Let us consider each of these differences. 1. Often, by its nature, service involves a much higher degree of customer contact than manufacturing. The performance of a service often occurs at the point of consumption. For example, repairing a leaky roof must take place where the roof is, and surgery re- quires the presence of the surgeon and the patient. On the other hand, manufacturing al- lows a separation between production and consumption, so that manufacturing may occur. away from the consumer. This permits a fair degree of latitude in selecting work methods, assigning jobs, scheduling work, and exercising control over operations. Service opera- tions, because of their contact with customers, can be much more limited in their range of options. Moreover, customers are sometimes a part of the system (e.g., self-service oper- ations such as gas stations, shopping), so tight control is impossible. In addition, product- oriented operations can build up inventories of finished goods (e.g., cars, refrigerators), CHAPTER ONE INTRODUCTION TO OPERATIONS MANAGEMENT enabling them to absorb some of the shocks caused by varying demand. Service opera- tions, however, cannot build up inventories of time and are much more sensitive to de- mand variability banks and supermarkets alternate between lines of customers waiting for service and idle tellers or cashiers waiting for customers. 2. Service operations are subject to greater variability of inputs than typical manufac- turing operations. Each patient, each lawn, and each auto repair presents a specific prob- lem that often must be diagnosed before it can be remedied. Manufacturing operations often have the ability to carefully control the amount of variability of inputs and thus achieve low variability in outputs. Consequently, job requirements for manufacturing are generally more uniform than those for services. 3. Services often require a higher labor content whereas manufacturing, with excep- tions, can be more capital-intensive (i.e., mechanized). 4. Because high mechanization generates products with low variability, manufactur- ing tends to be smooth and efficient; service activities sometimes appear to be slow and awkward, and output is more variable. Automated services are an exception to this. 5. Measurement of productivity is more straightforward in manufacturing due to the high degree of uniformity of most manufactured items. In service operations, variations in demand intensity and in requirements from job to job make productivity measurement considerably more difficult. For example, compare the productivity of two doctors. One may have a large number of routine cases while the other does not, so their productivity appears to differ unless a very careful analysis is made. 6. In many instances customers receive the service as it is performed (e.g., haircut, dental care). 7. Quality assurance is more challenging in services when production and consump- tion occur at the same time. Moreover, the higher variability of input creates additional opportunity for the quality f output to suffer unless quality assurance is actively man- aged. Quality at the point of creation is typically more evident for services than for man- ufacturing, where errors Ca, le corrected before the customer receives the output. Service jobs are sometimes categorized as professional or nonprofessional. Whole- sale/retail and personal services generally fall into the nonprofessional category. Often these jobs tend to be on the low end of the pay scale, whereas professional services (e.g., surgery, consulting) tend to be on the high end of the pay scale. Manufacturing jobs, on the other hand, don't show this bimodal tendency, and few salaries fall in either the high or low range. Table 1-5 gives an overview of the differences between production of goods and ser- vice operations. Although it is convenient to think in terms of systems devoted exclusively to goods or services, most real systems are a blend of both. For instance, maintenance and repair of equipment services performed by virtually every manufacturing firm. Similarly, most service organizations typically sell goods that complement their services. Thus, a lawn care firm usually sells goods such as weed killers, fertilizers, and grass seed. Hospitals
