Discuss the relationship between industrial 4.0, industrial internet of things (IIOT) and big data (BD) the implementation in the advanced modern era logistics business operations towards effective supply chain business processes.
Discuss the relationship between industrial 4.0, industrial internet of things (IIOT) and big data (BD) the implementation in the advanced modern era logistics business operations towards effective supply chain business processes.
Practical Management Science
6th Edition
ISBN:9781337406659
Author:WINSTON, Wayne L.
Publisher:WINSTON, Wayne L.
Chapter2: Introduction To Spreadsheet Modeling
Section: Chapter Questions
Problem 20P: Julie James is opening a lemonade stand. She believes the fixed cost per week of running the stand...
Related questions
Question
With the help of the case study. Discuss the relationship between industrial 4.0, industrial internet of things (IIOT) and big data (BD) the implementation in the advanced modern era logistics business operations towards effective supply chain business processes. You are required to include clear necessary reasonable assumptions.
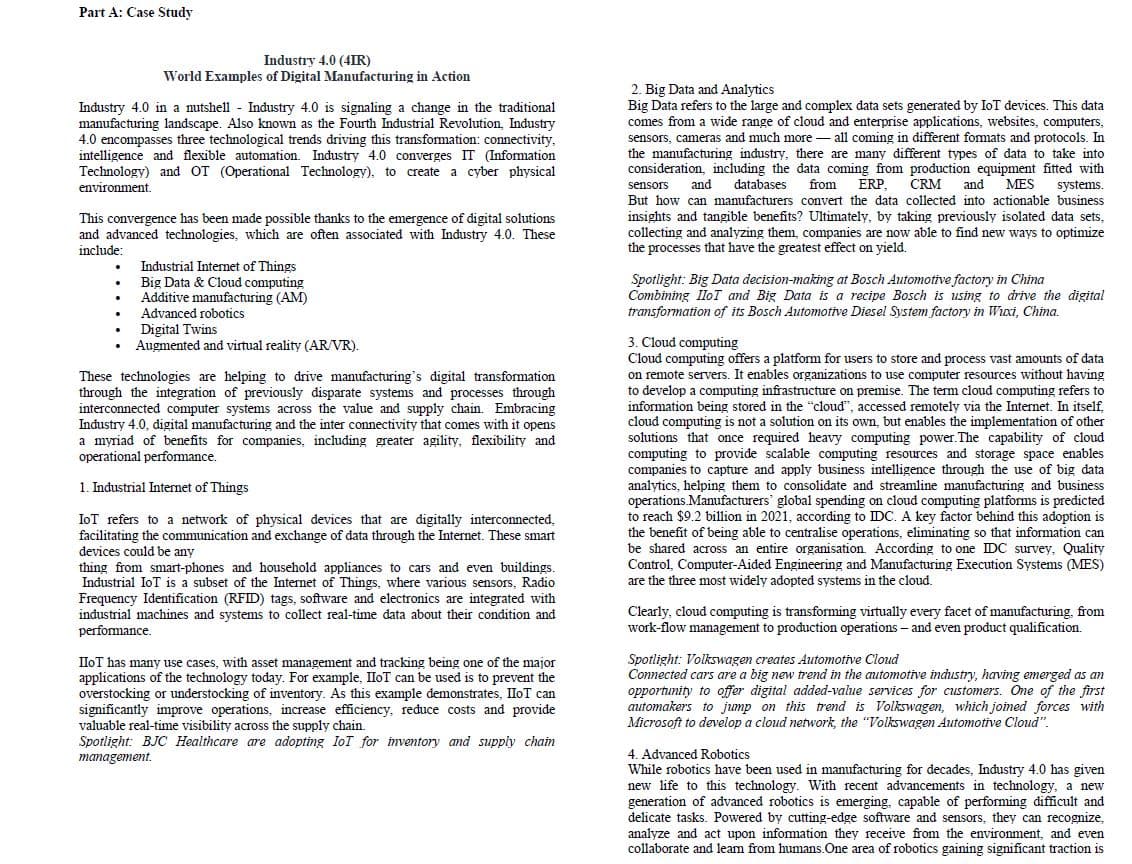
Transcribed Image Text:Part A: Case Study
Industry 4.0 (4IR)
World Examples of Digital Manufacturing in Action
Industry 4.0 in a nutshell - Industry 4.0 is signaling a change in the traditional
manufacturing landscape. Also known as the Fourth Industrial Revolution, Industry
4.0 encompasses three technological trends driving this transformation: connectivity,
intelligence and flexible automation. Industry 4.0 converges IT (Information
Technology) and OT (Operational Technology), to create a cyber physical
environment.
