How did the direct labor & direct materials amounts change for the milling and assembly departments? Did I miss that? I was following along with how to calculate total manufacturing overhead for each department, but I don’t know how the direct materials and direct labor amounts were calculated
How did the direct labor & direct materials amounts change for the milling and assembly departments? Did I miss that? I was following along with how to calculate total manufacturing overhead for each department, but I don’t know how the direct materials and direct labor amounts were calculated
Chapter5: Process Costing
Section: Chapter Questions
Problem 2PB: The following product costs are available for Kellee Company on the production of eyeglass frames:...
Related questions
Question
How did the direct labor & direct materials amounts change for the milling and assembly departments? Did I miss that? I was following along with how to calculate total manufacturing overhead for each department, but I don’t know how the direct materials and direct labor amounts were calculated. 
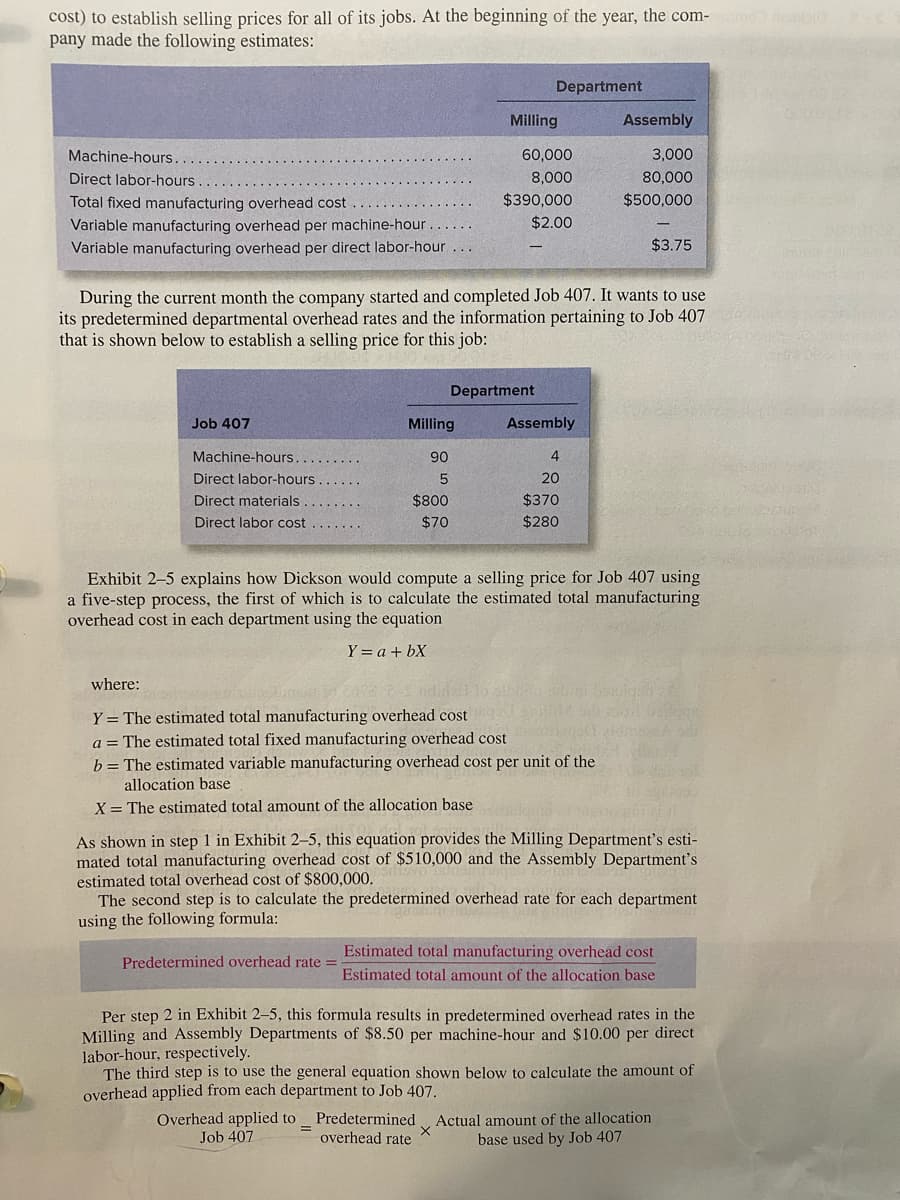
Transcribed Image Text:cost) to establish selling prices for all of its jobs. At the beginning of the year, the com- noatg
pany made the following estimates:
Department
Milling
Assembly
Machine-hours.
