Helsinki Inc. produces premium bottled water. Helsinki purchases artesian water, stores the water in large tanks, and then runs the water through two processes: Filtration, where workers microfilter and ozonate the water Bottling, where workers bottle and package the filtered water During December, the filtration process incurs the following costs in processing 200,000 liters: Wages of workers operating the filtration equipment $11,100 Wages of workers operating ozonation equipment $12,850 Manufacturing overhead allocated to filtration $24,050 Water $120,000 Question: Compute the December conversion costs in the Filtration Department. If the Filtration Department completely processed 200,000 liters, what would be the average filtration cost per liter? Now, assume that the total costs of the filtration process listed in the previous chart yield 160,000 liters that are completely filtered and ozonated, while the remaining 40,000 liters are only partway through the process at the end of December. Is the cost per completely filtered and ozonated liter higher, lower, or the same as in question 2? Why?
Master Budget
A master budget can be defined as an estimation of the revenue earned or expenses incurred over a specified period of time in the future and it is generally prepared on a periodic basis which can be either monthly, quarterly, half-yearly, or annually. It helps a business, an organization, or even an individual to manage the money effectively. A budget also helps in monitoring the performance of the people in the organization and helps in better decision-making.
Sales Budget and Selling
A budget is a financial plan designed by an undertaking for a definite period in future which acts as a major contributor towards enhancing the financial success of the business undertaking. The budget generally takes into account both current and future income and expenses.
Helsinki Inc. produces premium bottled water. Helsinki purchases artesian water, stores the water in large tanks, and then runs the water through two processes:
- Filtration, where workers microfilter and ozonate the water
- Bottling, where workers bottle and package the filtered water
During December, the filtration process incurs the following costs in processing 200,000 liters:
Wages of workers operating the filtration equipment $11,100
Wages of workers operating ozonation equipment $12,850
Manufacturing overhead allocated to filtration $24,050
Water $120,000
Question:
- Compute the December conversion costs in the Filtration Department.
- If the Filtration Department completely processed 200,000 liters, what would be the average filtration cost per liter?
- Now, assume that the total costs of the filtration process listed in the previous chart yield 160,000 liters that are completely filtered and ozonated, while the remaining 40,000 liters are only partway through the process at the end of December. Is the cost per completely filtered and ozonated liter higher, lower, or the same as in question 2? Why?
At Helsinki, water is added at the beginning of the filtration process. Conversion costs are incurred evenly throughout the process, and in December, 160,000 liters have been completed and transferred out of the Filtration Department to the Bottling Department.
The 40,000 liters remaining in the Filtration Department's ending work in process inventory are 80% of the way through the filtration process. Assume no beginning inventories.
4.Complete the first two steps of the
5.Complete Steps 3 and 4 of the process costing procedure: Summarize total costs to account for and then compute the cost per equivalent unit for both direct materials and conversion costs.
6.Prepare a schedule to complete step 5 of the process costing procedure to show the cost of the 160,000 liters completed and transferred out of the Filtration Department.
7.Use the same schedule above to show the cost of 40,000 liters remaining in the Filtration Department's ending work in process inventory.
We now consider Helsinki's second process-Bottling. In the Bottling Department, workers bottle the filtered water and pack the bottles into boxes. Conversion costs are incurred evenly throughout the Bottling process, but packaging materials are not added until the end of the process.
December data from the Bottling Department is given below:
Beginning work in process inventory (40% of the way through the process) 8,000 liters
Transferred in from Filtration 160,000 liters
Completed and transfer red out to Finished Goods Inventory in
December 154,000 liters
Ending work in process inventory (65% of the way through the bottling
process) 22,000 liters
The Filtration Department completed and transferred out 160,000 liters at a total cost of $136,000.
Costs in beginning work in process inventory Costs added during December
Transferred in $1,760 Transferred in $136,000
Direct materials $0 Direct materials $30,800
Direct labor $600 Direct labor $33, 726
Mfg overhead $520 Mfg overhead $25,742
Total beginning WIP on Dec 1 $2880 Total costs added in Dec $226,268
8.Complete the first two steps of the process costing procedure for the Bottling Department: summarize the physical flow of units and then compute the equivalent units of direct materials and conversion costs.
9.Complete Steps 3 and 4 of the process costing procedure: Summarize total costs to account for and then compute the cost per equivalent unit for both direct materials and conversion costs.
10.Complete Step 5 of the process costing procedure: Assign costs to units completed and to units in ending inventory.
11.What is the ending WIP balance on December 31?

Trending now
This is a popular solution!
Step by step
Solved in 5 steps

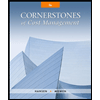
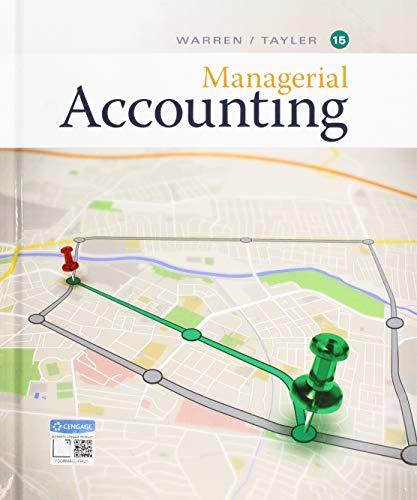
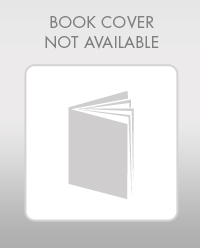
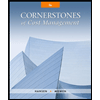
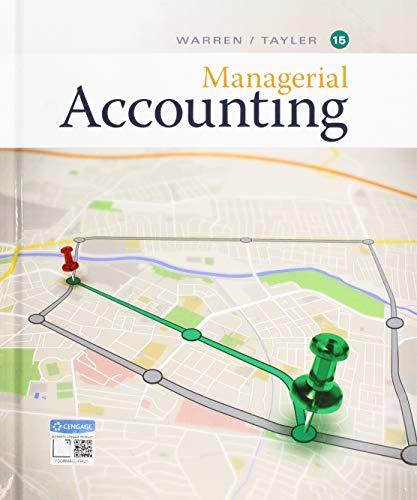
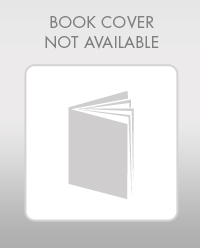
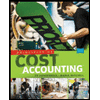
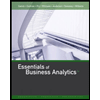
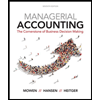