The Slate Company manufactures and sells television sets. Its assembly division (AD) buys television screens from the screen division (SD) and assembles the TV sets. The SD, which is operating at capacity, incurs an incremental manufacturing cost of $65 per screen. The SD can sell all its output to the outside market at a price of $100 per screen, after incurring a variable marketing and distribution cost of $8 per screen. If the AD purchases screens from outside suppliers at a price of $100 per screen, it will incur a variable purchasing cost of $7 per screen. Slate’s division managers can act autonomously to maximize their own division’s operating income. Q. Now suppose that the SD can sell only 70% of its output capacity of 20,000 screens per month on the open market. Capacity cannot be reduced in the short run. The AD can assemble and sell more than 20,000 TV sets per month. a. What is the minimum transfer price at which the SD manager would be willing to sell screens to the AD?
The Slate Company manufactures and sells television sets. Its assembly division (AD) buys television screens from the screen division (SD) and assembles the TV sets. The SD, which is operating at capacity, incurs an incremental
Q. Now suppose that the SD can sell only 70% of its output capacity of 20,000 screens per month on the open market. Capacity cannot be reduced in the short run. The AD can assemble and sell more than 20,000 TV sets per month.
a. What is the minimum transfer price at which the SD manager would be willing to sell screens to the AD?

Trending now
This is a popular solution!
Step by step
Solved in 2 steps with 1 images

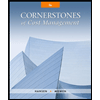
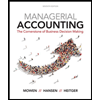
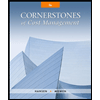
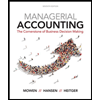
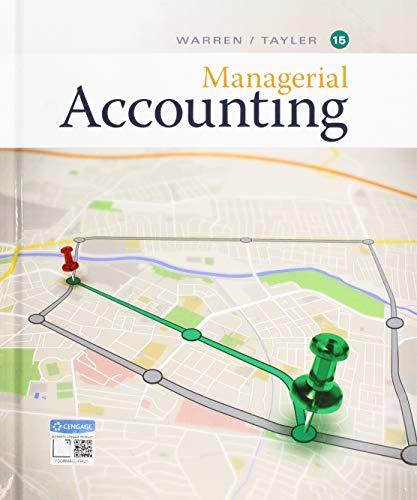
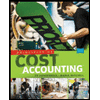
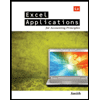