Let us consider each of these differences. 1. Often, by its nature, service involves a much higher degree of customer contact than manufacturing. The performance of a service often occurs at the point of consumption. For example, repairing a leaky roof must take place where the roof is, and surgery re- quires the presence of the surgeon and the patient. On the other hand, manufacturing al- lows a separation between production and consumption, so that manufacturing may occur. away from the consumer. This permits a fair degree of latitude in selecting work methods, assigning jobs, scheduling work, and exercising control over operations. Service opera- tions, because of their contact with customers, can be much more limited in their range of options. Moreover, customers are sometimes a part of the system (e.g., self-service oper- ations such as gas stations, shopping), so tight control is impossible. In addition, product- oriented operations can build up inventories of finished goods (e.g., cars, refrigerators), CHAPTER ONE INTRODUCTION TO OPERATIONS MANAGEMENT enabling them to absorb some of the shocks caused by varying demand. Service opera- tions, however, cannot build up inventories of time and are much more sensitive to de- mand variability banks and supermarkets alternate between lines of customers waiting for service and idle tellers or cashiers waiting for customers. 2. Service operations are subject to greater variability of inputs than typical manufac- turing operations. Each patient, each lawn, and each auto repair presents a specific prob- lem that often must be diagnosed before it can be remedied. Manufacturing operations often have the ability to carefully control the amount of variability of inputs and thus achieve low variability in outputs. Consequently, job requirements for manufacturing are generally more uniform than those for services. 3. Services often require a higher labor content whereas manufacturing, with excep- tions, can be more capital-intensive (i.e., mechanized). 4. Because high mechanization generates products with low variability, manufactur- ing tends to be smooth and efficient; service activities sometimes appear to be slow and awkward, and output is more variable. Automated services are an exception to this. 5. Measurement of productivity is more straightforward in manufacturing due to the high degree of uniformity of most manufactured items. In service operations, variations in demand intensity and in requirements from job to job make productivity measurement considerably more difficult. For example, compare the productivity of two doctors. One may have a large number of routine cases while the other does not, so their productivity appears to differ unless a very careful analysis is made. 6. In many instances customers receive the service as it is performed (e.g., haircut, dental care). 7. Quality assurance is more challenging in services when production and consump- tion occur at the same time. Moreover, the higher variability of input creates additional opportunity for the quality f output to suffer unless quality assurance is actively man- aged. Quality at the point of creation is typically more evident for services than for man- ufacturing, where errors Ca, le corrected before the customer receives the output. Service jobs are sometimes categorized as professional or nonprofessional. Whole- sale/retail and personal services generally fall into the nonprofessional category. Often these jobs tend to be on the low end of the pay scale, whereas professional services (e.g., surgery, consulting) tend to be on the high end of the pay scale. Manufacturing jobs, on the other hand, don't show this bimodal tendency, and few salaries fall in either the high or low range. Table 1-5 gives an overview of the differences between production of goods and ser- vice operations. Although it is convenient to think in terms of systems devoted exclusively to goods or services, most real systems are a blend of both. For instance, maintenance and repair of equipment services performed by virtually every manufacturing firm. Similarly, most service organizations typically sell goods that complement their services. Thus, a lawn care firm usually sells goods such as weed killers, fertilizers, and grass seed. Hospitals
Practical Management Science
6th Edition
ISBN:9781337406659
Author:WINSTON, Wayne L.
Publisher:WINSTON, Wayne L.
Chapter2: Introduction To Spreadsheet Modeling
Section: Chapter Questions
Problem 20P: Julie James is opening a lemonade stand. She believes the fixed cost per week of running the stand...
Related questions
Question
List five important differences between goods production and service operations.
IMPORTANT NOTE: PLEASE REFER TO THE GIVEN DIFFERENCES ON THE PHOTO ATTACHED.
