Canine Kernels Company (CKC) manufactures two different types of dog chew toys (A and B, sold in 1,000-count boxes) that are manufactured and assembled on three different workstations (W, X, and Y) using a small-batch process (see the following figure). Batch setup times are negligible. The flowchart denotes the path each product follows through the manufacturing process, and each product’s price, demand per week, and processing times per unit are indicated as well. Purchased parts and raw materials consumed during production are represented by inverted triangles. CKC can make and sell up to the limit of its demand per week; no penalties are incurred for not being able to meet all the demand. Each workstation is staffed by a worker who is dedicated to working on that workstation alone and is paid $6 per hour. Total labor costs per week are fixed. Variable overhead costs are $3,500/week. The plant operates one 8-hour shift per day or 40 hours/week. The senior management at Canine Kernels Company (CKC) is concerned with the existing capacity limitation, so they want to accept the mix of orders that maximizes the company’s profits. Traditionally, CKC has utilized a method whereby decisions are made to produce as much of the product with the highest contribution margin as possible (up to the limit of its demand), followed by the next highest contribution margin product, and so on until no more capacity is available. Because capacity is limited, choosing the proper product mix is crucial. Troy Hendrix, the newly hired production supervisor, is an avid follower of the bottleneck method for scheduling. He believes that profitability can indeed be approved if bottleneck resources are exploited to determine the product mix. Calculate the profit gain, both in absolute dollars as well as in terms of percentage gains, by using bottleneck principles for determining product mix.
Canine Kernels Company (CKC) manufactures two different types of dog chew toys (A and B, sold in 1,000-count boxes) that are manufactured and assembled on three different workstations (W, X, and Y) using a small-batch process (see the following figure). Batch setup times are negligible. The flowchart denotes the path each product follows through the manufacturing process, and each product’s price, demand per week, and processing times per unit are indicated as well. Purchased parts and raw materials consumed during production are represented by inverted triangles. CKC can make and sell up to the limit of its demand per week; no penalties are incurred for not being able to meet all the demand. Each workstation is staffed by a worker who is dedicated to working on that workstation alone and is paid $6 per hour. Total labor costs per week are fixed. Variable overhead costs are $3,500/week. The plant operates one 8-hour shift per day or 40 hours/week.
The senior management at Canine Kernels Company (CKC) is concerned with the existing capacity limitation, so they want to accept the mix of orders that maximizes the company’s profits. Traditionally, CKC has utilized a method whereby decisions are made to produce as much of the product with the highest contribution margin as possible (up to the limit of its demand), followed by the next highest contribution margin product, and so on until no more capacity is available. Because capacity is limited, choosing the proper product mix is crucial. Troy Hendrix, the newly hired production supervisor, is an avid follower of the bottleneck method for
- Calculate the profit gain, both in absolute dollars as well as in terms of percentage gains, by using bottleneck principles for determining product mix.
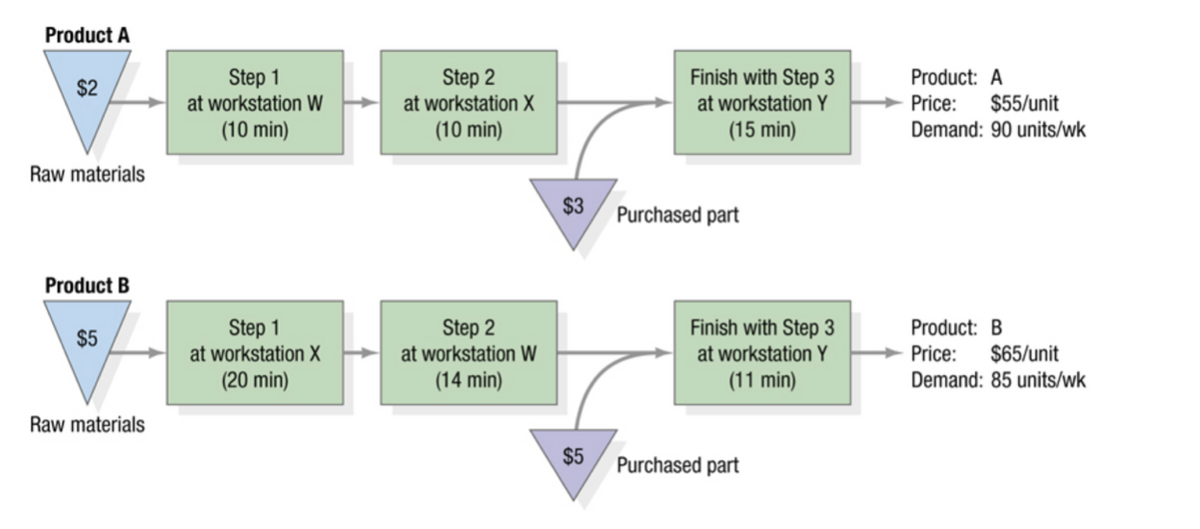

Trending now
This is a popular solution!
Step by step
Solved in 2 steps

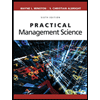
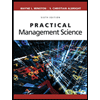