Kitchen Helper Company decides to produce and sell food blenders and is considering three different types of production facilities ("plants"). Plant A is a labor-intensive facility, employing relatively little specialized capital equipment. Plant B is a semi-automated facility that would employ less labor than A but would also have higher capital equipment costs. Plant Cis a completely automated facility using much more high-cost, high-technology capital equipment and even less labor than B. Information about the operating costs and production capacities of these three different types of plants is shown in the following table. Unit variable costs Material $3.50 $3.25 $3.00 Labor $4.50 $3.25 $2.00 Overhead $1.00 $1.50 $2.00 Total $9.00 $8.00 $7.00 Annual fixed costs Depreciation $60,000 $100,000 $200,000 Capital $30,000 $50,000 $100,000 Overhead $60,000 $100,000 $150,000 Total $150,000 $250,000 $450,000 Annual capacity 75,000 150,000 350,000
Kitchen Helper Company decides to produce and sell food blenders and is considering three different types of production facilities ("plants"). Plant A is a labor-intensive facility, employing relatively little specialized capital equipment. Plant B is a semi-automated facility that would employ less labor than A but would also have higher capital equipment costs. Plant Cis a completely automated facility using much more high-cost, high-technology capital equipment and even less labor than B. Information about the operating costs and production capacities of these three different types of plants is shown in the following table. Unit variable costs Material $3.50 $3.25 $3.00 Labor $4.50 $3.25 $2.00 Overhead $1.00 $1.50 $2.00 Total $9.00 $8.00 $7.00 Annual fixed costs Depreciation $60,000 $100,000 $200,000 Capital $30,000 $50,000 $100,000 Overhead $60,000 $100,000 $150,000 Total $150,000 $250,000 $450,000 Annual capacity 75,000 150,000 350,000
Cornerstones of Cost Management (Cornerstones Series)
4th Edition
ISBN:9781305970663
Author:Don R. Hansen, Maryanne M. Mowen
Publisher:Don R. Hansen, Maryanne M. Mowen
Chapter17: Activity Resource Usage Model And Tactical Decision Making
Section: Chapter Questions
Problem 18E: A company is considering a special order for 1,000 units to be priced at 8.90 (the normal price...
Related questions
Question

Transcribed Image Text:Determine the average total cost schedules for each plant type to fill first three empty columns of the following table. (Hint: For output levels beyond
the capacity of a given plant, assume that multiple plants of the same type are built. For example, to produce 200,000 units with Plant A, three of
these plants would be built.)
Note: If necessary, round to two decimal places.
Short-Run Average Total Cost (SRATC)
Long-Run Average Total Cost (LRATC)
Output (Q)
(Dollars)
(Dollars)
(Dollars)
(Dollars)
A
50,000
100,000
150,000
200,000
250,000
300,000
350,000
Based on the cost schedules calculated, construct the long-run average total cost schedule for the production of blenders and fill the final column of
the preceding table.

Transcribed Image Text:Kitchen Helper Company decides to produce and sell food blenders and is considering three different types of production facilities ("plants"). Plant A is
a labor-intensive facility, employing relatively little specialized capital equipment. Plant B is a semi-automated facility that would employ less labor
than A but would also have higher capital equipment costs. Plant C is a completely automated facility using much more high-cost, high-technology
capital equipment and even less labor than B. Information about the operating costs and production capacities of these three different types of plants
is shown in the following table.
B
Unit variable costs
Material
$3.50
$3.25
$3,00
Labor
$4.50
$3.25
$2.00
Overhead
$1.00
$1.50
$2.00
Total
$9.00
$8.00
$7.00
Annual fixed costs
Depreciation
$60,000
$100,000
$200,000
Capital
$30,000
$50,000
$100,000
Overhead
$60,000
$100,000
$150,000
Total
$150,000
$250,000
$450,000
Annual capacity
75,000
150,000
350,000
Expert Solution

This question has been solved!
Explore an expertly crafted, step-by-step solution for a thorough understanding of key concepts.
This is a popular solution!
Trending now
This is a popular solution!
Step by step
Solved in 5 steps with 4 images

Knowledge Booster
Learn more about
Need a deep-dive on the concept behind this application? Look no further. Learn more about this topic, accounting and related others by exploring similar questions and additional content below.Recommended textbooks for you
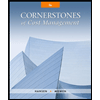
Cornerstones of Cost Management (Cornerstones Ser…
Accounting
ISBN:
9781305970663
Author:
Don R. Hansen, Maryanne M. Mowen
Publisher:
Cengage Learning
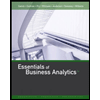
Essentials of Business Analytics (MindTap Course …
Statistics
ISBN:
9781305627734
Author:
Jeffrey D. Camm, James J. Cochran, Michael J. Fry, Jeffrey W. Ohlmann, David R. Anderson
Publisher:
Cengage Learning
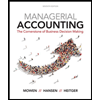
Managerial Accounting: The Cornerstone of Busines…
Accounting
ISBN:
9781337115773
Author:
Maryanne M. Mowen, Don R. Hansen, Dan L. Heitger
Publisher:
Cengage Learning
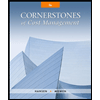
Cornerstones of Cost Management (Cornerstones Ser…
Accounting
ISBN:
9781305970663
Author:
Don R. Hansen, Maryanne M. Mowen
Publisher:
Cengage Learning
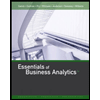
Essentials of Business Analytics (MindTap Course …
Statistics
ISBN:
9781305627734
Author:
Jeffrey D. Camm, James J. Cochran, Michael J. Fry, Jeffrey W. Ohlmann, David R. Anderson
Publisher:
Cengage Learning
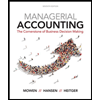
Managerial Accounting: The Cornerstone of Busines…
Accounting
ISBN:
9781337115773
Author:
Maryanne M. Mowen, Don R. Hansen, Dan L. Heitger
Publisher:
Cengage Learning