PROCESS IMPROVEMENT PLAN Wild Dog Coffee Company
.docx
keyboard_arrow_up
School
Capella University *
*We aren’t endorsed by this school
Course
FPX5016
Subject
Business
Date
Jan 9, 2024
Type
docx
Pages
14
Uploaded by BaronWildcatMaster674
PROCESS IMPROVEMENT PLAN Wild Dog Coffee Company (Assessment 1) Deidre Hugley-Smith MBA-
FPX5016 (Capella University
Introduction The Wild Dog Coffee Company serves a wide selection of expresso products, small breakfast
and lunch menu items, and a limited evening menu. It is locally owned with a single coffee shop location.
The company is now looking to expand the business by opening an new location but the company wants to ensure that the expresso beverage preparation process will remain exactly the same, while different menu items may be test at the new location. At this time there are three business partner's and their backgrounds include marketing and sales while my background is primarily in operations. Currently they are working on the external aspects of the business that will bring the customers in and my focus is to make sure the internal customer-facing processes are as efficient as possible. To avoid things such as the Panera Bread mosh pit problem that cause their company to lose customers because after the customer placed their orders the wait time was much to long. The Process Improvement Plan will prepare an analysis and recommendations that will help manage the core process improvement for the success of the Wild Dog Coffee Company and the additional coffee shop expansion. Procedure The Wild Dog Coffee Company relies on returning customers as an analysis to determine the excellence of the company. Its ability to retain customers helps us understand if the process and procedure we rely on is successful in increasing sales. We strive to provide the most premium and quality products for our consumer base. We rely on the current processes and how efficiently it performs to provide us with the best successful business. We have detailed the customer ordering process for an expresso to ensure we are doing the process effectively enough to satisfy the customer's expectations and also the timeframe of them waiting on their order to ensure order are prompt and being served in a timely matter to satisfy the customer's wait time expectation.
To make an WDDC Latte the steps include: Take customer's order (Greet the customer asking what they would like from the WDCC menu today or how you may help them) Enter items into the register or bring up mobile order and charge the customer and take the money Ask customer to take survey while they wait Send order to assembly Ground the coffee using a burr grinder (for better results and quality) Using a portafilter to grind directly into allows us to capture more and lose less product and keep the coffee flavor consistent by maintaining the same exact coffee to water ratio Tamp the grounds to ensure the portafilter is properly mixing coffee to water ratios for consistency within the coffee flavors The next step
is to brew the coffee and get the cup for serving the coffee hot and ready to hold the coffee. The Coffee is then put in the machine and locked into place with the filter and the tapped grounds. Ensure you have the hot cup prepared at the machine. Once the coffee is brewed allow the machine to make the cup of coffee. While the machine is prepping the coffee you can prepare all other personal ingredients the customer has requested on the order. The milk froth can then be prepared and added to the top of the WDCC special latte once it has fully poured and the milk froth reaches 150 degrees Fahrenheit. Once the cup has been prepare it can then be handed to the customer after all other personalized ingredients have been added. Handing the beverage to the customer
Metrics: A business metric is a quantifiable measure businesses use to track, monitor and assess the success or failure of variousbusiness processes[ CITATION Ben \l 1033 ]. In the case of the WildDog Coffee Company (WDCC) we want to measure the current process in place to ensure the success of the current coffee shop and the one we are planning to expand and open.To measure process efficiency and effectiveness, you need toidentify and collect relevant process metrics, or quantitative indicators of performance[ CITATION Lin23 \l 1033 ].By analyzing the process we can determine where we need
