Motorola is known as a company that saved itself. They are one of the companies mentioned in the 1980 television documentary on productivity. If Japan Can, Why Can't We? This program illustrated the quality and productivity problems of numerous companies. In the 1970s, Motorola produced television sets with a defect rate of 150 defects per 100 sets.. In 1974, Motorola sold their television plant to Mitsushita. Using the same American labor force and Japanese quality management techniques, television sets were produced with an average of only 4 defects per 100 sets. Motorola continued to produce two-way radios, pgers, cellular radiotelephones, and other electronic communication systems. In the 1980s, customers complained that Motorola's paging systems were not meeting quality standards; Japanes-made pagers were. Top Motorola executives could either continue losing customers and market share to Japan, as they did in customer electronics during the 1970s, or they could develop a new company culture and insist in TQM. Motorola restarted the company goals for improvement of processes, global market share, and employee involvement. They invested heavily in training, with each employee (top-down) required to take a minimum of forty hours of training each year. They promoted a quality culture by providing workers with a greater degree of job security. Employees are no longer fearful of making suggestions or even suggesting ways to eliminate their own jobs. 1. Managers basically want their company to do well. Why do many managers drift away from TQM or fail to implement basic elements of TQM?
Motorola is known as a company that saved itself. They are one of the companies mentioned in the 1980 television documentary on productivity. If Japan Can, Why Can't We? This program illustrated the quality and productivity problems of numerous companies.
In the 1970s, Motorola produced television sets with a defect rate of 150 defects per 100 sets.. In 1974, Motorola sold their television plant to Mitsushita. Using the same American labor force and Japanese
Motorola continued to produce two-way radios, pgers, cellular radiotelephones, and other electronic communication systems. In the 1980s, customers complained that Motorola's paging systems were not meeting quality standards; Japanes-made pagers were. Top Motorola executives could either continue losing customers and market share to Japan, as they did in customer electronics during the 1970s, or they could develop a new company culture and insist in TQM.
Motorola restarted the company goals for improvement of processes, global market share, and employee involvement. They invested heavily in training, with each employee (top-down) required to take a minimum of forty hours of training each year. They promoted a quality culture by providing workers with a greater degree of job security. Employees are no longer fearful of making suggestions or even suggesting ways to eliminate their own jobs.
1. Managers basically want their company to do well. Why do many managers drift away from TQM or fail to implement basic elements of TQM?

Step by step
Solved in 3 steps

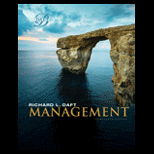
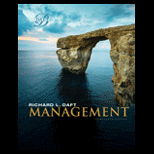