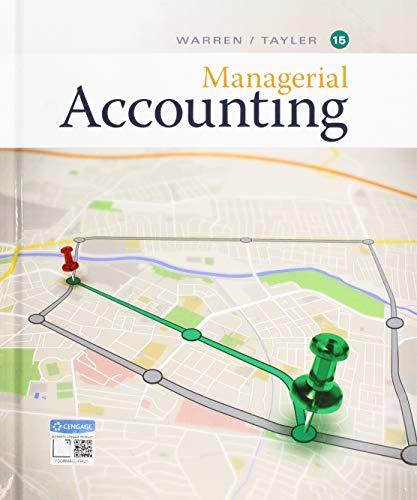