WK3Assgn_Rudolph_T
.docx
keyboard_arrow_up
School
Ashford University *
*We aren’t endorsed by this school
Course
DDBA8006
Subject
Management
Date
Jan 9, 2024
Type
docx
Pages
6
Uploaded by tbaby1110
1
Global Crisis Management-Toyota Case Study
Tiffany Rudolph
Doctor of Business Administration, Walden University
DDBA 8006: Contemporary Challenges in Business
Dr. Carol-Anne Faint
November 19, 2023
2
Global Crisis Management-Toyota Case Study
Companies exist to provide the best product or service. Many industries ranging from food, children’s products, cars, and even pharmaceuticals have specific quality and safety standards that they must meet before being sold to the public, or even quality and safety standards required for production. Even with the most rigorous and strict quality and safety standards, there are often still flaws that occur in products that ultimately result in recalls, and those recalls can have significant monetary and human costs. This paper is going to explore the Toyota’s recall issues, by defining product-harm with respect to Toyota, as well as the issues that
Toyota leadership must resolve, types of successful and unsuccessful organizational changes, and potential remedies for Toyota’s issues. Toyota
Toyota is one of many vehicle manufacturers that sell vehicles in the United States. Despite joining the US market in the 1950s, it took 50 years for Toyota to become one of the leading vehicle manufacturers (Rajasekera, 2013). One year after hitting its biggest financial milestone of gaining $15.1billion in profits, the worldwide financial crisis of 2008 occurred (Rajasekera, 2013). Despite the financial crisis of 2008, Toyota was still able to grow its market share, and surpass General Motors and become the world’s largest vehicle manufacturer (Rajasekera, 2013). Although in 2008, Toyota seemed to be winning, they still reported a loss of $1.5billion, and were facing a continuous stream of recalls, one of which resulted in 52 deaths because of unexpected acceleration issues (Rajasekera, 2013). Recalls and Product-Harm
The product-harm crisis is a more extreme version of a recall. While recalls typically occur for one of two reasons, “a defect related to safety and a defect not related to safety”
3
(Rajasekera, 2013, p. 4). Product-harm crises are widely reported cases of unsafe or faulty items (Lei et. al., 2012). In the case of Toyota, the product-harm crises that this company faced was related to the “sudden acceleration problem” (Rajasekera, 2013, p. 5). The issues with acceleration occurred around the time that Toyota became the world’s leading vehicle manufacturer, and because of this newly acquired title and the perceived nonchalant attitude towards the occurrences, the media began to focus on recall issues (Rajasekera, 2013). The reputational harm that companies face may do more harm than the financial damages the companies incur from replacing products and paying out consumer damages (Lei et. al., 2012). For Toyota, the increasing use of social networking sites (SNS), further allowed the news of their
mechanical issues to spread further, wider, and faster than before the widespread use of SNS. Problems that Toyota Leaders Must Solve
Toyota built a brand on quality control and the major recalls occurring in 2008 and 2010 had major consequences for the organization. To limit the amount of brand damage they could have faced because of the recalls, it was key for the Toyota executives to take swift action to ensure successful management of the crisis they were facing (Rajasekera, 2013). There is a saying that “there is no such thing as bad publicity”, however when it comes to product recalls, that saying is not exactly applicable. Toyota built its brand on quality, so the recalls they incurred were more detrimental to the
company than recalls that other brands had. In 1961, Toyota adopted the phrase of “total quality control”, and the more than seven million recalls occurring in 2010 was contradictory to the brand that they spent over 40 years building (Rajasekera, 2013). To combat this, executives must
improve their quality control protocols by implementing new or improving existing policies, procedures, and guardrails to prevent similar issues from occurring again.