2. Big Data and Analytics
Big Data refers to the large and complex data sets generated by IoT devices. This data
comes from a wide range of cloud and enterprise applications, websites, computers,
sensors, cameras and much more - all coming in different formats and protocols. In
the manufacturing industry, there are many different types of data to take into
consideration, including the data coming from production equipment fitted with
and
databases
from
ERP,
CRM
and
MES
systems,
sensors
But how can manufacturers convert the data collected into actionable business
This convergence has been made possible thanks to the emergence of digital solutions
and advanced technologies, which are often associated with Industry 4.0. These
include:
insights and tangible benefits? Ultimately, by taking previously isolated data sets,
collecting and analyzing them, companies
the processes that have the greatest effect on yield.
now able to find new ways to optimize
Industrial Internet of Things
Big Data & Cloud computing
Additive manufacturing (AM)
Spotlight: Big Data decision-making at Bosch Automotive factory in China
Combining IloT and Big Data is a recipe Bosch is using to drive the digital
transformation of its Bosch Automotive Diesel Svstem factory in Wxi, China.
Advanced robotics
Digital Twins
Augmented and virtual reality (AR/VR).
These technologies are helping to drive manufacturing's digital transformation
through the integration of previously disparate systems and processes through
interconnected computer systems across the value and supply chain. Embracing
Industry 4.0, digital manufacturing and the inter connectivity that comes with it opens
a myriad of benefits for companies, including greater agility, flexibility and
operational performance.
3. Cloud computing
Cloud computing offers a platform for users to store and process vast amounts of data
on remote servers. It enables organizations to use computer resources without having
to develop a computing infrastructure on premise. The term cloud computing refers to
information being stored in the "cloud", accessed remotely via the Internet. In itself,
cloud
is not a solution on its own, but enables the implementation of other
computing
solutions that once required heavy computing power. The capability of cloud
computing to
companies to capture and apply business intelligence through the use of big data
analytics, helping them to consolidate and streamline manufacturing and business
operations.Manufacturers' global spending on cloud computing platforms is predicted
to reach $9.2 billion in 2021, according to IDC. A key factor behind this adoption is
the benefit of being able to centralise operations, eliminating so that information can
be shared across an entire organisation. According to one IDC survey, Quality
Control, Computer-Aided Engineering and Manufacturing Execution Systems (MES)
are the three most widely adopted systems in the cloud.
provide scalable computing resources and storage space enables
1. Industrial Internet of Things
IoT refers to a network of physical devices that are digitally interconnected,
facilitating the communication and exchange of data through the Internet. These smart
devices could be any
thing from smart-phones and household appliances to cars and even buildings.
Industrial IoT is a subset of the Internet of Things, where various sensors, Radio
Frequency Identification (RFID) tags, software and electronics are integrated with
industrial machines and systems to collect real-time data about their condition and
performance.
Clearly, cloud computing is transforming virtually every facet of manufacturing, from
work-flow management to production operations – and even product qualification.
IIOT has many use cases, with asset management and tracking being one of the major
applications of the technology today. For example, IloT can be used is to prevent the
overstocking or understocking of inventory. As this example demonstrates, IloT can
significantly improve operations, increase efficiency, reduce costs and provide
valuable real-time visibility across the supply chain.
Spotlight: BJC Healthcare are adopting IoT for inventory and supply chain
management.
Spotlight: Volkswagen creates Automotive Cloud
Connected cars are a big new trend in the automotive industry, having emerged as an
opportunity to offer digital added-value services for customers. One of the first
automakers to jump on this trend is Volkswagen, which joined forces with
Microsoft to develop a cloud network, the "Volkswagen Automotive Cloud".
