Take Home FinalGSBA509(1)
.docx
keyboard_arrow_up
School
Arizona State University *
*We aren’t endorsed by this school
Course
380
Subject
Finance
Date
Jan 9, 2024
Type
docx
Pages
2
Uploaded by furymills
Take Home Final
Please submit your final answers on Blackboard under “Final Exam” located under the Assignments section. Please upload your work on Blackboard in an excel file. All work is to be done independently.
1. Apple will be introducing the ifridge, and will be in production for the next three years. Apple
has spent $450,000 in consumer demand studies and $100,000 in research in development. Apple
projects that it will be able to sell 80,000 units in the first year, and Apple assumes the number of
units sold will increase by 30% each year. Each ifridge will sell for $2,200. Consumers will have
the option to purchase the Apple Set-Up Plan which cost $300 at time of purchase. The Apple
Set up plan covers delivery and installation. It is projected that 30% of transactions will elect to
purchase the $300 Apple Set-Up plan. The ifridge will have variable cost of $1675 per unit, and
an annual fixed cost of 42 million a year (which includes any costs associated with the Apple
Set-Up Plan). In order to start making the ifridges at a competitive rate, Apple will need to buy a
new machine that will cost 30.89 million. Apple will use the 5-year MACRS schedule to
depreciate the machine. Apple expects that it will be able to sell the machine for $7 million at the
end of the third year. In order to promote the product, Apple will need to set aside $10 mil worth
in new working capital at the before launching the project, and will readjust NWC levels to
reflect 10% of ifridge sales (not including the Apple Set up plan), which will occur with the
timing of the cash flows for that year. For example, NWC for year 1 will be 10% of the sales
from the 80,000 units sold in year one. In the last year, all net working capital will be liquidated
and recouped. The required return for the project is 15%, and the tax rate is 21%.
Sales: 80,000 units, with annual growth of 30% in the number of units
Retail price $2,200, variable cost: $1675 per unit, 42 million in yearly fixed costs.
Optional $300 set up plan, 30% of units sold will purchase the set up plan
Machine cost 30,890,000, depreciated using 5 yr MACRS. Salvage value 7 million.
NWC 10,000,000 in year 0, and then adjust levels equal to 10% of iFridge sales for each
year. All NWC will be liquidated and recouped in the final year.
1.
1A. What is the NPV of this project? Round to the nearest penny.
1B. What is the IRR of this project?
1c. Perform a break-even sensitivity analysis for the following inputs: sales growth rate, retail price, variable cost, and the percentage of sales that elect to buy the Apple Set up Plan). What are the critical values for these variables that set NPV equal to zero?
1D. From the analysis performed in 1c, which variable is the riskiest from a capital budgeting perspective?
2.
WACC: Microsoft (MSFT) using data from Yahoo Finance.
a.
Using 10 years (from 12/15/2013 to 12/15/2023) of monthly returns, calculate the beta of Microsoft using VTI (ticker symbol) as the market returns. What is the Beta?
b.
What is your estimate for the cost of equity using the CAPM approach? Assume a market return of 9%, and a risk free rate of 3.91%.
c.
Pull historical dividend data for MSFT and estimate the cost of equity using the DGM. Explain the steps you take and assumptions you make. What is your final value for cost of equity using DGM.
d.
What rate do you use as the cost of debt for MSFT. Explain your answer.
e.
Calculate the final WACC for MSFT. For cost of equity, use the average value from the CAPM approach and the DGM approach. Explain your answer and any assumptions that
you make. Assume a corporate tax rate of 21%
3.
We are in the business of manufacturing stamped metal subassemblies. Whenever a stamping mechanism wears out, we must replace it with a new one to stay in business. We are considering which of two stamping mechanisms to buy. The company’s tax rate is 21%, and currently have 10% required rate. The company uses straight line depreciation (depreciates the full amount) and is unable to sell the machines after they worn out. Machine A costs $1000 to buy and $100 per year to operate. It wears out and must be replaced every three years. Machine B costs $1400 to buy and $80 per year to operate. It lasts for four years and must then be replaced. Which machine should we go with and why? Please explain your answers and values for each machine.