Your preview ends here
Eager to read complete document? Join bartleby learn and gain access to the full version
- Access to all documents
- Unlimited textbook solutions
- 24/7 expert homework help
Related Questions
Add more to this paragraph
Amazon Business has a significant impact on the environmental aspect of sustainability. On the positive side, Amazon's focus on renewable energy and waste reduction initiatives has led to the reduction of its carbon footprint. Additionally, Amazon has invested in electric delivery vehicles, reducing emissions from its logistics operations. However, Amazon's reliance on single-use packaging and its large-scale logistics operations have a negative impact on the environment. Amazon has been criticised for its excessive use of plastic packaging, which contributes to plastic waste in landfills and oceans. Therefore, Amazon must continue to prioritise sustainability in its operations to ensure that its environmental impact is reduced.
arrow_forward
1. Define the problem described in this case study. What management, organization, and technology factors contributed to this problem?
2. To what extent can information technology solve this problem? Explain your answer.
3. What management, organization, and technology issues should be addressed to redesign supply chains to deal with major disruptions such as the coronavirus pandemic?
arrow_forward
Indra Nooyi, the former CEO of PepsiCo describes how she led an effort to the company being a "better corporate citizen." She advises other companies who wish to adopt a "Performance with Purpose" approach to consider all of the following except:
Ensure the company's board of directors support the intiative
Hire a Chief Sustainability Officer to oversee all aspects of the initiative
Adapt the strategy to accommodate the needs of local markets
form partnerships and coalitions with NGOs and other companies
arrow_forward
The COVID-19 pandemic is considered as the leading factor which has collapsed most businesses in the last four months. Your company has been awarded a contract to produce 20 million bottles of hand sanitizers to be given to the citizens by the government. Examine five strategies you would implement with regards to organizations manpower to meet this demand by the government, considering the limited availability of staff.
arrow_forward
Q#2: Discuss the main causes of ethical issues in business and suggest what
preventive measures a business owner can take to avoid them. Please use
appropriate examples?
arrow_forward
THE NISSAN LEAF
With environmental concerns growing among consumers, rising gasoline prices and a desire for a reliable vehicle, Nissan embarked on becoming the first to develop an electric vehicle. The Nissan Leaf was rolled out for public purchase in 2008. Nissan has remained a leader in the electric vehicle market. A number of stakeholders in the automobile industry and other interest groups, will be leading the way in lobbying the Government of Jamaica to reduce the import duty on electric vehicles coming into the island. The need for this move came out of last Wednesday’s (September 27), Electric Vehicle Seminar hosted by JPS and the USAID Caribbean Clean Energy Programme, held at the Spanish Court Hotel in New Kingston. It was recognized that the import duty as high as over 60% is prohibitive to the purchase of these vehicles.
“Electric vehicles have a positive contribution to make to our economy,” JPS Senior Vice President of Energy Delivery, Sheree Martin, pointed out. “Not…
arrow_forward
What role does sustainability play in business trends?
arrow_forward
Explain the following Real Estate Drivers for Jones Lang LaSalle's 2020 Global Real Estate Transparency Index (GRETI)
Corporate social responsibility
Zero carbon buildings
Health and wellness
Technology, proptech and transparency
arrow_forward
Our relationships with companies and other organizations are complex and many issues that impact quality of life relate directly to marketing practices. These include the tradeoff between our privacy and the ability of companies to tailor their offerings to our individual needs. Other issues revolve around market access because many people are unable to navigate the marketplace as a result of disabilities, illiteracy, or other conditions. In addition, our fragile environment requires a commitment to sustainable business practices that attempt to maximize the triple bottom-line that emphasizes financial, social, and environmental benefits. Assume that you are the owner of a construction company in Pakistan, then how you will apply a triple bottom line approach to gain financial, social, and environmental benefits?
arrow_forward
In what ways does Unilever's focus on sustainability (see Illustration Capsule 9.4), in the long-term interest of its shareholders? Does it contribute to the company's competitive advantage or profitability. Discuss.
arrow_forward
Create a PowerPoint Presentation Slide about Coca-Cola's story relating to its 2018 'World Without Waste' campaign business interacting with the external environment.