4. Advanced Robotics
While robotics have been used in manufacturing for decades, Industry 4.0 has given
new life to this technology. With recent advancements in technology, a new
generation of advanced robotics is emerging, capable of performing difficult and
delicate tasks. Powered by cutting-edge software and sensors, they can recognize,
analyze and act upon infomation they receive from the environment, and even
collaborate and leam from humans.One area of robotics gaining significant traction is
![collaborative robots ("cobots"), designed to work safely around people, freeing to this concept. As an IloT device sends data almost in real time, a digital twin is able
to collect this data continuously, maintaining its fidelity with the original throughout
the lifespan of the product or system. This enables the digital twin to predict potential
issues so that preemptive measures can be taken. For example, an operator can use a
malfunctioning or to predict the lifetime of a
product. This continuous simulation helps to improve designs of products as well as to
workers from repetitive and dangerous tasks.
Spotlight: Fetch Robotics help DHL improve warehouse operations. Fetch Robotics
in a warehouse [Image credit: Fetch Robotics]
to identify why a part
ryin
digital
ensure equipment uptime.
California-based Fetch Robotics has developed collaborative Autonomous Mobile
Robots (AMRS) for locating, tracking, and moving inventory in warehouse and This use of digital twins has long been an important tool in demanding aerospace,
logistics
A DHL distribution centre in the Netherlands is using Fetch AMRS to perform pick technology, machine learning and sensors are expanding the concept of digital
and place operations. At DHL, AMRS autonomously move across the facility
alongside the workers, automatically learning and sharing the most efficient travel
routes. Using self-driving robots
50% and provide up to twice the picking productivity gain, according to the
company.As robots become more autonomous, flexible and cooperative, they will be
able to tackle even more complex assignments, relieving the workers from
monotonous tasks and increasing productivity on the factory floor.
facilities.
heavy machinery and automotive applications. Now, advances in computing
twinning across other industries.
this way can help reduce order cycle time by up to Spotlight: Racing to win with digital twins. Siemen's Digital Twin technology can be
used to create a virtual version of factory assets [Image credit: Siemens).
7. Augmented reality
5. Additive Manufacturing
Alongside robotics and intelligent systems, additive manufacturing, or 3D printing, is
a key technology driving Industry 4.0. Additive manufacturing works by using digital
3D models to create parts with a 3D printer layer by layer. Within the context of
Industry 4.0,
Despite its uptake in consumer applications, the manufacturing industry is just
beginning to explore the benefits of Augmented Reality (AR) technology. And yet,
there is a huge untapped potential for the technology, from helping with assembly
processes to helping to maintain manufacturing equipment. Augmented reality bridges
the gap between the digital and physical worlds by superimposing virtual images or
data onto a physical object. For this, the technology uses AR-capable devices, such as
3D printing is emerging as a valuable digital manufacturing technology.
a rapid prototyping technology, today AM offers a huge scope of smart-phones, tablets and smart glasses.In the context of manufacturing. AR could
possibilities for manufacturing from tooling to mass customization across virtually all
industries.It enables parts to be stored as design files in virtual inventories, so that
they can be produced on-demand and closer to the point of need
enable workers to speed up the assembly process and improve decision-making. For
example, AR glasses could be used to project data, such as layouts, assembly
guidelines, sites of possible malfunction, or a serial number of components, on the
real part, facilitating faster and easier work procedures.
a model known
as distributed manufacturing.Such a decentralized approach to manufacturing can
reduce transportation distances, and hence costs, as well as simplify inventory
management by storing digital files instead of physical parts.
Spotlight: Fast Radius' digital additive manufacturing solutions to enable new
business models. There is a multitude of examples of additive manufacturing being
put to great use, but a key example is, perhaps, Fast Radius.
Spotlight: AR increases productivity at GE
General Electric offers a glimpse at how AR technology can empower manufacturing.
The company is currently piloting the use of AR glasses at its jet engine
manufacturing facility in Cincinnati. Before using these smart glasses, jet engine
ensure tasks were being performed correctly.