improvement and the cause and affects of specific changes or implemented processes to the improvement plan process. The most key point in measuring business metrics is to ensure you measure the right business metrics to improve company performance. There To measure how well the WDCC is doing we will use the following metrics to measure the new process: 1.Customer Retention (how many times the customer returns, this can be measured through the app because returning customers are more likely to download the app because of the points system them can use which give them special discounted offers and freebies) 2.Beverage process performance (This can be measured through analyzing the beverage service times data that is for 50 beverage preparation events that was collected using WDCC's order processing system) 3.Order delivery time (This is the time between when the order is submitted and the time the beverage is handed to the customer)
When measuring customer retention, we want to allow our customers to take survey for a 5% discount on their next visit for the first survey. They will be able to answer on a scale of one to ten. Ten being they were most satisfied with their visit, the wait time, and the overall taste of the menu item they purchased. Our target value is that 90% of our customers choose between 8 and 10 rating for all three categories of satisfaction on the survey. If they, don't we hope to get them to return to change their experience and offer then a 10% discount on their next coffee. S0 the target value is that 90% of the customers who take the survey scale their satisfaction at 8 or above. The second metric involves how well the process is performing. The target value for this metrics is having no more than 5 orders per day be returned to the barista to be corrected or refunded. We'd like to ensure the proper training is provided to each employee on the assembly line, the machines are properly functioning, the products necessary to create a drink or lunch menu item is in stock and available for use. We also have to ensure that the steps within the beverage making process are correctly followed through before completing a drink and handing to a customer. The next metric that is vital the success of the WDCC is the beverage process performance. This is vital because when preparing something within a specified timeframe we also want to ensure quality within the products we serve our customers. To measure the time there is a timestamp there is a timestamp from the time the order is submitted and another at the time the order is handed to the customer to measure how long it takes to get the customer's order completed. This measure is vital because it allows us to measure our delivery time for our in store orders because slow orders can decrease our customer satisfaction and also a measurement we use in the survey's for customer retention measurement. The senior baristas have set the target value at 2-3 mins for beverage delivery time.
Purpose Analyze Data for Process Changes Every company would like to maintain the quality their customer's see in their products to increase customer retention and customer satisfaction which increase sales and revenue for the company. The main purpose for process improvement is the identify and eliminate the weaknesses within the business process to assist us in increasing quality and efficiency
and to eliminate bottleneck in within the company's day-to-day operations. It also allows us to improve workflow or daily output and to optimize the team's performance and deliver more customer satisfaction. By creating a more standardized process we can guarantee that the quality and output will be the same at the newly opened location. Using this process improvement we can follow the same the day to day operations at both locations to ensure the customers satisfaction is met at both locations. This improvement process will also assist in maintaining customer satisfaction. Three Sigma is the third Sigma level, which dictates that there can only be a margin of error up to three standard deviations from the mean[ CITATION Ind23 \l 1033 ]. To ensure a small margin of error this is Sigma 3 is a statical
approach to monitoring quality.Sigma levels appear from one to six, where each level represents a percentage of acceptable error as it relates to the statistical standard deviation[ CITATION Ind23 \l 1033 ]. To analyze the date we collected for 50 beverage preparation events using the WDDC order processing system. This data will help us measure if the process improvement plan is actually working towards the success or failure of meeting the 2-3 minute beverage preparation process. Within the data analysis we will see if the process is capable of 3-Sigma, if its centered, and if the process is within statistical control. The summary and calculations of this data is accessible in Appendix D.
