Operation Costing, Just-in-Time System and Backflush Costing 269 11. Exercises Exercise 1 (Operation Costing) The Packo Company, a small manufacturer, makes a variety of tool boxes. The company's manufacturing operations and their costs for November were Cutting Assembly Finishing P16,500 22.900 P39,400 Total Direct manufacturing labor Manufacturing overhead P2,600 3.000 P5,600 P4,800 P23.900 3.300 29,200 P8,100 P53,100 Three styles of boxes were produced in November. The quantities and direct materials costs were Style Standard Quantity 1,200 600 Direct materials P18,000 6,600 5.400 P30,060 Home Industrial 200 The company uses actual costing. It takes direct materials to each style of box. It combines direct manufacturing labor and manufacturing overhead and allocates the conversion costs on the basis of all product units passing through an operation. All product units are assumed to receive an identical amount of time and effort in each operation. The industrial style, however, does not go through the finishing operation. Required: 1. Tabulate the conversion costs of each operation, the total units produced, and the conversion costs per unit for November. 2. Calculate the total costs and the cost per unit of each style of box produced in November. Be sure to account for all the total costs. 3. Prepare summary journal entries for each operation. For simplicity, assume that all direct materials are introduced at the beginning of the cutting operation. Also, assume that all units were transferred to finished goods when completed and that there was no beginning or ending work in process. Prepare one summary entry for all conversion costs incurred, but prepare a separate entry for allocating conversion costs in each operation.
Operation Costing, Just-in-Time System and Backflush Costing 269 11. Exercises Exercise 1 (Operation Costing) The Packo Company, a small manufacturer, makes a variety of tool boxes. The company's manufacturing operations and their costs for November were Cutting Assembly Finishing P16,500 22.900 P39,400 Total Direct manufacturing labor Manufacturing overhead P2,600 3.000 P5,600 P4,800 P23.900 3.300 29,200 P8,100 P53,100 Three styles of boxes were produced in November. The quantities and direct materials costs were Style Standard Quantity 1,200 600 Direct materials P18,000 6,600 5.400 P30,060 Home Industrial 200 The company uses actual costing. It takes direct materials to each style of box. It combines direct manufacturing labor and manufacturing overhead and allocates the conversion costs on the basis of all product units passing through an operation. All product units are assumed to receive an identical amount of time and effort in each operation. The industrial style, however, does not go through the finishing operation. Required: 1. Tabulate the conversion costs of each operation, the total units produced, and the conversion costs per unit for November. 2. Calculate the total costs and the cost per unit of each style of box produced in November. Be sure to account for all the total costs. 3. Prepare summary journal entries for each operation. For simplicity, assume that all direct materials are introduced at the beginning of the cutting operation. Also, assume that all units were transferred to finished goods when completed and that there was no beginning or ending work in process. Prepare one summary entry for all conversion costs incurred, but prepare a separate entry for allocating conversion costs in each operation.
Chapter5: Process Costing
Section: Chapter Questions
Problem 2PB: The following product costs are available for Kellee Company on the production of eyeglass frames:...