The contract manufacturer, which focuses on AM but also offers CNC machining and
injection molding. has production sites in Chicago, Singapore and at the UPS
Worldport facility. This makes Fast Radius well-positioned to drive its vision of fast-
turnaround and mass customisation of products with the help of advanced
manufacturing technologies.
Ultimately, Industry 4.0 is set to take root across the manufacturing ecosystem. But
only by understanding and hamessing the technologies driving Industry 4.0, will
manufacturers stay on the cutting edge of this new digital era.
6. Digital Twins
The concept of a digital twin holds great promise for optimizing the performance and
maintenance of industrial systems. Global research fim, Gartner, predicts that by
2021, 50% of large industrial companies will be using digital twins to monitor and
control their assets and processes.A digital twin is a digital representation of a real-
world product, machine, process, or system, that allows companies to better
understand, analyze and optimize their processes through real-time simulation. While
digital twins can be confused with simulation used in engineering, there is much more
Source: Extracted from Autonomous Mamıfacturing (AMFG) cmd Spotlight reports.](/v2/_next/image?url=https%3A%2F%2Fcontent.bartleby.com%2Fqna-images%2Fquestion%2F92cb8d88-6f81-40a7-a088-e9cbc088f316%2Fd7368a0e-79da-426b-975e-7c92ead461fa%2F7q95cz_processed.jpeg&w=3840&q=75)
Transcribed Image Text:collaborative robots ("cobots"), designed to work safely around people, freeing to this concept. As an IloT device sends data almost in real time, a digital twin is able
to collect this data continuously, maintaining its fidelity with the original throughout
the lifespan of the product or system. This enables the digital twin to predict potential
issues so that preemptive measures can be taken. For example, an operator can use a
malfunctioning or to predict the lifetime of a
product. This continuous simulation helps to improve designs of products as well as to
workers from repetitive and dangerous tasks.
Spotlight: Fetch Robotics help DHL improve warehouse operations. Fetch Robotics
in a warehouse [Image credit: Fetch Robotics]
to identify why a part
ryin
digital
ensure equipment uptime.
California-based Fetch Robotics has developed collaborative Autonomous Mobile
Robots (AMRS) for locating, tracking, and moving inventory in warehouse and This use of digital twins has long been an important tool in demanding aerospace,
logistics
A DHL distribution centre in the Netherlands is using Fetch AMRS to perform pick technology, machine learning and sensors are expanding the concept of digital
and place operations. At DHL, AMRS autonomously move across the facility
alongside the workers, automatically learning and sharing the most efficient travel
routes. Using self-driving robots
50% and provide up to twice the picking productivity gain, according to the
company.As robots become more autonomous, flexible and cooperative, they will be
able to tackle even more complex assignments, relieving the workers from
monotonous tasks and increasing productivity on the factory floor.
facilities.
heavy machinery and automotive applications. Now, advances in computing
twinning across other industries.
this way can help reduce order cycle time by up to Spotlight: Racing to win with digital twins. Siemen's Digital Twin technology can be
used to create a virtual version of factory assets [Image credit: Siemens).
7. Augmented reality
5. Additive Manufacturing
Alongside robotics and intelligent systems, additive manufacturing, or 3D printing, is
a key technology driving Industry 4.0. Additive manufacturing works by using digital
3D models to create parts with a 3D printer layer by layer. Within the context of
Industry 4.0,
Despite its uptake in consumer applications, the manufacturing industry is just
beginning to explore the benefits of Augmented Reality (AR) technology. And yet,
there is a huge untapped potential for the technology, from helping with assembly
processes to helping to maintain manufacturing equipment. Augmented reality bridges
the gap between the digital and physical worlds by superimposing virtual images or
data onto a physical object. For this, the technology uses AR-capable devices, such as
3D printing is emerging as a valuable digital manufacturing technology.
a rapid prototyping technology, today AM offers a huge scope of smart-phones, tablets and smart glasses.In the context of manufacturing. AR could
possibilities for manufacturing from tooling to mass customization across virtually all
industries.It enables parts to be stored as design files in virtual inventories, so that
they can be produced on-demand and closer to the point of need
enable workers to speed up the assembly process and improve decision-making. For
example, AR glasses could be used to project data, such as layouts, assembly
guidelines, sites of possible malfunction, or a serial number of components, on the
real part, facilitating faster and easier work procedures.
a model known
as distributed manufacturing.Such a decentralized approach to manufacturing can
reduce transportation distances, and hence costs, as well as simplify inventory
management by storing digital files instead of physical parts.
