Process Costing versus Alternative Costing Methods, Impact onResource Allocation DecisionGolding Manufacturing, a division of Farnsworth Sporting Inc., produces two different modelsof bows and eight models of knives. The bow-manufacturing process involves the productionof two major subassemblies: the limbs and the handles. The limbs pass through four sequential processes before reaching final assembly: layup, molding, fabricating, and finishing. In thelayup department, limbs are created by laminating layers of wood. In the molding department,the limbs are heat-treated, under pressure, to form strong resilient limbs. In the fabricating department, any protruding glue or other processing residue is removed. Finally, in the finishingdepartment, the limbs are cleaned with acetone, dried, and sprayed with the final finishes.The handles pass through two processes before reaching final assembly: pattern and finishing. In the pattern department, blocks of wood are fed into a machine that is set to shape thehandles. Different patterns are possible, depending on the machine’s setting. After coming outof the machine, the handles are cleaned and smoothed. They then pass to the finishing department, where they are sprayed with the final finishes. In final assembly, the limbs and handlesare assembled into different models using purchased parts such as pulley assemblies, weightadjustment bolts, side plates, and string.Golding, since its inception, has been using process costing to assign product costs. A predetermined overhead rate is used based on direct labor dollars (80% of direct labor dollars).Recently, Golding has hired a new controller, Karen Jenkins. After reviewing the productcosting procedures, Karen requested a meeting with the divisional manager, Aaron Suhr. Thefollowing is a transcript of their conversation:Karen: Aaron, I have some concerns about our cost accounting system. We make two different models of bows and are treating them as if they were the same product. Now I know thatthe only real difference between the models is the handle. The processing of the handles is thesame, but the handles differ significantly in the amount and quality of wood used. Our currentcosting does not reflect this difference in material input. Aaron: Your predecessor is responsible. He believed that tracking the difference in materialcost wasn’t worth the effort. He simply didn’t believe that it would make much difference in theunit cost of either model.Karen: Well, he may have been right, but I have my doubts. If there is a significant difference, it could affect our views of which model is more important to the company. The additionalbookkeeping isn’t very stringent. All we have to worry about is the pattern department. Theother departments fit what I view as a process-costing pattern.Aaron: Why don’t you look into it? If there is a significant difference, go ahead and adjustthe costing system.After the meeting, Karen decided to collect cost data on the two models: the Deluxe modeland the Econo model. She decided to track the costs for one week. At the end of the week, shehad collected the following data from the pattern department:a. There were a total of 2,500 bows completed: 1,000 Deluxe models and 1,500 Economodels.b. There was no BWIP; however, there were 300 units in EWIP: 200 Deluxe and 100 Economodels. Both models were 80% complete with respect to conversion costs and 100%complete with respect to materials.c. The pattern department experienced the following costs:Direct materials $114,000Direct labor 45,667d. On an experimental basis, the requisition forms for materials were modified to identifythe dollar value of the materials used by the Econo and Deluxe models:Econo model $30,000Deluxe model 84,000 Required:1. Compute the unit cost for the handles produced by the pattern department, assumingthat process costing is totally appropriate. Round unit cost to two decimal places.2. Compute the unit cost of each handle, using the separate cost information provided onmaterials. Round unit cost to two decimal places.3. Compare the unit costs computed in Requirements 1 and 2. Is Karen justified in her beliefthat a pure process-costing relationship is not appropriate? Describe the costing systemthat you would recommend.4. In the past, the marketing manager has requested more money for advertising the Econoline. Aaron has repeatedly refused to grant any increase in this product’s advertisingbudget because its per-unit profit (selling price minus manufacturing cost) is so low. Giventhe results in Requirements 1 through 3, was Aaron justified in his position?
Variance Analysis
In layman's terms, variance analysis is an analysis of a difference between planned and actual behavior. Variance analysis is mainly used by the companies to maintain a control over a business. After analyzing differences, companies find the reasons for the variance so that the necessary steps should be taken to correct that variance.
Standard Costing
The standard cost system is the expected cost per unit product manufactured and it helps in estimating the deviations and controlling them as well as fixing the selling price of the product. For example, it helps to plan the cost for the coming year on the various expenses.
Resource Allocation Decision
Golding Manufacturing, a division of Farnsworth Sporting Inc., produces two different models
of bows and eight models of knives. The bow-manufacturing process involves the production
of two major subassemblies: the limbs and the handles. The limbs pass through four sequential processes before reaching final assembly: layup, molding, fabricating, and finishing. In the
layup department, limbs are created by laminating layers of wood. In the molding department,
the limbs are heat-treated, under pressure, to form strong resilient limbs. In the fabricating department, any protruding glue or other processing residue is removed. Finally, in the finishing
department, the limbs are cleaned with acetone, dried, and sprayed with the final finishes.