Your preview ends here
Eager to read complete document? Join bartleby learn and gain access to the full version
- Access to all documents
- Unlimited textbook solutions
- 24/7 expert homework help
Related Questions
Give typing answer with explanation and conclusion
Brookes, Inc. expects to sell 700 of its designer suits every week. The store is open seven days a week and expects to sell the same number of suits every day. The company has an economic order quantity (EOQ) of 500 suits and a safety stock of 100 suits. Once an order is placed, it takes three days for Brookes to get the suits in. How many orders does the company place per year? Assume that it is Monday morning before the store opens, and a shipment of suits has just arrived. When will Brookes place its next order?
arrow_forward
The Sandstone Corporation uses an injection molding machine to make a plastic product, Z35, after receiving firm orders from its customers. Sandstone estimates that it will receive 60 orders for Z35 during the coming year. Each order of Z35 will take 100 hours of machine time. The annual machine capacity is 8,000 hours.
Q. Sandstone is considering introducing a new product, Y21. The company expects it will receive 30 orders of Y21 in the coming year. Each order of Y21 will take 40 hours of machine time. Assuming the demand for Z35 will not be affected by the introduction of Y21, calculate (a) the average waiting time for an order received and (b) the average manufacturing cycle time per order for each product, if Sandstone introduces Y21.
arrow_forward
Hello tutor please provide answer this accounting questions ⁉️
arrow_forward
Please read all of the instructions carefully before completing the exam. All work must be completed
independently.
Part 1: The sales manager of Tesla Sales is considering expanding sales by producing three different versions of
their product. Each will be targeted by the marketing department to different income levels and will be produced
from three different qualities of materials. After reviewing the sales forecasts, the sales department feels that 65% of
units sold will be the original product, 20% will be new model #1 and the remainder will be new model #2.
The following information has been assembled by the sales department and the production department.
Original
Sales price (per unit)
$ 50.00
$ 21.75
Material cost
Direct labor
$
10.50 $
Variable overhead $ 7.25 $
Model #1 Model #2
$35.00 $ 25.00
$ 15.00 $ 10.00
7.75 $ 5.00
5.00 $
3.00
The fixed costs associated with the manufacture of these three products are $250,000 per year.
Required:
(a) Determine the number of units of each…
arrow_forward
The
Reward One
Company manufactures windows. Its manufacturing plant has the capacity to produce
12,000
windows each month. Current production and sales are
10,000
windows per month. The company normally charges
$250 per window.
Requirement 1. Should
Reward One
accept this special order? Show your calculations.
Begin by completing an analysis, and start by showing the computation of the company's operating income without the special order. Next, calculate operating income with the special order, and then calculate the differences between the two columns. (Complete all input fields. For amounts with no change, make sure to enter "0" in the appropriate cells of the Difference column.)
Variable costs that vary with number of units produced
Direct materials
$600,000
Direct manufacturing labor
700,000
Variable costs (for setups, materials handling, quality control, and so on) that vary with number of batches, 100 batches × $1,500 per batch…
arrow_forward
The Sandstone Corporation uses an injection molding machine to make a plastic product, Z35, after receiving firm orders from its customers. Sandstone estimates that it will receive 60 orders for Z35 during the coming year. Each order of Z35 will take 100 hours of machine time. The annual machine capacity is 8,000 hours.
Q. Calculate (a) the average amount of time that an order for Z35 will wait in line before it is processed and (b) the average manufacturing cycle time per order for Z35.
arrow_forward
Blue Spruce Inc. has two divisions. Division A makes and sells student desks. Division B manufactures and sells reading lamps.
Each desk has a reading lamp as one of its components. Division A can purchase reading lamps at a cost of $10 from an outside
vendor. Division A needs 8,200 lamps for the coming year.
Division B has the capacity to manufacture 41,000 lamps annually. Sales to outside customers are estimated at 32,800 lamps for
the next year. Reading lamps are sold at $12 each. Variable costs are $7 per lamp and include $1 of variable sales costs that are not
incurred if lamps are sold internally to Division A. The total amount of fixed costs for Division B is $65,600.
Consider the following independent situations.
(a)
What should be the minimum transfer price accepted by Division B for the 8,200 lamps and the maximum transfer price paid
by Division A?