To check if the process is center we had to measure the Cp and Cpk values to determine if they were equal.Cp and Cpk measure your consistency compared to your average performance[CITATION Ted \l 1033 ].The CP score is calculated by taking the(Upper limit- Lowe Limit)/(6* standard deviation). On the other hand Cpk measures how close a process is performing compared to is specification limits and account for the natural variability of the process. When the Cpk is negative, it means that a process will product will not meet customer satisfaction.Cpk score is calculated by taking (Upper Limit-Mean)/(3*standard deviation). Based on the calculation we were able to conclude that they process is centered. The values were equal. When looking at the Cpk or the Capability Index we can determine that since it is 1 it is under the "need control" category, meaning that the process could be worse off but it does have room for improvement before we finalize and consider it the most success option or process for efficiency. More quality testing should take places to improve the process. The current standard deviation is 0.5903 minutes, and our mean is 2.47 minutes. The max value is 3+ Standard deviation is 4.24 minutes and the lowest value of -3 standard deviation is 0.7minutes. Our shortest time to produce the latte was 1:55 minutes and the longest time is 3:43 minutes. This tells us that we are capable of 3 Sigma. The data is statically under control as well. Analyze Cause and Effect of Process Variances With any process variance there is an cause and effect and always chance for error. There are a number of significant factors that play a role in the errors that may or have occurred. Some of those potential causesof variance can be identified to ensure we can avoid error within the process and find opportunities for improvement. In Appendix B we detailed four the M's which are machine, manpower, method and management. In the case of the WDCC we used these three M's of the six because they were the most success baring factors that could hinder the process.
One of the first possible causes could be Manpower because though the employees are trained in beverage preparation, they have to also be trained to uphold the quality standards of the WDCC company employee policy of providing quality products and services. When baristas have a full lobby this
can make them rush a little more to produce the drinks within the 2-3 minute time frame but we also want to ensure they are providing quality drinks that will meet customer satisfaction. Half trained employees could sacrifice the quality and beverage process preparation time slowing down the lobby and creating customer dissatisfaction. Management has to ensure they are also helping the manpower to be better than when they first started by pushing employees to do better and create quality for all menu items they sever to the customers. For example, encouraging employees to want to work together and providing them with small incentives as they go along. Such as employee of the month or barista of the week for great preparation and no returned orders. This will allow us to see each employee perform greater. They can also provide monthly performance updates to keep employees updated on their work and track with the process we have at WDCC. Next, methods we currently use can be the cause of the process variances due to the new changes and implemented system that has been put in place. No process is perfect so there is room for improvement as we continue to operate. If baristas are unable to
make the drinks within the proposed preparation time then management may need to take necessary steps to improve the process. Reviewing this process over time can help determine if a new process is need or there is room for improvement to ensure we are preparing beverages within the 2-3 min target valued time. Lastly, the machine could also be olde or require necessary monthly service to ensure they are up and running to their full capacity and to ensure we don't run into mechanical failures during
service times. The machine allows for the WDCC to cut back on the time it takes to prepare a beverage. If
the machine is not functional at full capacity this could slow down the process and cause us to lose customers due to lack of customer satisfaction. Recommendation It can be a challenge to make improvement to an already existing process because changes can be harder to accepts as it reshapes the steps, the management, the quality and the outcome of a process's success or failure. Analyzing is the first step to reshaping the outcome of the process to determine if the intent of the process improvement
plan was successfully achieved. By conducting through analysis of the order times we implemented a process improvement plan that WDCC could use to keep those process times between 2-3 minutes. This analysis gave a full understanding of if the process was centered and capable of the 3-sigma and is statistically controlled. The process is centered and capable of 3-sigma and statically in control. This tells us that the process is successful and well designed. Appendix C will detail that we are operating efficiently and producing high quality menu items and beverages. We determine major items such as manpower, machine, management, and method may cause process variation. These process variations should always be considered when customer dissatisfaction is present. If there is a returned drink or issue with an order, we must ensure these mistakes don't become repetitive and that we allow improvement process changes to shape the areas that are affecting the process. Management will work to document these issue as they arise and create mitigation that ensure they don't arise again. Manpower will focus on perfecting the process so that they're able to complete drink prep in 2-3 minutes expected. Machines should be serviced once a month to ensure they are functional to full capacity. The method must be monitored to ensure the 2-3-minute prep time is consistent and constant.
It is recommended that the WDCC follow the Latte Prep process detailed in the flow chart in Appendix A.