The handles pass through two processes before reaching final assembly: pattern and finishing. In the pattern department, blocks of wood are fed into a machine that is set to shape the
handles. Different patterns are possible, depending on the machine’s setting. After coming out
of the machine, the handles are cleaned and smoothed. They then pass to the finishing department, where they are sprayed with the final finishes. In final assembly, the limbs and handles
are assembled into different models using purchased parts such as pulley assemblies, weightadjustment bolts, side plates, and string.
Golding, since its inception, has been using process costing to assign product costs. A predetermined overhead rate is used based on direct labor dollars (80% of direct labor dollars).
Recently, Golding has hired a new controller, Karen Jenkins. After reviewing the productcosting procedures, Karen requested a meeting with the divisional manager, Aaron Suhr. The
following is a transcript of their conversation:
Karen: Aaron, I have some concerns about our cost accounting system. We make two different models of bows and are treating them as if they were the same product. Now I know that
the only real difference between the models is the handle. The processing of the handles is the
same, but the handles differ significantly in the amount and quality of wood used. Our current
costing does not reflect this difference in material input.
Aaron: Your predecessor is responsible. He believed that tracking the difference in material
cost wasn’t worth the effort. He simply didn’t believe that it would make much difference in the
unit cost of either model.
Karen: Well, he may have been right, but I have my doubts. If there is a significant difference, it could affect our views of which model is more important to the company. The additional
bookkeeping isn’t very stringent. All we have to worry about is the pattern department. The
other departments fit what I view as a process-costing pattern.
Aaron: Why don’t you look into it? If there is a significant difference, go ahead and adjust
the costing system.
After the meeting, Karen decided to collect cost data on the two models: the Deluxe model
and the Econo model. She decided to track the costs for one week. At the end of the week, she
had collected the following data from the pattern department:
a. There were a total of 2,500 bows completed: 1,000 Deluxe models and 1,500 Econo
models.
b. There was no BWIP; however, there were 300 units in EWIP: 200 Deluxe and 100 Econo
models. Both models were 80% complete with respect to conversion costs and 100%
complete with respect to materials.
c. The pattern department experienced the following costs:
Direct materials $114,000
Direct labor 45,667
d. On an experimental basis, the requisition forms for materials were modified to identify
the dollar value of the materials used by the Econo and Deluxe models:
Econo model $30,000
Deluxe model 84,000
Required:
1. Compute the unit cost for the handles produced by the pattern department, assuming
that process costing is totally appropriate. Round unit cost to two decimal places.
2. Compute the unit cost of each handle, using the separate cost information provided on
materials. Round unit cost to two decimal places.
3. Compare the unit costs computed in Requirements 1 and 2. Is Karen justified in her belief
that a pure process-costing relationship is not appropriate? Describe the costing system
that you would recommend.
4. In the past, the marketing manager has requested more money for advertising the Econo
line. Aaron has repeatedly refused to grant any increase in this product’s advertising
budget because its per-unit profit (selling price minus
the results in Requirements 1 through 3, was Aaron justified in his position?

Trending now
This is a popular solution!
Step by step
Solved in 3 steps

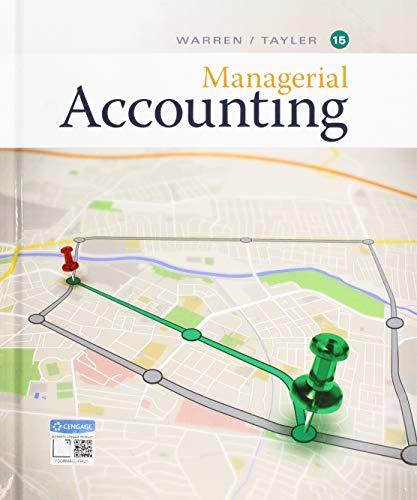
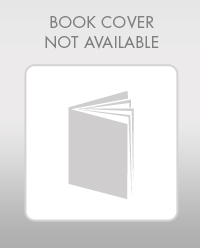
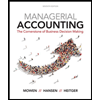
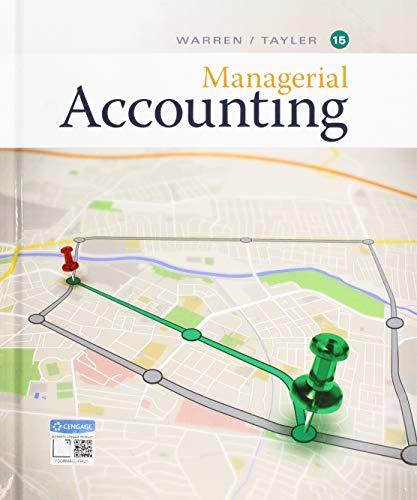
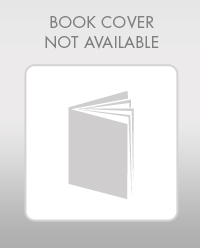
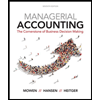
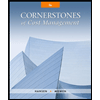