Minimum transfer price accepted by Division B
Maximum transfer price paid by Division A
$
$
per unit
per unit
arrow_forward
Crede Inc. has two divisions. Division A makes and sells student desks. Division B manufactures and sells reading lamps.
Each desk has a reading lamp as one of its components. Division A can purchase reading lamps at a cost of $10.10 from an outside vendor. Division A needs 11,100 lamps for the coming year.
Division B has the capacity to manufacture 49,600 lamps annually. Sales to outside customers are estimated at 38,500 lamps for the next year. Reading lamps are sold at $12.09 each. Variable costs
are $6.87 per lamp and include $1.41 of variable sales costs that are not incurred if lamps are sold internally to Division A. The total amount of fixed costs for Division B is $75,900. Consider the
following independent situations.
What should be the minimum transfer price accepted by Division B for the 11,100 lamps and the maximum transfer price paid by Division A? (Round answers to 2 decimal places, e.g. 15.25.)
Per unit
Minimum transfer price accepted by Division B $_
Maximum transfer…
arrow_forward
PFA Attached screenshot. Could you please help me with the correct solution.
arrow_forward
Flounder Inc. has two divisions. Division A makes and sells student desks. Division B manufactures and sells reading lamps.
Each desk has a reading lamp as one of its components. Division A can purchase reading lamps at a cost of $10 from an outside vendor.
Division A needs 9,000 lamps for the coming year.
Division B has the capacity to manufacture 45,000 lamps annually. Sales to outside customers are estimated at 36,000 lamps for the
next year. Reading lamps are sold at $12 each. Variable costs are $7 per lamp and include $2 of variable sales costs that are not
incurred if lamps are sold internally to Division A. The total amount of fixed costs for Division B is $72,000.
Consider the following independent situations.
arrow_forward
TimsTabletCo (TTC) produces tablet computers, and it must determine the number of units to be produced during each of the
next four months. The following table gives the monthly demand and the monthly cost of producing each unit:
Month
1
2
3
4
Demand (in units)
5000
2000 6000 1000
Production Cost (dollars per unit)
400 600 200 300
At the start, before Month 1, TTC has an inventory of 2000 units. Each month, up to 4000 units can be produced. TTC can use
the units produced in a particular month in two ways: either use some units to satisfy the demand in the same month, or store
some units in inventory for future use. The cost of storing units in inventory is $100 per unit per month.
(a) Formulate an LP problem (P) to minimize the total cost of meeting the demands of the next four months.
(b) Write the dual LP (D) of (P).
arrow_forward
At the end of the month, approximately what percentage complete will gummy bears be with respect to direct materials?
arrow_forward
At the end of the month, approximately what percentage complete will those gummy bears be with respect to direct materials?
arrow_forward
Ceso Corporation manufactures and sells custom snowmobiles. From the time an order is placed till
the time the snowmobile reaches the customer averages 50 days. This 50 days is spent as follows:
Wait time: 10 days
Move time: 5 days
Process time: 15 days
Queue time: 15 days
Inspection time: 5 days
What is it's manufacturing cycle efficiency (MCE) for its snowmobiles?
30.0%
37.5%
40.0%
60.0%
arrow_forward
Smart Strike Company manufactures and sells soccer balls for teams of children in elementary and high school. Smart Strike's best-selling lines are the practice ball line (durable soccer balls for training and practice) and the match ball line (high-performance soccer balls used in games). In the first four months of next year, Smart Strike expects to sell the following:
Practice Balls
Match Balls
Units
Selling Price
Units
Selling Price
January
50,000
$8.25
7,000
$16.00
February
58,000
$8.25
7,500
$16.00
March
80,000
$8.25
14,000
$16.00
April
100,000
$8.25
18,000
$16.00
Required:
1. Construct a sales budget for Smart Strike for the first three months of the coming year. Show total sales for each product line by month and in total for the first quarter. If required, round your answers to the nearest cent.