This process ensure consistency over all the drinks that are created and creates customer satisfaction that can be consistent. The data analysis performed in Appendix D details a successful plan if monitoring of suspected areas of process variation and manage those issue as they arise. Appendix A
Appendix B Appendix C:Order is submitted Ground the coffee using a burr grinder Send order to assembly Use a portafilter to grind directly Ask customer to take survey while they wait Fill Forthing pitcher Brew beans from protafilter in the machine Tamp grounds and release Warm up the customer servicing cup/latte cup Pour the hot water out of the customer cup and replace withprepare latte, then add the milk forth Steam the milk with the steam wand in the center of the froth pitcher until it reaches 150 degrees F. Add desired toppings from the customer's order preferances Add desired toppings from the customer's order preferances Machines can slow down the process if they are new and state of the art Machine The current method may not be the most time effiective and there is a faster method for the process Method Proper training and consistentnt employees who want to work and care about the quality of work they produce. They must uphold the quality standards within the position's responsibilites. Manpower Mangement may not be ensure employees are doing their full job and the output is quality. Mangement must also evaluate employees to stay on track and also to determine which employees are not helping the company's success Management
Appendix D: Beverage Service Time Analysis Appendix D References
Ben Lutkevich. (n.d.).business metric. Retrieved from https://www.techtarget.com/searchcustomerexperience/definition/business-metric Hessing, T. (2017, Feb).Process Capability (Cp&Cpk). Retrieved from Sixsignmastudguide: https://sixsigmastudyguide.com/process-capability-cp-cpk/ LinkedIn. (2023, August 17).Process Metrics. Retrieved from LinkedIn: https://www.linkedin.com/advice/3/how-do-you-define-measure-process-
efficiency- effectiveness#:~:text=To%20measure%20process%20efficiency%20and%20effectiveness%2C %20you%20need%20to%20identify,%2C%20quality%2C%20and%20customer%20satisfaction. Team, I. E.
(2023).Three Sigma vs. Six Sigma: Differences, Similarities and Examples. Retrieved from Indeed : https://www.indeed.com/career-advice/career-development/3-sigma-vs-6-sigma
Uploaded by ProfessorRookPerson2833 on coursehero.com
Related business documents
The second process metric that will be tracked is process failure.A process failure is any arget value of the metric will be set to a percentage of total order at 10% incorrectly made orders of coffee. At the end of the month the rate is calculated as well as the reason errors were made.From there, opportunities for improvement are discussed. The third metric to be tracked is
Your preview ends here
Eager to read complete document? Join bartleby learn and gain access to the full version
- Access to all documents
- Unlimited textbook solutions
- 24/7 expert homework help
Related Questions
2. Benefits of Process Capability Analysis
arrow_forward
Calculate the process capability
arrow_forward
Th ree ice-cream packing machines at the Creamy TreatCompany are being evaluated for their capability. Th e followingdata are recorded:
Packing Machine Standard Deviation A 0.2 B 0.3 C 0.05
If specifi cations are set between 15.8 and 16.2 ounces,determine which of the machines are capable of producing withinspecifi cations
arrow_forward
Volumetric Glassware: Utility and Calibration (Dry Lab)
Table B1: Calculation of a 100-mL Volumetric Flask.
temperature of the Distilled H2O (°C)
27
density of distilled H2O at calibration temperature
mass (g) of volumetric flask + distilled H₂O
Trial 1
198.5893
Trial 2
198.6114
Trial 3
mass (g) of dry volumetric flask
98.6563
98.7503
198.6001
98.7145
mass (g) of distilled H₂O
m true g
calculated volume of water dispensed, cm³
corrected volume, V20 °c, cm³
average corrected volume, V20 °C, cm³
standard deviation (4 sig figs)
%RSD (2 sig figs)
arrow_forward
You are the quality control manager and you are now setting up a HACCP plan for your soymilk production plant to make sure your food is safe for consumption.
