Spartax Corp manufactures cranes for commercial use. The company produces two models. Designed as regular and advanced. The company uses job-order cost accounting system with manufacturing overhead applied on the basis of direct-labor hours. The system has been in place with little change for 25 years. Product cost and annual sales are as follows: *The calculation of manufacturing overhead rate, based on budgeted direct labor hour of 34,000 hours, is as follows: Regular Model: Annual Sales = 20,000 unit Direct Material = $ 60 Direct Labor = $ 60 (1 hour at $ 60) Manufacturing Overhead* = $ 630 ( 1 hour at $ 630) Advanced Model: Annual Sales = 1,000 unit Direct Material = $ 150 Direct Labor = $ 120 ( 2 hour at $ 60) Manufacturing Overhead* = $ 1,260 ( 2 hour at $ 630) *The calculation of manufacturing overhead rate, based on budgeted direct labor hour of 34,000 hours, is as follows: Manufacturing Overhead budget: Depreciation, machinery = $ 8,880,000 Maintenance, machinery = $ 720,000 Depreciation, taxes, and insurance for factory = $ 1,800,000 Engineering = $ 2,100,000 Purchasing, receiving, and shipping = $ 1,500,000 Inspection and repair for defects = $ 2,250,000 Material handling = $ 2,400,000 Miscellaneous manufacturing overhead cost = $ 1,770,000 Predetermined Overhead Rate = Manifacturing Overhead Budget / Direct Labor hour budget = $ 21420,000/34,000 hours = $ 630 per hour For the past 10 years, the company’s pricing formula has been to set each product’s target price at 115% of its full product cost. Recently, however, the regular-model has come under increasing price pressure from offshore competitors. The offshore competitor can sell similar product for $800. The result was that the price on the regular model has been lowered to $825. The controller proposed a change in product costing system and collected data needed to implement an activity-based costing system. The data are as follows: Activity Cost Pool Cost Driver Regular Model Advanced Model 1. Depreciation, machinery Maintenance, machinery Machine Time 42% 58% 2. Engineering Inspection adn repair of defects Engineering hour 50% 50% 3. Purchasing, receiving and shipping Material handling Number of material orders 50% 50% 4. Depreciation, taxes, and insurance for fac tory Miscellaneous manufacturing overhead Factory space usage 45% 55% Required: 1. Compute target price of the two models, based on the traditional, volume based product costing system. 2. Compute new product cost for the two models based on the new data collected by the controller. 3. Calculate a new target price for the two models, based on the activiti-based costing system.
Process Costing
Process costing is a sort of operation costing which is employed to determine the value of a product at each process or stage of producing process, applicable where goods produced from a series of continuous operations or procedure.
Job Costing
Job costing is adhesive costs of each and every job involved in the production processes. It is an accounting measure. It is a method which determines the cost of specific jobs, which are performed according to the consumer’s specifications. Job costing is possible only in businesses where the production is done as per the customer’s requirement. For example, some customers order to manufacture furniture as per their needs.
ABC Costing
Cost Accounting is a form of managerial accounting that helps the company in assessing the total variable cost so as to compute the cost of production. Cost accounting is generally used by the management so as to ensure better decision-making. In comparison to financial accounting, cost accounting has to follow a set standard ad can be used flexibly by the management as per their needs. The types of Cost Accounting include – Lean Accounting, Standard Costing, Marginal Costing and Activity Based Costing.