What should be included in the presentation:
Define and describe Sustainability and the Community as topics in the relevance of the 2018 'World Without Waste' campaign
Summarize the news story you chose and why this is an example of a business interacting with its external environment (what happened / what is happening)
What was the outcome, or what is the intended outcome of this interaction between the business and its external environment? Which stakeholders are impacted by this interaction?
arrow_forward
ADD MORE TO THE CONCLUSION BELOW
In conclusion, Amazon Business has had a significant impact on society, and it is essential to analyse this impact through the lens of sustainable development. By prioritising responsible management that considers the three pillars of sustainability - social, economic, and environmental - Amazon can ensure that its impact is positive and sustainable for the long term. Amazon has played a significant role in shaping the e-commerce industry and has contributed to economic growth. However, the company's operations have raised concerns about working conditions, market monopolisation, and environmental impact. Therefore, there is a need for responsible management to ensure sustainable development. Amazon should improve working conditions, promote fair competition, and adopt environmentally sustainable practices. By doing so, Amazon can play a positive role in society and achieve sustainable development. To improve its impact on society, Amazon should focus…
arrow_forward
Add more to this paragraph below
Amazon Business has a significant impact on the environmental aspect of sustainability. On the positive side, Amazon's focus on renewable energy and waste reduction initiatives has led to the reduction of its carbon footprint. Additionally, Amazon has invested in electric delivery vehicles, reducing emissions from its logistics operations. However, Amazon's reliance on single-use packaging and its large-scale logistics operations have a negative impact on the environment. Amazon has been criticised for its excessive use of plastic packaging, which contributes to plastic waste in landfills and oceans. Therefore, Amazon must continue to prioritise sustainability in its operations to ensure that its environmental impact is reduced. In addition to the points mentioned, it is important to note that Amazon's overall impact on the environment goes beyond just its direct operations. As one of the largest online retailers in the world, Amazon has a significant…
arrow_forward
Add more to this question below
Amazon Business has a significant impact on the social aspect of sustainability. On the positive side, it provides a convenient platform for businesses to buy products and supplies, thus helping them save time and money. As well as at the individual level, Amazon has played a significant role in providing employment opportunities. The company has created over 1.3 million jobs globally in doing so amazon has significantly helped in lowering employment levels. Additionally, it offers a vast selection of products, making it easier for businesses to find what they need. Also, amazon actively work to help communities by responding to the urgent needs of reducing hunger and homelessness and investing in education for children and young adults. However, Amazon has been criticised for its treatment of workers, with some employees complaining about low pay, poor working conditions, and lack of job security. which have led to protests and strikes by workers.Amazon…
arrow_forward
Write 500words about Pest analysis (political economic social-cultural and technological) of H&M in 2021 (pandemic) with Journal article
arrow_forward
Economic and business environment analysis:
What is the Business environment like: Government attitude to foreign investment and trends, ease ofdoing business, trade regulations in germany What is the Inflation levels, currency exchange rate; risks of devaluation versus the dollar in germanyWhat is the Education and literacy levels, availability of skilled labor, labor costs in germany
This information must be linked to the product ( time and patience bakery bread)
arrow_forward
how can business achieve sustainability.
arrow_forward
Conduct additional research on how companies worldwide are detecting and preventingintrusions. Identify the most suitable tools that TransUnion, the Department of Justice, Transnetand Experian could employ in identifying and repairing system weaknesses.
arrow_forward
What are the strategies that should be used by the "Tech Companies" to reduce the impact of pandemic on their operations, logistics and global supply chains?500 words Please include the referencesPlease plagarism below 5%
arrow_forward
You are to analyze the case about Exxon Valdez Oil Spill by answering the following questions:
Analyze the action Exxon took and determine whether what the company did was ethical.