60,000
3,000
Direct labor-hours
8,000
80,000
Total fixed manufacturing overhead cost
$390,000
$500,000
Variable manufacturing overhead per machine-hour
$2.00
Variable manufacturing overhead per direct labor-hour
$3.75
During the current month the company started and completed Job 407. It wants to use
its predetermined departmental overhead rates and the information pertaining to Job 407
that is shown below to establish a selling price for this job:
Department
Job 407
Milling
Assembly
Machine-hours
90
Direct labor-hours
20
Direct materials
$800
$370
Direct labor cost
$70
$280
Exhibit 2-5 explains how Dickson would compute a selling price for Job 407 using
a five-step process, the first of which is to calculate the estimated total manufacturing
overhead cost in each department using the equation
Y = a + bX
where:
Y = The estimated total manufacturing overhead cost
a = The estimated total fixed manufacturing overhead cost
b = The estimated variable manufacturing overhead cost per unit of the
allocation base
X = The estimated total amount of the allocation base
As shown in step 1 in Exhibit 2–5, this equation provides the Milling Department's esti-
mated total manufacturing overhead cost of $510,000 and the Assembly Department's
estimated total overhead cost of $800,000.
The second step is to calculate the predetermined overhead rate for each department
using the following formula:
Estimated total manufacturing overhead cost
Predetermined overhead rate =
Estimated total amount of the allocation base
Per step 2 in Exhibit 2-5, this formula results in predetermined overhead rates in the
Milling and Assembly Departments of $8.50 per machine-hour and $10.00 per direct
labor-hour, respectively.
The third step is to use the general equation shown below to calculate the amount of
overhead applied from each department to Job 407.