Spartax Corp manufactures cranes for commercial use. The company produces two models. Designed as regular and advanced. The company uses
*The calculation of manufacturing overhead rate, based on budgeted direct labor hour of 34,000 hours, is as follows:
Regular Model:
Annual Sales = 20,000 unit
Direct Material = $ 60
Direct Labor = $ 60 (1 hour at $ 60)
Manufacturing Overhead* = $ 630 ( 1 hour at $ 630)
Advanced Model:
Annual Sales = 1,000 unit
Direct Material = $ 150
Direct Labor = $ 120 ( 2 hour at $ 60)
Manufacturing Overhead* = $ 1,260 ( 2 hour at $ 630)
*The calculation of manufacturing overhead rate, based on budgeted direct labor hour of 34,000 hours, is as follows:
Manufacturing Overhead budget:
Maintenance, machinery = $ 720,000
Depreciation, taxes, and insurance for factory = $ 1,800,000
Engineering = $ 2,100,000
Purchasing, receiving, and shipping = $ 1,500,000
Inspection and repair for defects = $ 2,250,000
Material handling = $ 2,400,000
Miscellaneous
Predetermined Overhead Rate = Manifacturing Overhead Budget / Direct Labor hour budget
= $ 21420,000/34,000 hours
= $ 630 per hour
For the past 10 years, the company’s pricing formula has been to set each product’s target price at 115% of its full product cost. Recently, however, the regular-model has come under increasing price pressure from offshore competitors. The offshore competitor can sell similar product for $800. The result was that the price on the regular model has been lowered to $825.
The controller proposed a change in product costing system and collected data needed to implement an activity-based costing system. The data are as follows:
Activity Cost Pool | Cost Driver | Regular Model | Advanced Model |
1. Depreciation, machinery Maintenance, machinery |
Machine Time | 42% | 58% |
2. Engineering Inspection adn repair of defects |
Engineering hour | 50% | 50% |
3. Purchasing, receiving and shipping Material handling
|
Number of material orders | 50% | 50% |
4. Depreciation, taxes, and insurance for fac tory Miscellaneous manufacturing overhead |
Factory space usage | 45% | 55% |
Required:
1. Compute target price of the two models, based on the traditional, volume based product costing system.
2. Compute new product cost for the two models based on the new data collected by the controller.
3. Calculate a new target price for the two models, based on the activiti-based costing system.

Step by step
Solved in 2 steps with 6 images

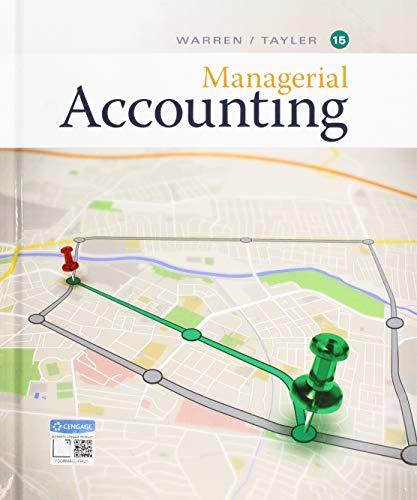
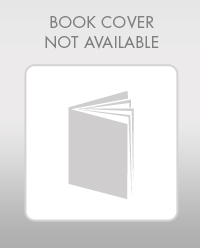
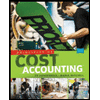
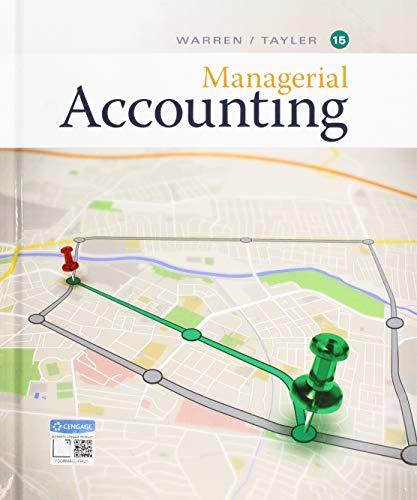
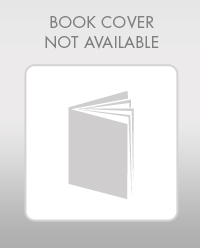
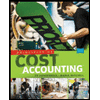
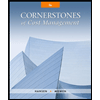
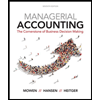