Walton Bike Company makes the frames used to build its bicycles. During year 2, Walton made 21,000 frames; the costs incurred follow. Unit-level materials costs (21,000 units x $49) Unit-level labor costs (21,000 units x $56) Unit-level overhead costs (21,000 x $11) Depreciation on manufacturing equipment Bike frame production supervisor's salary Inventory holding costs Allocated portion of facility-level costs $1,029,000 1,176,000 231,000 90,000 93,400 280,000 590,000 Total costs $3,489,400 Walton has an opportunity to purchase frames for $120 each. Additional Information 1. The manufacturing equipment, which originally cost $550,000, has a book value of $410,000, a remaining useful life of 4 years, and a zero salvage value. If the equipment is not used to produce bicycle frames, it can be leased for $76,000 per year. 2. Walton has the opportunity to purchase for $990,000 new manufacturing equipment that will have an expected useful life of 4 years and a salvage value of $47,600. This equipment will increase productivity substantially, reducing unit-level labor costs by 50 percent. Assume that Walton will continue to produce and sell 21,000 frames per year in the future. 3. If Walton outsources the frames, the company can eliminate 70 percent of the inventory holding costs. Required a. Determine the avoidable cost per unit of making the bike frames, assuming that Walton is considering the alternatives of making the product using the existing equipment or outsourcing the product to the independent contractor. Based on the quantitative data, should Walton outsource the bike frames? b. Assuming that Walton is considering whether to replace the old equipment with the new equipment, determine the avoidable cost per unit to produce the bike frames using the new equipment and the avoidable cost per unit to produce the bike frames using the old equipment. Calculate the increase or decrease in the company's profit if the company uses new equipment. c. Assuming that Walton is considering whether to either purchase or outsource, calculate the impact on profitability between the two alternatives.
Walton Bike Company makes the frames used to build its bicycles. During year 2, Walton made 21,000 frames; the costs incurred follow. Unit-level materials costs (21,000 units x $49) Unit-level labor costs (21,000 units x $56) Unit-level overhead costs (21,000 x $11) Depreciation on manufacturing equipment Bike frame production supervisor's salary Inventory holding costs Allocated portion of facility-level costs $1,029,000 1,176,000 231,000 90,000 93,400 280,000 590,000 Total costs $3,489,400 Walton has an opportunity to purchase frames for $120 each. Additional Information 1. The manufacturing equipment, which originally cost $550,000, has a book value of $410,000, a remaining useful life of 4 years, and a zero salvage value. If the equipment is not used to produce bicycle frames, it can be leased for $76,000 per year. 2. Walton has the opportunity to purchase for $990,000 new manufacturing equipment that will have an expected useful life of 4 years and a salvage value of $47,600. This equipment will increase productivity substantially, reducing unit-level labor costs by 50 percent. Assume that Walton will continue to produce and sell 21,000 frames per year in the future. 3. If Walton outsources the frames, the company can eliminate 70 percent of the inventory holding costs. Required a. Determine the avoidable cost per unit of making the bike frames, assuming that Walton is considering the alternatives of making the product using the existing equipment or outsourcing the product to the independent contractor. Based on the quantitative data, should Walton outsource the bike frames? b. Assuming that Walton is considering whether to replace the old equipment with the new equipment, determine the avoidable cost per unit to produce the bike frames using the new equipment and the avoidable cost per unit to produce the bike frames using the old equipment. Calculate the increase or decrease in the company's profit if the company uses new equipment. c. Assuming that Walton is considering whether to either purchase or outsource, calculate the impact on profitability between the two alternatives.
Cornerstones of Cost Management (Cornerstones Series)
4th Edition
ISBN:9781305970663
Author:Don R. Hansen, Maryanne M. Mowen
Publisher:Don R. Hansen, Maryanne M. Mowen
Chapter2: Basic Cost Management Concepts
Section: Chapter Questions
Problem 13E: Wyandotte Company provided the following information for the last calendar year: During the year,...
