4. Analyse why is it more efficient for the work cells to prepare "modules" and deliver them to the assembly line than it would be to produce the component (e.g., interior upholstery) on the line. 5. Find an alternative process strategy to the assembly line that Wheeled Coach currently uses. Justify your proposal.
4. Analyse why is it more efficient for the work cells to prepare "modules" and deliver them to the assembly line than it would be to produce the component (e.g., interior upholstery) on the line. 5. Find an alternative process strategy to the assembly line that Wheeled Coach currently uses. Justify your proposal.
Practical Management Science
6th Edition
ISBN:9781337406659
Author:WINSTON, Wayne L.
Publisher:WINSTON, Wayne L.
Chapter2: Introduction To Spreadsheet Modeling
Section: Chapter Questions
Problem 20P: Julie James is opening a lemonade stand. She believes the fixed cost per week of running the stand...
Related questions
Question
EXPLAIN IN DETAILS AND PROVIDE REFERENCES IF POSSIBLE
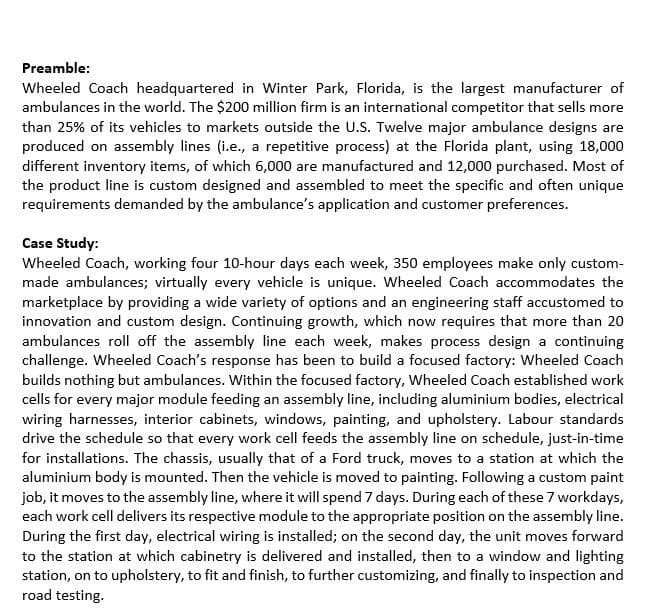
Transcribed Image Text:Preamble:
Wheeled Coach headquartered in Winter Park, Florida, is the largest manufacturer of
ambulances in the world. The $200 million firm is an international competitor that sells more
than 25% of its vehicles to markets outside the U.S. Twelve major ambulance designs are
produced on assembly lines (i.e., a repetitive process) at the Florida plant, using 18,000
different inventory items, of which 6,000 are manufactured and 12,000 purchased. Most of
the product line is custom designed and assembled to meet the specific and often unique
requirements demanded by the ambulance's application and customer preferences.
Case Study:
Wheeled Coach, working four 10-hour days each week, 350 employees make only custom-
made ambulances; virtually every vehicle is unique. Wheeled Coach accommodates the
marketplace by providing a wide variety of options and an engineering staff accustomed to
innovation and custom design. Continuing growth, which now requires that more than 20
ambulances roll off the assembly line each week, makes process design a continuing
challenge. Wheeled Coach's response has been to build a focused factory: Wheeled Coach
builds nothing but ambulances. Within the focused factory, Wheeled Coach established work
cells for every major module feeding an assembly line, including aluminium bodies, electrical
wiring harnesses, interior cabinets, windows, painting, and upholstery. Labour standards
drive the schedule so that every work cell feeds the assembly line on schedule, just-in-time
for installations. The chassis, usually that of a Ford truck, moves to a station at which the
aluminium body is mounted. Then the vehicle is moved to painting. Following a custom paint
job, it moves to the assembly line, where it will spend 7 days. During each of these 7 workdays,
each work cell delivers its respective module to the appropriate position on the assembly line.
During the first day, electrical wiring is installed; on the second day, the unit moves forward
to the station at which cabinetry is delivered and installed, then to a window and lighting
station, on to upholstery, to fit and finish, to further customizing, and finally to inspection and
road testing.
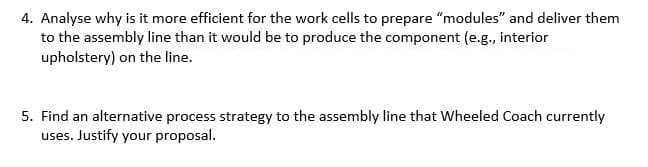
Transcribed Image Text:4. Analyse why is it more efficient for the work cells to prepare "modules" and deliver them
to the assembly line than it would be to produce the component (e.g., interior
upholstery) on the line.
5. Find an alternative process strategy to the assembly line that Wheeled Coach currently
uses. Justify your proposal.
Expert Solution

This question has been solved!
Explore an expertly crafted, step-by-step solution for a thorough understanding of key concepts.
This is a popular solution!
Trending now
This is a popular solution!
Step by step
Solved in 2 steps

Recommended textbooks for you
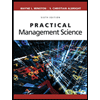
Practical Management Science
Operations Management
ISBN:
9781337406659
Author:
WINSTON, Wayne L.
Publisher:
Cengage,
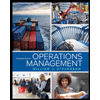
Operations Management
Operations Management
ISBN:
9781259667473
Author:
William J Stevenson
Publisher:
McGraw-Hill Education
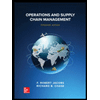
Operations and Supply Chain Management (Mcgraw-hi…
Operations Management
ISBN:
9781259666100
Author:
F. Robert Jacobs, Richard B Chase
Publisher:
McGraw-Hill Education
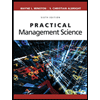
Practical Management Science
Operations Management
ISBN:
9781337406659
Author:
WINSTON, Wayne L.
Publisher:
Cengage,
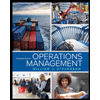
Operations Management
Operations Management
ISBN:
9781259667473
Author:
William J Stevenson
Publisher:
McGraw-Hill Education
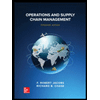
Operations and Supply Chain Management (Mcgraw-hi…
Operations Management
ISBN:
9781259666100
Author:
F. Robert Jacobs, Richard B Chase
Publisher:
McGraw-Hill Education
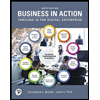
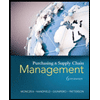
Purchasing and Supply Chain Management
Operations Management
ISBN:
9781285869681
Author:
Robert M. Monczka, Robert B. Handfield, Larry C. Giunipero, James L. Patterson
Publisher:
Cengage Learning
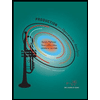
Production and Operations Analysis, Seventh Editi…
Operations Management
ISBN:
9781478623069
Author:
Steven Nahmias, Tava Lennon Olsen
Publisher:
Waveland Press, Inc.