Here is the flow chart of preparing the soymilk from the soybean.
i. Soaking the soybean ( 15 degree Celsius, 8-12 hours)
ii. Draining the water ( room temperature, 3 hours)
iii. Refrigerated the soybean ( freezing temperature, 2 hours)
iv. Grinding the soybean
V. Cooking slurry (110 degree Celsius, 10 minutes)
vi. Cooling to room temperature (less than 15 minutes)
vii. Filtering
vili. Bottled and seal
CPs and CCPs are food safety terms
a. All the possible control (CPs) and critical control (CCPs) and explain why it is a CP, or CCP, illustrate with the use of the CCP Decision Tree. Comment on the critical limits for each CCP.
b. To establish the HACCP plan, the seven principles are required to set up for identifying the possible hazards. Please describe in detail the rest of the principles after the critical limits have been…
arrow_forward
Erros Pharma Product Performance Appraisal
Erros Pharma Products is engaged in the manufacture and distribution of generic and
branded medicines for various ailment. It employs more than 450 production employees
and 30 sales distribution people. Products are well accepted by the market and physicians
patronize the product together with their patients.
A performance appraisal has been regularly conducted at six month intervals using the
Graphic Rating Scale. The company uses the five point rating scale and the factors
evaluated are quality of work, quantity of work and observable factors as initiative,
leadership, responsibility and dependability. Two supervisors rate the employees and the
average of the two raters becomes the basis for salary evaluation. The department
manager reviews the ratings and discusses with the employees the final results given by the
supervisors.
Three most vocal activists in the company complain directly to the president about the…
arrow_forward
Topic: Quiality control
Indicate three companies in which internal and external quality controls are carried out; the periodicity in which they are carried out, advantages and disadvantages of preparing them.
arrow_forward
In making squash soup, what are the tests to quantify certain parameters as indicators of quality?
arrow_forward
recommended actions by managers when dealing with Process Risks?
arrow_forward
Does process capability match product needs matter?
arrow_forward
3. Describe the concept of the internal customer and its relevance from a quality perspective.
arrow_forward
SEE MORE QUESTIONS
Recommended textbooks for you
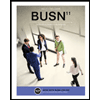
BUSN 11 Introduction to Business Student Edition
Business
ISBN:9781337407137
Author:Kelly
Publisher:Cengage Learning
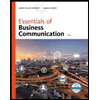
Essentials of Business Communication (MindTap Cou...
Business
ISBN:9781337386494
Author:Mary Ellen Guffey, Dana Loewy
Publisher:Cengage Learning
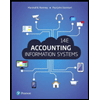
Accounting Information Systems (14th Edition)
Business
ISBN:9780134474021
Author:Marshall B. Romney, Paul J. Steinbart
Publisher:PEARSON
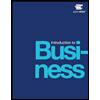
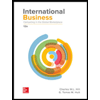
International Business: Competing in the Global M...
