Helsinki Inc. produces premium bottled water. Helsinki purchases artesian water, stores the water in large tanks, and then runs the water through two processes: Filtration, where workers microfilter and ozonate the water Bottling, where workers bottle and package the filtered water During December, the filtration process incurs the following costs in processing 200,000 liters: Wages of workers operating the filtration equipment $11,100 Wages of workers operating ozonation equipment $12,850 Manufacturing overhead allocated to filtration $24,050 Water $120,000 We now consider Helsinki's second process-Bottling. In the Bottling Department, workers bottle the filtered water and pack the bottles into boxes. Conversion costs are incurred evenly throughout the Bottling process, but packaging materials are not added until the end of the process. December data from the Bottling Department is given below: Beginning work in process inventory (40% of the way through the process) 9,000 liters Transferred in from Filtration 160,000 liters Completed and transfer red out to Finished Goods Inventory in December 154,000 liters Ending work in process inventory (65% of the way through the bottling process) 22,000 liters The Filtration Department completed and transferred out 160,000 liters at a total cost of $136,000. Costs in beginning work in process inventory Transferred in $1,760 Direct materials $0 Direct labor $600 Mfg overhead $520 Total beginning WIP on Dec 1 $2880 Costs added during December Transferred in $136,000 Direct materials $30,800 Direct labor $33, 726 Mfg overhead $25,742 Total costs added in Dec $226,268. 8.Complete the first two steps of the process costing procedure for the Bottling Department: summarize the physical flow of units and then compute the equivalent units of direct materials and conversion costs. 9.Complete Steps 3 and 4 of the process costing procedure: Summarize total costs to account for and then compute the cost per equivalent unit for both direct materials and conversion costs. 10.Complete Step 5 of the process costing procedure: Assign costs to units completed and to units in ending inventory. 11.What is the ending WIP balance on December 31?
I only need answers for 8,9,10 and 11. I have attached what I have answered until step 6. You may use it for reference to complete the questions.
Helsinki Inc. produces premium bottled water. Helsinki purchases artesian water, stores the water in large tanks, and then runs the water through two processes:
- Filtration, where workers microfilter and ozonate the water
- Bottling, where workers bottle and package the filtered water
During December, the filtration process incurs the following costs in processing 200,000 liters:
- Wages of workers operating the filtration equipment $11,100
- Wages of workers operating ozonation equipment $12,850
- Manufacturing
overhead allocated to filtration $24,050 - Water $120,000
We now consider Helsinki's second process-Bottling. In the Bottling Department, workers bottle the filtered water and pack the bottles into boxes. Conversion costs are incurred evenly throughout the Bottling process, but packaging materials are not added until the end of the process.
December data from the Bottling Department is given below:
- Beginning work in process inventory (40% of the way through the process) 9,000 liters
- Transferred in from Filtration 160,000 liters
- Completed and transfer red out to Finished Goods Inventory in December 154,000 liters
- Ending work in process inventory (65% of the way through the bottling process) 22,000 liters
The Filtration Department completed and transferred out 160,000 liters at a total cost of $136,000.
Costs in beginning work in process inventory
- Transferred in $1,760
- Direct materials $0
- Direct labor $600
- Mfg overhead $520
- Total beginning WIP on Dec 1 $2880
Costs added during December
- Transferred in $136,000
- Direct materials $30,800
- Direct labor $33, 726
- Mfg overhead $25,742
- Total costs added in Dec $226,268.
8.Complete the first two steps of the
9.Complete Steps 3 and 4 of the process costing procedure: Summarize total costs to account for and then compute the cost per equivalent unit for both direct materials and conversion costs.
10.Complete Step 5 of the process costing procedure: Assign costs to units completed and to units in ending inventory.
11.What is the ending WIP balance on December 31?


Step by step
Solved in 3 steps

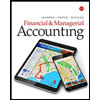
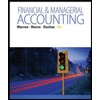
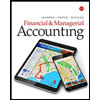
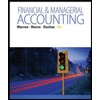