Overhead applied to Predetermined Actual amount of the allocation
overhead rate
Job 407
base used by Job 407
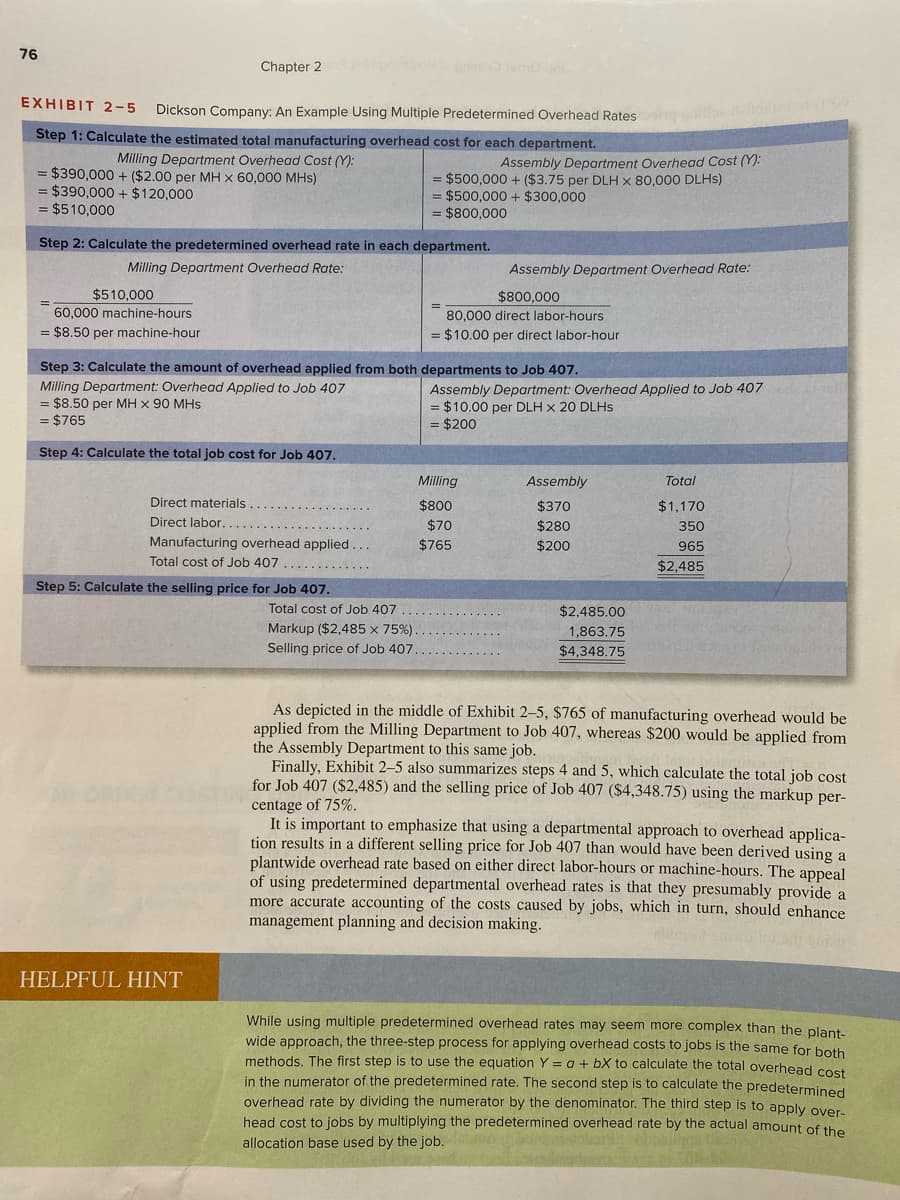
Transcribed Image Text:76
Chapter 2
EXHIBIT 2-5
Dickson Company: An Example Using Multiple Predetermined Overhead Rates
Step 1: Calculate the estimated total manufacturing overhead cost for each department.
Milling Department Overhead Cost (Y):
Assembly Department Overhead Cost (Y):
= $390,000 + ($2.00 per MH x 60,000 MHs)
= $390,000 + $120,000
= $510,000
= $500,000 + ($3.75 per DLH x 80,000 DLHS)
= $500,000 + $300,000
$800,000
Step 2: Calculate the predetermined overhead rate in each department.
Milling Department Overhead Rate:
Assembly Department Overhead Rate:
$510,000
$800,000
%3D
60,000 machine-hours
80,000 direct labor-hours
= $8.50 per machine-hour
= $10.00 per direct labor-hour
Step 3: Calculate the amount of overhead applied from both departments to Job 407.
Milling Department: Overhead Applied to Job 407
= $8.50 per MH x 90 MHs
Assembly Department: Overhead Applied to Job 407
= $10.00 per DLH x 20 DLHS
= $200
= $765
Step 4: Calculate the total job cost for Job 407.
Milling
Assembly
Total
Direct materials
$800
$370
$1,170
Direct labor..
$70
$280
350
Manufacturing overhead applied ..
$765
$200
965
Total cost of Job 407
$2,485
Step 5: Calculate the selling price for Job 407.
Total cost of Job 407
$2,485.00
Markup ($2,485 x 75%).
1,863.75
Selling price of Job 407
$4,348.75
As depicted in the middle of Exhibit 2-5, $765 of manufacturing overhead would be
applied from the Milling Department to Job 407, whereas $200 would be applied from
the Assembly Department to this same job.
Finally, Exhibit 2-5 also summarizes steps 4 and 5, which calculate the total job cost
for Job 407 ($2,485) and the selling price of Job 407 ($4,348.75) using the markup per-
centage of 75%.