Business
ISBN:9781259929441
Author:Charles W. L. Hill Dr, G. Tomas M. Hult
Publisher:McGraw-Hill Education
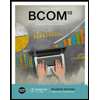
Related Questions
- 2. Benefits of Process Capability Analysisarrow_forwardCalculate the process capabilityarrow_forwardTh ree ice-cream packing machines at the Creamy TreatCompany are being evaluated for their capability. Th e followingdata are recorded: Packing Machine Standard Deviation A 0.2 B 0.3 C 0.05 If specifi cations are set between 15.8 and 16.2 ounces,determine which of the machines are capable of producing withinspecifi cationsarrow_forward
- Volumetric Glassware: Utility and Calibration (Dry Lab) Table B1: Calculation of a 100-mL Volumetric Flask. temperature of the Distilled H2O (°C) 27 density of distilled H2O at calibration temperature mass (g) of volumetric flask + distilled H₂O Trial 1 198.5893 Trial 2 198.6114 Trial 3 mass (g) of dry volumetric flask 98.6563 98.7503 198.6001 98.7145 mass (g) of distilled H₂O m true g calculated volume of water dispensed, cm³ corrected volume, V20 °c, cm³ average corrected volume, V20 °C, cm³ standard deviation (4 sig figs) %RSD (2 sig figs)arrow_forwardYou are the quality control manager and you are now setting up a HACCP plan for your soymilk production plant to make sure your food is safe for consumption. Here is the flow chart of preparing the soymilk from the soybean. i. Soaking the soybean ( 15 degree Celsius, 8-12 hours) ii. Draining the water ( room temperature, 3 hours) iii. Refrigerated the soybean ( freezing temperature, 2 hours) iv. Grinding the soybean V. Cooking slurry (110 degree Celsius, 10 minutes) vi. Cooling to room temperature (less than 15 minutes) vii. Filtering vili. Bottled and seal CPs and CCPs are food safety terms a. All the possible control (CPs) and critical control (CCPs) and explain why it is a CP, or CCP, illustrate with the use of the CCP Decision Tree. Comment on the critical limits for each CCP. b. To establish the HACCP plan, the seven principles are required to set up for identifying the possible hazards. Please describe in detail the rest of the principles after the critical limits have been…arrow_forwardErros Pharma Product Performance Appraisal Erros Pharma Products is engaged in the manufacture and distribution of generic and branded medicines for various ailment. It employs more than 450 production employees and 30 sales distribution people. Products are well accepted by the market and physicians patronize the product together with their patients. A performance appraisal has been regularly conducted at six month intervals using the Graphic Rating Scale. The company uses the five point rating scale and the factors evaluated are quality of work, quantity of work and observable factors as initiative, leadership, responsibility and dependability. Two supervisors rate the employees and the average of the two raters becomes the basis for salary evaluation. The department manager reviews the ratings and discusses with the employees the final results given by the supervisors. Three most vocal activists in the company complain directly to the president about the…arrow_forward
- Topic: Quiality control Indicate three companies in which internal and external quality controls are carried out; the periodicity in which they are carried out, advantages and disadvantages of preparing them.arrow_forwardIn making squash soup, what are the tests to quantify certain parameters as indicators of quality?arrow_forwardrecommended actions by managers when dealing with Process Risks?arrow_forward
arrow_back_ios
arrow_forward_ios
Recommended textbooks for you
- BUSN 11 Introduction to Business Student EditionBusinessISBN:9781337407137Author:KellyPublisher:Cengage LearningEssentials of Business Communication (MindTap Cou...BusinessISBN:9781337386494Author:Mary Ellen Guffey, Dana LoewyPublisher:Cengage LearningAccounting Information Systems (14th Edition)BusinessISBN:9780134474021Author:Marshall B. Romney, Paul J. SteinbartPublisher:PEARSON
- International Business: Competing in the Global M...BusinessISBN:9781259929441Author:Charles W. L. Hill Dr, G. Tomas M. HultPublisher:McGraw-Hill Education
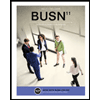
BUSN 11 Introduction to Business Student Edition
Business
ISBN:9781337407137
Author:Kelly
Publisher:Cengage Learning
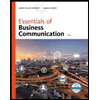
Essentials of Business Communication (MindTap Cou...
Business
ISBN:9781337386494
Author:Mary Ellen Guffey, Dana Loewy
Publisher:Cengage Learning
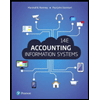
Accounting Information Systems (14th Edition)
Business
ISBN:9780134474021
Author:Marshall B. Romney, Paul J. Steinbart
Publisher:PEARSON
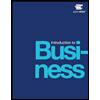
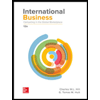
International Business: Competing in the Global M...
Business
ISBN:9781259929441
Author:Charles W. L. Hill Dr, G. Tomas M. Hult
Publisher:McGraw-Hill Education
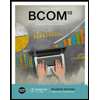