An aluminium alloy component, is machined on a lathe. The lathe has a mechanical efficiency of 91%. The lathe performs a turning operation on the workpiece which has a diameter of 150 mm and a length of 400 mm. The shear strength of the aluminium alloy work piece is 230 MPa and the tensile strength is 420 MPa. To machine the component, the lathe operator uses a cemented carbide tipped tool, having a rake angle of 6°. Furthermore, the relevant processing parameters are selected from the relevant data provided in a handbook by the lathe tool supplier. Some of the data is reproduced in Tables 1 and 2. Table 1. Surface Cutting Speeds (m/min) Part Material Aluminium Brass Cast Iron Mild Steel Alloy High Speed Steel 75 18 120 28 Tool Material Cemented 180 100 220 170 Carbide Table 2. Typical recommended feeds for turning (mm/rev) Part Material Aluminium Brass Cast Iron Mild Steel Alloy High Speed 0.2 0.15 0.2 0.15 Tool Steel Material Cemented 0.3 0.25 0.4 0.25 Carbide The operator applies a depth of cut of 2.30 mm and the chip thickness measured after the cut was found to be 0.64 mm. a) Using the data provided above, suggest appropriate values for the cutting speed and feed that need to be used by the operator to satisfactorily turn the aluminium workpiece. State any rationale/assumptions made. b) Using the orthogonal cutting model as an approximation of the turning process, determine: the cutting force, and the gross power required to operate the machine tool. i. i.
An aluminium alloy component, is machined on a lathe. The lathe has a mechanical efficiency of 91%. The lathe performs a turning operation on the workpiece which has a diameter of 150 mm and a length of 400 mm. The shear strength of the aluminium alloy work piece is 230 MPa and the tensile strength is 420 MPa. To machine the component, the lathe operator uses a cemented carbide tipped tool, having a rake angle of 6°. Furthermore, the relevant processing parameters are selected from the relevant data provided in a handbook by the lathe tool supplier. Some of the data is reproduced in Tables 1 and 2. Table 1. Surface Cutting Speeds (m/min) Part Material Aluminium Brass Cast Iron Mild Steel Alloy High Speed Steel 75 18 120 28 Tool Material Cemented 180 100 220 170 Carbide Table 2. Typical recommended feeds for turning (mm/rev) Part Material Aluminium Brass Cast Iron Mild Steel Alloy High Speed 0.2 0.15 0.2 0.15 Tool Steel Material Cemented 0.3 0.25 0.4 0.25 Carbide The operator applies a depth of cut of 2.30 mm and the chip thickness measured after the cut was found to be 0.64 mm. a) Using the data provided above, suggest appropriate values for the cutting speed and feed that need to be used by the operator to satisfactorily turn the aluminium workpiece. State any rationale/assumptions made. b) Using the orthogonal cutting model as an approximation of the turning process, determine: the cutting force, and the gross power required to operate the machine tool. i. i.
Elements Of Electromagnetics
7th Edition
ISBN:9780190698614
Author:Sadiku, Matthew N. O.
Publisher:Sadiku, Matthew N. O.
ChapterMA: Math Assessment
Section: Chapter Questions
Problem 1.1MA
Related questions
Question
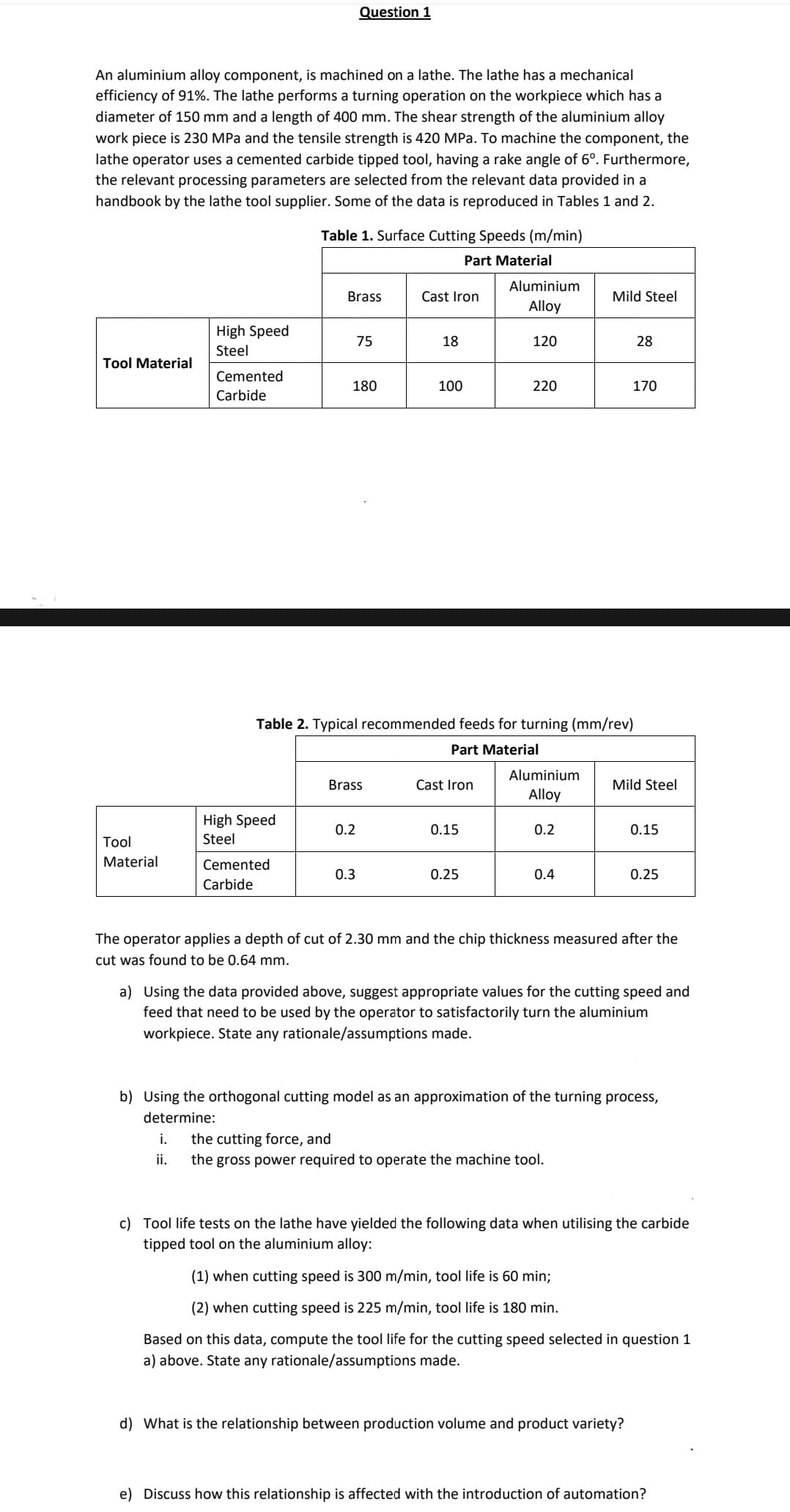
Transcribed Image Text:Question 1
An aluminium alloy component, is machined on a lathe. The lathe has a mechanical
efficiency of 91%. The lathe performs a turning operation on the workpiece which has a
diameter of 150 mm and a length of 400 mm. The shear strength of the aluminium alloy
work piece is 230 MPa and the tensile strength is 420 MPa. To machine the component, the