Related questions
Question
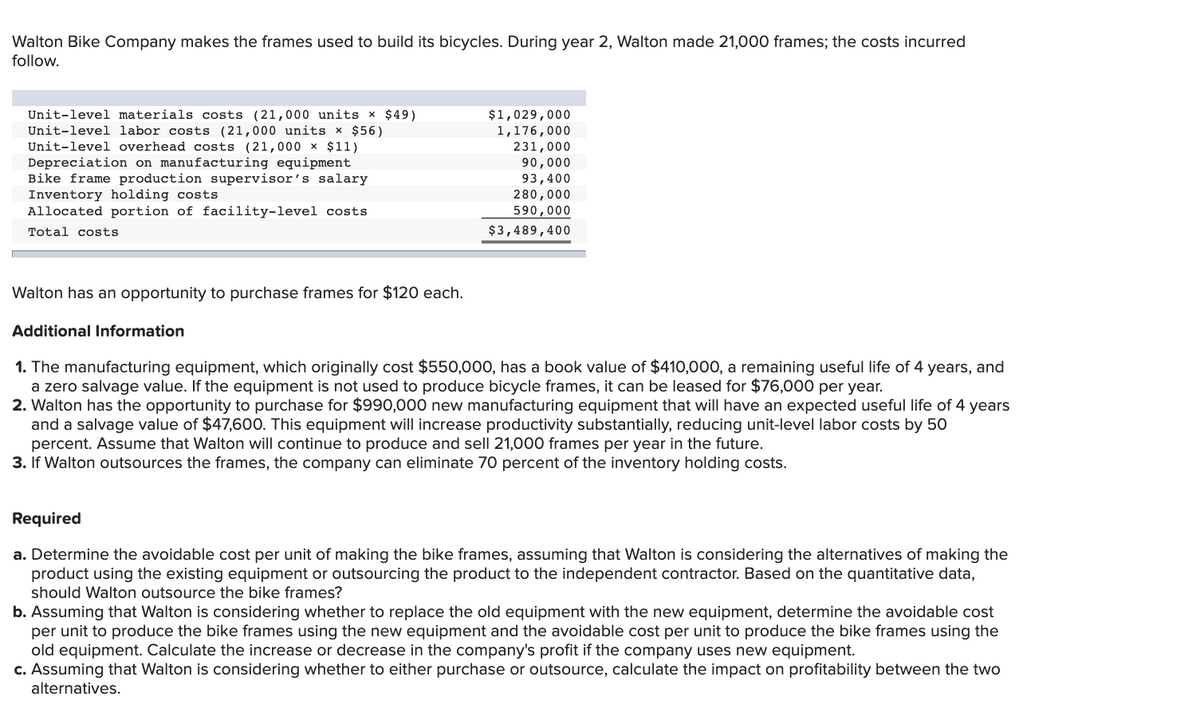
Transcribed Image Text:Walton Bike Company makes the frames used to build its bicycles. During year 2, Walton made 21,000 frames; the costs incurred
follow.
Unit-level materials costs (21,000 units x $49)
Unit-level labor costs (21,000 units × $56)
Unit-level overhead costs (21,000 x $11)
Depreciation on manufacturing equipment
Bike frame production supervisor's salary
Inventory holding costs
Allocated portion of facility-level costs
$1,029,000
1,176,000
231,000
90,000
93,400
280,000
590,000
Total costs
$3,489,400
Walton has an opportunity to purchase frames for $120 each.
Additional Information
1. The manufacturing equipment, which originally cost $550,000, has a book value of $410,000, a remaining useful life of 4 years, and
a zero salvage value. If the equipment is not used to produce bicycle frames, it can be leased for $76,000 per year.
2. Walton has the opportunity to purchase for $990,000 new manufacturing equipment that will have an expected useful life of 4 years
and a salvage value of $47,600. This equipment will increase productivity substantially, reducing unit-level labor costs by 50
percent. Assume that Walton will continue to produce and sell 21,000 frames per year in the future.
3. If Walton outsources the frames, the company can eliminate 70 percent of the inventory holding costs.
Required
a. Determine the avoidable cost per unit of making the bike frames, assuming that Walton is considering the alternatives of making the
product using the existing equipment or outsourcing the product to the independent contractor. Based on the quantitative data,
should Walton outsource the bike frames?
b. Assuming that Walton is considering whether to replace the old equipment with the new equipment, determine the avoidable cost
per unit to produce the bike frames using the new equipment and the avoidable cost per unit to produce the bike frames using the
old equipment. Calculate the increase or decrease in the company's profit if the company uses new equipment.
c. Assuming that Walton is considering whether to either purchase or outsource, calculate the impact on profitability between the two
alternatives.