Related questions
Question
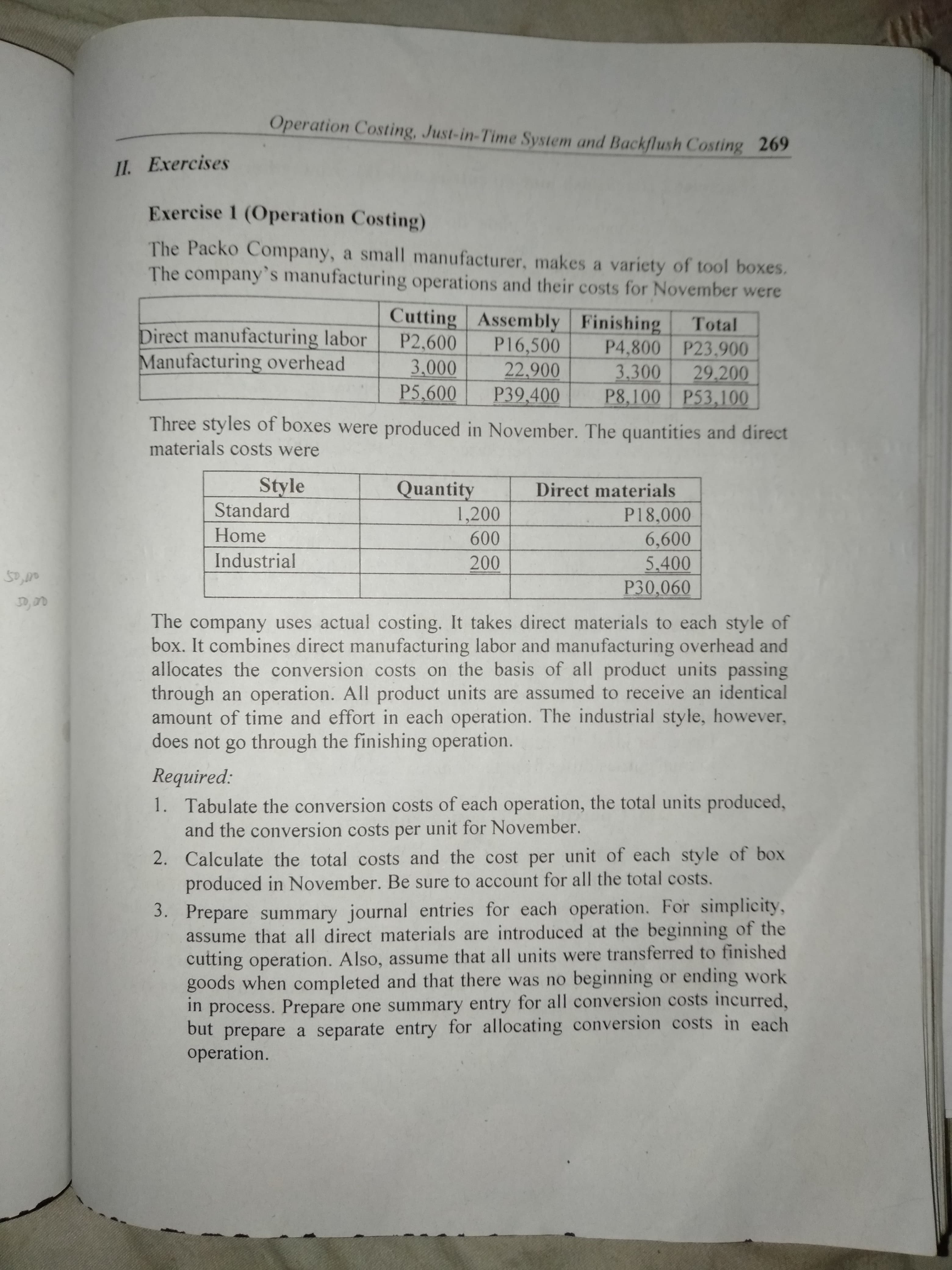
Transcribed Image Text:Operation Costing, Just-in-Time System and Backflush Costing 269
11. Exercises
Exercise 1 (Operation Costing)
The Packo Company, a small manufacturer, makes a variety of tool boxes.
The company's manufacturing operations and their costs for November were
Cutting Assembly Finishing
P16,500
22.900
P39,400
Total
Direct manufacturing labor
Manufacturing overhead
P2,600
3.000
P5,600
P4,800 P23.900
3.300
29,200
P8,100 P53,100
Three styles of boxes were produced in November. The quantities and direct
materials costs were
Style
Standard
Quantity
1,200
600
Direct materials
P18,000
6,600
5.400
P30,060
Home
Industrial
200
The company uses actual costing. It takes direct materials to each style of
box. It combines direct manufacturing labor and manufacturing overhead and
allocates the conversion costs on the basis of all product units passing
through an operation. All product units are assumed to receive an identical
amount of time and effort in each operation. The industrial style, however,
does not go through the finishing operation.