Spotlight: Fast Radius' digital additive manufacturing solutions to enable new
business models. There is a multitude of examples of additive manufacturing being
put to great use, but a key example is, perhaps, Fast Radius.
Spotlight: AR increases productivity at GE
General Electric offers a glimpse at how AR technology can empower manufacturing.
The company is currently piloting the use of AR glasses at its jet engine
manufacturing facility in Cincinnati. Before using these smart glasses, jet engine
ensure tasks were being performed correctly.
The contract manufacturer, which focuses on AM but also offers CNC machining and
injection molding. has production sites in Chicago, Singapore and at the UPS
Worldport facility. This makes Fast Radius well-positioned to drive its vision of fast-
turnaround and mass customisation of products with the help of advanced
manufacturing technologies.
Ultimately, Industry 4.0 is set to take root across the manufacturing ecosystem. But
only by understanding and hamessing the technologies driving Industry 4.0, will
manufacturers stay on the cutting edge of this new digital era.
6. Digital Twins
The concept of a digital twin holds great promise for optimizing the performance and
maintenance of industrial systems. Global research fim, Gartner, predicts that by
2021, 50% of large industrial companies will be using digital twins to monitor and
control their assets and processes.A digital twin is a digital representation of a real-
world product, machine, process, or system, that allows companies to better
understand, analyze and optimize their processes through real-time simulation. While
digital twins can be confused with simulation used in engineering, there is much more
Source: Extracted from Autonomous Mamıfacturing (AMFG) cmd Spotlight reports.
Expert Solution

This question has been solved!
Explore an expertly crafted, step-by-step solution for a thorough understanding of key concepts.
This is a popular solution!
Trending now
This is a popular solution!
Step by step
Solved in 2 steps

Knowledge Booster
Learn more about
Need a deep-dive on the concept behind this application? Look no further. Learn more about this topic, operations-management and related others by exploring similar questions and additional content below.Recommended textbooks for you
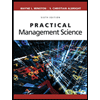
Practical Management Science
Operations Management
ISBN:
9781337406659
Author:
WINSTON, Wayne L.
Publisher:
Cengage,
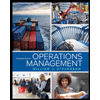
Operations Management
Operations Management
ISBN:
9781259667473
Author:
William J Stevenson
Publisher:
McGraw-Hill Education
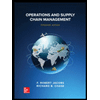
Operations and Supply Chain Management (Mcgraw-hi…
Operations Management
ISBN:
9781259666100
Author:
F. Robert Jacobs, Richard B Chase
Publisher:
McGraw-Hill Education
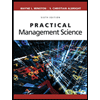
Practical Management Science
Operations Management
ISBN:
9781337406659
Author:
WINSTON, Wayne L.
Publisher:
Cengage,
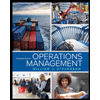
Operations Management
Operations Management
ISBN:
9781259667473
Author:
William J Stevenson
Publisher:
McGraw-Hill Education
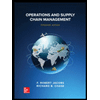
Operations and Supply Chain Management (Mcgraw-hi…
Operations Management
ISBN:
9781259666100
Author:
F. Robert Jacobs, Richard B Chase
Publisher:
McGraw-Hill Education
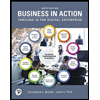
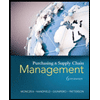
Purchasing and Supply Chain Management
Operations Management
ISBN:
9781285869681
Author:
Robert M. Monczka, Robert B. Handfield, Larry C. Giunipero, James L. Patterson
Publisher:
Cengage Learning
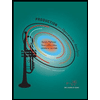
Production and Operations Analysis, Seventh Editi…
Operations Management
ISBN:
9781478623069
Author:
Steven Nahmias, Tava Lennon Olsen
Publisher:
Waveland Press, Inc.