Thunder Bolt, Inc., is a manufacturer of the very popular G36 motorcycles. The management at Thunder Bolt has recently adopted absorption costing and is debating which denominatorlevel concept to use. The G36 motorcycles sell for an average price of $8,200. Budgeted fixed manufacturing overhead costs for 2017 are estimated at $6,480,000. Thunder Bolt, Inc., uses subassembly operators that provide component parts. The following are the denominator-level options that management has been considering: a. Theoretical capacity—based on three shifts, completion of five motorcycles per shift, and a 360-day year—3 * 5 * 360 = 5,400. b. Practical capacity—theoretical capacity adjusted for unavoidable interruptions, breakdowns, and so forth—3 * 4 * 320 = 3,840. c. Normal capacity utilization—estimated at 3,240 units. d. Master-budget capacity utilization—the strengthening stock market and the growing popularity of motorcycles have prompted the marketing department to issue an estimate for 2017 of 3,600 units. Q.Under a cost-based pricing system, what are the negative aspects of a master-budget denominator level? What are the positive aspects?
Thunder Bolt, Inc., is a manufacturer of the very popular G36 motorcycles. The management at Thunder Bolt has recently adopted absorption costing and is debating which denominatorlevel concept to use. The G36 motorcycles sell for an average price of $8,200. Budgeted fixed
a. Theoretical capacity—based on three shifts, completion of five motorcycles per shift, and a 360-day year—3 * 5 * 360 = 5,400.
b. Practical capacity—theoretical capacity adjusted for unavoidable interruptions, breakdowns, and so forth—3 * 4 * 320 = 3,840.
c. Normal capacity utilization—estimated at 3,240 units.
d. Master-budget capacity utilization—the strengthening stock market and the growing popularity of motorcycles have prompted the marketing department to issue an estimate for 2017 of 3,600 units.
Q.Under a cost-based pricing system, what are the negative aspects of a master-budget denominator level? What are the positive aspects?

Trending now
This is a popular solution!
Step by step
Solved in 2 steps

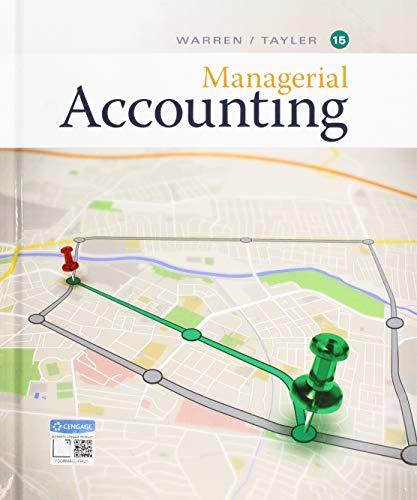
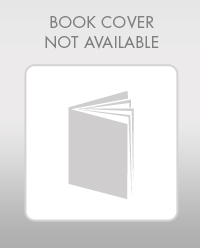
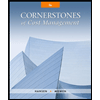
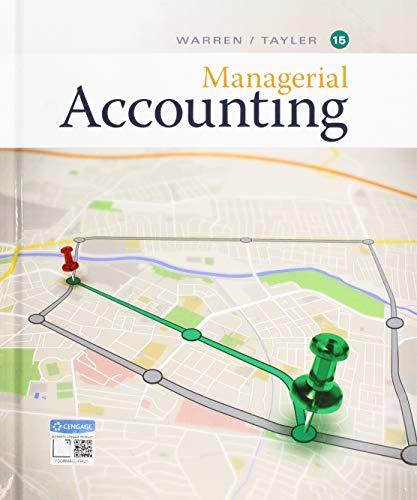
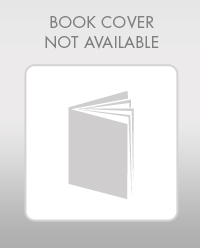
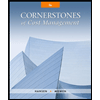