Required:
1. Tabulate the conversion costs of each operation, the total units produced,
and the conversion costs per unit for November.
2. Calculate the total costs and the cost per unit of each style of box
produced in November. Be sure to account for all the total costs.
3. Prepare summary journal entries for each operation. For simplicity,
assume that all direct materials are introduced at the beginning of the
cutting operation. Also, assume that all units were transferred to finished
goods when completed and that there was no beginning or ending work
in
process. Prepare one summary entry for all conversion costs incurred,
but prepare a separate entry for allocating conversion costs in each
operation.
Expert Solution

This question has been solved!
Explore an expertly crafted, step-by-step solution for a thorough understanding of key concepts.
This is a popular solution!
Trending now
This is a popular solution!
Step by step
Solved in 4 steps with 4 images

Recommended textbooks for you
Principles of Accounting Volume 2
Accounting
ISBN:
9781947172609
Author:
OpenStax
Publisher:
OpenStax College
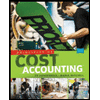
Principles of Cost Accounting
Accounting
ISBN:
9781305087408
Author:
Edward J. Vanderbeck, Maria R. Mitchell
Publisher:
Cengage Learning
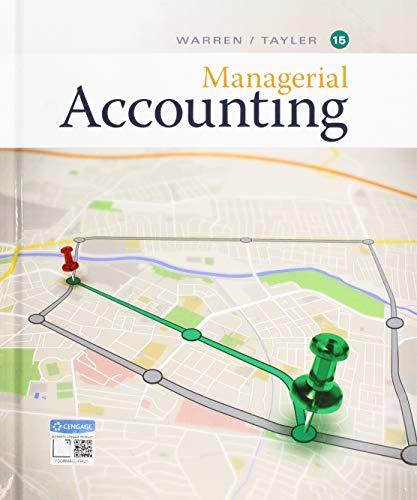
Managerial Accounting
Accounting
ISBN:
9781337912020
Author:
Carl Warren, Ph.d. Cma William B. Tayler
Publisher:
South-Western College Pub
Principles of Accounting Volume 2
Accounting
ISBN:
9781947172609
Author:
OpenStax
Publisher:
OpenStax College
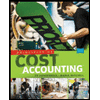
Principles of Cost Accounting
Accounting
ISBN:
9781305087408
Author:
Edward J. Vanderbeck, Maria R. Mitchell
Publisher:
Cengage Learning
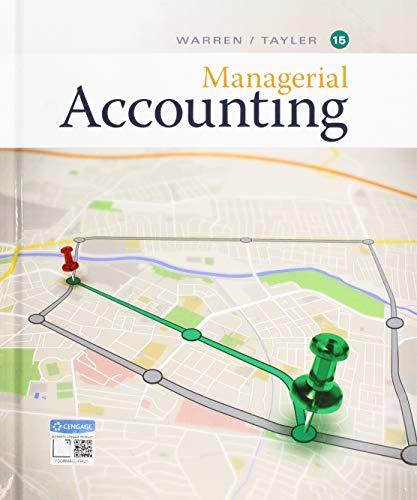
Managerial Accounting
Accounting
ISBN:
9781337912020
Author:
Carl Warren, Ph.d. Cma William B. Tayler
Publisher:
South-Western College Pub
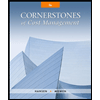
Cornerstones of Cost Management (Cornerstones Ser…
Accounting
ISBN:
9781305970663
Author:
Don R. Hansen, Maryanne M. Mowen
Publisher:
Cengage Learning
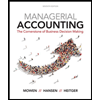
Managerial Accounting: The Cornerstone of Busines…
Accounting
ISBN:
9781337115773
Author:
Maryanne M. Mowen, Don R. Hansen, Dan L. Heitger
Publisher:
Cengage Learning
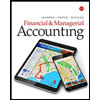
Financial & Managerial Accounting
Accounting
ISBN:
9781337119207
Author:
Carl Warren, James M. Reeve, Jonathan Duchac
Publisher:
Cengage Learning