In this section, I will explain the causes of the difficulties which I have explained above. The reason for the missing cages uses to be that the cage is still being picked or not and if the picker is still using the cage to pick the items then request the picker to drop the cage off to the packing department so that the items can be packed and sent out the shipping department for the delivery. Also, if the cage is not in the picking department buffer or pack buffer and is not being picked then as a process guide it was my duty to search for the cage at the packing stations first, and if not found then to escalate to the management so that relevant department can be contacted for the action. During the critical pool time, there were a few shipments IDs use to get sent down from the picking department which they couldn’t send into the picker’s scanners as either the batch assigned for the item by the stowing department would be wrong or they are very heavy items which require team lifting due to which the shipments use to get sent down to the problem solver. Other causes for the hot pick used to be if any items are missing from the priority cage or if the item has been damaged while packing then the shipment used to get sent down to the problem solver by the pack process guide or by the team leader. During peak time and prime time, the number of hot pick used to be very high and to get them picked and pack on time, I potentially had to request the 2- 3 hot pickers to pick the items and bring them down to the problem solver desk. It used to get very hectic sometimes and if there are many items to pack then I use to request the team lead to send packers down to problem-solving department who could help with the packing so that all the items are sent down to the shipping within the timeframe. It used to be busier during the prime and peak time because the amount of product orders will be more than usual due to discounts and sales. Hence there will be more mistake expected than off-peak time. Also, the missing items from the cage used to be either the picker has scanned the item and forgot to put it in the cage, or the item is fallen out of the cage while tugging from one buffer to another and all these items use to get hot picked to ensure customer satisfaction is met. Damaged items- Damaged items use to be placed into the damaged totes however sometimes the items used to be missing from the damaged cage and the reason for that used to be that sometimes the pickers used to scan the item from the location and mark it as damaged and use to leave the item back on the location rather than putting into the damage tote. As a problem solver, if I was unable to locate those items in the damaged cage then I use to provide the hot picker with the location number and the item barcode and request them to go to the location and look for those items. If the hot picker is not able to find the item at the location, I had to escalate this further with the PPQA department and then they would investigate this matter further. Even from the packing department as well sometimes the packers use to mark the items as damaged however they use to keep the items in the stations rather than putting the item straight into the damaged cage which used to make the damage tote number goes high virtually but not physically. Refer to the theories for the difficulties and recommendations for the above task and skills: 1)Organizational culture 2)Barker’s notion of control through team-work 3)Theories of empowerment
Theories and concepts: Cause of the difficulties
In this section, I will explain the causes of the difficulties which I have explained above. The reason for the missing cages uses to be that the cage is still being picked or not and if the picker is still using the cage to pick the items then request the picker to drop the cage off to the packing department so that the items can be packed and sent out the shipping department for the delivery. Also, if the cage is not in the picking department buffer or pack buffer and is not being picked then as a process guide it was my duty to search for the cage at the packing stations first, and if not found then to escalate to the management so that relevant department can be contacted for the action.
During the critical pool time, there were a few shipments IDs use to get sent down from the picking department which they couldn’t send into the picker’s scanners as either the batch assigned for the item by the stowing department would be wrong or they are very heavy items which require team lifting due to which the shipments use to get sent down to the problem solver. Other causes for the hot pick used to be if any items are missing from the priority cage or if the item has been damaged while packing then the shipment used to get sent down to the problem solver by the pack process guide or by the team leader. During peak time and prime time, the number of hot pick used to be very high and to get them picked and pack on time, I potentially had to request the 2- 3 hot pickers to pick the items and bring them down to the problem solver desk. It used to get very hectic sometimes and if there are many items to pack then I use to request the team lead to send packers down to problem-solving department who could help with the packing so that all the items are sent down to the shipping within the timeframe. It used to be busier during the prime and peak time because the amount of product orders will be more than usual due to discounts and sales. Hence there will be more mistake expected than off-peak time. Also, the missing items from the cage used to be either the picker has scanned the item and forgot to put it in the cage, or the item is fallen out of the cage while tugging from one buffer to another and all these items use to get hot picked to ensure customer satisfaction is met.
Damaged items- Damaged items use to be placed into the damaged totes however sometimes the items used to be missing from the damaged cage and the reason for that used to be that sometimes the pickers used to scan the item from the location and mark it as damaged and use to leave the item back on the location rather than putting into the damage tote. As a problem solver, if I was unable to locate those items in the damaged cage then I use to provide the hot picker with the location number and the item barcode and request them to go to the location and look for those items. If the hot picker is not able to find the item at the location, I had to escalate this further with the PPQA department and then they would investigate this matter further. Even from the packing department as well sometimes the packers use to mark the items as damaged however they use to keep the items in the stations rather than putting the item straight into the damaged cage which used to make the damage tote number goes high virtually but not physically.
Refer to the theories for the difficulties and recommendations for the above task and skills:
1)Organizational culture
2)Barker’s notion of control through team-work
3)Theories of empowerment

Step by step
Solved in 3 steps

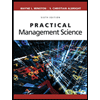
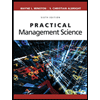