It is important to emphasize that using a departmental approach to overhead applica-
tion results in a different selling price for Job 407 than would have been derived using a
plantwide overhead rate based on either direct labor-hours or machine-hours. The appeal
of using predetermined departmental overhead rates is that they presumably provide a
more accurate accounting of the costs caused by jobs, which in turn, should enhance
management planning and decision making.
HELPFUL HINT
While using multiple predetermined overhead rates may seem more complex than the plant-
wide approach, the three-step process for applying overhead costs to jobs is the same for both
methods. The first step is to use the equation Y = a + bX to calculate the total overhead cost
in the numerator of the predetermined rate. The second step is to calculate the predetermined
overhead rate by dividing the numerator by the denominator. The third step is to apply over
head cost to jobs by multiplying the predetermined overhead rate by the actual amount of the
allocation base used by the job.
Expert Solution

This question has been solved!
Explore an expertly crafted, step-by-step solution for a thorough understanding of key concepts.
Step by step
Solved in 2 steps

Knowledge Booster
Learn more about
Need a deep-dive on the concept behind this application? Look no further. Learn more about this topic, accounting and related others by exploring similar questions and additional content below.Recommended textbooks for you
Principles of Accounting Volume 2
Accounting
ISBN:
9781947172609
Author:
OpenStax
Publisher:
OpenStax College
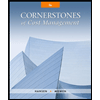
Cornerstones of Cost Management (Cornerstones Ser…
Accounting
ISBN:
9781305970663
Author:
Don R. Hansen, Maryanne M. Mowen
Publisher:
Cengage Learning
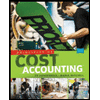
Principles of Cost Accounting
Accounting
ISBN:
9781305087408
Author:
Edward J. Vanderbeck, Maria R. Mitchell
Publisher:
Cengage Learning
Principles of Accounting Volume 2
Accounting
ISBN:
9781947172609
Author:
OpenStax
Publisher:
OpenStax College
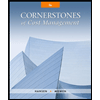
Cornerstones of Cost Management (Cornerstones Ser…
Accounting
ISBN:
9781305970663
Author:
Don R. Hansen, Maryanne M. Mowen
Publisher:
Cengage Learning
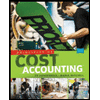
Principles of Cost Accounting
Accounting
ISBN:
9781305087408
Author:
Edward J. Vanderbeck, Maria R. Mitchell
Publisher:
Cengage Learning
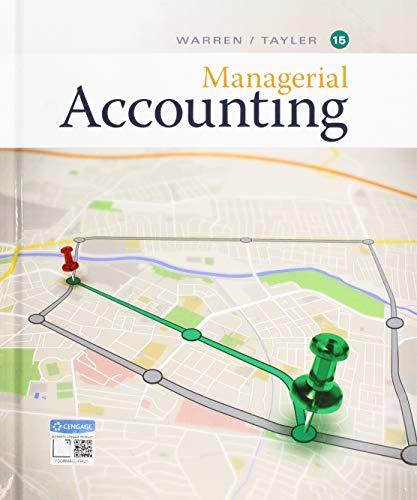
Managerial Accounting
Accounting
ISBN:
9781337912020
Author:
Carl Warren, Ph.d. Cma William B. Tayler
Publisher:
South-Western College Pub
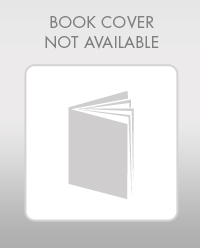
Financial And Managerial Accounting
Accounting
ISBN:
9781337902663
Author:
WARREN, Carl S.
Publisher:
Cengage Learning,
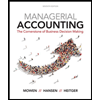
Managerial Accounting: The Cornerstone of Busines…
Accounting
ISBN:
9781337115773
Author:
Maryanne M. Mowen, Don R. Hansen, Dan L. Heitger
Publisher:
Cengage Learning