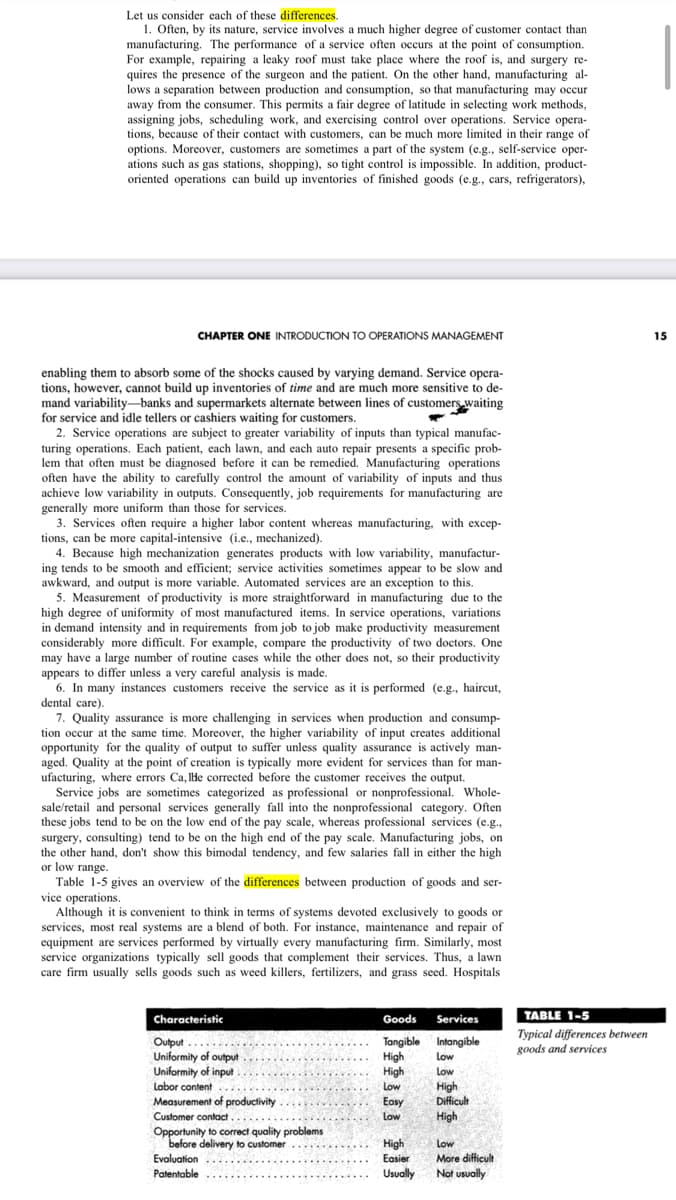
Transcribed Image Text:Let us consider each of these differences.
1. Often, by its nature, service involves a much higher degree of customer contact than
manufacturing. The performance of a service often occurs at the point of consumption.
For example, repairing a leaky roof must take place where the roof is, and surgery re-
quires the presence of the surgeon and the patient. On the other hand, manufacturing al-
lows a separation between production and consumption, so that manufacturing may occur
away from the consumer. This permits a fair degree of latitude in selecting work methods,
assigning jobs, scheduling work, and exercising control over operations. Service opera-
tions, because of their contact with customers, can be much more limited in their range of
options. Moreover, customers are sometimes a part of the system (e.g., self-service oper-
ations such as gas stations, shopping), so tight control is impossible. In addition, product-
oriented operations can build up inventories of finished goods (e.g., cars, refrigerators),
CHAPTER ONE INTRODUCTION TO OPERATIONS MANAGEMENT
enabling them to absorb some of the shocks caused by varying demand. Service opera-
tions, however, cannot build up inventories of time and are much more sensitive to de-
mand variability-banks and supermarkets alternate between lines of customers waiting
for service and idle tellers or cashiers waiting for customers.
2. Service operations are subject to greater variability of inputs than typical manufac-
turing operations. Each patient, each lawn, and each auto repair presents a specific prob-
lem that often must be diagnosed before it can be remedied. Manufacturing operations
often have the ability to carefully control the amount of variability of inputs and thus
achieve low variability in outputs. Consequently, job requirements for manufacturing are
generally more uniform than those for services.
3. Services often require a higher labor content whereas manufacturing, with excep-
tions, can be more capital-intensive (i.e., mechanized).
4. Because high mechanization generates products with low variability, manufactur-
ing tends to be smooth and efficient; service activities sometimes appear to be slow and
awkward, and output is more variable. Automated services are an exception to this.