lathe operator uses a cemented carbide tipped tool, having a rake angle of 6°. Furthermore,
the relevant processing parameters are selected from the relevant data provided in a
handbook by the lathe tool supplier. Some of the data is reproduced in Tables 1 and 2.
Table 1. Surface Cutting Speeds (m/min)
Part Material
Aluminium
Brass
Cast Iron
Mild Steel
Alloy
High Speed
75
18
120
28
Steel
Tool Material
Cemented
180
100
220
170
Carbide
Table 2. Typical recommended feeds for turning (mm/rev)
Part Material
Aluminium
Brass
Cast Iron
Mild Steel
Alloy
High Speed
0.2
0.15
0.2
0.15
Тool
Steel
Material
Cemented
0.3
0.25
0.4
0.25
Carbide
The operator applies a depth of cut of 2.30 mm and the chip thickness measured after the
cut was found to be 0.64 mm.
a) Using the data provided above, suggest appropriate values for the cutting speed and
feed that need to be used by the operator to satisfactorily turn the aluminium
workpiece. State any rationale/assumptions made.
b) Using the orthogonal cutting model as an approximation of the turning process,
determine:
the cutting force, and
the gross power required to operate the machine tool.
i.
ii.
c) Tool life tests on the lathe have yielded the following data when utilising the carbide
tipped tool on the aluminium alloy:
(1) when cutting speed is 300 m/min, tool life is 60 min;
(2) when cutting speed is 225 m/min, tool life is 180 min.
Based on this data, compute the tool life for the cutting speed selected in question 1
a) above. State any rationale/assumptions made.
d) What is the relationship between production volume and product variety?
e) Discuss how this relationship is affected with the introduction of automation?
Expert Solution

This question has been solved!
Explore an expertly crafted, step-by-step solution for a thorough understanding of key concepts.
This is a popular solution!
Trending now
This is a popular solution!
Step by step
Solved in 2 steps

Recommended textbooks for you
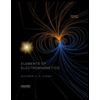
Elements Of Electromagnetics
Mechanical Engineering
ISBN:
9780190698614
Author:
Sadiku, Matthew N. O.
Publisher:
Oxford University Press
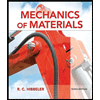
Mechanics of Materials (10th Edition)
Mechanical Engineering
ISBN:
9780134319650
Author:
Russell C. Hibbeler
Publisher:
PEARSON
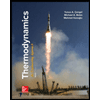
Thermodynamics: An Engineering Approach
Mechanical Engineering
ISBN:
9781259822674
Author:
Yunus A. Cengel Dr., Michael A. Boles
Publisher:
McGraw-Hill Education
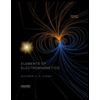
Elements Of Electromagnetics
Mechanical Engineering
ISBN:
9780190698614
Author:
Sadiku, Matthew N. O.
Publisher:
Oxford University Press
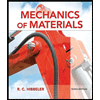
Mechanics of Materials (10th Edition)
Mechanical Engineering
ISBN:
9780134319650
Author:
Russell C. Hibbeler
Publisher:
PEARSON
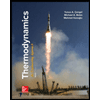
Thermodynamics: An Engineering Approach
Mechanical Engineering
ISBN:
9781259822674
Author:
Yunus A. Cengel Dr., Michael A. Boles
Publisher:
McGraw-Hill Education
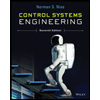
Control Systems Engineering
Mechanical Engineering
ISBN:
9781118170519
Author:
Norman S. Nise
Publisher:
WILEY
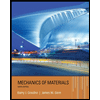
Mechanics of Materials (MindTap Course List)
Mechanical Engineering
ISBN:
9781337093347
Author:
Barry J. Goodno, James M. Gere
Publisher:
Cengage Learning
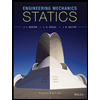
Engineering Mechanics: Statics
Mechanical Engineering
ISBN:
9781118807330
Author:
James L. Meriam, L. G. Kraige, J. N. Bolton
Publisher:
WILEY