MiniTek manufactures private-label small electronic products, such as alarm clocks, calculators, kitchen timers, stop watches, and automatic pencil sharpeners. Some of the products are sold as a set, and others are sold individually. Products are studied as to their sales potential, and then cost estimates are made. The engineering Department develops production plans, and then cost estimates are made. The Engineering Department develops product introductions. Only two products introduced by the company have been discontinued. One of the products currently sold is a mini-alarm clock. The clock has four alarms and can be programmed to sound at various times and for varying lengths of time. The company has experienced a great deal of difficulty in making circuit boards for the clocks. The production process has never operated smoothly. The production is unprofitable at the present time, primarily because of warranty repairs and product recalls. Two models of the clocks were recalled, for example, because they sometimes cause an electrical shock when the alarms were being shut off. The Engineering Department is attempting to revise the manufacturing process, but the revision will take another 6 months at least. The clocks were very popular when they were introduced, and since they are private label, the company has not suffered much from the recalls. Presently, the company has a very large order for several items from Kmart Stores. The order includes 5,000 of the multi-alarm clocks. When the company suggested that Kmart purchase the clock from another manufacturer, Kmart threatened to rescind the entire order unless the clock were included. The company has therefore investigated the possibility of having another company make the clocks for them. The clocks were bid for the Kmart order based on an estimated $6.90 cost to manufacture: Circuit Board, 1 each @ $2.00 $2.00 Plastic Case, 1 each @ $0.80 0.08 Alarms, 4 @ $0.15 each 0.60 Labor, 15minutes @ 12/hour 3.00 Overhead, $2.00 per labor hour 0.50 MiniTek could purchase the clocks to fill the Kmart order at $10 from Trans-Tech Asia, a Korean manufacturer with a very good quality record, Trans-Tech has offered to reduce the price to $7.50 after MiniTek has been a customer for 6 months, placing an order of at least 1,000 units per month. If MiniTek becomes a “preferred customer” by purchasing 15,000 units per year, the price would be reduced still further to $4.50. Omega Products, a local manufacturing, has also offered to make clocks for MiniTek. They have offered to sell $5,000 clocks for $5 each. However, Omega Products has been in business for only 6 months. They have experienced significant turnover in their labor force, and the local press has reported that the owner may face tax evasion charges soon. The owner of Omega Products is an electronic engineer, however, and the quality of the clocks is likely to be good. If MiniTek decides to purchase the clocks from either Trans-Tech or Omega, all the costs to manufacture could be avoided, except a total of $5,000 in overhead costs for machine depreciation. The machinery is fairly new and has no alternative use. Instructions Answer the following questions What is the difference in profit under each of the alternatives if the clocks are to be sold for $14.50 each to Kmart? What are the most important nonfinancial factors that MiniTek should consider when making this decision? What do you think MiniTek should do in regard to the Kmart order? What should it do in regard to continuing to manufacture the multi-alarm clocks? Be prepared to defend your answer.
MiniTek manufactures private-label small electronic products, such as alarm clocks, calculators, kitchen timers, stop watches, and automatic pencil sharpeners. Some of the products are sold as a set, and others are sold individually. Products are studied as to their sales potential, and then cost estimates are made. The engineering Department develops production plans, and then cost estimates are made. The Engineering Department develops product introductions. Only two products introduced by the company have been discontinued.
One of the products currently sold is a mini-alarm clock. The clock has four alarms and can be programmed to sound at various times and for varying lengths of time. The company has experienced a great deal of difficulty in making circuit boards for the clocks. The production process has never operated smoothly. The production is unprofitable at the present time, primarily because of warranty repairs and product recalls. Two models of the clocks were recalled, for example, because they sometimes cause an electrical shock when the alarms were being shut off. The Engineering Department is attempting to revise the manufacturing process, but the revision will take another 6 months at least.
The clocks were very popular when they were introduced, and since they are private label, the company has not suffered much from the recalls. Presently, the company has a very large order for several items from Kmart Stores. The order includes 5,000 of the multi-alarm clocks. When the company suggested that Kmart purchase the clock from another manufacturer, Kmart threatened to rescind the entire order unless the clock were included.
The company has therefore investigated the possibility of having another company make the clocks for them. The clocks were bid for the Kmart order based on an estimated $6.90 cost to manufacture:
Circuit Board, 1 each @ $2.00 $2.00
Plastic Case, 1 each @ $0.80 0.08
Alarms, 4 @ $0.15 each 0.60
Labor, 15minutes @ 12/hour 3.00
Overhead, $2.00 per labor hour 0.50
MiniTek could purchase the clocks to fill the Kmart order at $10 from Trans-Tech Asia, a Korean manufacturer with a very good quality record, Trans-Tech has offered to reduce the price to $7.50 after MiniTek has been a customer for 6 months, placing an order of at least 1,000 units per month. If MiniTek becomes a “preferred customer” by purchasing 15,000 units per year, the price would be reduced still further to $4.50.
Omega Products, a local manufacturing, has also offered to make clocks for MiniTek. They have offered to sell $5,000 clocks for $5 each. However, Omega Products has been in business for only 6 months. They have experienced significant turnover in their labor force, and the local press has reported that the owner may face tax evasion charges soon. The owner of Omega Products is an electronic engineer, however, and the quality of the clocks is likely to be good.
If MiniTek decides to purchase the clocks from either Trans-Tech or Omega, all the costs to manufacture could be avoided, except a total of $5,000 in overhead costs for machine
Instructions
Answer the following questions
- What is the difference in profit under each of the alternatives if the clocks are to be sold for $14.50 each to Kmart?
- What are the most important nonfinancial factors that MiniTek should consider when making this decision?
- What do you think MiniTek should do in regard to the Kmart order? What should it do in regard to continuing to manufacture the multi-alarm clocks? Be prepared to defend your answer.

Trending now
This is a popular solution!
Step by step
Solved in 4 steps with 2 images

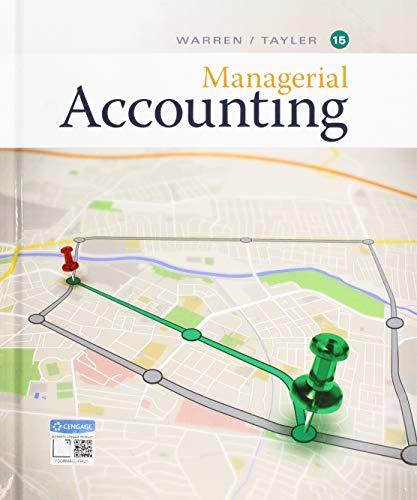
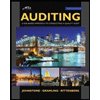
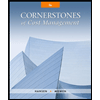
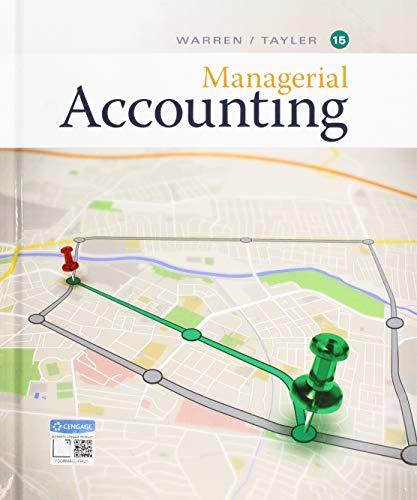
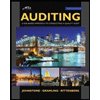
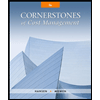
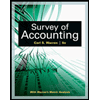
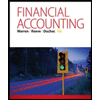
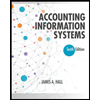