5. Measurement of productivity is more straightforward in manufacturing due to the
high degree of uniformity of most manufactured items. In service operations, variations
in demand intensity and in requirements from job to job make productivity measurement
considerably more difficult. For example, compare the productivity of two doctors. One
may have a large number of routine cases while the other does not, so their productivity
appears to differ unless a very careful analysis is made.
6. In many instances customers receive the service as it is performed (e.g., haircut,
dental care).
7. Quality assurance is more challenging in services when production and consump-
tion occur at the same time. Moreover, the higher variability of input creates additional
opportunity for the quality of output to suffer unless quality assurance is actively man-
aged. Quality at the point of creation is typically more evident for services than for man-
ufacturing, where errors Ca, lhe corrected before the customer receives the output.
Service jobs are sometimes categorized as professional or nonprofessional. Whole-
sale/retail and personal services generally fall into the nonprofessional category. Often
these jobs tend to be on the low end of the pay scale, whereas professional services (e.g.,
surgery, consulting) tend to be on the high end of the pay scale. Manufacturing jobs, on
the other hand, don't show this bimodal tendency, and few salaries fall in either the high
or low range.
Table 1-5 gives an overview of the differences between production of goods and ser-
vice operations.
Although it is convenient to think in terms of systems devoted exclusively to goods or
services, most real systems are a blend of both. For instance, maintenance and repair of
equipment are services performed by virtually every manufacturing firm. Similarly, most
service organizations typically sell goods that complement their services. Thus, a lawn
care firm usually sells goods such as weed killers, fertilizers, and grass seed. Hospitals
Characteristic
Output..
Uniformity of output
Uniformity of input.
Labor content
Measurement of productivity
Customer contact.......
Opportunity to correct quality problems
before delivery to customer
Evaluation
Patentable
Goods
Tangible
High
High
Low
Easy
Low
High
Easier
Usually
Services
Intangible
Low
Low
High
Difficult
High
Low
More difficult
Not usually
TABLE 1-5
Typical differences between
goods and services
15
Expert Solution

This question has been solved!
Explore an expertly crafted, step-by-step solution for a thorough understanding of key concepts.
Step by step
Solved in 2 steps

Recommended textbooks for you
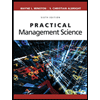
Practical Management Science
Operations Management
ISBN:
9781337406659
Author:
WINSTON, Wayne L.
Publisher:
Cengage,
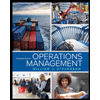
Operations Management
Operations Management
ISBN:
9781259667473
Author:
William J Stevenson
Publisher:
McGraw-Hill Education
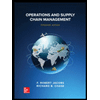
Operations and Supply Chain Management (Mcgraw-hi…
Operations Management
ISBN:
9781259666100
Author:
F. Robert Jacobs, Richard B Chase
Publisher:
McGraw-Hill Education
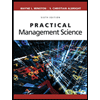
Practical Management Science
Operations Management
ISBN:
9781337406659
Author:
WINSTON, Wayne L.
Publisher:
Cengage,
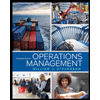
Operations Management
Operations Management
ISBN:
9781259667473
Author:
William J Stevenson
Publisher:
McGraw-Hill Education
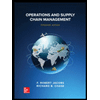
Operations and Supply Chain Management (Mcgraw-hi…
Operations Management
ISBN:
9781259666100
Author:
F. Robert Jacobs, Richard B Chase
Publisher:
McGraw-Hill Education
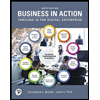
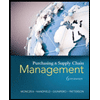
Purchasing and Supply Chain Management
Operations Management
ISBN:
9781285869681
Author:
Robert M. Monczka, Robert B. Handfield, Larry C. Giunipero, James L. Patterson
Publisher:
Cengage Learning
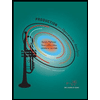
Production and Operations Analysis, Seventh Editi…
Operations Management
ISBN:
9781478623069
Author:
Steven Nahmias, Tava Lennon Olsen
Publisher:
Waveland Press, Inc.