Smart Strike CompanySales BudgetFor the First Quarter of Next Year
January
February
March
Quarter
Practice ball:
Units
____
____
_____…
arrow_forward
Please provide answers in excel and step by step explanation
arrow_forward
help
arrow_forward
How to work this probl
arrow_forward
Best Ink produces printers for personal computers. The following information is available for production of a recent order of 500 printers. Process time 16.0 hours Inspection time 3.5 hours Move time 9.0 hours Wait time 21.5 hours 1. Compute the company’s manufacturing cycle time. 2. Compute the company’s manufacturing cycle efficiency. 3. Assume the company wishes to increase its manufacturing cycle efficiency to 0.80. If process time is unchanged, what is the maximum number of hours of non-value-added time the company can have and meet this goal?
arrow_forward
Instruction: Please answer the following with complete solution and explanation. Thank you!
1. Summer Company offers a set of building blocks to customers who send in three (3) UPC codes from Summer cereal, along with P50.00. The blocks sets cost Summer P110 each to purchase and P60 each to mail to customers. During 20x1, Summer sold 1,000,000 boxes of cereal. The company expects 30% of the UPC codes to be sent in. During 20x1, 120,000 UPC codes are redeemed.
Required:
1. What is the cost of estimated claims outstanding?
2. Prepare Summer’s December 31, 20x1 adjusting entry.
arrow_forward
Fill in both of the blanks!
arrow_forward
Plz solve it within 30-40 mins with full explanation I'll give you multiple upvote.
arrow_forward
A carton manufacturer produces two sizes of carton for a fortune 100 logistics company. The logistics
company has agreed to buy the cartons for next 12 months. The carton manufacturer now has tasked their
operations manager to identify the number of cartons to produce for each size to achieve maximum
revenue. When sold to the logistics company, carton A5 sells for 6 dollars a piece and carton C5 sells for 8
dollars a piece.
The carton manufacturer has a labor hours capacity of 8,300 hours and budget for raw material limited to $
185,580.
Carton A5 utilizes 0.09 hours of labor and $2 of material cost per piece whereas, carton C5 utilizes 0.12
hours of labor and $2.75 of material cost per piece.
Formulate a LP model and solve in excel solver to calculate the optimal quantities of each type leading to
maximizing the revenue and satisfying all constraints.
arrow_forward
Smart Strike Company manufactures and sells soccer balls for teams of children in elementary and high school. Smart Strike's best-selling lines are the practice ball line (durable soccer balls for training and practice) and the match ball line (high-performance soccer balls used in games). In the first four months of next year, Smart Strike expects to sell the following:
Practice Balls
Match Balls
Units
Selling Price
Units
Selling Price
January
48,000
$8.85
6,400
$17.20
February
58,000
$8.85
7,500
$17.20
March
86,000
$8.85
13,000
$17.20
April
105,000
$8.85
17,000
$17.20
Smart Strike requires ending inventory of product to equal 20 percent of the next month's unit sales. Beginning inventory in January was 9,600 practice soccer balls and 1,280 match soccer balls.
Every practice ball requires 0.7 square yard of polyvinyl chloride panels, one bladder with valve (to fill with air), and 2 ounces of glue. Smart Strike's policy is that 20…
arrow_forward
Plz solve it within 30-40 mins with full explanation I'll give you multiple upvote.
arrow_forward
Smart Company manufactures and sells soccer balls for teams of children in elementary and high school. Smart best-selling lines are the practice ball line (durable soccer balls for training and practice) and the match ball line (high-performance soccer balls used in games). In the first four months of next year, Smart expects to sell the following:
Practice BaseBalls
Match BaseBalls
Units
Selling Price
Units
Selling Price
January
48,000
$8.85
6,400
$17.20
February
58,000
$8.85
7,500
$17.20
March
86,000
$8.85
13,000
$17.20
April
105,000
$8.85
17,000
$17.20
Smart requires ending inventory of product to equal 20 percent of the next month's unit sales. Beginning inventory in January was 9,600 practice soccer balls and 1,280 match soccer balls.