Provide a review of the damage done to the ecosystem of Prince William Sound and discuss whether Exxon had acted responsibly in dealing with the disaster.
arrow_forward
What is environmental sustainability? How should companies gauge their progress toward achieving it?
arrow_forward
Read the following case study and then answer the question that follows:InvestSure has created what it claims is a world first — insurance that protects innocent shareholders from loss caused by allegations of management fraud and dishonesty of Johannesburg Stock Exchange (JSE) listed companies. The startup’s service is currently available on the EasyEquities platform and the startup said in a statement yesterday that it is working on integrations with multiple investment platforms in South Africa. It also plans to roll out the product to all investors in South Africa in December. The startup was founded in 2017 by Ignatious Nkwinika, Shane Curran and Mbulelo Mpofana.
Identify the type of disruptive innovation represented by InvestSure. Justifyyour selection.
arrow_forward
Cape Town-founded mobility tech startup WhereIsMyTransport has secured R42-million in
funding from Naspers. This investment forms part of R201-million funding round led by Naspers
Foundry, Cathay AfricInvest Innovation Fund, and SBI Investment.
WhereIsMyTransport has secured R42-million in funding from Naspers
Phuthi Mahanyele-Dabengwa, South Africa CEO of Naspers comments on the importance of supporting innovations that address mobility issues.
“Mobility remains an obstacle for billions of people in high-growth markets across the world. Our investment in WhereIsMyTransport is a testimony of our belief that great innovation and tech talent is found in South Africa, and with the right backing and support these businesses can provide solutions to local challenges that can improve the lives of ordinary people in South Africa and abroad.”
WhereIsMyTransport, Founded in Cape Town in 2015, the mobility tech startup maps formals and informal public transport networks and uses this data and…
arrow_forward
Cape Town-founded mobility tech startup WhereIsMyTransport has secured R42-million in
funding from Naspers. This investment forms part of R201-million funding round led by Naspers
Foundry, Cathay AfricInvest Innovation Fund, and SBI Investment.
WhereIsMyTransport has secured R42-million in funding from Naspers
Phuthi Mahanyele-Dabengwa, South Africa CEO of Naspers comments on the importance of supporting innovations that address mobility issues.
“Mobility remains an obstacle for billions of people in high-growth markets across the world. Our investment in WhereIsMyTransport is a testimony of our belief that great innovation and tech talent is found in South Africa, and with the right backing and support these businesses can provide solutions to local challenges that can improve the lives of ordinary people in South Africa and abroad.”
WhereIsMyTransport, Founded in Cape Town in 2015, the mobility tech startup maps formals and informal public transport networks and uses this data and…
arrow_forward
What are the components of the 3 pillars of sustainable development? Why do we need to balance 3 pillars to run the company sustainability?
Provide 5 reasons and explain in detail.
arrow_forward
Business sustainability become one of the most important pillars for all kind of business. What are the main methods or approaches that could be used to enhance business sustainability in the business sector?
arrow_forward
SEE MORE QUESTIONS
Recommended textbooks for you
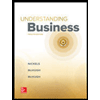
Understanding Business
Management
ISBN:9781259929434
Author:William Nickels
Publisher:McGraw-Hill Education
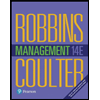
Management (14th Edition)
Management
ISBN:9780134527604
Author:Stephen P. Robbins, Mary A. Coulter
Publisher:PEARSON
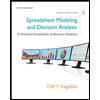
Spreadsheet Modeling & Decision Analysis: A Pract...
Management
ISBN:9781305947412
Author:Cliff Ragsdale
Publisher:Cengage Learning
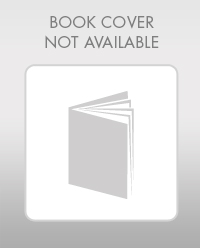
Management Information Systems: Managing The Digi...
Management
ISBN:9780135191798
Author:Kenneth C. Laudon, Jane P. Laudon
Publisher:PEARSON
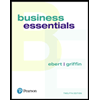
Business Essentials (12th Edition) (What's New in...