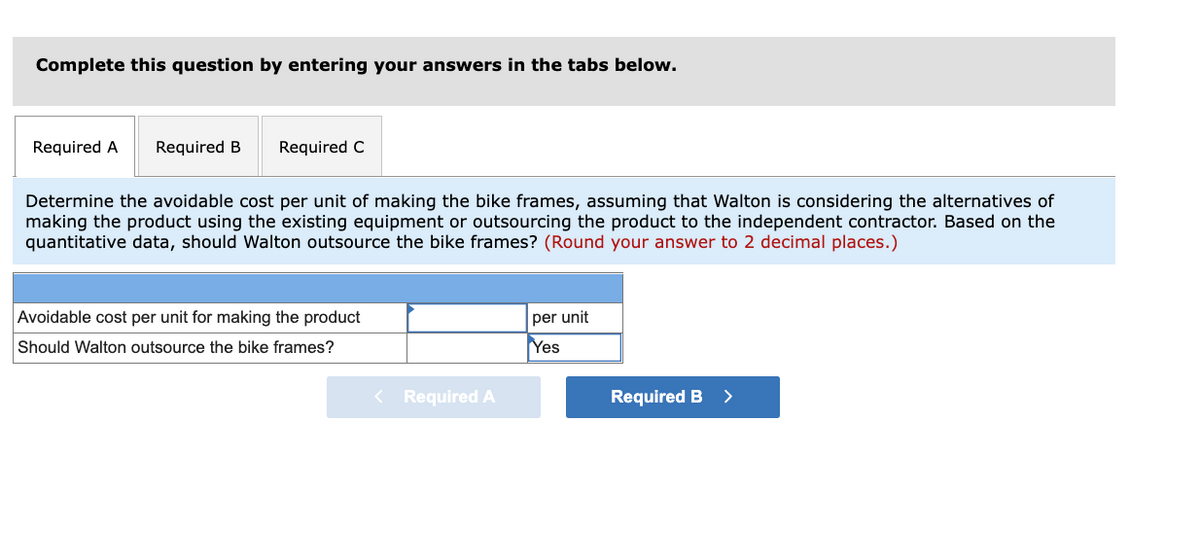
Transcribed Image Text:Complete this question by entering your answers in the tabs below.
Required A
Required B
Required C
Determine the avoidable cost per unit of making the bike frames, assuming that Walton is considering the alternatives of
making the product using the existing equipment or outsourcing the product to the independent contractor. Based on the
quantitative data, should Walton outsource the bike frames? (Round your answer to 2 decimal places.)
Avoidable cost per unit for making the product
per unit
Should Walton outsource the bike frames?
Yes
< Required A
Required B >
Expert Solution

This question has been solved!
Explore an expertly crafted, step-by-step solution for a thorough understanding of key concepts.
This is a popular solution!
Trending now
This is a popular solution!
Step by step
Solved in 4 steps

Knowledge Booster
Learn more about
Need a deep-dive on the concept behind this application? Look no further. Learn more about this topic, accounting and related others by exploring similar questions and additional content below.Recommended textbooks for you
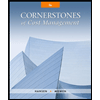
Cornerstones of Cost Management (Cornerstones Ser…
Accounting
ISBN:
9781305970663
Author:
Don R. Hansen, Maryanne M. Mowen
Publisher:
Cengage Learning
Principles of Accounting Volume 2
Accounting
ISBN:
9781947172609
Author:
OpenStax
Publisher:
OpenStax College
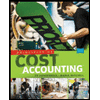
Principles of Cost Accounting
Accounting
ISBN:
9781305087408
Author:
Edward J. Vanderbeck, Maria R. Mitchell
Publisher:
Cengage Learning
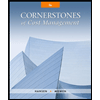
Cornerstones of Cost Management (Cornerstones Ser…
Accounting
ISBN:
9781305970663
Author:
Don R. Hansen, Maryanne M. Mowen
Publisher:
Cengage Learning
Principles of Accounting Volume 2
Accounting
ISBN:
9781947172609
Author:
OpenStax
Publisher:
OpenStax College
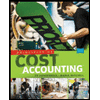
Principles of Cost Accounting
Accounting
ISBN:
9781305087408
Author:
Edward J. Vanderbeck, Maria R. Mitchell
Publisher:
Cengage Learning
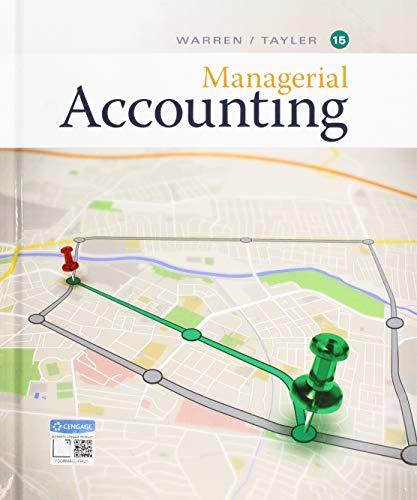
Managerial Accounting
Accounting
ISBN:
9781337912020
Author:
Carl Warren, Ph.d. Cma William B. Tayler
Publisher:
South-Western College Pub
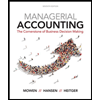
Managerial Accounting: The Cornerstone of Busines…
Accounting
ISBN:
9781337115773
Author:
Maryanne M. Mowen, Don R. Hansen, Dan L. Heitger
Publisher:
Cengage Learning