Every practice ball requires 0.7 square yard of polyvinyl chloride panels, one bladder with valve (to fill with air), and 2 ounces of glue. Smart Strike's policy is that 20 percent of the following…
arrow_forward
Smart Strike Company manufactures and sells soccer balls for teams of children in elementary and high school. Smart Strike's best-selling lines are the practice ball line (durable soccer balls for training and practice) and the match ball line (high-performance soccer balls used in games). In the first four months of next year, Smart Strike expects to sell the following:
Practice Balls
Match Balls
Units
Selling Price
Units
Selling Price
January
47,000
$8.55
6,700
$16.80
February
61,000
$8.55
7,600
$16.80
March
81,000
$8.55
13,500
$16.80
April
100,000
$8.55
16,000
$16.80
Smart Strike requires ending inventory of product to equal 20 percent of the next month's unit sales. Beginning inventory in January was 9,400 practice soccer balls and 1,340 match soccer balls.
Every practice ball requires 0.7 square yard of polyvinyl chloride panels, one bladder with valve (to fill with air), and 3 ounces of glue. Smart Strike's policy is that 20…
arrow_forward
not use ai please
arrow_forward
SEE MORE QUESTIONS
Recommended textbooks for you
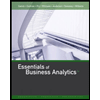
Essentials of Business Analytics (MindTap Course ...
Statistics
ISBN:9781305627734
Author:Jeffrey D. Camm, James J. Cochran, Michael J. Fry, Jeffrey W. Ohlmann, David R. Anderson
Publisher:Cengage Learning
Related Questions
- Give typing answer with explanation and conclusion Brookes, Inc. expects to sell 700 of its designer suits every week. The store is open seven days a week and expects to sell the same number of suits every day. The company has an economic order quantity (EOQ) of 500 suits and a safety stock of 100 suits. Once an order is placed, it takes three days for Brookes to get the suits in. How many orders does the company place per year? Assume that it is Monday morning before the store opens, and a shipment of suits has just arrived. When will Brookes place its next order?arrow_forwardThe Sandstone Corporation uses an injection molding machine to make a plastic product, Z35, after receiving firm orders from its customers. Sandstone estimates that it will receive 60 orders for Z35 during the coming year. Each order of Z35 will take 100 hours of machine time. The annual machine capacity is 8,000 hours. Q. Sandstone is considering introducing a new product, Y21. The company expects it will receive 30 orders of Y21 in the coming year. Each order of Y21 will take 40 hours of machine time. Assuming the demand for Z35 will not be affected by the introduction of Y21, calculate (a) the average waiting time for an order received and (b) the average manufacturing cycle time per order for each product, if Sandstone introduces Y21.arrow_forwardHello tutor please provide answer this accounting questions ⁉️arrow_forward
- Please read all of the instructions carefully before completing the exam. All work must be completed independently. Part 1: The sales manager of Tesla Sales is considering expanding sales by producing three different versions of their product. Each will be targeted by the marketing department to different income levels and will be produced from three different qualities of materials. After reviewing the sales forecasts, the sales department feels that 65% of units sold will be the original product, 20% will be new model #1 and the remainder will be new model #2. The following information has been assembled by the sales department and the production department. Original Sales price (per unit) $ 50.00 $ 21.75 Material cost Direct labor $ 10.50 $ Variable overhead $ 7.25 $ Model #1 Model #2 $35.00 $ 25.00 $ 15.00 $ 10.00 7.75 $ 5.00 5.00 $ 3.00 The fixed costs associated with the manufacture of these three products are $250,000 per year. Required: (a) Determine the number of units of each…arrow_forwardThe Reward One Company manufactures windows. Its manufacturing plant has the capacity to produce 12,000 windows each month. Current production and sales are 10,000 windows per month. The company normally charges $250 per window. Requirement 1. Should Reward One accept this special order? Show your calculations. Begin by completing an analysis, and start by showing the computation of the company's operating income without the special order. Next, calculate operating income with the special order, and then calculate the differences between the two columns. (Complete all input fields. For amounts with no change, make sure to enter "0" in the appropriate cells of the Difference column.) Variable costs that vary with number of units produced Direct materials $600,000 Direct manufacturing labor 700,000 Variable costs (for setups, materials handling, quality control, and so on) that vary with number of batches, 100 batches × $1,500 per batch…arrow_forwardThe Sandstone Corporation uses an injection molding machine to make a plastic product, Z35, after receiving firm orders from its customers. Sandstone estimates that it will receive 60 orders for Z35 during the coming year. Each order of Z35 will take 100 hours of machine time. The annual machine capacity is 8,000 hours. Q. Calculate (a) the average amount of time that an order for Z35 will wait in line before it is processed and (b) the average manufacturing cycle time per order for Z35.arrow_forward