Management
ISBN:9780134728391
Author:Ronald J. Ebert, Ricky W. Griffin
Publisher:PEARSON
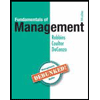
Fundamentals of Management (10th Edition)
Management
ISBN:9780134237473
Author:Stephen P. Robbins, Mary A. Coulter, David A. De Cenzo
Publisher:PEARSON
Related Questions
- Add more to this paragraph Amazon Business has a significant impact on the environmental aspect of sustainability. On the positive side, Amazon's focus on renewable energy and waste reduction initiatives has led to the reduction of its carbon footprint. Additionally, Amazon has invested in electric delivery vehicles, reducing emissions from its logistics operations. However, Amazon's reliance on single-use packaging and its large-scale logistics operations have a negative impact on the environment. Amazon has been criticised for its excessive use of plastic packaging, which contributes to plastic waste in landfills and oceans. Therefore, Amazon must continue to prioritise sustainability in its operations to ensure that its environmental impact is reduced.arrow_forward1. Define the problem described in this case study. What management, organization, and technology factors contributed to this problem? 2. To what extent can information technology solve this problem? Explain your answer. 3. What management, organization, and technology issues should be addressed to redesign supply chains to deal with major disruptions such as the coronavirus pandemic?arrow_forwardIndra Nooyi, the former CEO of PepsiCo describes how she led an effort to the company being a "better corporate citizen." She advises other companies who wish to adopt a "Performance with Purpose" approach to consider all of the following except: Ensure the company's board of directors support the intiative Hire a Chief Sustainability Officer to oversee all aspects of the initiative Adapt the strategy to accommodate the needs of local markets form partnerships and coalitions with NGOs and other companiesarrow_forward
- The COVID-19 pandemic is considered as the leading factor which has collapsed most businesses in the last four months. Your company has been awarded a contract to produce 20 million bottles of hand sanitizers to be given to the citizens by the government. Examine five strategies you would implement with regards to organizations manpower to meet this demand by the government, considering the limited availability of staff.arrow_forwardQ#2: Discuss the main causes of ethical issues in business and suggest what preventive measures a business owner can take to avoid them. Please use appropriate examples?arrow_forwardTHE NISSAN LEAF With environmental concerns growing among consumers, rising gasoline prices and a desire for a reliable vehicle, Nissan embarked on becoming the first to develop an electric vehicle. The Nissan Leaf was rolled out for public purchase in 2008. Nissan has remained a leader in the electric vehicle market. A number of stakeholders in the automobile industry and other interest groups, will be leading the way in lobbying the Government of Jamaica to reduce the import duty on electric vehicles coming into the island. The need for this move came out of last Wednesday’s (September 27), Electric Vehicle Seminar hosted by JPS and the USAID Caribbean Clean Energy Programme, held at the Spanish Court Hotel in New Kingston. It was recognized that the import duty as high as over 60% is prohibitive to the purchase of these vehicles. “Electric vehicles have a positive contribution to make to our economy,” JPS Senior Vice President of Energy Delivery, Sheree Martin, pointed out. “Not…arrow_forward
- What role does sustainability play in business trends?arrow_forwardExplain the following Real Estate Drivers for Jones Lang LaSalle's 2020 Global Real Estate Transparency Index (GRETI) Corporate social responsibility Zero carbon buildings Health and wellness Technology, proptech and transparencyarrow_forwardOur relationships with companies and other organizations are complex and many issues that impact quality of life relate directly to marketing practices. These include the tradeoff between our privacy and the ability of companies to tailor their offerings to our individual needs. Other issues revolve around market access because many people are unable to navigate the marketplace as a result of disabilities, illiteracy, or other conditions. In addition, our fragile environment requires a commitment to sustainable business practices that attempt to maximize the triple bottom-line that emphasizes financial, social, and environmental benefits. Assume that you are the owner of a construction company in Pakistan, then how you will apply a triple bottom line approach to gain financial, social, and environmental benefits?arrow_forward
