A Dallas, TX-based manufacturer of small gasoline engines has developed monthly forecasts for a family of lawnmowers. Data for the 6-month period from January to June is presented in the table below. The firm would like to use an aggregate plan. MONTH Expected Demand Production Days Jan. 800 22 Feb. 700 18 Mar. 800 24 Apr. 1,200 25 May 1,600 26 June 1,900 26 One possible strategy for the manufacturer is to maintain a constant workforce throughout the 6-month period. The information below provides the cost information necessary for analyzing this alternative. Inventory carrying cost $3.00 Subcontracting cost per unit $15.00 Average pay rate $12.00 Daily pay rate = $96.00 Overtime pay rate $18.00 Labor-hours to produce a unit 2.2 Cost of increasing daily production rate (hiring and training) $200.00 Cost of decreasing daily production rate (layoffs) $350.00 The number of units produced per day = 45 and we have a constant workforce, no overtime or idle time, no safety stock, and no subcontractors. The firm accumulates inventory during the slack period of demand, January through March, and depletes it during the high-demand warm season, April through June. We have a beginning inventory = 0 and a planned inventory ending = 0. The cost of this approach over the 6 month period using the number of workers needed to produce 45 units per day is $ _______. We now allow subcontracting. To meet demand in March, the month of least demand, we can set the constant labor force at the rate that will meet the March demand and use subcontractors to fill the rest of the production demand. The total cost of using this approach is $ _______. We now want to vary the workforce size by hiring and laying off workers as necessary to meet the demand. The production rate will equal the demand. There is no change in production from the previous month, December. Remember that increasing production costs $200 per unit. The cost of decreasing production costs $350 per unit. The total cost of the varying workforce to meet the demand for the 6-month period is $ _______.
A Dallas, TX-based manufacturer of small gasoline engines has developed monthly
MONTH | Expected Demand | Production Days |
Jan. | 800 | 22 |
Feb. | 700 | 18 |
Mar. | 800 | 24 |
Apr. | 1,200 | 25 |
May | 1,600 | 26 |
June | 1,900 | 26 |
One possible strategy for the manufacturer is to maintain a constant workforce throughout the 6-month period. The information below provides the cost information necessary for analyzing this alternative.
Inventory carrying cost | $3.00 |
Subcontracting cost per unit | $15.00 |
Average pay rate | $12.00 |
Daily pay rate = | $96.00 |
Overtime pay rate | $18.00 |
Labor-hours to produce a unit | 2.2 |
Cost of increasing daily production rate (hiring and training) | $200.00 |
Cost of decreasing daily production rate (layoffs) | $350.00 |
The number of units produced per day = 45 and we have a constant workforce, no overtime or idle time, no safety stock, and no subcontractors. The firm accumulates inventory during the slack period of demand, January through March, and depletes it during the high-demand warm season, April through June. We have a beginning inventory = 0 and a planned inventory ending = 0. The cost of this approach over the 6 month period using the number of workers needed to produce 45 units per day is $ _______.
We now allow subcontracting. To meet demand in March, the month of least demand, we can set the constant labor force at the rate that will meet the March demand and use subcontractors to fill the rest of the production demand. The total cost of using this approach is $ _______.
We now want to vary the workforce size by hiring and laying off workers as necessary to meet the demand. The production rate will equal the demand. There is no change in production from the previous month, December. Remember that increasing production costs $200 per unit. The cost of decreasing production costs $350 per unit. The total cost of the varying workforce to meet the demand for the 6-month period is $ _______.

Trending now
This is a popular solution!
Step by step
Solved in 2 steps with 3 images

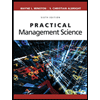
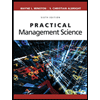