- Blue Spruce Inc. has two divisions. Division A makes and sells student desks. Division B manufactures and sells reading lamps. Each desk has a reading lamp as one of its components. Division A can purchase reading lamps at a cost of $10 from an outside vendor. Division A needs 8,200 lamps for the coming year. Division B has the capacity to manufacture 41,000 lamps annually. Sales to outside customers are estimated at 32,800 lamps for the next year. Reading lamps are sold at $12 each. Variable costs are $7 per lamp and include $1 of variable sales costs that are not incurred if lamps are sold internally to Division A. The total amount of fixed costs for Division B is $65,600. Consider the following independent situations. (a) What should be the minimum transfer price accepted by Division B for the 8,200 lamps and the maximum transfer price paid by Division A? Minimum transfer price accepted by Division B Maximum transfer price paid by Division A $ $ per unit per unitarrow_forwardCrede Inc. has two divisions. Division A makes and sells student desks. Division B manufactures and sells reading lamps. Each desk has a reading lamp as one of its components. Division A can purchase reading lamps at a cost of $10.10 from an outside vendor. Division A needs 11,100 lamps for the coming year. Division B has the capacity to manufacture 49,600 lamps annually. Sales to outside customers are estimated at 38,500 lamps for the next year. Reading lamps are sold at $12.09 each. Variable costs are $6.87 per lamp and include $1.41 of variable sales costs that are not incurred if lamps are sold internally to Division A. The total amount of fixed costs for Division B is $75,900. Consider the following independent situations. What should be the minimum transfer price accepted by Division B for the 11,100 lamps and the maximum transfer price paid by Division A? (Round answers to 2 decimal places, e.g. 15.25.) Per unit Minimum transfer price accepted by Division B $_ Maximum transfer…arrow_forwardPFA Attached screenshot. Could you please help me with the correct solution.arrow_forward
- Flounder Inc. has two divisions. Division A makes and sells student desks. Division B manufactures and sells reading lamps. Each desk has a reading lamp as one of its components. Division A can purchase reading lamps at a cost of $10 from an outside vendor. Division A needs 9,000 lamps for the coming year. Division B has the capacity to manufacture 45,000 lamps annually. Sales to outside customers are estimated at 36,000 lamps for the next year. Reading lamps are sold at $12 each. Variable costs are $7 per lamp and include $2 of variable sales costs that are not incurred if lamps are sold internally to Division A. The total amount of fixed costs for Division B is $72,000. Consider the following independent situations.arrow_forwardTimsTabletCo (TTC) produces tablet computers, and it must determine the number of units to be produced during each of the next four months. The following table gives the monthly demand and the monthly cost of producing each unit: Month 1 2 3 4 Demand (in units) 5000 2000 6000 1000 Production Cost (dollars per unit) 400 600 200 300 At the start, before Month 1, TTC has an inventory of 2000 units. Each month, up to 4000 units can be produced. TTC can use the units produced in a particular month in two ways: either use some units to satisfy the demand in the same month, or store some units in inventory for future use. The cost of storing units in inventory is $100 per unit per month. (a) Formulate an LP problem (P) to minimize the total cost of meeting the demands of the next four months. (b) Write the dual LP (D) of (P).arrow_forwardAt the end of the month, approximately what percentage complete will gummy bears be with respect to direct materials?arrow_forward
arrow_back_ios
SEE MORE QUESTIONS
arrow_forward_ios
Recommended textbooks for you
- Essentials of Business Analytics (MindTap Course ...StatisticsISBN:9781305627734Author:Jeffrey D. Camm, James J. Cochran, Michael J. Fry, Jeffrey W. Ohlmann, David R. AndersonPublisher:Cengage Learning
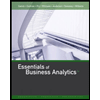
Essentials of Business Analytics (MindTap Course ...
Statistics
ISBN:9781305627734
Author:Jeffrey D. Camm, James J. Cochran, Michael J. Fry, Jeffrey W. Ohlmann, David R. Anderson
Publisher:Cengage Learning