- In what ways does Unilever's focus on sustainability (see Illustration Capsule 9.4), in the long-term interest of its shareholders? Does it contribute to the company's competitive advantage or profitability. Discuss.arrow_forwardCreate a PowerPoint Presentation Slide about Coca-Cola's story relating to its 2018 'World Without Waste' campaign business interacting with the external environment. What should be included in the presentation: Define and describe Sustainability and the Community as topics in the relevance of the 2018 'World Without Waste' campaign Summarize the news story you chose and why this is an example of a business interacting with its external environment (what happened / what is happening) What was the outcome, or what is the intended outcome of this interaction between the business and its external environment? Which stakeholders are impacted by this interaction?arrow_forwardADD MORE TO THE CONCLUSION BELOW In conclusion, Amazon Business has had a significant impact on society, and it is essential to analyse this impact through the lens of sustainable development. By prioritising responsible management that considers the three pillars of sustainability - social, economic, and environmental - Amazon can ensure that its impact is positive and sustainable for the long term. Amazon has played a significant role in shaping the e-commerce industry and has contributed to economic growth. However, the company's operations have raised concerns about working conditions, market monopolisation, and environmental impact. Therefore, there is a need for responsible management to ensure sustainable development. Amazon should improve working conditions, promote fair competition, and adopt environmentally sustainable practices. By doing so, Amazon can play a positive role in society and achieve sustainable development. To improve its impact on society, Amazon should focus…arrow_forward
arrow_back_ios
SEE MORE QUESTIONS
arrow_forward_ios
Recommended textbooks for you
- Understanding BusinessManagementISBN:9781259929434Author:William NickelsPublisher:McGraw-Hill EducationManagement (14th Edition)ManagementISBN:9780134527604Author:Stephen P. Robbins, Mary A. CoulterPublisher:PEARSONSpreadsheet Modeling & Decision Analysis: A Pract...ManagementISBN:9781305947412Author:Cliff RagsdalePublisher:Cengage Learning
- Management Information Systems: Managing The Digi...ManagementISBN:9780135191798Author:Kenneth C. Laudon, Jane P. LaudonPublisher:PEARSONBusiness Essentials (12th Edition) (What's New in...ManagementISBN:9780134728391Author:Ronald J. Ebert, Ricky W. GriffinPublisher:PEARSONFundamentals of Management (10th Edition)ManagementISBN:9780134237473Author:Stephen P. Robbins, Mary A. Coulter, David A. De CenzoPublisher:PEARSON
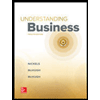
Understanding Business
Management
ISBN:9781259929434
Author:William Nickels
Publisher:McGraw-Hill Education
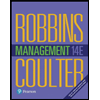
Management (14th Edition)
Management
ISBN:9780134527604
Author:Stephen P. Robbins, Mary A. Coulter
Publisher:PEARSON
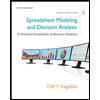
Spreadsheet Modeling & Decision Analysis: A Pract...
Management
ISBN:9781305947412
Author:Cliff Ragsdale
Publisher:Cengage Learning
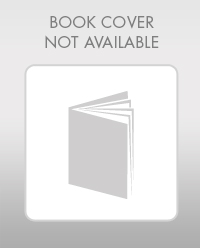
Management Information Systems: Managing The Digi...
Management
ISBN:9780135191798
Author:Kenneth C. Laudon, Jane P. Laudon
Publisher:PEARSON
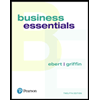
Business Essentials (12th Edition) (What's New in...
Management
ISBN:9780134728391
Author:Ronald J. Ebert, Ricky W. Griffin
Publisher:PEARSON
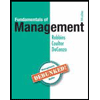
Fundamentals of Management (10th Edition)
Management
ISBN:9780134237473
Author:Stephen P. Robbins, Mary A. Coulter, David A. De Cenzo
Publisher:PEARSON