21. Backwoods American, Inc. produces expensve water repellent down-filled parkas. The company implemented a total quality manage- ment program in 2014. Following are quality-related accounting data that have been accumulated for the fiveyear period after the program's start. Year 2015 2016 2017 2018 2019 Quality Costs (000) Prevention $3.2 10.7 28.3 426 50.0 Appraisal 26.3 29.2 30.6 24.1 19.6 Internal failure 39.1 51.3 48.4 35.9 32.1 External failure 118.6 110.5 105.2 91.3 65.2 Accounting Measures (000s) Sales $2,700.6 2,690.1 2,705.3 2,310.2 2,880.7
21. Backwoods American, Inc. produces expensve water repellent down-filled parkas. The company implemented a total quality manage- ment program in 2014. Following are quality-related accounting data that have been accumulated for the fiveyear period after the program's start. Year 2015 2016 2017 2018 2019 Quality Costs (000) Prevention $3.2 10.7 28.3 426 50.0 Appraisal 26.3 29.2 30.6 24.1 19.6 Internal failure 39.1 51.3 48.4 35.9 32.1 External failure 118.6 110.5 105.2 91.3 65.2 Accounting Measures (000s) Sales $2,700.6 2,690.1 2,705.3 2,310.2 2,880.7
Purchasing and Supply Chain Management
6th Edition
ISBN:9781285869681
Author:Robert M. Monczka, Robert B. Handfield, Larry C. Giunipero, James L. Patterson
Publisher:Robert M. Monczka, Robert B. Handfield, Larry C. Giunipero, James L. Patterson
ChapterC: Cases
Section: Chapter Questions
Problem 5.3SD: Scenario 4 Sharon Gillespie, a new buyer at Visionex, Inc., was reviewing quotations for a tooling...
Related questions
Question
SOLVE 2.2 ONLY
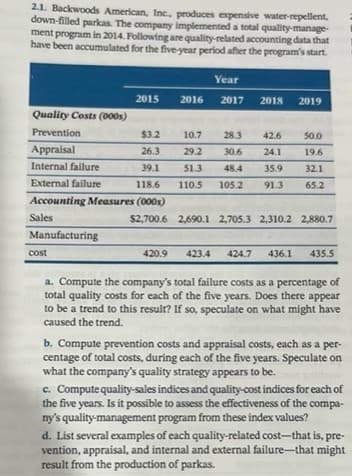
Transcribed Image Text:2.1. Backwoods American, Inc, produces expensive water-repellent,
down-filled parkas. The company implemented a total quality-manage
ment program in 2014. Following are quality-related accounting data that
have been accumulated for the five-year period after the program's start.
Year
2015
2016
2017
2018
2019
Quality Costs (000s)
Prevention
$3.2
10.7
28.3
42.6
50.0
Appraisal
26.3
29.2
30.6
24.1
19.6
Internal failure
39.1
51.3
48.4
35.9
32.1
External failure
118.6
110.5
105.2
91.3
65.2
Accounting Measures (000s)
Sales
$2,700.6 2,690.1 2,705.3 2,310.2 2,880.7
Manufacturing
cost
420.9
423.4
424.7
436.1
435.5
a. Compute the company's total failure costs as a percentage of
total quality costs for each of the five years. Does there appear
to be a trend to this result? If so, speculate on what might have
caused the trend.
b. Compute prevention costs and appraisal costs, each as a per-
centage of total costs, during each of the five years. Speculate on
what the company's quality strategy appears to be.
c. Compute quality-sales indices and quality-cost indices for each of
the five years. Is it possible to assess the effectiveness of the compa-
ny's quality-management program from these index values?
d. List several examples of each quality-related cost-that is, pre-
vention, appraisal, and internal and external failure-that might
result from the production of parkas.
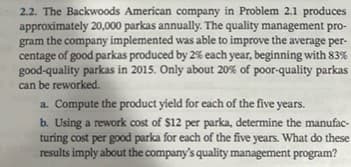
Transcribed Image Text:2.2. The Backwoods American company in Problem 2.1 produces
approximately 20,000 parkas annually. The quality management pro-
a the company implemented was able to improve the average per-
gram
centage of good parkas produced by 2% each year, beginning with 83%
good-quality parkas in 2015. Only about 20% of poor-quality parkas
can be reworked.
a. Compute the product yield for each of the five years.
b. Using a rework cost of $12 per parka, determine the manufac-
turing cost per good parka for each of the five years. What do these
results imply about the company's quality management program?
Expert Solution

This question has been solved!
Explore an expertly crafted, step-by-step solution for a thorough understanding of key concepts.
This is a popular solution!
Trending now
This is a popular solution!
Step by step
Solved in 3 steps

Recommended textbooks for you
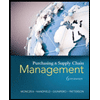
Purchasing and Supply Chain Management
Operations Management
ISBN:
9781285869681
Author:
Robert M. Monczka, Robert B. Handfield, Larry C. Giunipero, James L. Patterson
Publisher:
Cengage Learning
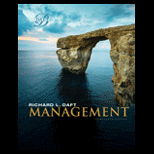
Management, Loose-Leaf Version
Management
ISBN:
9781305969308
Author:
Richard L. Daft
Publisher:
South-Western College Pub
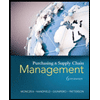
Purchasing and Supply Chain Management
Operations Management
ISBN:
9781285869681
Author:
Robert M. Monczka, Robert B. Handfield, Larry C. Giunipero, James L. Patterson
Publisher:
Cengage Learning
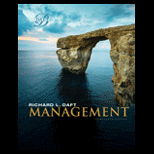
Management, Loose-Leaf Version
Management
ISBN:
9781305969308
Author:
Richard L. Daft
Publisher:
South-Western College Pub